Editor's note: This article first appeared in the 2021 Hydraulic Fracturing Techbook. View the full PDF of this techbook here.
In the journey to better understand the relationship between parent and child wells, or primary and infill wells, and the effects of interactions between the two, various thoughts and ideas exist from a variety of industry experts. Since the issue of fracture-driven interactions (FDIs) first arose around 2014, the oil and gas industry has recognized the importance of both understanding and, in most cases, limiting those interactions.
While FDIs were the topic du jour by 2018, the COVID-19 pandemic, OPEC+ price war and subsequent drop in oil prices and financial belt-tightening have shifted the industry’s focus. Well interactions were less of a priority when few companies were drilling wells.
However, the issue didn’t just simply go away. The unconventional development industry is still searching for answers and solutions as well as a firm understanding of FDIs. From better well spacing designs to fluid tracing to pressure monitoring to fracture diagnostics, a wide array of well designs and technologies are being applied to understand and alleviate negative impacts of FDIs.
“As is typical in our industry, when observations are made like this, people buckle down and try to figure out what is going [on], and they have with the concept of fracture-drive interactions,” said Peter Duncan, president and CEO of MicroSeismic, a provider of real-time reservoir analysis. “Those interactions can range anywhere from a temporary loss of production to a permanent loss of production to the child well not performing as well as the parent well right up to the loss of the wellbore.”
Understanding the challenges
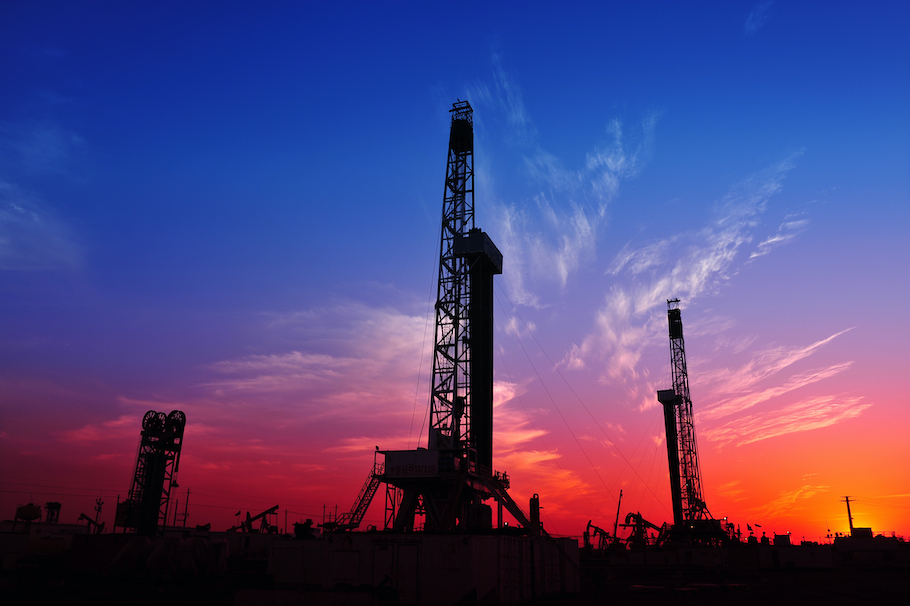
Darcy Partners, an oil and gas technology analyst and consulting firm, hosted a webinar in February that focused on FDIs and primary and infill well design challenges. In a subsequent interview with Hart Energy, Jack Blears, Darcy’s head of E&P technology research, said the virtual conference had more than 400 attendees, and many of those attendees stated that their primary challenge for addressing FDIs was in the modeling phase.
“We took some survey data and we had over 130 responses, and the first question we asked was ‘What’s the biggest challenge with parent/child modeling for your organization?’” Blears said. “And the top three things out of the list of about 10 potential options were [about] the accuracy of the models themselves.”
The other top challenges noted by Blears were workflow complexities, such as the number of softwares and disciplines in the modeling process, and the ability to gain actionable insights.
“Regarding accuracy, it’s no secret these systems are highly complex,” Blears said. “They are multiscale physics, non-linear physics, and all of these models we are building require a lot of different input parameters that are just inherently uncertain because the systems that we care about, they’re a mile underneath the earth.”
He explained that tasks such as estimating frac length, frac height, permeability and leak-off has to be performed indirectly.
