Anyone who has engaged in hydraulic fracturing in unconventional basins is aware of the ‘jungle of iron’ at the well site that poses numerous challenges to equipment reliability, HSE, well site footprint, flow rates, and nonproductive time (NPT). These iron jungles and the challenges they pose stem from the fact that conventional fracturing fluid delivery systems are constructed primarily of multiple, connected frac iron components. Conventional treating iron systems require more than 50 connections per well from the zipper manifold to the frac tree. During operations, NPT is associated with fluid leaks through the connections. The leaks are not easy to spot on frac iron and create delays and risks when people are required to “chase” them. The more connections there are, the higher the risk.
Since 2018, MonoFlex* dual-connection fracturing fluid delivery technology has been building a track record for successfully addressing these challenges and improving operational efficiency and safety in shale basins. Operators have used the technology, which is based on flexible pipe as an alternative to conventional iron, in more than 5,000 wells to connect frac trees with zipper manifolds and trunk lines. These operations have been 100% successful with no downtime or NPT due to fluid delivery system failure reported. The fracturing fluid delivery technology can also be used to connect frac pumps with the frac missile and on the pump-down side for perforating operations.
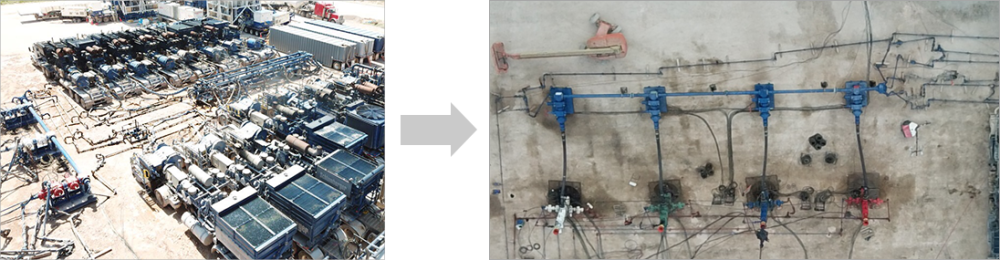

Finding a better way
Cameron, a Schlumberger company, has been finding ways to optimize the fracturing fluid delivery system since 2014, when it released the Monoline* flanged-connection fracturing fluid delivery technology. In 2016, the company sought further improvements for simpler setup on location with less equipment that is safer to install and manage. A key tactic for achieving this goal was to eliminate the ‘jungle of iron’ typically used with traditional frac fluid delivery systems.
Key features identified during the product planning phase included the following:
- A stronger connection that is resistant to the abrasiveness of the proppant in fracturing fluid;
- Flexibility to accommodate different pad configurations; and
- The ability to perform inspections quickly in the field to enable rapid movement of equipment from one field location to another.
The resulting dual-connection fracturing fluid delivery technology features a robust and flexible high-pressure system with only two connections—a significant reduction versus the numbers required per well with conventional treating iron systems. This key technology eliminates the potential to mismatch equipment, simplifies pad setup, eliminates excess flowlines, decreases NPT by reducing the number of possible leak paths, and reduces operating expenses and HSE risks. Eliminating the leaks reduces environmental risk by preventing the frac fluids from being discharged to the atmosphere. Environmental benefits also include a cleaner and reduced footprint and reduction in pump horsepower consumption.
Mobilization, demobilization and time to first production are expedited because of the small number of connections and the flexibility of the system. Some operators have reported average savings of 75% on rig-up and rig-downtime versus traditional iron systems, and field teams can rig up in very short time, even in tight-spaced locations where rig-up with “regular” pipe would have been lengthy or very difficult. The system is typically rigged up before the frac pumping crew arrives.
The capability of the system to easily accommodate vertical and horizontal misalignments between the frac tree and the manifold leave a less complicated well site. Additionally, by eliminating sharp turns and multiple flow paths, the technology reduces friction losses by 2%-4%, typically reducing horsepower requirements while still accommodating flow rates up to 160 bbl/m. The higher fluid velocity requires less equipment for long-range pumping rates. Eliminating the turns that the fluid must make compared with regular iron allows the fluid to be less turbulent, which simultaneously reduces wear on equipment and pressure losses due to friction in the system.

The technology eliminates risk associated with traditional high-pressure iron, such as lifting, tripping, accidental discharge, connection separation, and other issues related to the physical activity of handling iron.
Testing and field trials
Before dual-connection fracturing fluid delivery technology was developed, nothing like it had been used before in onshore fracturing operations, specifically unconventional fracturing, which demands continuous operations. Many technical controlled lab and facility tests were performed to demonstrate that the technology met or exceeded industry safety requirements.
