[Editor's note: A version of this story appears in the July 2020 edition of E&P. Subscribe to the magazine here.]
Humans long ago figured out that tools were the secret to prosperity. For the oil and gas industry, tools are necessary in tackling tough challenges. In all stages of development, from exploration to production, operators seek out innovative technologies to increase efficiencies and hydrocarbon recovery in a sustainable manner.
“Contrary to popular belief, the oil and gas industry has always been at the forefront of technological advancement,” Dr. Gary Aillud, reservoir geology team leader with RPS Group, told E&P. “With our ever-changing world and the increasing importance of sustainability, the role of technology in improving the efficiency of hydrocarbon recovery from shale plays has never been more important. With advancements in technology comes the added benefit of reduction in the environmental impact and energy security for the producing countries.”
While technology and tools are continually evolving, the development of shale resources required some creative thinking to efficiently and effectively drill, complete and produce shale wells.
“Oil and gas operators require service providers to develop solutions for continuous improvement in order to lower extraction costs,” Wayne Prejean, president and CEO of Drilling Tools International, told E&P.
“Legacy technology has been improved but is limited, and new innovation is what drives efficiency improvement.”
One way the industry is driving improvements is through the use of digital technologies. A recent report from GlobalData stated there is an increase in the number of companies that are “leveraging immersive technologies, such as augmented reality and virtual reality, to improve operational efficiency, lower costs and overcome [the] skilled labor shortage.”
While there are significant costs associated with digital technologies, it is minimal when compared with the potential returns. Data properly collected today can deliver long-term returns when properly applied to future operations.
“The shale industry is rapidly moving their subsurface data to the cloud, and companies need to seriously consider the true costs of these initiatives and how they’ll be able to access their data thereafter,” Patrick Meroney, vice president of U.S. Operations and Consulting Services with Katalyst Data Management, told E&P. “Subsurface data in the cloud still needs to have some level of context or metadata extracted and applied, otherwise E&P companies will just have a big file server on someone else’s computer.”
But there are more than bytes and pixels being improved upon by shale technology innovators.
The industry runs on complex combinations of big iron, tiny sand grains, explosive powders and metallurgical wonders that vanish over time. Everything from plugs, frac fluids and perforating systems to proppants and diverters can help drive down breakevens. New technologies in the completions field are among the most important components to the overall cycle of producing a barrel of oil. Additionally, affordable and effective solutions are being developed for water management to ensure continued optimization of water resources.
“Once again our industry has been hit by oil pricing that’s daunting and unforgiving. We must rise to the challenge by focusing on minimizing operating costs at every level,” Lisa Henthorne, P.E., senior vice president and CTO with Water Standard and president of Produced Water Society, told E&P. “Water management contributes about $4/bbl of water when considered from cost of sourcing through its life cycle to disposal. This equates to $10 to $20/bbl of oil. We’ve greatly improved our overall economics the last few years, but there’s still much to be done to reduce water management costs. [For example,] recycling/reusing produced water can reduce transportation and disposals costs. It’s also good for the environment.”
There is an underlying need to increase efficiencies across the upstream sector.
“There is a reason we coined the term Shale Revolution. Together we have changed the entire business of energy extraction. But we cannot stop evolving. We must push forward into new frontiers of efficiency, safety and productivity. The world depends on us to deliver plentiful, affordable, clean energy for everyone,” Frac Shack CEO Todd Van Vliet told E&P.
Below, E&P’s annual Shale Technology Showcase features a sampling of new shale technologies and services that were developed to improve efficiencies in the exploration, drilling, completions, production and water management space.
—Introduction written by Ariana Hurtado and Jennifer Presley
Editor’s note: The copy herein is contributed from service companies and does not reflect the opinions of Hart Energy. If you would like to be added to this article, submit a 150-200 words describing your latest shale technology or service to Ariana Hurtado at ahurtado@hartenergy.com (the tool must have been developed, released or updated in the last year). Inclusion is at the discretion of the editors.
Compiled by Ariana Hurtado, Senior Managing Editor, Print Media
EXPLORATION >>>
Data security: revealing data to the right people
The amount of subsurface data available to the shale industry has exploded in recent years. As subsurface databases become larger, cover more geographical areas and contain multiple business units’ data, companies are challenged with regulating access to certain datasets. Confidential datasets and assets still need to be managed and available online but not to everyone. To maintain data security, Katalyst Data Management recently developed an entitlements module for its iGlass solution. Now users can easily limit who sees what data and what actions they can take with it. The iGlass data management software has the ability to restrict data access on a per inventory item, per user basis, to ensure subsurface data remain secure within an organization.

