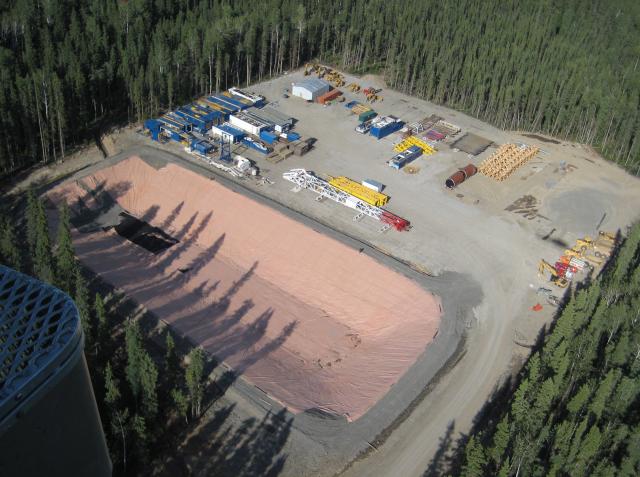
Operations that require primary and secondary containment are turning to an advanced spray-applied polyurea system. (Source: VersaFlex)
When used for primary or secondary containment, traditional coatings have been too inflexible and not sufficiently elastic to accommodate ground, concrete or metal substrate movement. This deficiency can lead to cracks or holes developing in both the substrate and the coatings, which can compromise containment.
Tough monolithic flexible coatings such as polyurea are resolving this issue for contractors, engineers and facility managers. When applied directly to concrete or metal surfaces, polyurea not only reinforces and protects the underlying substrate but also can bridge gaps or cracks of 1⁄8 in. or larger.
Polyurea is being preapplied to geotextile liners that can be quickly rolled out in sheets to protect more heavily damaged surfaces or for use in field applications such as dirt or gravel pads at drilling sites. Once installed, applicators need to only coat the seams of the liners to create a monolithic surface that is ideal for containment.
Containment requirements
Whether at refineries, industrial plants or other manufacturing facilities, federal and state regulations mandate the use of primary and secondary containment systems to keep toxic or hazardous substances from escaping into the ground and potentially entering the water supply.
Implied in this requirement is the understanding that primary containment (typically via a concrete or metal storage vessel that holds chemicals or liquids) is not foolproof. Though durable, metals corrode, and concrete cracks and is porous as well so will leach liquids if uncoated. This requires secondary containment, which often takes the form of concrete pits with barriers installed around the perimeter of a tank or other storage container.
To protect these structures, coatings such as epoxies, tars and polyurethanes often are applied as an added barrier of protection. However, these traditional coatings are frequently inflexible when cured and can crack along with the concrete.
“Typical coatings do not hold up well to substrate movement or daily, seasonal or process-related thermal expansion and contraction, which can lead to cracks and leaks,” said Jim Collins, co-owner of South Penn Resources, a company that creates containment systems in the Pennsylvania region.
After considerable research and testing, Collins turned to an advanced polyurea system from VersaFlex, a manufacturer of spray-applied polyurea for primary and secondary containment.
When applied to substrates such as concrete or steel, the spray-applied waterproof coating creates a durable, seamless, flexible and protective barrier that stops leaks and strengthens the integrity of primary and secondary containment systems. The coating exhibits superior physical properties such as hardness, tensile strength, and crack bridging and elongation up to 400% to create a robust, industrial-grade protective lining.
“Polyurea can bridge cracks as well as flex at a rate similar to concrete and steel,” he said. “This not only helps it last but also seals the concrete so it does not absorb contaminants if there is a spill inside the contained area.”
Collins also appreciates the quick return to service possible when spraying the polyurea system for containment. While traditional coatings such as cementitious, epoxies, tars and polyurethanes will prematurely fail if not installed under a relatively narrow range of temperatures, polyurea is designed for installation and use from -40 C to 177 C (-40 F to 350 F). It sets and cures quickly and will withstand decades of freeze/thaw cycling as well as wide variations of temperature and humidity.
