
Fugro’s new remote operations center near Katy, Texas, operates surveying equipment in the Gulf of Mexico. (Source: Fugro)
Remote operations onshore can improve safety and sustainability by reducing the need for people to travel offshore.
Fugro’s newly christened remote operations center (ROC) in Houston is the company’s latest advance, allowing it to perform offshore services without leaving land.
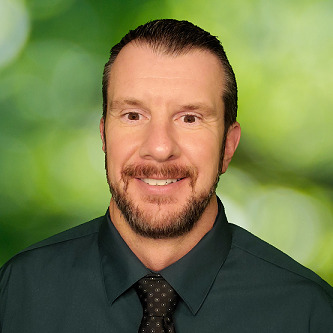
“We have personnel in vessels, but we realized we can take those positions, bring them on land and let them do the same work, but also improve their life because they’re not having to go offshore,” said Michael Cole, service line director of positioning services Americas for the Netherlands-based company, which specializes in geological data onshore and offshore.
Fugro launched its first remote positioning services in 2014, and its capabilities have grown with gains in data transmission. The first operations could support data speeds of only 128 kilobits per second (kbps)—it takes approximately 17 hours to download a 1 gigabyte file at this speed—and now the transmission is almost instant on Fugro’s encrypted network.
Industry adoption took some time, Cole said.
“In the early 2000s, communications technology offshore just wasn’t there,” he said. “And then once they started putting the satellite systems onboard the vessel, we became able to do it, but the bandwidth was expensive. Over time it got down and then in 2012 we took a look at it again and found that we can do this economically.”
The ROC primarily does work on the U.S. East Coast and in the Gulf of Mexico, Cole said. It has also done projects in Alaska, Puerto Rico and Trinidad.
“The technology of the interface is almost like an iPhone app,” he said. “If you look at a survey program, they can be complicated. So we made a simplified version of it with some icons. And as soon as the data is shipped off the vessel and it comes through, we use docker containers to reassemble it inside of the cloud, which then gives us access to the findings.”
On top of that speed of data, a big driver for the ROC is the safety the center provides by removing people from dangerous offshore environments.
In 2015, not long after Fugro launched remote operations, Fugro’s clients had an issue with two vessels in Alaska that they couldn’t reach because of bad weather. One of the vessels was equipped with Fugro’s software, and Fugro pulled the data off the vessel and delivered it to the client in under 10 minutes.