DRILLING >>>
Energy storage system for land drilling

Traditionally, lean-burn generator sets do not typically have the transient response capability that land drilling applications require, and while rich-burn generator sets can approach the transient response requirement, they do not have the power density and efficiency that lean-burn generator sets have. Caterpillar Oil & Gas has released the Cat Land Drilling Energy Storage System as a first-of-its-kind hybrid system. This integrated solution consisting of natural gas gensets and energy storage technology presents key advantages for drilling contractors and operators. Advantages include improved fuel economy, reduced engine maintenance, reduced emissions, improved uptime and capital efficiency, reduced engine noise, added spinning reserve and cold-start generator elimination. The energy storage system and natural gas gensets are fully integrated, automated and optimized to power drilling rigs efficiently. The key components of the system that enable seamless operation between gensets and energy storage include the smart engine management system, bidirectional power inverters and a master controller. These tools are easy to integrate into existing rigs and future newbuilds. The energy storage system has demonstrated exceptional performance in diverse ambient conditions and altitudes.
Quantitative lithotyping from cuttings: a cost-effective alternative to coring
CGG Geoscience continues to develop advanced cuttings analysis workflows with the addition of RoqLith to its RoqScan deliverables. The new workflow capitalizes on the imaging and elemental interpretation capabilities of RoqScan, an automated portable scanning electron microscope with EDX elemental detectors, to generate distinct lithotype proportions per cuttings bag. This is important as a cuttings bag is likely to represent multiple lithotypes spread over a 10-ft to 30-ft interval. Other cuttings analysis techniques tend to generate only one lithotype interpretation per cuttings bag and therefore underestimate the heterogeneity of the sample.
The data produced from RoqLith delivers deeper insight into lithology and rock property variations at a much higher resolution than ever before generated from automated cuttings analysis, in both vertical and lateral wells. By calibrating back to a representative core, RoqLith provides a cost-effective alternative to further coring within the asset. It also complements CGG’s earlier release of RoqLog, a workflow for generation of pseudo-elastic logs (Young’s Modulus, Poisson’s Ratio) and rock weakness curve from cuttings that help to optimally design completions and predict borehole breakdown pressures throughout the lateral well.

On-demand well operations platform scales to match drilling needs
Producers looking to rapidly scale operations, drive capex down and extract maximum production returns can rely on Corva’s on-demand operations platform. A hybrid combination of technology, process and people, the platform provides operators with real-time data and analytics for optimizing operations across the well life cycle as well as a Houston-based 24/7 operations center that supports customers with a team of drilling optimization experts. Featuring a suite of more than 100 apps and dashboards, Corva’s ecosystem of engineering tools optimizes capital spending and increases operational performance, including crew operations, directional drilling, geosteering, wireline, stimulation and drillout. All are available in a single workspace accessible on the web and mobile devices. Corva’s on-demand platform enables operators to do more with a leaner team, reduce drilling projects by days through optimized ROP and slide percent, precisely steer laterals along the pay zone, accelerate wireline work and optimize frac treatments.

Tool provides answer to high-torque challenges
The recently introduced Frank’s International Drill Pipe Torque Reducer (DPTR) tool offers a powerful, clamp-on solution to the excessive tubular wear and high torque experienced in complex and demanding drilling applications. It was developed to address the challenges of long lateral environments and the dynamic forces of aggressive openhole operations. As the new, modular cousin of the DSTR Drill String Torque Reducer, the DPTR tool provides an answer to the high-torque challenges posed by extended-reach drilling and extreme tangent sections in shale plays.