“There is some good progress on what we can measure through fiber optics,” he said. “But for the most part, what we see in our data here is that given a parent/child study is involving four to five wells, so when you multiply that by the number of parameters that are required, there’s just a lot of uncertainty, a lot of unknowns. That’s really one of the biggest challenges around the accuracy as well as just the fundamental lack of knowing what these fracture systems actually look like.”
Blears explained that the inability to achieve actionable insights on modeling data stems from “not being ahead of the bit,” meaning that a lot of the modeling work, especially in physics-based modeling, is done on a look-back basis.
“So you drill a few wells and you take a couple of weeks to months to analyze and try to tease out a relationship between why a given fracture treatment design resulted in a given outcome versus understanding on an upcoming well pad for how we use this model to predict the behavior and use it as a tool to really guide our completion design,” he said. “That’s where the industry wants to go.”
Real-time monitoring
A number of industry consultants and technology providers see that such post-mortem, post-frac analysis, while still valuable, essentially comes too late when trying to mitigate the negative impacts of FDIs before they can occur. Technologies and methods that allow operators to make on-the-spot decisions on their frac jobs are a solution to FDIs that many, including industry consultant Ali Daneshy, favor.
In 2010 Daneshy was contracted by Canadian producer Penn West to analyze post-frac data, and it was then that Daneshy first identified pressure changes in primary wells during infill well frac jobs. Since then, he has been working with and through various companies and associations to find solutions to FDIs. One solution Daneshy favors is real-time pressure analysis.
“One of the things the industry has known for a long time is that these horizontal wells are very unforgiving,” he said. “Once you drill the well, doing any kind of remedial work is often not possible or very expensive. If you drill a well and get suboptimal production, you really don’t have a chance to go back and spend a bunch of money to improve it.”
Daneshy said that dynamic gave rise to massive— and largely uniform—frac designs.
“Because we cannot go back and correct our errors, the industry decided that if we are going to make a mistake, let’s do it toward making a bigger job,” he said. “As a result, they repeat the same frac schedule. If you have a well with 50 stages, you repeat the same fracture 50 times.”
What Daneshy discovered was that by using the frac data, operators could decide when each stage reached its optimum usefulness.
“And when you get to that point, you stop it and go to the next one,” he said. “As you are observing what is happening in the primary well [in terms of pressure changes], you are observing that in real time. If you reach a point where you think it’s going to cause damage, you stop it. It is no problem at all to look at that pressure in real time as that job [on the infill well] is in progress.”
Daneshy has also been a voice for the positive impacts FDIs can offer. He said that perhaps the most significant positive effect is achieving a better understanding of the individual fractures.
“As I started to dig in to this issue, I started to realize that this technology could revolutionize oil and gas productions,” he said. “If you record these pressures in real time based on the level of interaction, you can get a very good picture of the relative position of the two fractures in the two wells. And based on that level of interaction, you can decide when you have done enough.”
He said the data from real-time pressure monitoring can provide valuable information on the different frac signatures.
“This is giving you an indication of the length of the different fractures, each of the different fractures in the (primary well) and infill wells,” Daneshy said.
Subsurface diagnostics
Real-time frac job analysis can be applied to more than just pressure monitoring. Deep Imaging, a subsurface imaging and frac diagnostics company, announced its acquisition of ESG Solutions in May. According to a press release, the combined company offers a suite of technologies that includes advanced diagnostic tools that track and measure frac fluid placement from the surface and away from the pad.
“Our technology really helps you constrain the X and the Y, where your fluid and proppant go during the frac,” said David Moore, president and CEO of Deep Imaging. “But we really needed a Z component to our product. So we went out and acquired ESG. We really liked ESG because they took on the same thought process that we did.”
He said that thought process included continued investments in velocity models and data processing that leads to actionable insights.
“They have real time, and we’re going to be helping them by iterating it to an even better real-time product on their borehole seismic,” Moore said.
Chief Development Officer Josh Ulla explained more as to the benefits of real-time monitoring as compared to post-frac evaluation.
“Post-mortems are useful to start cultivating the ‘why?’” he said. “Why did we have that frac hit? But you need to have the ‘what’ as well. You need to know what has happened. If you’re driving a car and you’re about to hit a wall, you’d love to know what’s happening so you can hit the brakes and avoid those obstacles.”
