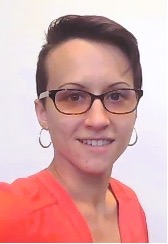
Downstream industry assets often operate at temperatures exceeding 1,200 F (650 C). Today, the standard practice for managing and controlling heat is to use mechanical insulation, such as mineral wool or calcium silicate, and metal jacketing on heated tanks, piping and related equipment. Insulation improves energy retention and ensures workers are protected from hot surfaces.
While mechanical insulation addresses the issues of retaining energy and protecting workers, all these systems have drawbacks. Traditional systems are cumbersome to install because they require significant scaffolding for large applications, precise cutting for complex geometries and proper sealing to prevent water ingress.
The industry needs a better solution, one that provides the necessary protections but is easier to install.
Traditional insulation system challenges
Mechanical insulation systems require a primer coat on the substrate, fitting the insulation, and securing a jacketing layer to protect against damage and water ingress. Over time, rainwater or washdowns can seep under the jacketing and saturate the insulation, which leads to reduced thermal insulation capacity and creates an environment prone to corrosion under insulation (CUI). Heavy saturation can cause the insulation to shift or collapse, compromising its effectiveness.
Conventional spray-applied coatings, primarily waterborne acrylic or epoxy-based coatings, are limited in temperature resistance—serving equipment operating at 350 F (177 C) or lower—and often require multiple layers to achieve the desired thickness for optimal protection. These limitations restrict the use of conventional coatings and result in long application times. The need for multiple layers can lead to extensive schedule additions and potential intercoat issues due to weather, especially when the coatings are applied to large structures such as storage tanks.
Both mechanical insulation and conventional spray-on insulations face significant challenges in preventing CUI. Mechanical insulation can trap moisture, leading to high corrosion levels, while spray-on insulation coatings still require a primer to protect the steel substrate.
CUI can result in costly maintenance, repairs, shutdowns and even catastrophic failures. For instance, in 2001, corrosion led to a rupture in a pipe carrying flammable gas in the U.K. that resulted in an explosion and fire. It is clear that effective corrosion prevention is necessary to avoid incidents like this and that there is a need for a better solution.
A robust spray-on insulation is the answer.
The future of insulation
Recent developments have led to the creation of a new silicone-based, spray-on insulation coating that is not only effective but easy to apply. This innovative solution can be applied at high film builds, withstand a broader temperature range than conventional spray-applied coatings and mitigate corrosion in atmospheric and immersion conditions. The new hydrophobic spray-on insulation coating uses silicone technology with thermally insulative fillers.
Before the new insulation coating was introduced in the field, it underwent multiple tests to validate its performance, including those assessing application robustness, thermal properties, corrosion resistance and water permeability.
Thermal testing shows that the coating endures continuous and cyclic temperatures reaching as high as 500 F (260 C), surpassing the 350 F (177 C) upper limit associated with conventional insulation coatings.
Apart from withstanding temperature extremes, field applications and lab tests confirm the silicone-based coating’s low thermal conductivity. This property allows the coating to significantly reduce surface temperatures and minimize heat loss, even at high temperatures, providing energy efficiency and safe-to-touch surfaces. A single coat is enough to provide safe-to-touch surface temperatures per American Society for Testing and Materials (ASTM) standards.
Improved CUI mitigation
Another advantage of applying the new hydrophobic coating is that it resists water absorption better than many fibrous insulation materials. It absorbs less than 3% water when submerged after 72 hours, compared to much higher absorption rates in mineral wool. The fact that there is less moisture means increased insulation performance for greater operational efficiency.
Application properties were evaluated using a range of equipment, including high-volume, low-pressure conventional spray and texture spray with diaphragm or low-pressure transfer pumps. Conditions ranged from 40 F (4.4 C) to 300 F (149 C), with 20% to 95% relative humidity. The coating could be applied easily with conventional spray equipment, reaching dry-to-touch in a few hours or less at 77 F (25 C) and were hard enough to walk on the next day, allowing for the quick application of a second coat if needed.
Thermal heat resistance was evaluated using the ASTM D2485 method B, assessing the coating for degradation, delamination, cracking and loss of adhesion. The coating demonstrated less than 5% mass loss after 100 hours of dry heat exposure to 500 F (260 C) and could withstand cyclic temperatures up to 600 F (316 C) without visual degradation. Cryogenic testing showed resistance to temperatures from -321 F to 500 F (-196 C to +260 C) without delamination, blistering, rusting or cracking.
The coating’s water permeability and corrosion resistance were internally tested through the anti-corrosion performance requirements of the International Organization for Standardization (ISO) 12944-6 C5H corrosion performance, ISO 9227 salt spray and ISO 6270-1 water condensation tests. The coating demonstrated excellent corrosion resistance even under harsh conditions.
Innovative insulation impact in the field
An integrated energy company recently applied the new silicone-based spray-on insulation coating, PPG PITT-THERM 909, to one of its storage tanks. The company initially faced significant challenges with traditional mechanical insulation systems, including high maintenance costs, frequent CUI and energy inefficiency. The application of the new insulation solution went smoothly, and now the company is measuring the spray-on insulation coating’s effects on energy efficiency, surface temperature and CUI mitigation.
The new silicone-based spray-on insulation coating offers significant advancements in thermal management not only for storage tank protection but for other assets in the petrochemical and energy industries. It addresses the limitations of traditional insulation methods, providing faster application, greater durability and superior protection for workers and assets. The coating’s ability to withstand a wide range of temperatures and reliably mitigate CUI makes it an optimal choice for petrochemical and energy assets operating in demanding environments.
Recommended Reading
Inside Ineos’ US E&P Business Plan: Buy, Build, Buy
2025-01-27 - The E&P chief of U.K.’s Ineos says its oily Eagle Ford Shale acquisition in 2023 has been a profitable platform entry for its new U.S. upstream business unit. And it wants more.
E&P Highlights: Feb. 24, 2025
2025-02-24 - Here’s a roundup of the latest E&P headlines, from a sale of assets in the Gulf of Mexico to new production in the Bohai Sea.
PE Firm Voyager to Merge Haynesville OFS Firm with Permian’s Tejas
2025-03-17 - Private equity firm Voyager Interests’ Haynesville Shale portfolio company VooDoo Energy Services will merge with Tejas Completion Services as part of a transaction backing Tejas, Voyager said.
BKV Positions Itself to Meet Growing Power, CCS Demand
2025-02-26 - Electricity needs across the U.S. are expected to soar as industrial and manufacturing facilities, data centers and other consumers crave more power. BKV is exploring ways to bridge the gap between demand and energy supply.
Sitio Fights for its Place Atop the M&R Sector
2025-04-02 - The minerals and royalties space is primed for massive growth and consolidation with Sitio aiming for the front of the pack.
Comments
Add new comment
This conversation is moderated according to Hart Energy community rules. Please read the rules before joining the discussion. If you’re experiencing any technical problems, please contact our customer care team.