The DPTR tool is designed and manufactured to withstand more extreme downhole conditions than other clamp-on torque reduction technologies, and it has an axial holding force of 30,000 lb and a lateral force capacity of 5,000 lb. It attaches to the outside diameter of the drillpipe. Inner steel clamps remain stationary on the drillpipe tube body, while the outer sleeve halves are coupled together around the inner clamps. During operation, the inner clamps rotate with the drillstring while the outer sleeve remains stationary against the sides of the wellbore, limiting the contact between the wellbore wall and the drillstring and preventing wear on previously installed casing.
A recent field trial showed a substantial reduction in torque, and the same customer is utilizing the DPTR tools while drilling their next well.
New offerings increase efficiencies
Logan Industries recently introduced a mobile service truck to address the shortage of readily accessible frac site provision within the 100-mile radius of Midland, Odessa. Logan’s service truck is outfitted with all required tools and spares for the most common hydraulic troubleshooting and light repair work. With a crew of three on rotation and a service manager located in Hempstead, Texas, Logan delivers quality repair services to customers in remote locations, enabling them to perform their frac site operations safely and efficiently every day of the year.
To further support the shale market, Logan has developed and patented a catwalk pipehandler “kicker” cylinder that fully loads the pipe onto the catwalk every time. In fact, 10,000 ft of pipe equates to 333 pipe joints, and on average, a kicker problem occurs on every third joint. Each time this happens, the rig loses about 5 minutes, which equates to about 9 hours of built-in downtime, simply because the machine does not work efficiently. The new kicker cylinder serves as a direct/drop-in replacement of current original equipment manufacturer supply and features a faster speed to load pipe, increasing efficiency for rig operations and reducing downtime.
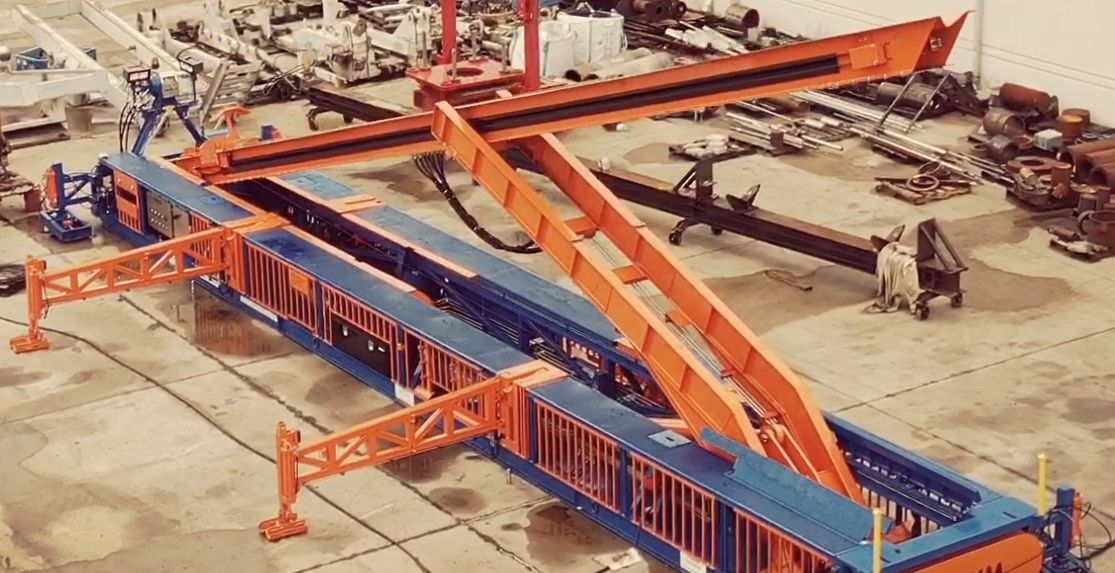
Chemical stratigraphy as a tool enhances wellbore placement
Accurate horizontal well placement is critical in the development of shale plays. The combination of close well spacing and extended-reach horizontal wellbores, which are commonly drilled to more than 10,000 ft, increases the risk of being able to identify the pay zone accurately. RPS’ wellsite chemical stratigraphy services are highly effective in resolving subsurface strata to support critical decision-making during wellbore placement. The services provide a backup spectral gamma ray data source in an environment where increased pressure can lead to downhole tool failure. The net result is a reduction in subsurface uncertainty. Using a robust synthetic gamma ray requires no legacy data and can be applied from the onset of drilling. A chemical stratigraphic framework can be constructed from one or more offset wells. A combination of these techniques delivers valuable insight into reservoir correlation and aids in maximizing the reservoir.
Ridged diamond element improves ROP

The Axe Ultra ridged diamond element builds on the AxeBlade cutting element bits from Smith Bits, a Schlumberger company. Launched in 2020, the ridged diamond element features a new interface between the diamond table and carbide substrate, resulting in increased cutting efficiency in hard and brittle rock types, while increasing cutter life and improving durability.
Since 2016, AxeBlade bits have been used in more than 13,000 runs in unconventional U.S. and Canadian shale basins. The ridged diamond cutting element was developed after a large volume of accumulated runs that enabled the review of thousands of used Axe cutting elements to better understand how the cutter could be further improved.
The new interface results in lower stress levels to increase its strength and reduce impact-related cutter damage such as breakage and delamination. Improving the overall strength of the Axe element ensures that bits drill for longer intervals and sustain higher levels of ROP to save drilling time and costs for operators.
A Permian Basin operator used a PDC bit with the ridged diamond element to drill a 2-mile, 6¾-inch lateral section across the Wolfcamp Formation and improved ROP by 18%.
Soy-based drilling lubricant soluble in water and oil, reduces torque and drag

