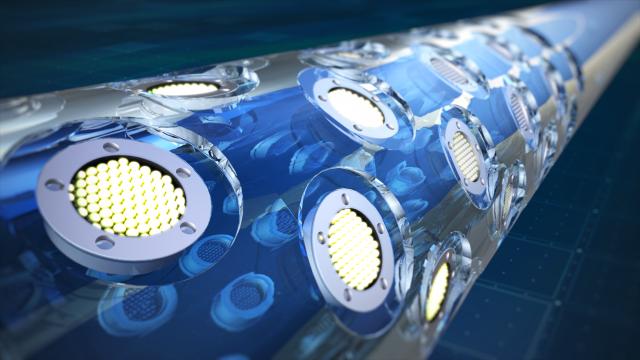
BeadScreen media cartridges are installed directly into the DEEPFRAC multiposition sleeve to provide long-term proppant flowback control with improved reliability over conventional sand screens. (Source: Baker Hughes)
There’s been considerable effort and capital invested into solving the riddle that is the Gulf of Mexico’s (GoM) Lower Tertiary resource trend. Fracturing the Paleogene (as the Lower Tertiary also is called) is a multifaceted obstacle course that includes thick salt layers, high pressures, high temperatures and water depths of more than 1,500 m (5,000 ft) with even deeper tightrock reservoirs at an additional 6,096 m (20,000 ft).
Success stories from fields like Jack/St. Malo, Perdido and Stones have helped demonstrate the industry’s commitment to developing this trend that, according to various estimates, holds about 5 Bbbl of potentially recoverable resources.
Innovative approaches and new technologies helped operators overcome the technical challenges presented by the extreme conditions of the Lower Tertiary. As with most all offshore projects, success comes with significant costs. In the lower-for-longer market environment the offshore industry is facing, finding ways to reduce those costs while increasing returns is a top priority. Improving the efficiencies and economics of offshore completions are two areas where Baker Hughes believed it could make a significant impact.
“We all know that these deepwater wells require stimulation. The economics of oil prices continue to drive the need for a more efficient and effective way to stimulate these wells,” said Jonathan Croy, global product line manager at Baker Hughes.
To accomplish this, the company took a page out of its unconventional playbook and developed, at the request of a major GoM operator, a new multistage fracturing service that offers an alternative to the way deepwater wells are completed.
Challenge accepted
The operator approached Baker Hughes in second-half 2015 looking for new ways to significantly reduce its opex across its Lower Tertiary developments and also explore a radically new completion approach.
The typical approach is to perform a cased-hole multizone frack-pack completion. However, this approach has a reputation for being complex and time-intensive, taking more than a month and at a cost of up to $100 million or more, to case and cement the well, displace fluids and run the upper and lower completion, according to a Baker Hughes press release. More than half of that time is spent on the lower completion phase, including reservoir stimulation. In addition, the complexity of the conventional completions—with extensive tool running procedures and mechanical manipulation— requires increased rig time and opex.
The increased complexity, however, does not result in increased production. It adds weight and creates “dead space” between the individual stages. This results in significant sections of the wellbore being covered, restricting contact with the reservoir and limiting the fracturing treatment to only five zones.
“Basically, the customer came to us with a problem, explained what its team was doing and asked if there was something we could do to improve the process,” said Beau Wright, applications engineering manager for unconventional multistage completion systems at Baker Hughes. “The managers said ignore what we’ve done in the past and do something different, and so that’s where we started. We created and presented the concept to them, asked if it would be something they would be interested in partnering on the development project for and that’s how we got to where we are today.”
Multistage method
That concept turned reality is the DEEPFRAC deepwater multistage fracturing service. Using ball-activated multiposition sleeves found in onshore unconventional applications and patented flowback control technology, the process was simplified, and rapid stimulation of more than 20 stages makes it possible to contact more of the reservoir.