The first trials took place in Canada, working with a customer to perform several risk assessments before applying the technology in the field. The field trial began during winter in Canada, which provided a good indication of the technology’s performance under extreme low temperatures. System performance compared with that using regular iron surpassed expectations. After the first successful trial, the customer decided to continue using the technology in regular operations and continues to use it today as part of its frac fluid delivery system.
Case history: cutting iron-related NPT during zipper fracs
PDC Energy develops unconventional fields in the D-J Basin. To achieve maximum efficiency in its hydraulic fracturing pumping operations, PDC fractures an average of 12 wells per pad in up to 6 zipper groups. Because each pad requires an average of 216 pieces of frac iron between the zipper manifold and the frac tree, rig-up is slow, even with four or five extra crew members brought in just for that. The large number of connections also increases the risk of leaks.
To reduce iron requirements and pre-job rig-up time, PDC asked the pressure pumping supplier to rig up the frac iron for one zipper group at a time. This necessitated shutting down the fracturing operation for 16 to 24 hours when it was time to shift the iron to a new set of wells.
Cameron recommended deploying the dual-connection fracturing fluid delivery technology to replace the 216 pieces of conventional frac iron between the zipper manifold and the frac tree with just 12—one for each well. PDC pumped approximately 13,250 fracturing stages through the dual-connection fracturing fluid deliver technology in 2019 and 2020, reducing its iron-related NPT—mostly related to remediating connection leaks—by 2%, to 5%.
Coincidentally, PDC discovered that the technology simplified winter operations. Only one line had to be heated between the zipper manifold and the tree, compared with four to five lines in a conventional rig-up.
Case history: delivering savings in the Permian Basin
For Chevron operating in the Permian Basin, improving overall operational efficiency, operating expense, and wellsite safety for multiwell pads stimulated using abrasive, sand-laden fracturing fluids pumped at 100 bbl/min. meant switching from conventional treating iron to dual-connection fracturing fluid delivery technology. This improved rig-up time and wellsite safety, eliminating dozens of hammer union connections while still enabling 100-bbl/min delivery of abrasive, proppant-laden fracturing fluid. Within 3 months of deploying the technology with one fracturing crew, Chevron added the technology to a second crew. Reduced rig-up times saved the company 4.5 hours per well for a total savings of $108,000 per year. Additionally, the sealing technology improved the integrity of the fluid delivery system, which eliminated NPT related to repairing fluid leaks in hammer union connections.
Deploying the dual-connection technology also eliminated the need for jumper lines and restraint systems, which could have resulted in at least $580,000 in additional cost per year.
Iron jungle tamed
Dual-connection technology significantly reduces the challenges posed by conventional fracturing fluid delivery systems. By eliminating the need for multiple connections per well, operators can realize several benefits during this critical well phase, including reduced environmental impact from fluid leaks, a safer working environment, and more efficient, cost-effective well stimulation operations.
*Mark of Schlumberger.
Recommended Reading
E&Ps Pivot from the Pricey Permian
2025-02-01 - SM Energy, Ovintiv and Devon Energy were rumored to be hunting for Permian M&A—but they ultimately inked deals in cheaper basins. Experts say it’s a trend to watch as producers shrug high Permian prices for runway in the Williston, Eagle Ford, the Uinta and the Montney.
US Drillers Add Oil, Gas Rigs for First Time in Eight Weeks
2025-01-31 - For January, total oil and gas rigs fell by seven, the most in a month since June, with both oil and gas rigs down by four in January.
Liberty Capitalizing on Power Generation as Completions Stay Flat
2025-01-31 - New Liberty Energy Inc. CEO Ron Gusek says company is ‘uniquely positioned’ to deliver modular units for data centers.
Hibernia IV Joins Dawson Dean Wildcatting Alongside EOG, SM, Birch
2025-01-30 - Hibernia IV is among a handful of wildcatters—including EOG Resources, SM Energy and Birch Resources—exploring the Dean sandstone near the Dawson-Martin county line, state records show.
Cummins, Liberty Energy to Deploy New Engine for Fracking Platform This Year
2025-01-29 - Liberty Energy Inc. and Cummins Inc. are deploying the natural gas large displacement engine developed in a partnership formed in 2024.
Comments
Add new comment
This conversation is moderated according to Hart Energy community rules. Please read the rules before joining the discussion. If you’re experiencing any technical problems, please contact our customer care team.