Synalloy Material Science Group’s BioLube SD is a novel drilling lubrication technology based on soybean oil. This chemistry is soluble in both water and oil, brine tolerant, biodegradable, low foaming and highly effective in reducing torque and drag.
BioLube SD is engineered to be broadly adaptable to a wide range of applications and geological challenges.
Because it contains renewable vegetable content in excess of 98.5%, it is a logical choice for environmentally conscious companies, restricted areas, where drinking water is affected or offshore drilling in consideration of aquatic life.
Biolube SD can be used as supplied or as an intermediate with which to compound specialty formulations.
BioLube SD is formulated from U.S. grown soybean oil with quantifiable direct benefits to U.S. farmers.
BioLube SD, and variations, also have impact in certain demanding metal working applications. The flexibility to use as an oil or convert to a water emulsion is a sought after feature by many formulators.
New microelectronics enhance downhole drilling automation
In 2005 Tomax patented a downhole regulator with the intention of optimizing the bit to rock interaction downhole. The invention was named Anti Stick-Slip Tool (AST). The AST did well and surpassed expectations by consistently improving drilling efficiency. But sometimes most of the rotary energy is used to overcome friction instead of cutting and the AST benefits are not observed. To change this and make the industry able to differentiate between productive drilling and waste to friction, Tomax has initiated the Tomax Energy Monitoring (TEM) project. The TEM recordings will reveal if the bit makes a cut deep enough to make the AST effective or if the cut is marginalized by friction. The TEM is based on new, cost-efficient, one-wire microelectronics. Although simple, the output is reliable and will end the guesswork on bit strategies.

COMPLETIONS >>>
Acoustic imaging tool captures data sent to the surface in real time
DarkVision’s HADES-F technology uses a next-generation high-resolution acoustic imaging head mounted on an articulating robotic arm. The arm is remotely controlled by a technician on site and captures data that are sent to the surface in real time. This allows imaging of a target area from multiple perspectives and can be deployed on any well regardless of fluid clarity. Operators gain dimensionally accurate 3D views with resolutions of 0.1 sq mm that can be used to create computer-aided design models or 3D printed reconstructions of the area of interest. The technology can be applied to fishing or wellbore obstruction jobs as well as to any area where detailed measurements and images are required for improved diagnostics. This includes well integrity applications like inspecting casing, connections, flow control devices, valves, inside diameter (ID) restrictions and deformations.
Additive designed for high-temperature formations and high-flow-rate wells

Hexion has released its VFC-2000 additive, a new on-the-fly proppant flowback solution designed for high-temperature formations and wells with high flow rate. This liquid additive is added directly to the blender tub with any type or mesh size proppant. The resin chemistry latches onto the outside of the proppant grains and forms grain-to-grain bonds. T
he PropShield proppant flowback control additive was released in 2018 and has been successfully used in more than 150 wells. While the PropShield additive has an upper application temperature of 215 F, the VFC-2000 additive’s chemistry is designed for higher temperature formations up to 350 F.
This technology is being field tested in North Dakota with additional field trials expected in the Bakken and Haynesville in the coming months.
Biosurfactant technology boosts production and EUR
Biosurfactants have proven to outperform traditional treatments in well remediation and EOR. Now they’re being used as a highly effective technology for shale completions to mobilize otherwise immobile oil and improve flowback performance—immediately increasing revenue streams while improving EUR. Known as SUSTAIN, the newly launched green products from Locus Bio-Energy Solutions comprise multifunctional biosurfactants that sustainably boost the performance of completion fluids. Unlike synthetic surfactants, SUSTAIN penetrates and adsorbs onto reservoir minerals, altering the rock wettability and reducing surface tension, at less than 1/50th of the typical synthetic surfactant dosages. Up to 50% of the biosurfactant is adsorbed by the minerals in shale reservoirs and then slowly desorbs over weeks and months, ensuring long-term positive impacts on fluid properties and production rates after flowback.
Improving completion efficiency with hydraulic toe subs
Once somewhat of a novelty, extended-reach laterals are being drilled at a greater pace across North America. These longer laterals have helped increase stage counts and achieve greater reservoir coverage—typically resulting in higher production—yet it hasn’t come without challenges. One challenge is effective stimulation at the toe stages of a well. Operational challenges and risks arise when using tubing-conveyed perforating for the first stage of completion operations just by the nature of the extreme distance the tools must travel downhole. Although hydraulically activated sliding sleeves were introduced to solve this challenge, reliability has been an issue and many operators have been forced to run multiple sleeves as a precautionary measure. Packers Plus recently released a suite of tools to run at the toe of horizontal wells that addresses challenges by decreasing risk with interventionless operation and increasing reliability: TREX Wet Shoe Sub, TREX Rupture Disc Sub, Toe-AP Hydraulic Sleeve and Toe-XT Testable Hydraulic Sleeve. Combining these toe options with sliding sleeve completion technology can further expedite completion time and bring wells online quicker.