“We looked at our ball-drop actuated sleeve technology as a starting point,” Croy said. “To make it more suitable for deepwater applications, we looked at ways to ensure we had a reliable, long-term solution that would not require intervention later in the life of the well.”
The target well had been drilled to more than 7,620 m (25,000 ft) total measured depth in 3,048 m (10,000 ft) of water. The Baker Hughes engineering teams worked to adapt the technology to meet the operator’s specifications, which included that the completion had to be performed openhole, treat 15 stages in a single trip, provide proppant flowback control without the use of conventional sand screens and enable flowback without post-intervention treatment.
“One way we did this was through the use of IN-Tallic disintegrating frack balls to actuate the sleeves so that we would not have to mill out balls or seats later on,” Croy said. “Another was determining how to control proppant at the reservoir level so there would be no proppant flowback. That’s where the BeadScreen media cartridges installed directly into the frack sleeves were leveraged to ensure long-term sand-free production over the life of the well.”
The DEEPFRAC sleeve has three positions: closed for run-in, ports open for treatment delivery and ports closed with production ports open for flowback. The modular design of the sleeves allowed delivery of the lower completion assembly in only seven weeks as opposed to the average six months for conventional equipment. The openhole completion method eliminated the need for casing and cementing operations and simplified fluid logistics, trimming rig days by more than a week before lower completions operations ever began, according to a Baker Hughes press release.
“With this multistage service, we reduced opex by 40%, increased it from a normal five-stage completion to 20 stages and dramatically increased the efficiency for the operator,” Croy noted.
Also, because of the modular design, each sleeve can be placed as close as 3.9 m (13 ft) apart. This tighter spacing enables a more uniform delivery of the fracture treatment and maximum reservoir contact.
“With this modularity we’re able to provide the operator the ability to space out the fracture treatments based on its well logs,” Croy said. “We can set the system up to correlate with the well logs, so if the operator needs a 20-ft or 30-ft [6-m to 9-m] fracture spacing, then we can set it up to provide better reservoir contact and better fracture for the entire reservoir.”
Wright added that the multistage system provides the operator with more control in determining treatment locations.
“Depending on what your logs tell you—for example, where the natural fractures are or where the shale bands are—the stimulation can be customized to the size needed rather than broken up into five even sections. The system makes it possible to treat in multiple small sections to get more even displacement of your fracture treatment or possibly skip sections that are not of interest.”
According to Baker Hughes, the multistage service delivered to the operator increased reservoir contact and a savings of an estimated 25 days of rig time and $40 million as compared to the average time and cost for a conventional cased-hole multizone completion.
Recommended Reading
TPG to Buy Solar Company Altus Power, Take Private in $2.2B Deal
2025-02-06 - TPG's all-cash acquisition, being made through the TPG Rise Climate Transition Infrastructure strategy, takes the public company Altus Power private at a 66% premium to the company's Oct. 15 share price.
Inpex to Acquire Renewable Energy Portfolio in Australia
2025-02-06 - Inpex Corp.’s JV will acquire a 4-gigawatts portfolio that includes wind, solar and battery energy storage system assets in Australia.
Ecopetrol Closes $452MM Deal for Repsol’s Interests in Colombian Block
2025-02-06 - Ecopetrol has completed a deal with Repsol Colombia Oil & Gas Ltd. to acquire its 45% participation interest in CPO-09 Block—assets GeoPark Ltd. had originally proposed buying.
Gevo Completes $210MM Red Trail Assets Deal for Ethanol Plant
2025-02-05 - Gevo has renamed an ethanol production plant and CCS assets acquired from Red Trail Energy as “Net-Zero North.”
Marketed: Bison Energy 30-Well Package in Niobrara Shale
2024-12-02 - Bison Energy has retained EnergyNet for the sale of a 30 well package in Adams and Arapahoe counties, Colorado.
Comments
Add new comment
This conversation is moderated according to Hart Energy community rules. Please read the rules before joining the discussion. If you’re experiencing any technical problems, please contact our customer care team.