“We even had a client who used to go offshore to do his quality control checks who now does it fully comfortable from his home office, cell phone, wherever he’s at in the world, he doesn’t have to go offshore anymore,” Cole said. “So we’re removing personnel from us and reducing our agency exposure, but we’re also helping the client reduce theirs as well. And they don’t have that lost time by traveling to the rig.”
That brings another advantage: an increase in sustainability and a reduced carbon footprint.
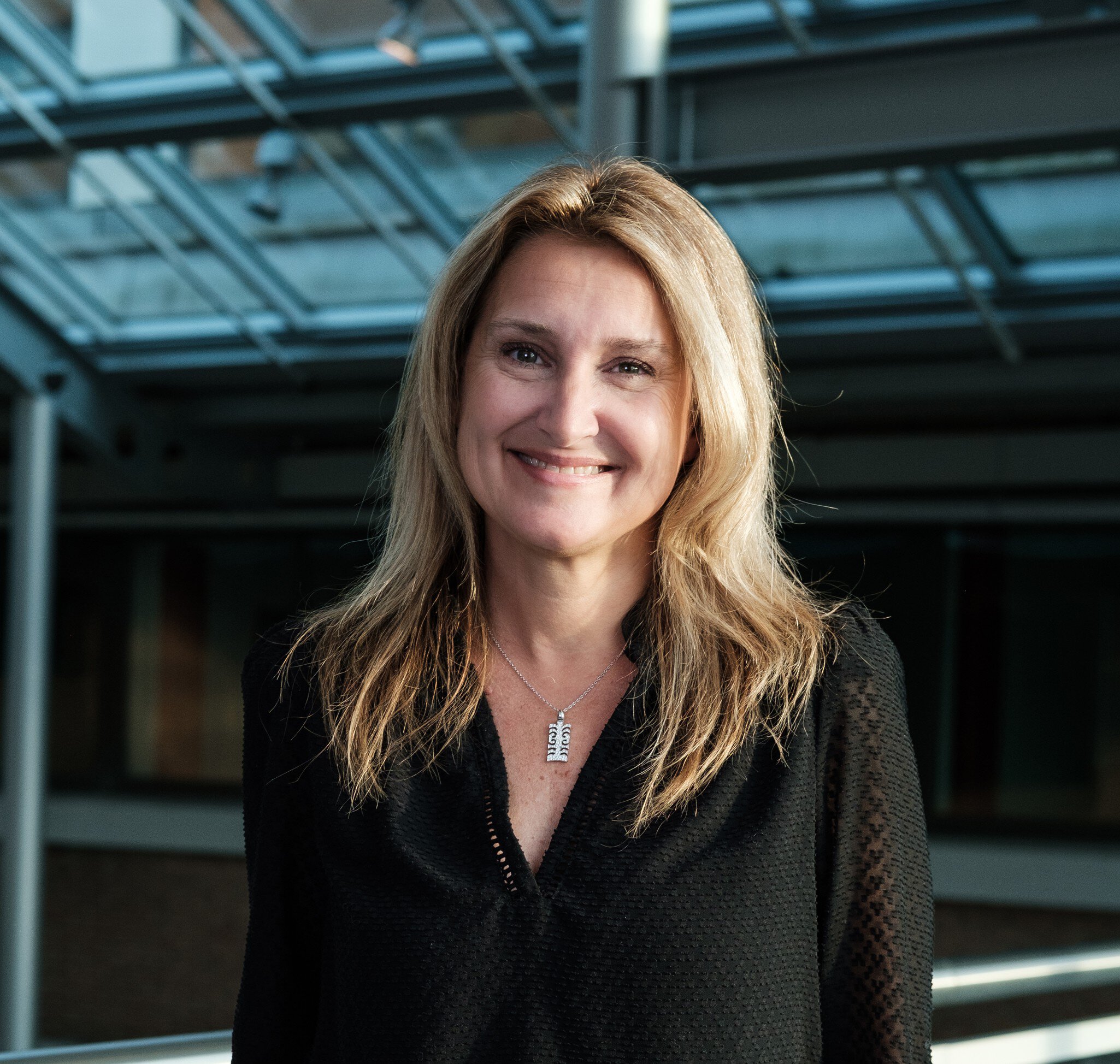
“We’re really capturing the impact from a sustainability standpoint, not having to fly people to those projects all over the world and reducing our carbon footprint as well, which is really something which is a key focus for the company,” said Celine Gerson, Fugro’s president of Americas.
This impact aligns with Fugro’s “net zero by 2035” roadmap, said Gerson, as one of its goals is to become “asset lighter.” Instead of having people working on data processing onboard vessels, crews have less people, which provide more flexibility as data is readily available through remote operations. So teams can work together with immediate access to the data required to provide the proper insight that is required for the specific project, she said.
Cole said there’s another advantage.
“One of the good things is as we perform more items remotely, you’re kind of blending all the services from your group together. It allows you to say, ‘Hey, I need this,’ and whatever you need is instantly put onto your plate,” said Cole.
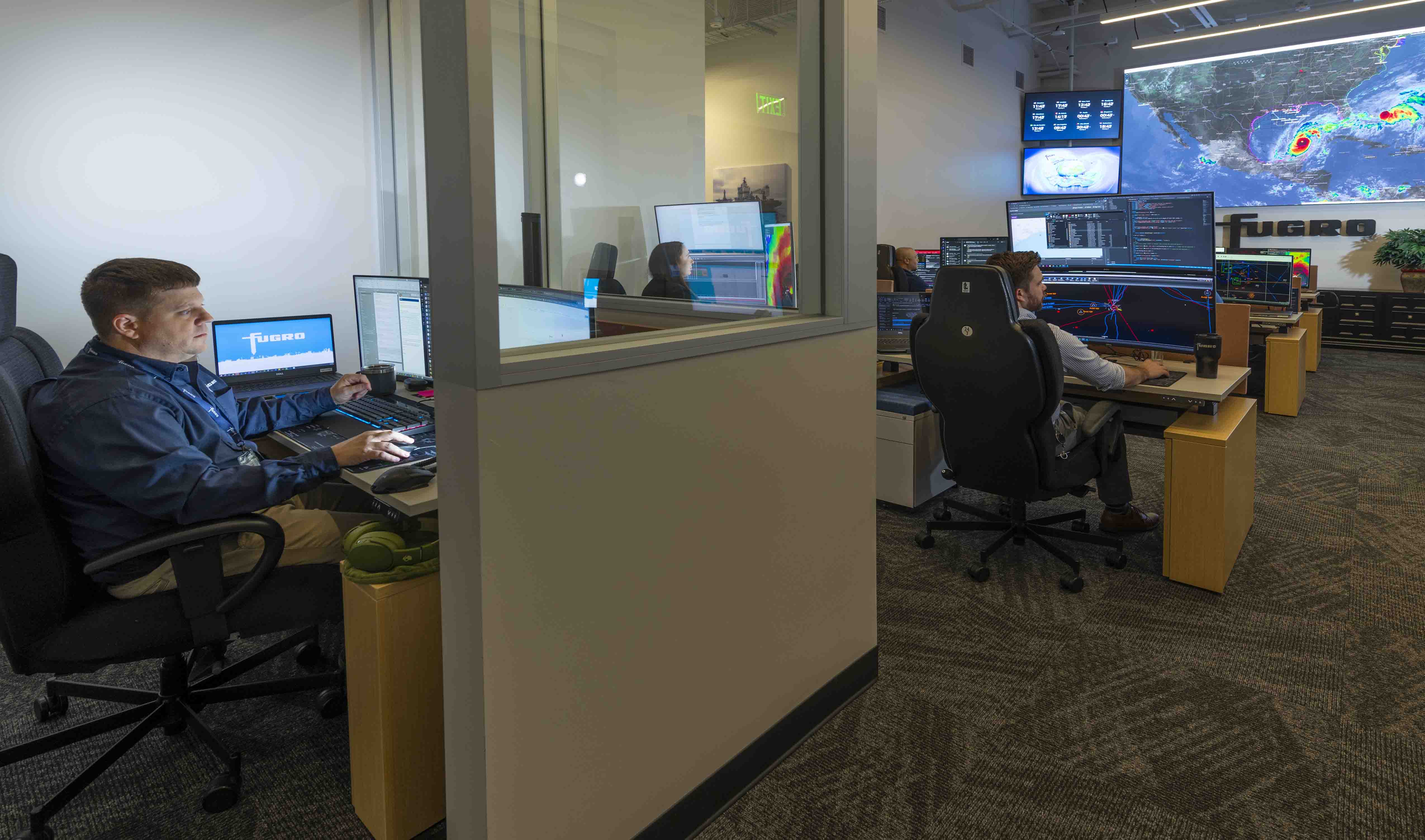
In the future Fugro is looking to have completely remote operations, although both Cole and Gerson acknowledge that goal is a long way off.
“Of course for certain large vessels, it’s going to take a little bit more to be able to replace them with fully uncrewed vessels,” Gerson admitted. “But we have them in Australia where we do subsea inspection work and have them in the Middle East and in the U.K. to look at inspecting infrastructure for offshore wind. We also have the first one coming in Brazil, as it’s on a trial that’s supposed to be a commission before the end of the year. We’re focusing on working with Petrobras for shallow water subsea inspection.”