Wet sand system lowers capital and operational costs

The PropX Wet Sand System is a novel method that was introduced to the oil field using equipment to screen, transport, deliver and meter wet sand from local mines to the frac blender, bypassing the drying process altogether. This process has successfully delivered more than 500 MMlb of sand downhole to date. There are many ways pumping wet sand can provide value: lower capital costs, lower operational costs, reduced regulatory complexity, enhanced plant storage efficiency, lower energy input and emissions, and reduced fugitive silica dust in the air. If the total sand supply chain could be redesigned from scratch with the knowledge that sand could be delivered and metered to the blender prior to drying and processing, what would that supply chain look like?
Optimize a completion design for a target fracture geometry
A Permian Basin operator needed a completion design that would generate fracture geometries closest to a target half-length, based on an upcoming pad’s well spacing. The operator’s pressure-based fracture measurements, loaded into Reveal Energy Services’ DSCVRi cloud-based completion evaluation engine, enabled the solution. The operator, working with Reveal Energy Services and the DSCVRi platform, binned the stage-level datapoints into high, medium and low ranges of pumped proppant and fluid volumes, as shown in the scatter plot. Box-and-whisker plots displayed the means and ranges of each completion design group’s fracture half-lengths. The operator selected the group with the mean closest to the target fracture geometry and chose the smallest standard deviation [1-1] to optimize the completion design. The DSCVRi database offered easy access to and interpretation of the empirical data. Going forward, the operator can customize each design using the DSCVRi platform.

Technology alerts operators on poor perforation efficiency stages
Seismos-CONNECT leverages a new acoustics-based technology to measure perforation tunnel efficiency right after wireline perforates a stage and prior to pumping commencing. The technology alerts operators on poor perforation efficiency stages enabling timely mitigation action, eliminating nonproductive time (NPT) and ensuring proper stimulation. Poor perf to reservoir coupling can lead to abnormal pressure patterns, nonuniform fracture propagation, difficulties in placing proppant and eventually screenouts. Existing perforation analysis technologies (i.e., fiber) can only provide information once pumping has commenced and after the perforations have started taking fluid. However, waiting for pumping to commence and for the abnormal pressure patterns to occur before taking action can cause irreversible damages to the fracture system and typically leads to incremental NPT.
With Seismos-CONNECT the operator receives an accurate reading (historical accuracy at 98%) piror to pumping, enabling mitigation action. The product is easy to deploy and involves a small hardware configuration connected to the wellhead on surface. Seismos-AI is a data-driven machine learning platform leveraging real-time fracture measurements, completions data and reservoir information to develop the ability to identify the point of diminishing returns for each completion design variable. The machine learning interface generates custom completion designs that optimize the return on expense. In one study, Seismos-AI identified that pumping more than 170,000 lb of 100 mesh had a negative effect on fracture length and only added extra cost.

New service for field management of fracturing chemicals
Solvay has released its TankIQ system for enhanced field management of its chemicals across all major U.S. basins. This service centers on an advanced telemetry system specifically designed by Solvay to meet the demands and challenges of a fracturing site. A reliable satellite connection delivers a full view of product location and a to-the-gallon volume reading through a secure portal that can be accessed from anywhere at any time. Custom reports are used to track usage trends and alerts set to make sure volumes of critical chemicals are always on location. Products are delivered by well-trained, dedicated drivers in specialized, lined tankers that can be fully operated at ground level to ensure crew safety. The larger volume of the tankers has been proven to reduce onsite truck traffic as well as the number of deliveries and transfers to optimize supply chains and costs.