Moore added that the operational tool helps you immediately identify a runaway frac stage toward a parent well or adjacent well.
“It’s an evolution of technology,” he said. “If you can stop it before it happens, you would, because it’s an evolution of technology. We have been on fracs where there has been a frac hit, it a hit a parent well, and that parent well was only a 5,000- psi well, and they pressurized it to 4,500 [to] 4,800 psi. At that point, you’ve got to shut the frac down for 12 to 14 hours. So that alone, operationally you’ve wasted $100,000 and people’s time.”

MicroSeismic’s Duncan noted that his business has recently started to see an uptick in activity.
“Five or six years ago, the majority of our practice was driven toward people wanting to understand the stimulated reservoir volume that was being created,” he said. “Now, probably 50% of my practice is being driven by people wanting to be aware of fracture-driven interactions, and specifically being concerned in places like the Eagle Ford [and] specifically being concerned about wellbores being constricted or sheared off by the reactivation of previously existing faults and fractures.”
MicroSeismic’s technology monitors the fracturing of rock through the proxy of the microseismic events that occur.

“We can locate those microseismic events around the stimulated wellbore,” Duncan said. “We can locate them in time so we can see them change dynamically and how they move away from the wellbore. We can also tell whether the movement on these fractures when they stimulate the well are dip-slip or strike-slip, or more or less horizontal.”
Trends he has identified include more emphasis on protecting the wellbore rather than protecting production.
“Some of our monitoring in the past was driven by trying to minimize fracture-driven interactions that would affect production volumes,” Duncan said. “I see less emphasis on that now and more emphasis on monitoring fracture-driven interactions and detecting those prior to there being any negative emphasis on the mechanical integrity of well.”
Well spacing trends
In addition to the myriad technologies available to limit and understand FDIs, operators are still trying to determine which well spacing patterns can both optimize production while also mitigating risk factors. And not just well spacing—completion designs, well economics and the age of a play are all factors producers are considering when trying to better understand FDIs.
“If there is a risk of interference in the oil production, if you space the wells too tightly, that doesn’t necessarily mean that upspacing is always going to lead to better productivity because it really also depends on the rock and on the completion and on a whole lot of different factors,” said Amanda Richardson, senior research analyst with Wood Mackenzie. “So it’s not as clear cut of a trend as you might expect between productivity and spacing. It’s just a risk that needs to be mitigated basically.
Wood Mackenzie recently compiled a report studying well spacing and productivity in the Permian and Eagle Ford basins. The study looked at well densities in both plays compared to basin maturity, the effect of co-completions on wells, and single-well economics versus full section development economics. Wood Mackenzie found that multi-bench developments are more common in the Permian Basin’s Wolfcamp development, which likely contributes to wider spacing on average than in the Eagle Ford.
“In the Eagle Ford, they are using much tighter well spacing, around 330 ft on average versus in the Wolfcamp [where] it’s 600 to 800 ft,” Richardson said. “In the Wolfcamp you see multi-bench developments a lot more often. Those are staggered between the two benches, where as in the Eagle Ford, you see more of that. Also it’s just much more drilled out and there’s not as much room. So operators are getting the most value out of the acreages they have by fitting those wells in.”
According to Wood Mackenzie, the average horizontal spacing in the Wolfcamp in Reeves, Loving and Lea counties was about 1,300 ft in 2014. Since then, that spacing distance has declined to between 800 ft and 1,000 ft. In the Eagle Ford, well spacing distances have only varied slightly, particularly in the Hawkville and Maverick condensate plays where wells have typically been spaced about 600 ft apart. In the Edwards Condensate and Karnes Trough—the two most productive Eagle Ford subplays—average horizontal spacings have declined slightly from about 500 ft in 2014 to about 300 ft in 2020.
“[Well spacing in the Eagle Ford] really hasn’t changed a lot in the past three years,” Richardson said. “Prior to that, there was more downspacing, but in recent years when you look at it on an average level at the subplays, it’s been fairly consistent.”
However, despite the plateauing of well spacing, particularly in the Eagle Ford, Wood Mackenzie found those efforts haven’t necessarily led to production increases.
“The performance hasn’t shown a corresponding uptick though, and that’s where it’s hard to parse out the multivariate aspect of all of this and how impact spacing alone has,” said Ryan Duman, principal analyst of Lower 48 upstream with Wood Mackenzie. He provided an example of the Midland Wolfcamp, where production related to well spacing has remained “about flat.”
