
The SWAT system uses real-time monitoring and PLC control technology to provide operators with 24/7 access to their water recycling operations. This allows a transparent, on-demand view of the chemistry, treatment volumes and water quality being delivered from the system. (Source: TETRA Technologies)
From the dawn of the frac era, it was apparent that a cheap and plentiful water supply would be vital to the hydraulic fracturing process. Back then it was normal to pump freshwater out of the ground for fracturing, then to pump the produced water back into the ground.
The idea of treating and recycling produced water for fracturing was floated—and dismissed—due to the cost of treating the water sufficiently to work with existing frac fluids. Although there was a cost to buy freshwater and to dispose of produced water, historically those costs when added together were much less than treating and reusing water.
Fifteen years and billions of barrels of water later, three things have happened to create a rush to treat and reuse produced water.
The first was a notion of preserving water in dry regions. Even though those billions of barrels represent less than 0.1% of all water used in the U.S., it’s still a lot of freshwater to take out of mostly arid landscapes. With a plentiful supply of produced water available for treatment and reuse, why not use produced water instead of freshwater when possible?
Second, engineers have modified frac fluids to accommodate high levels of chloride and other chemicals, eliminating the need for pure freshwater.
Third, and the subject here, is that treatment methods have become much more cost-effective, especially when they integrate chemical and mechanical treatment methods and optimization of the labor force by relying on automation to monitor and control the process. Creating water systems that replace thousands of truck trips with pipelines and pump stations is integral to this efficiency.
Automation
Early treatment methods were highly labor-intensive, requiring someone to occupy every pump, tank, pond and chemical injection location to monitor levels and to be ready to make adjustments to accommodate varying inflow/outflow rates and storage levels. Reassigning those people to other tasks and installing sensors for the water systems allows companies to treat about 75,000 bbl/d at permanent, centralized gathering and treatment facilities, with only three people on site at any given time. Even larger numbers of barrels can be treated with additional personnel. Trailer-based mobile systems also are available for short-term solutions lasting from a few days to a few weeks.
For both permanent and mobile requirements, automated systems using pump and valve controls connected through cellular-based communications handle pressure limit controls, remote monitoring and realtime data access and logging. Data can be accessed and monitored by system operators and clients from a desktop or mobile device.
With monitors and controls at every significant step, programmable logic computers (PLCs) are programmed to make constant adjustments in pump speeds and injection rates for maximum flow and treatment levels throughout the system with minimal human intervention and downtime.
There is also the bigger picture of how each piece interacts with the rest. Automating each pump or valve is simple. But all these parts depend on each other—a change in one piece affects all the others before it and behind it.
For example, if the manifold determines that the frac is pulling 93 bbl/min, the unit tells the pumps to give it backfill of the same amount. Or if there is a blending controller that is blending produced water and freshwater, its purpose is to maintain the proper ratio of the two. This unit must also control both freshwater and produced water pumps.
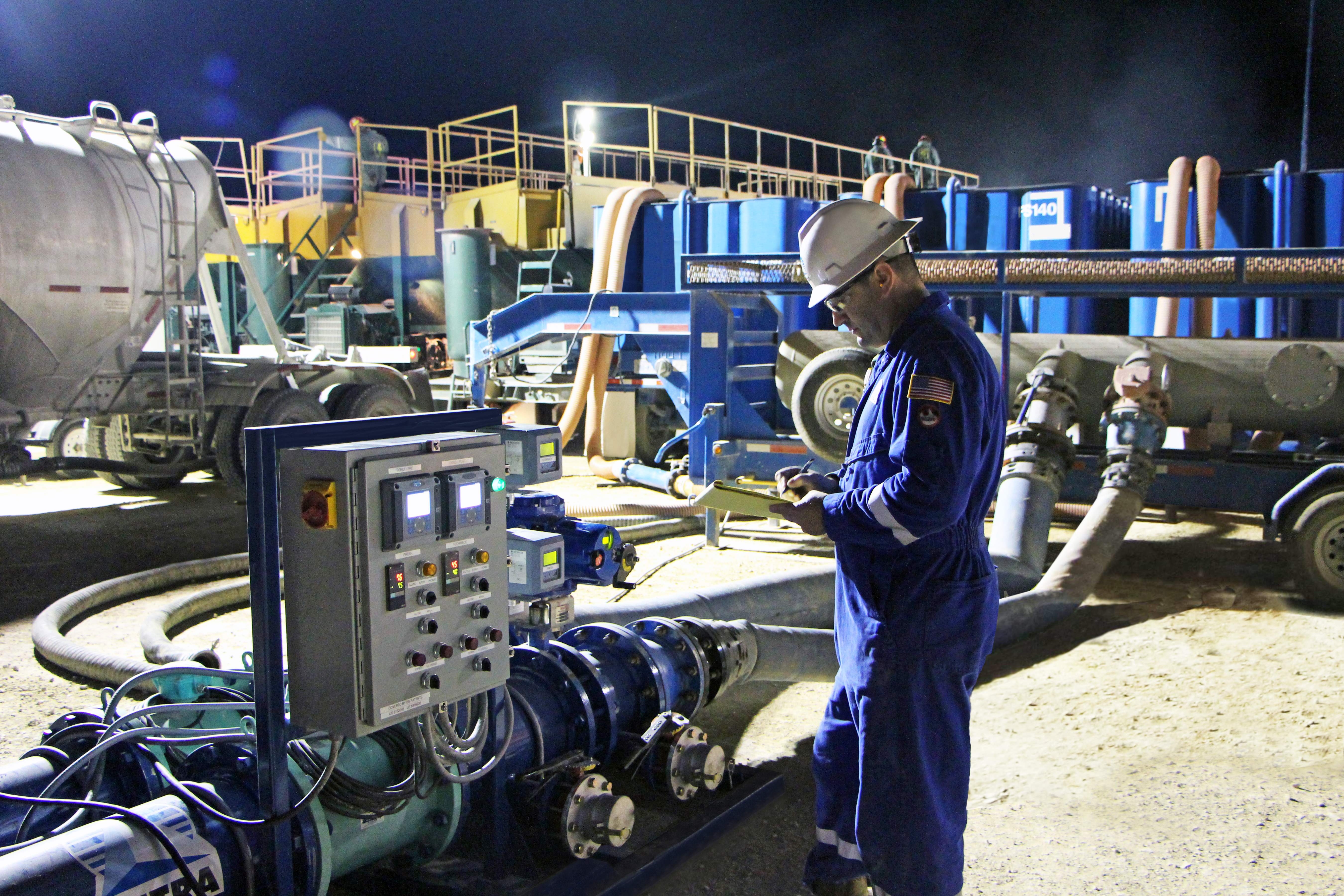
In a location where flow rates are changing due to the completion of additional wells or the rerouting of produced water to other facilities, this systemwide view is vital to the efficiency and safety of the operation.