Technology delivers cost-effective isolation for refracturing

Tendeka’s SwellFrac uses swelling elastomer technology to isolate existing fractures in oil and gas wells while maintaining full internal diameter allowing the well to be refractured. Sized swellable elastomer particles are pumped in an aqueous slurry from surface into the existing perforation tunnels immediately creating enough pressure differential to cause diversion ensuring that all existing perforations are affected. In-situ swelling then creates an effective high-pressure seal to enable refracturing operations to take place in the wellbore.
SwellFrac’s water swellable particles use a combination of super absorbent polymers and osmotic swell mechanisms to optimize speed and strength of the swelling process and maximize chemical resistance. Because the SwellFrac material seals inside the perforation tunnel are chemically resistant, the risk of erosion and/or dissolution during the refracturing process is minimized. The internal diameter of the existing completion is fully maintained allowing standard plug sizes to be used and multiple refracturing operations to take place as subsequent production decline is experienced with time.
Frac hit mitigation chemical technology
TenEx Technologies’ NoHIT is a frac-hit mitigation chemical technology via in-situ gradual and continual pressuring of depleted reservoir intervals around a parent well. When injected with a recharge fluid (preload or active load) into the parent well, NoHIT produces a slow in-situ exergonic gas-generating reaction when promoted with selective activators at reservoir conditions. Test data showed the reaction also could improve parent well productivity as the proppant pack permeability/conductivity was significantly increased at moderate-to-high closure stresses. In a field pilot test on a multistage horizontal well, NoHIT was proven to be very simple and safe to pump using typical oilfield pumping procedures. With only 600 bbl of produced water and 900 gal of NoHIT, the bottomhole pressure (BHP) exceeded virgin reservoir pressure for about 24 hours and continued to exceed prejob BHP for nine days.

Service helps operators optimize cluster efficiency
Well Data Labs’ Sealed Wellbore Pressure Monitoring (SWPM) service combines the power of its machine learning platform with technology pioneered by Devon Energy. The SWPM service helps operators optimize cluster efficiency by serving as a faster and inexpensive option within the hydraulic fracture diagnostic toolkit. Clients utilizing this service will receive a detailed report that includes visualizations of fracture half-lengths, volume to first response, diffusion curves and dominant fracture apparent diffusivity. Devon has proven through its work that this technology can serve as a proxy for fiber optics, making this a powerful, cost-effective alternative for operators. At present, this service is provided as a post-job analysis following well completion operations. Real-time analysis is expected to be available for clients this fall.


In-well surveillance optimizes fracturing operations
FiberLine Intervention (FLI) from Well-SENSE is a single-use, plug-and-play, well surveillance technology that allows operators to quickly investigate a variety of well conditions using high-definition, thermal and acoustic profiling.
FLI’s rigless, self-contained fiber-optic sensing system is deployed by one engineer and in some cases directly by the customer with remote support.
FLI can access vertical, deviated and horizontal wells and can help shale completion and fracturing operations by monitoring strain events in adjacent wells during the fracturing process. By doing this, FLI can identify optimal pressure and fluid use and ensure no crossover or breakthrough between neighboring wells.
FLI also can assess perforation and completion design effectiveness and identify integrity issues. It can provide location accuracy within 1 m of depth resolution to register and monitor acoustic events.
FLI can be delivered faster than wireline methods and answers the industry challenge to reduce costs, personnel and the carbon footprint of wellsite operations.
PRODUCTION >>>
Plunger lift automation provides production optimization at scale
With fewer new wells coming online, every barrel, every thousand cubic feet, every hour of downtime matters more than ever to a company’s bottom line. Well optimization has become a top priority, but production engineers’ toolbox has not seen an upgrade in decades.
Using cloud computing, Ambyint technology automatically sorts and analyzes large volumes of data in real time. Patterns and priorities are applied based on the operator’s specific criteria such as production rates, pressure or detecting paraffin problems. Anomaly detection starts with data about the well and completion design. Once these fundamentals are defined, Ambyint’s algorithms continuously scan customer data, applying artificial intelligence and a full physics engine to characterize the well’s performance. The wells that need attention are immediately presented on a single software screen. This detection is focused on the most common issues in plunger wells that can lead to bigger issues if not resolved. The software further identifies anomalies in terms of what can be automatically fixed (i.e., set points or remote changes) and where human intervention is required (e.g., a mechanical surface issue or worn plunger that needs replacement). Surfacing anomaly insights save valuable time by revealing which wells need immediate attention.

Paraffin additives help resolve issues found in heavier crudes
As well conditions become more challenging with a wide variety of crude characteristics, the need for novel technology to address these issues continues to grow. The issues that are manifested from paraffin deposition, downhole and topside include higher fluid viscosities that affect pump pressures, lower operating efficiency and the blockage of hydrocarbon flow. A variety of paraffin inhibitors and/or pour point depressants are utilized in the field to assure the flow of hydrocarbon; however, due to extreme variations in the properties of crude oil, this leads to a range of product efficacies and dosage levels. BYK’s BYK-GO 8710 and 8711 paraffin additives can help resolve the issues found in heavier crudes by reducing the pour point and paraffin deposition with lower dosages and higher efficiency. BYK-GO 8710 and 8711 are optimized for performance in challenging crude types, such as those with higher wax content and may well be highly beneficial for increased production efficiency and less production downtime for the mechanical removal of paraffin buildup.