“I think the key question that is asked as operators theoretically continue to upspace [is] do you see performance follow, or is it one where they just mitigated some of that risk of performance rolling over like we’ve seen in the Eagle Ford and portions of the Delaware Basin?” he said.

Wood Mackenzie analyzed the impact co-completions along with upspacing might have on well performance and determined that while tightly spaced wells performed better if they were co-completed, they still underperformed more widely spaced wells on average.
According to Wood Mackenzie, in the Midland Wolfcamp, co-completed wells with wide spacing (defined as 660 ft or more) produced at about 35 boe/ft after 36 months on production, similar to wide-spaced wells that were not co-completed. However, tightly spaced wells that were not co-completed saw production fall to less than 30 boe/ft. Co-completed tightly spaced wells performed only slightly better, just over 30 boe/ft.
Over the years, there have been a variety of efforts and technologies emerge to help alleviate FDIs, some with more success than others. Proppant tracing and real-time pressure monitoring have each proven beneficial to varying degrees, but well spacing remains an inexact science.
“We’re years down the line, and there’s no simple solution or agreed upon solution that folks can employ,” Duman said. “Generally, spacing is going to mitigate that risk or tailor completion design or other things to impact performance. It’s dependent on individual operators and what rock they’re actually trying to exploit, which can make it challenging to try to do more of the basinwide or very wide macro analysis.
In an analysis of Karnes Trough P50 type curves, Wood Mackenzie found that wells spaced 330 ft to 660 ft apart would be expected to recover about 10% more barrels per foot than wells spaced less than 165 ft apart. Widely spaced wells recovered about 44 boe/ ft in the Karnes Trough, while tightly spaced wells recovered about 39 boe/ft.
“If you look at sections, levels, NPV [net present value] or payback or whatever metric of choice, as you start to move wider, say six wells per section, you start sacrificing the amount of resource you’re going to develop and the overall value starts to decline again,” Duman said. “So it’s trying to balance that sweet spot of how much resource overall you can develop while accepting that individual well performance isn’t necessarily going to be the best that it possibly can be.”
RELATED CONTENT:
Aug. 5, 2021 Academia and Industry Embrace Nuance in Fracturing
Aug. 2, 2021 Shale Producers Talk Development Plans, ESG and Completion Designs
July 29, 2021 Cold Bore Technology Closes $14 Million Financing
July 28, 2021 Halliburton Launches Low Cost, Direct Fracture Monitoring Service
July 12, 2021 Seneca Resources, NexTier to Develop Comprehensive Emissions Testing for Well Completions Work
July 7, 2021 Liberty Completes digiFrac Electric Frac Pump Field Test in Permian Basin
July 6, 2021 Reveal Energy Inks Deal to Commercialize Hydraulic Fracture Pressure Diagnostics
June 21, 2021 Specialized Chemistry Increases Sustainability of Traditional Hydraulic Fracturing
Recommended Reading
California Resources Continues to Curb Emissions, This Time Using CCS for Cement
2025-03-04 - California Resources’ carbon management business Carbon TerraVault plans to break ground on its first CCS project in second-quarter 2025.
Google, SLB, Project Innerspace Form Geothermal Partnership
2025-03-06 - The geothermal partnership between Google Cloud, SLB and Project Innerspace takes shape as energy demand surges, driven in the U.S. by data center growth, the rise of electrification and an increase in manufacturing activity.
API’s Multi-Pronged Approach to Lower Carbon Operations
2025-01-28 - API has published nearly 100 standards addressing environmental performance and emissions reduction, which are constantly reviewed to support low carbon operations without compromising U.S. energy security.
BKV Reaches FID, Forms Midstream Partnership for Eagle Ford CCS Project
2025-02-13 - If all required permits are secured, BKV’s CCS project in the Eagle Ford Shale will begin full operations in first-quarter 2026, the Barnett natural gas producer says.
Energy Transition in Motion (Week of Jan. 31, 2025)
2025-01-31 - Here is a look at some of this week’s renewable energy news, including two more solar farms in Texas.
Comments
Add new comment
This conversation is moderated according to Hart Energy community rules. Please read the rules before joining the discussion. If you’re experiencing any technical problems, please contact our customer care team.