When Peter Duncan shared his decision to launch MicroSeismic in early 2003, the response was, admittedly, unenthusiastic.
The CEO and founder recalls his peers asking him, “Are you crazy? What is microseismic monitoring? Is there a business?”
People had never heard of it, yet Duncan was determined to redefine how the oil and gas industry approached subsurface monitoring, turning what was once a niche academic concept into a commercial powerhouse.
In the early days, most practitioners believed that capturing microseismic events required geophones placed downhole, close to the source of seismic activity. But Duncan took a new approach.
“You don’t need to drill down; you can place geophones on the surface and still hear those events,” he said. “In the past, they put their geophones—just single geophones—on the surface of the earth, and they listened and they didn’t hear anything. The signals were too small.”
Duncan and MicroSeismic decided to scatter multiple geophones across the surface and use “the power of the stack” to overcome the signal-to-noise problem and produce clearer data. He likened this to using a dish microphone at a football game—where gathering sounds from afar can yield clearer results than placing a microphone close to the source.
While initially laughed off by his peers, Duncan’s method allowed the company to provide a valuable service and spearhead the microseismic industry, although he does not like to take credit for that.
Bringing the downhole picture into focus
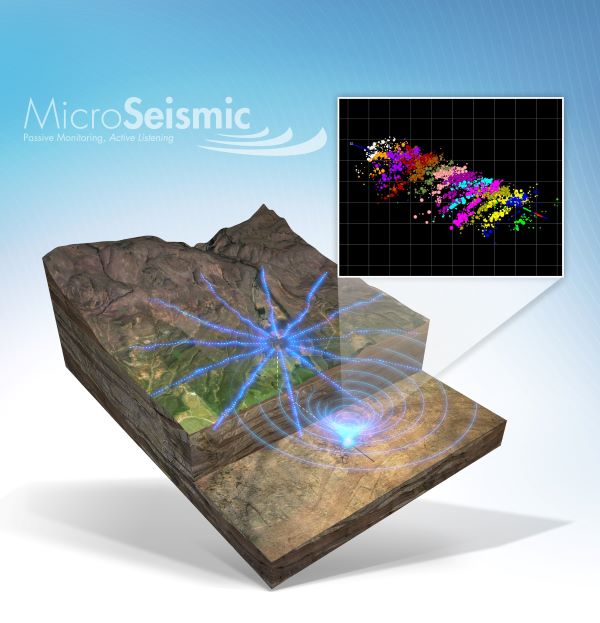
The better visibility created by the added geophones allowed MicroSeismic to create a clearer picture of downhole operations, Duncan said. By recognizing the focal mechanisms of microseismic events—how rocks slip past each other—his team enhanced data accuracy, allowing for better interpretation of fracking results, no longer having to use the old-fashioned “dots in a box” display.
“We can actually put in a little planar element where the size of the planar element is proportional to the magnitude that we see and where we can tell whether the event moved like this or like that. And so, now we’ve got a much better geologic picture of how the frac looked,” he said.
This development transformed microseismic data into detailed discrete fracture networks and laid the groundwork for FracRx, a real-time monitoring system that helps engineers make decisions during fracking operations.
“We started to use that [data] to monitor in real time. We’re going to predict the hydrocarbons, and we’re going to use an extrapolation and say, ‘Well, if you keep fracking for another half-hour, you’re going to get this much more hydrocarbons,’” Duncan said.
“We’re going to help you make efficient decisions about not how to frac—someone else is deciding where to drill the well—but we’re going to help you make more efficient decisions about when you complete that well, how long you should pump, how much you should pump into it, and more.”
This capability became even more critical as the industry faced challenges, especially during the COVID-19 pandemic, which saw a dramatic decrease in operational capacity.
As the company adapted to new challenges, it also explored additional markets. One significant development involved CO2 sequestration, aiming to monitor carbon stored underground to ensure safety and prevent leaks.
“The DOE (Department of Energy) sent out a general notice that they’re looking for ways to monitor carbon when it’s been sequestered to make sure that it’s not causing earthquakes, and to make sure that the carbon is staying in the reservoir where you put it. And we said, ‘Well, we think we could hear little earthquakes that are the precursors to big earthquakes. We think we could hear if it starts to leak out of the reservoir.’ We’d actually done this once,” Duncan said.
This led to the advent of the CO2SeQure suite of technologies, which includes the BuriedArray system, which is similar to a high-tech security system for CO2 storage, Duncan said.
The BuriedArray system is a network of underground sensors that continuously monitors CO2 storage, keeping track of CO2 movement, detecting small seismic events and sending data to a central processing facility.
Before CO2 injection starts, the array measures baseline seismic activity. During injection, it monitors for seismic events that could indicate caprock issues or regional fault slippage, using a “stoplight system” to alert operators if certain critical levels are exceeded.
MicroSeismic also is venturing into the advanced geothermal business. This initiative brings the company’s technologies full circle, as the process is based on the original FracRx solution, Duncan said.
“In places like California, hot rocks are close to the surface. You can drill in and circulate water through the rocks to heat the water and then harvest the heat for electricity,” he said. Geothermal systems take the process into a different realm. “What enhanced geothermal systems are all about is drilling down into the deep basement rocks that are very hot to make supercritical steam and be able to bring more energy up to the surface so that it becomes more commercial.”
Duncan sees potential for enhanced geothermal systems (EGS) to reshape the energy landscape. By applying lessons learned from fracking, he believes technologies such as distributed acoustic sensing (DAS) can facilitate more effective geothermal energy extraction.
DAS, also known as Distributed Fiber Optic Sensing, is an innovative technology that uses lasers to detect sound in real time along an optical fiber cable. Connecting a DAS unit to one end of a standard optical fiber transforms the fiber into thousands of vibration sensors or microphones spread over many kilometers. This setup requires no additional electronics or hardware, making it a highly efficient way to monitor sound and vibrations over large distances.
MicroSeismic is currently working with Australian company Terra15 to offer a DAS-based microseismic solution to enhance the company’s monitoring capabilities.
“DAS is a technology that I’m hopeful will come to bear to be able to get higher-resolution signals than we can get with geophones. But, as a general application, it’s not there yet,” Duncan said. “There are limitations on what the DAS can do, and we’re still working on that. But, I’m hopeful that will be something that replaces our conventional geophone.”
Recommended Reading
Halliburton Secures Drilling Contract from Petrobras Offshore Brazil
2025-01-30 - Halliburton Co. said the contract expands its drilling services footprint in the presalt and post-salt areas for both development and exploration wells.
SLB Launches Electric Well Control Tech to Replace Hydraulics
2025-03-04 - SLB says the new systems reduce costs and provide real-time data for operators.
Halliburton, Sekal Partner on World’s First Automated On-Bottom Drilling System
2025-02-26 - Halliburton Co. and Sekal AS delivered the well for Equinor on the Norwegian Continental Shelf.
E&P Highlights: March 3, 2025
2025-03-03 - Here’s a roundup of the latest E&P headlines, from planned Kolibri wells in Oklahoma to a discovery in the Barents Sea.
Inside Prairie’s 11-Well Program in the D-J
2025-04-08 - Prairie Operating Co.’s 11-well program in the Denver-Julesburg Basin is drilling horizontal 2-milers with a Precision Drilling rig.
Comments
Add new comment
This conversation is moderated according to Hart Energy community rules. Please read the rules before joining the discussion. If you’re experiencing any technical problems, please contact our customer care team.