Accessing accurate multiphase flow measurements

Shale operations require accurate, reliable and cost-effective oil and gas flow measurements. Emerson’s Roxar 2600 Multiphase Flow Meter (MPFM) provides accurate measurements in flowback operations and initial, mid- and late-life shale production. The version 2.6 flow computer software release, launched in January, helps to solve operator challenges in accessing accurate multiphase flow measurements.
A challenge in shale operations is wax layer deposits, which require meters to undergo periodic cleaning. The Roxar 2600’s software includes an insulating layer compensation feature designed for continuous oil flow, which enables increased measurement robustness and reliability, and reduced cleaning.
Production with high gas fractions is common in shale. The software improves the annularity correction model for gas volume fractions of 90% or above, ensuring higher performance in challenging conditions.
Finally, the software provides a complete pressure, volume and temperature calculation engine. In addition to actual and standard conditions, the software includes two new flashing stages with measurement outputs provided at specified pressure and temperature conditions, making comparisons and verification straightforward for operators.

(Source: Halliburton)
Unconventional well test data retriever
Halliburton has released the SPIDRlive self-powered intelligent data retriever, an unconventional well testing and fracture interaction monitoring technology that acquires real-time well data without the need for intervention to reduce costs and improve fracture understanding for higher recovery.
The SPIDRlive retriever combines quartz-based hardware and modeling software to capture high-resolution, high-accuracy and high-frequency data from the wellhead without running downhole equipment. In unconventional wells, operators can acquire data to optimize fracture design or perform an engineered flowback to improve well performance. In multiple wells, operators can utilize the streaming capability for remote monitoring of fracture interactions in offset wells.
In West Texas, an operator recently deployed the technology on multiple offset wells to monitor for fracture interactions. During the fracture treatment, SPIDRlive transmitted data via a wireless signal to a field edge device and then streamed into a secure cloud application for the client to visualize. The streaming data indicated an interaction on a neighboring well pad alerting the operator of potential consequences during their production optimization campaign.
Metering pumps simplify operation and maintenance

Hydraulically actuated diaphragm metering pumps, like Pulsefeeder’s PulsaPro, are positive displacement pumps that deliver flow assurance chemicals and scale inhibitors in precise volumes within 1% accuracy or better.
PulsaPro metering pumps inject precise volumes of flow assurance chemicals to increase recovery rates and protect equipment.
Oil, gas and unwanted debris must be separated before the product enters pipelines. During separation, liquid hydrocarbons can become unstable, which can reduce “flow-ability.” To remedy this, various asphaltine and paraffin inhibitors are metered in specific doses using metering pumps, such as PulsaPro. Accuracy matters, because these chemicals are expensive, and injecting too much upstream requires removal downstream.
When it comes to selecting a metering pump for upstream applications, strict adherence to API-675 standards is required. PulsaPro is the only metering pump that meets API-675 specifications without exceptions. This makes it quicker and easier for original equipment manufacturers to procure PulsaPro pumps and incorporate them into skids that are built and deployed to job sites.
Surface sand management at a fraction of the footprint and opex

Sandtinel, Frac Shack’s sand separation business, has released the Maverick sand separator for use in flowback and production operations.
Recent years have seen a push for finer sand, sourced in-basin, with high crushability. This sand causes problems downstream, including erosion, backpressure on the well and accumulation in tanks.
The Maverick was designed by leveraging simulations with computational fluid dynamics together with field testing, case studies and validation. It has been proven to remove more than 95% of sand as small as 100 mesh across a wide operating envelope (rated up to 10,000 psi), up to 9,500 bbl/d, with no turndown.
Separation is achieved through purely mechanical means (no filters, moving components or replaceable elements). It has consistently outperformed competing solutions by removing 10% to 60% more of the total sand on site.
The phase separation also reduces emissions during dumping; simulations and field results have shown reductions in emissions of up to 55 times compared to competing solutions.
Nonintrusive level measurement of chemicals
When the oil and gas production sector is thriving, the amount of water for production projects is immense, and in the world of water treatment and recycling, water quality has become more stringent. Due to the corrosive nature of the chemicals used in the treatment process, chemicals are stored in plastic totes. The challenge with these containers is that manual intervention is required to determine on-hand inventory or delivery quantities. Furthermore, these vessels do not have process connections for instrumentation. With the new Siemens SITRANS LR110 80-GHz radar transmitter, nonintrusive level measurement is possible. The instrument can be simply put on top of a plastic tote to monitor the level inside. The risks of running out of chemicals or any liquid or paying too much for erroneous amounts is eliminated. Setup is easy with Bluetooth technology and its low power requirement makes this transmitter practical for battery-powered operations in remote locations.
New rod coupling reduces friction and increases efficiency
Stinger Oil Tools, a division of Drilling Tools International, has developed a sucker rod coupling called the Roller Coupling to help reduce friction. The system can maneuver 360 degrees, allowing the Roller Couplings to reduce side loads, torque and drag while lowering friction coefficients to 0.005 per friction reduction unit. The company’s engineered placement analytics will help users apply the correct amount of Roller Couplings in troubled areas. The Roller Couplings reduce wear on the sucker rods, tubing and surface equipment. A proven well in the Bakken has been producing more than 225 days while showing a 20% increase in downhole stroke length.