“After spraying the polyurea, return to service is almost instantaneous, which can make a big difference in minimizing production downtime,” Collins said. “We coated about 8,000 sq ft [743 sq m] of concrete in 12 truck-offl oading areas that required drive-in containment with VersaFlex polyurea. Within minutes of spray application, trucks were safely driving across it.”
Effective field containment
Although spraying polyurea directly to the substrate has many advantages, for containment over soil, gravel or even concrete that is too damaged to be effectively rehabilitated, presprayed composite panels offer superior protection.
This coating is particularly suited for field applications that must be able to endure heavy traffic from trucks loading or unloading materials. Although plastic liners that are seam-welded together often are used for such applications, they are more easily punctured and can bunch up under heavy use.
“For primary containment at oilfield drilling sites we used to put various plastic systems on the well pads, but we moved away from that because plastic was not durable enough,” Collins said.
Repairing plastic liners also presents a problem at the seams, when damaged areas are cut out and new sections welded in, he added. “The result is a patchwork liner with seams that are prone to failure due to improper welding as well,” he said.
As a solution, he turned to geotextiles with preapplied polyurea for its durability and reusability.
“Polyurea products are so much more durable than plastics for containment systems,” Collins said. “When needed, we can custom-apply more polyurea millage to geotextile panels and berms to accommodate even the heaviest truck use and vehicle abuse.”
To verify the strength of the polyurea coating on containment mats and berms, in fact, Collins conducted a number of tests.
“I ran an 11,000-pound skid loader onto a containment mat, stood the forks straight up and tried to puncture it, but it did not puncture through,” he said, adding that the test video is on South Penn Resources’ website. “We also ran 6,044 fully loaded water trucks across a containment system, and it withstood [the truck traffic] with zero holes and no compromise to the liner.”
Collins credits both the durability of the VersaFlex polyurea and its extended recoating window for his company’s ability to extensively reuse its containment systems.
“To reuse a containment system, we’ll cut it up into rolls, roll it up and move it. Then we’ll take it back out, respray certain areas and reinstall the original containment system at another location,” he said.
“Some polyureas look fine the first time you spray them, but the preparation needed to get any seams to bond for reuse can be challenging. However, we’ve found the extended open window for recoat and repair of the VF380 polyurea allows us to easily cut out any damaged section of geotextile, put a new piece in and spray the seams to make it virtually seamless again. We get better repair and more reuse out of our containment systems.”
Have a story idea for Tech Watch? This feature highlights leading-edge technology that has the potential to eventually address real-life upstream challenges. Submit your story ideas to Group Managing Editor Jo Ann Davy at jdavy@hartenergy.com.
Recommended Reading
Matador’s Stake in San Mateo JV Rises to $1.5B After Pipeline Deal
2024-12-19 - Matador Resources closed a deal adding subsidiary Pronto Midstream to its 51%-owned joint venture with Five Point Energy.
TotalEnergies Enters 10-Year LNG Supply Deal with Indian E&P
2025-02-12 - Commencing in 2026, TotalEnergies will supply Gujarat State Petroleum Corp. with 400,000 tons of LNG, amounting to six cargoes per year, to terminals on India's west coast.
Diversified Bolts-On Appalachia Gas Production, Midstream Assets
2025-01-06 - Diversified Energy will buy Summit Natural Resources’ assets, including producing wells and coal mine methane wells, in the southern part of the Appalachian Basin.
Summit Acquires Moonrise Midstream Assets to Alleviate D-J Constraints
2025-03-10 - A Summit Midstream Corp. (SMC) subsidiary will acquire Moonrise Midstream from Fundare Resources Co. in a cash-and-stock deal valued at $90 million.
Energy Transfer’s Lake Charles LNG Closer to FID with Chevron Deal
2024-12-19 - Energy Transfer entered a 20-year agreement to supply Chevron with 2 mtpa of LNG from its Lake Charles LNG export facility, which is awaiting a final investment decision.
Comments
Add new comment
This conversation is moderated according to Hart Energy community rules. Please read the rules before joining the discussion. If you’re experiencing any technical problems, please contact our customer care team.