The diverse quantity of public data available today makes it possible to explore the impact of various completion factors on production. The market has changed considerably over the last few years, consistently pushing to produce more with less in a shorter period of time. Efficiency gains through fluid chemistry, equipment performance and logistics have arguably become as important as the EUR. Strides made in any of these areas to decrease the time from drilling to production have become a top priority.
One of the major areas of focus for BJ Services has been fracturing fluids systems. Hydraulic fracturing operations tend to have added complexity, which oftentimes increases the need for logistical management and project costs. One way to eliminate some of these complications is by developing fluids that can be tuned to work in a variety of applications and environments. Homing in on a fluid system that will provide flexibility to work in different water qualities and applications and yet provide production uplift has been a challenge, especially in places such as the Eagle Ford. High rate and high-pressure jobs in low-permeability formations have become the norm, and with the overall trend moving toward executing mostly slickwater designs, an adaptable fluid is needed.
Public databases can provide large amounts of data, but it is very important to scrub through these datasets and use only good, relevant data that make sense. Using knowledge of completion design, geology and fluid chemistry helps in understanding and using data to demonstrate trends for what fluids may work best in a given area.
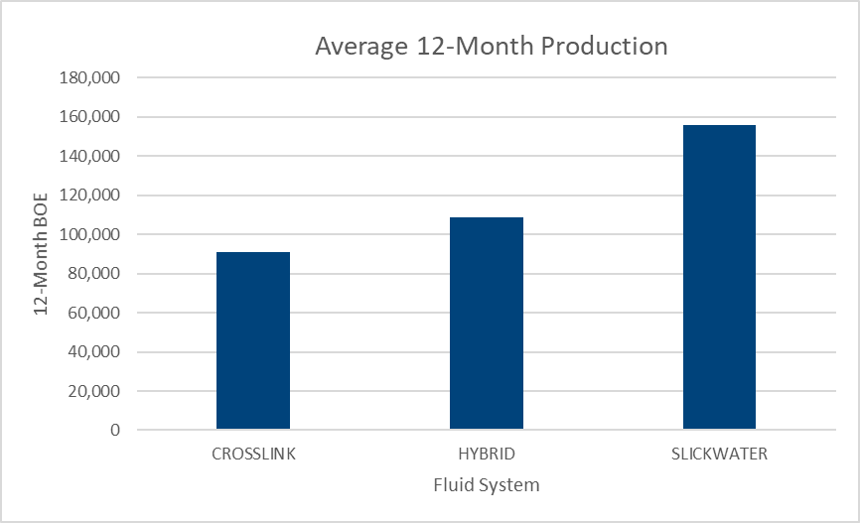
Using the public database to investigate a 16-km (10-mile) radius in the Eagle Ford, there have been about 927 horizontal wells drilled and completed. After analyzing the production per well by fluid system, the data show that wells completed using slickwater designs have a better 12-month production compared to wells completed with slickwater crosslink hybrid or crosslink designs.
Additionally, the public domain can be used to drill down farther and examine more specific cases. One area of interest is where BJ Services has pumped its own proprietary friction reducer. Within the aforementioned 16-km radius, there are 120 identified wells that were completed using a slickwater design. Seventy-eight of those wells were completed using conventional friction reducers and 40 wells were completed using BJ Services’ friction reducer. The normalized monthly production comparison shows that the wells completed with BJ Services’ friction reducer performed better in the first 13 months of recorded production.
Slickwater fluids consist of only friction reducer and other miscellaneous chemical additives (biocide, scale inhibitor, etc.) in the base fluid, whereas there are multiple chemicals needed to build viscosity to carry higher proppant concentration in linear gel and crosslink jobs. Multiple chemicals increase location footprint due to more equipment needed. This increases the number of equipment operators on location as well as chances of nonproductive time (NPT) due to equipment breakdown or logistics uncertainties.

Though production improvements are significant for the operator, there are a multitude of ways to improve efficiency throughout the fracturing operation. BJ Services pumped more than 4,000 stages in 2018 with its friction reducer in all major basins in the U.S. and Canada. The engineered polymer backbone is designed for a clean, efficient break with little to no formation or proppant pack damage. It leaves no residue in the proppant pack or formation when compared to that left behind by pumping conventional friction reducers or guar-based linear gels, thus enhancing hydrocarbon recovery. It is a single fluid system that provides instant friction reduction at lower loadings and provides proppant carrying capacity at higher loadings. This flexibility of application drives operational efficiency by eliminating the additional chemicals and equipment needed for slickwater linear gel hybrid design.
In cases where BJ Services has run its tunable friction reducer, improvements such as a decrease in pump time and a reduction in NPT have been observed. The operator also benefited from more simplified logistics by using only one chemical as opposed to having to order, deliver and set up a linear gel or crosslink job, which would require three to four chemicals and additional equipment. Eliminating additional chemicals and equipment results in a smaller equipment footprint, which decreases project costs, onsite maintenance and the risk for NPT associated with the equipment.
Case study
One specific application was on a two-well zipper pad, where a conventional friction reducer was used for the first 10 stages. The operator observed very high treating pressures and switched to BJ Services’ friction reducer on the remaining stages thereafter. An average of 1,175- psi reduction in average surface treating pressure was observed throughout the remainder of the stages on both wells, decreasing the horsepower requirement. The ability to tune the friction reducer to run at higher concentrations while pumping enabled the operator to increase the fluid viscosity easily and thereby transport proppant farther when needed. Though the initial loading of friction reducer was 1 gpt, after achieving positive results, the loading was optimized to 0.5 gpt. Overall, there was 20% less product consumed when compared to the conventional friction reducer.
The single-fluid, tunable system enabled the remaining stages to be completed faster than the initial 10 stages where the conventional friction reducer was run. The operator switched over to this technology when completing subsequent wells and saw less NPT, shutdowns and screenouts.
Recommended Reading
US Halts Construction of Equinor’s Empire Wind Project Offshore NY
2025-04-16 - In a post on X, Interior Secretary Doug Burgum said construction activity is being stopped “until further review of information that suggests the Biden administration rushed through its approval without sufficient analysis.”
Spearmint Energy Secures Financing to Connect 400 MWh to ERCOT
2025-04-16 - Spearmint Energy has closed more than $250 million in financing for the construction of two battery energy storage systems that will be connected to Texas’ ERCOT grid.
US NatGas Prices Slide 3% to 10-Week Low on Near-Record Output, Mild Weather
2025-04-16 - U.S. natural gas futures slid about 3% on April 16 to a 10-week low on near-record output.
Expand Energy Joins EQT in Triple-Investment-Grade Credit-Rating Club
2025-04-16 - The trifecta of endorsements assures Expand Energy, the largest gas producer in the U.S., a seat alongside EQT Corp. at the LNG and AI data center gas-supply negotiating tables.
Renewables Company Catalyze Gains $85MM Investment from RBC
2025-04-16 - Catalyze said the $85 million financing is expected to support the construction and completion of approximately 75 megawatts of solar projects across the U.S.
Comments
Add new comment
This conversation is moderated according to Hart Energy community rules. Please read the rules before joining the discussion. If you’re experiencing any technical problems, please contact our customer care team.