Presented by:
Editor's note: This article appears in the new E&P newsletter. Subscribe to the E&P newsletter here.
What do all workover rigs have in common? From the smaller rod rigs to the largest double-drum big-pullers, they all stand a derrick. This results in the removal of surface parts of the beam pump to accommodate them. These derricks also become problematic when the winds increase and, simply put, elevate operational complexity and overall risk.
A good portion of workover operations can be classified as light remedial, which means they don’t require the use of a derrick or masted apparatus to perform the task because multiple stands of rod or tubing (or both) are not being pulled. Bringing big horsepower and heavy iron to the wellhead is overkill and overtly irresponsible for operations like a polish rod, BOP, stuffing box swap or shallow fishing. The same premise applies to well optimization strategies, such as unseating downhole pumps, providing a chemical flush and reseating. Operators tend to neglect proactive optimization efforts based purely on cost or availability of assets. In these instances, equipment-wise, less is more.
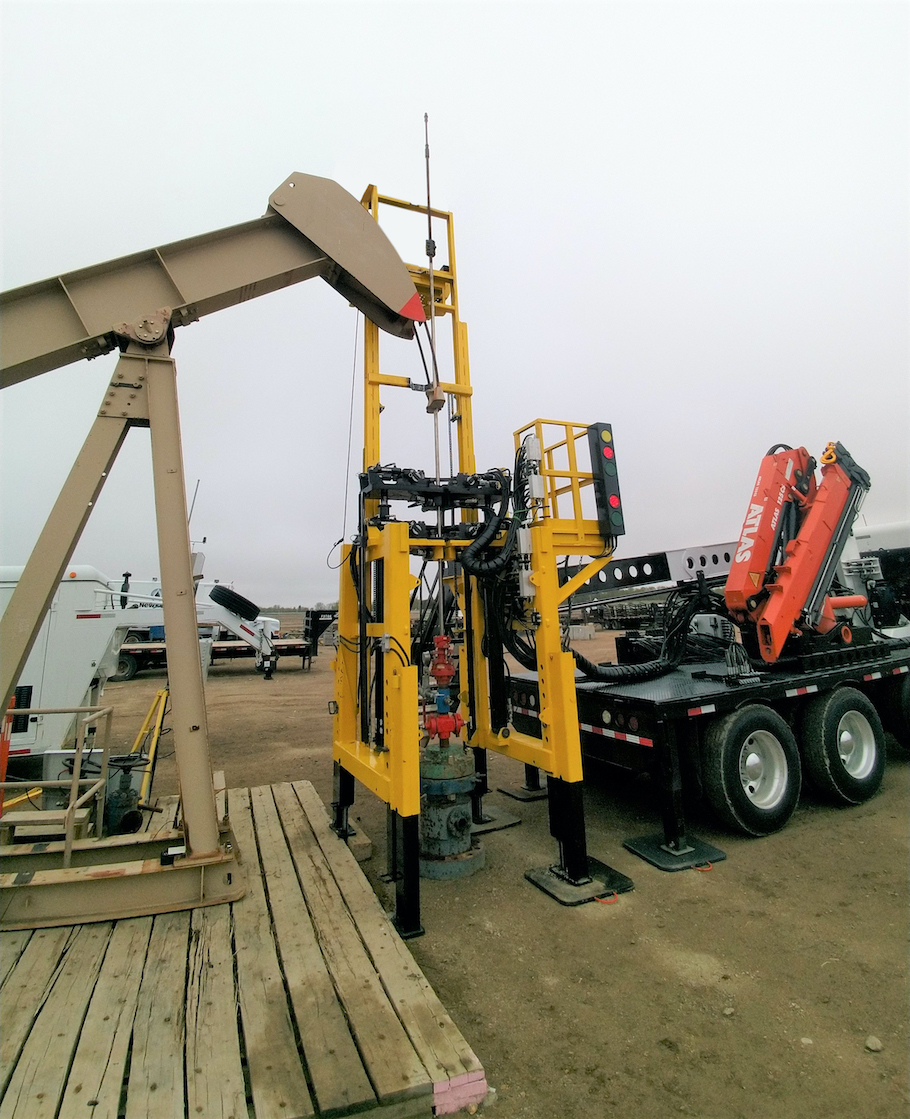
Hydraulic tables, such as NewKota’s Gorilla Jack, are engineered without a derrick and with ESR principles in mind. Those job types listed above can be performed with smaller-footprint equipment designs, fewer men on location and lower horsepower/ more efficient engines to drive the hydraulics—all things NewKota’s Bakken clients have been requesting.