Automation also improves safety by reducing the risk of injury to personnel. Creating and automating treatment facilities and pipeline networks eliminates thousands of truck trips every month. For example, TETRA has recycled 15.3 MMbbl of water in the Permian Basin over the last 12 months. That is the equivalent of eliminating 128,000 truckloads of water.
Planning
Although water treatment does have some variable costs for supplies such as chemicals, much of the equipment costs are the same whether the system is running or not. Right-sizing the installation is the next biggest key to cost savings after automation. Because undersizing can cause its own issues, such as restraints in treating the flow of produced water or failure to deliver enough water for fracs, making decisions regarding automated equipment installation is usually best left to companies that focus on water treatment and handling.
Right-sizing a mobile installation may be an ongoing task as units may need to be added or subtracted as flow rates change. Operational personnel numbers also can be flexed.
Even permanent facilities may face changes on occasion as a pump goes down or a well is taken offline for a workover, so there may be times when a unit is not operating at full efficiency.
This is where the expertise of a water management company is necessary. The company’s engineers can use any existing historical data from the operator—flow rates, injection rates, flowback volumes and more—to determine what equipment and controls are necessary to optimize the investment.
Treatment levels
The level of treatment required is another key to right-sizing. Levels can range from minimal—what the treatment industry calls “sock filtering”—to extensive removal or treatment of iron, bacteria and, where needed, H2S. Therefore, the appropriate amount of equipment needed varies widely.
It might seem more economical to treat less, but produced water that retains iron, suspended solids and bacteria can quickly allow scale accumulation and other problems in pipelines, pumps and in the formation itself, along with sludge buildup in tanks and ponds. For an operator committed to a field long term, fixing these problems once they exist is far more costly than using a complete treatment to prevent them from ever occurring.
Skim oil must be removed because it can be sold into the pipeline and it will cause a long list of problems if left in the water.
Bacteria must be treated now and throughout the process. Many treatment methods use a “shock treatment” to kill existing bacteria. However, if the water is to be stored in aboveground ponds for more than a few days, airborne bacteria can recontaminate the water and is much harder to treat in a 500,000-bbl pond once the bacteria get started—hence the need for ongoing treatment for storage.
Anaerobic sulfate-reducing bacteria turn sulfate into sulfide, which combines with iron to make iron sulfide. This turns the water a murky black color and, because it’s sticky to metals, creates corrosion. The acid produced by aerobic acid producing bacteria also creates corrosion in equipment and in shale formations. When an automated water system includes the appropriate treatment systems, it is much more cost-effective to treat the produced water to prevent damage to systems and formations that would otherwise come into play.
Older, labor-intensive treatment systems are being replaced by automated systems that are more efficient and more accurate. These efficiencies are making the treatment and use of produced water more available as freshwater scarcity and other issues render it imperative.
Recommended Reading
Elliott Demands Phillips 66 Sell or Spin Off Midstream Biz for $40B+
2025-02-12 - Activist investor Elliott Capital Management disclosed Feb. 11 it has built a $2.5 billion position in Phillips 66 and issued a series of initiatives, including the sale or spinning off of the company’s midstream assets.
ONEOK Completes EnLink Midstream Takeover for $4.3B
2025-02-02 - ONEOK had agreed to acquire the remaining stake in EnLink in November 2024 for $4.3 billion after having acquired the controlling interest a month prior.
ONEOK, MPLX Enter $1.75B JV for Texas LPG Export Terminal, Pipeline
2025-02-04 - ONEOK Inc. and MPLX have entered into agreements to invest $1.4 billion to build a 400,000 bbl/d LPG export terminal in Texas and a $350 million pipeline project.
Amplify Updates $142MM Juniper Deal, Divests in East Texas Haynesville
2025-03-06 - Amplify Energy Corp. is moving forward on a deal to buy Juniper Capital portfolio companies North Peak Oil & Gas Holdings LLC and Century Oil and Gas Holdings LLC in the Denver-Julesburg and Powder River basins for $275.7 million, including debt.
NAPE Panelist: Occidental Shops ~$1B in D-J Basin Minerals Sale
2025-02-05 - Occidental Petroleum is marketing a minerals package in Colorado’s Denver-Julesburg Basin valued at up to $1 billion, according to a panelist at the 2025 NAPE conference.
Comments
Add new comment
This conversation is moderated according to Hart Energy community rules. Please read the rules before joining the discussion. If you’re experiencing any technical problems, please contact our customer care team.