The company is also looking to downsize vessels in order to reduce its footprint, said Cole.
“Smaller vessels help a lot with what we’re trying to do. Our biggest carbon footprint is the amount of fuel for our larger vessels,” he said. “Sure there are other technologies we put on vessels that can help, but retrofitting vessels is expensive, time consuming and it doesn't always work well.”
In the meantime, the company is focused on its Blue Dragon technology, which looks to revolutionize geotechnical exploration by enabling fully automated seafloor drill performs in situ testing, soil sampling and rock coring in a single dive.
“We’ve focused on the marine environment first because that’s where our hard assets are and our most expensive assets that rely on a lot of personnel,” Cole said. “There’s applications and land that’s going to be the next big push, especially once autonomous vessels really start to have the regulations and the requirements kind of outlined for that.”
Recommended Reading
E&Ps Posting Big Dean Wells at Midland’s Martin-Howard Border
2025-04-13 - Diamondback Energy, SM Energy and Occidental Petroleum are adding Dean laterals to multi-well developments south of the Dean play’s hotspot in southern Dawson County, according to Texas Railroad Commission data.
On The Market This Week (April 7, 2025)
2025-04-11 - Here is a roundup of marketed oil and gas leaseholds in the Permian, Uinta, Haynesville and Niobrara from select E&Ps for the week of April 7, 2025.
US Oil Rig Count Falls by Most in a Week Since June 2023
2025-04-11 - The oil and gas rig count fell by seven to 583 in the week to April 11. Baker Hughes said this week's decline puts the total rig count down 34 rigs, or 6% below this time last year.
IOG, Elevation Resources to Jointly Develop Permian Wells
2025-04-10 - IOG Resources and Elevation Resources’ partnership will focus on drilling 10 horizontal Barnett wells in the Permian’s Andrews County, Texas.
Saudi Aramco Discovers 14 Minor Oil, Gas Reservoirs
2025-04-10 - Saudi Aramco’s discoveries in the eastern region and Empty Quarter totaled about 8,200 bbl/d.
Comments
Add new comment
This conversation is moderated according to Hart Energy community rules. Please read the rules before joining the discussion. If you’re experiencing any technical problems, please contact our customer care team.