Platform collects and aggregates millions of datapoints from disparate field assets
WellAware 2.0 is an interconnected mesh of smart devices that reengineers production operations automation on the edge, connected to the cloud and connected locally with other smart devices. The platform enables the configuration of smart devices via templates, making it possible to configure a large collection of devices at scale, in turn eliminating hours spent on the field to configure devices or manage individual connections using tags. This blurs the lines between edge and cloud by deploying core performance code in distributed environments creating a secure mesh of smart devices, with permission to access regardless of organization or team. Decentralized processing provides edge compute and real-time controls for managing high-intensity operations, including artificial intelligence. The cryptographic security framework blocks intrusion without hindering productivity and the patented mesh architecture enables WellAware to offer a Data-as-a-Service subscription model while implementing a fully scalable technology across a few assets to millions of assets.

WATER MANAGEMENT >>>

Quality control testing of slickwater fracturing fluids
Measuring fracture pressure of fluids as they flow through different pipe geometries is a serious procedure. Chandler Engineering has designed a new benchtop unit that can determine the relative effects of friction reducer chemistries and treatments. The unit is ideal for quality control testing of slickwater fracturing fluids.
The 6500-M Mini-Loop benchtop instrument allows rapid test turnaround for the repeat testing of stimulation fluids. It circulates fluid through a single test section and uses custom Chandler Engineering software to record and analyze the test data. This enables reliable testing in a simple-to-operate compact system.
Advancement in produced water controls

Water Standard’s produced water subsidiary, Monarch Separators, designs, engineers and manufactures technologies for oil-water and solids-water separation. The companies’ water treatment platform H2O Spectrum platform technology provides operators a variety of affordable produced and flowback water treatment to safely and responsibly reuse water as an asset in operations and/or safely discharge it back into the water cycle. As part of their water treatment platform H2O Spectrum technology, the company has deployed a progressive control platform. The code that has been developed optimizes more advanced produced water treatment process controls for biological and chemical treatment processes including oxidation, coagulation and flocculation for reuse applications, which can be prone to upsets, are susceptible to significant operational cost changes from overdosing and require significant operator intervention to manage upsets. These control solutions improve product integrity and simplify the operation of the systems for the end user.
View last year's Shale Technology Showcase.
Recommended Reading
E&P Highlights: Jan. 13, 2025
2025-01-13 - Here’s a roundup of the latest E&P headlines, including Chevron starting production from a platform in the Gulf of Mexico and several new products for pipelines.
Judgment Call: Ranking the Haynesville Shale’s Top E&P Producers
2025-03-03 - Companies such as Comstock Resources and Expand Energy topped rankings, based on the greatest productivity per lateral foot and other metrics— and depending on who did the scoring.
E&P Highlights: Jan. 21, 2025
2025-01-21 - Here’s a roundup of the latest E&P headlines, with Flowserve getting a contract from ADNOC and a couple of offshore oil and gas discoveries.
Cummins, Liberty Energy to Deploy New Engine for Fracking Platform This Year
2025-01-29 - Liberty Energy Inc. and Cummins Inc. are deploying the natural gas large displacement engine developed in a partnership formed in 2024.
E&P Highlights: March 31, 2025
2025-03-31 - Here’s a roundup of the latest E&P headlines, from a big CNOOC discovery in the South China Sea to Shell’s development offshore Brazil.
Comments
Add new comment
This conversation is moderated according to Hart Energy community rules. Please read the rules before joining the discussion. If you’re experiencing any technical problems, please contact our customer care team.