As lean initiatives continue to be the norm, offering efficiency in a service segment that has seen little innovation in the past 50 years, prompted two-plus years of R&D by the NewKota team. With a compact design, all whilst having the ability to pull upward of 75,000 lb (via a slip/die mechanism), maneuvering on and off the wellhead is done in a fraction of the time, also allowing more wells to be touched in a single day. A less than 80-hp deck engine, or hydraulic power unit (HPU), means less fuel consumption, cleaner emissions and reduced decibel levels.
Having heard client concerns about working at height and holding to the smaller footprint mantra, Gorilla Jack V2.0 has an integrated lifting platform that meets all necessary OSHA standards and avoids the need for a separate bucket truck when removing the bridle.
Case study
A major operator in the Williston Basin experienced a rash of polish rod failures. Some of the parted rod(s) remained at surface and others fell as deep as 40 ft. Logistically, it was going to be difficult for the operator to have each well addressed promptly using conventional methods, resulting in an estimated 30-plus days of lost production. The service niche in which the Gorilla Jack exists was able to address those needs with a 100% success rate retrieving each fish and individual operations running as short as 4 hours from start to finish. Downtime for each well was negated by upward of three weeks.
Efficient, safer and cleaner tools
This equipment also provides hydraulic legs for easy adjustment on rigup height. This accommodates a multitude of flowline configurations and removes unnecessary pinch points with manual leg adjustments.
A wireless remote control (or belly pack) allows the operator to move about freely, always achieving the optimal viewpoint for safe operations.
The redundancy option of switching to full manual hydraulic controls, should the operator choose, provides less downtime when electronics need to be calibrated.
Advanced Cat Tier 4 Stage IIIB deck engines (or HPUs) with ACERT technology providing fewer carbon emissions and ease of service.
A custom digital interface allows for set points or kick-outs when client-operating thresholds are reached (set pull weight at 22,000 lb; once this limit is reached, controls lock with a manual override to reset).
Jack dimensions have been thoroughly researched and applied to the design, providing optimal space for personnel when working on the wellhead once the Gorilla Jack is in place. This allows room for the requisite tools to be used all while achieving the necessary engineering standards for the forces being applied when rod manipulation commences.
As commodity prices rise, an increase in fracturing activity is inevitable. The concept of offset well protection will see an uptick accordingly. Whether it is a soft-set or a true well suspension to mitigate cross-communication issues, providing an option other than a crane, rig and/or bucket truck allows this technology to straddle both the completion and production segments of the industry.
RELATED CONTENT:
June 21, 2021: Artificial Lift: HP/HT Pollution Control
June 16, 2021: Artificial Lift—An Uplifting Choice
June 14, 2021: Subsurface Compressors Increase Cash Flow and Generate Attractive ROI
June 4, 2021: Sustainable Advantages in Artificial Lift
May 31, 2021: New Gas Separator Provides Increased Efficiency and Flow Rate
Recommended Reading
Slant Energy Secures Capital Commitment from Pearl Energy Investments
2025-02-25 - Newly formed Slant Energy III LLC has secured an equity commitment from Dallas-based private equity firm Pearl Energy Investments.
NextEra Energy Resources CEO Rebecca Kujawa to Retire
2025-03-18 - NextEra Energy CFO Brian Bolster will become CEO for NextEra Energy Resources, and NextEra Energy Treasurer Mike Dunne will become CFO, the company says.
Origis Secures $1B in New Investments from Brookfield, Antin
2025-01-15 - Brookfield Asset Management is joining Origis Energy’s investor group alongside existing investor and majority owner Antin Infrastructure Partners.
Dividends Declared Week of Feb. 17
2025-02-21 - 2024 year-end earnings season is underway. Here is a compilation of dividends declared from select upstream, midstream, downstream and service and supply companies.
Dividends Declared Week of Feb. 24
2025-03-02 - As 2024 year-end earnings wrap up, here is a compilation of dividends declared from select upstream and midstream companies.
Comments
Add new comment
This conversation is moderated according to Hart Energy community rules. Please read the rules before joining the discussion. If you’re experiencing any technical problems, please contact our customer care team.