The objective of unconventional developments is to produce as much shale oil and gas as possible from a reservoir, but even with the most advanced EOR solutions, a large percentage remains in the ground.
According to a report by the U.S. Department of Energy’s Office of Fossil Energy and Carbon Management, “even under the best of circumstances, primary, secondary, and tertiary (enhanced) techniques can ultimately lead to recovery of 30 to 60 percent of the original oil in place,” which leaves a lot of hydrocarbons unproduced.
Operators are looking for ways to extract more oil and gas from producing wells, but they need evidence that new technologies can outperform traditional EOR solutions.
Shale Ingenuity’s SuperEOR, which has been field tested with positive results, could be one answer to the recovery conundrum. Similar to huff and puff injection, this solution involves injecting a solvent into the reservoir, which expands into a gas to drive oil out of the rock.
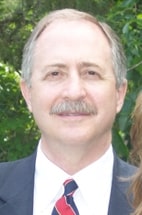
Robert Downey, CEO of Shale Ingenuity, explained the technology to E&P. “What we use is a liquid hydrocarbon solvent solution that you pump into a shale formation,” Downey said. “When you pump [the solvent] into the formation, it becomes miscible in the oil at low pressure of around 7 [PSI] or 8 PSI and the formation heats it up, but the minute you open that well to flow, that solvent wants to explode into a gas and push that oil very explosively out of the rock and up the wellbore.”
SuperEOR offers higher recovery rates and reduces production costs by about 50% compared to primary recovery methods, Downey said.
“Obviously, there are a lot of depleted shale wells out there now, and people are looking for a way to make this work, but using natural gas or CO2 just doesn’t work very well, even without having all the fracturing issues,” Downey said.
SuperEOR works at lower bottomhole pressures than natural gas or CO2 because the solvent is miscible in the formation oil at much lower pressure. Because it has much greater viscosity, it is also much less likely to move into fractures in offset wells.
The recovered solvent, which is gathered by a special solvent recovery unit, significantly improves oil recovery. According to Downey, the company’s proprietary solvent not only improves production up to 500% more than traditional methods, but also can be recovered from the rock and reused.
How it works
“The big problem when injecting natural gas into these shales is that you get to a certain bottom of pressure and the natural fractures that are in the shale start opening up. Then the gas wants to move into the shale fractures and bypass the matrix. It doesn’t go into the matrix and become miscible in the oil, so you end up pushing the gas to an offset well, and you don’t get good oil recovery,” Downey said.
Shale Ingenuity’s solution works differently. “We don’t have that problem because when you inject the liquid and you don’t have to go to this high bottomhole pressure, you don’t activate those fractures,” he explained. “The liquid goes right into the shale oil in the formation and then you flush it back out.”
This closed-loop system minimizes environmental impact and has the potential to cut greenhouse-gas emissions from oil production by up to 75%, Downey said.
“At the surface, your production goes to the tanks, your gas goes to your gas gathering line, the solvent gets stored as a liquid on the surface, and then you reinject it with a triplex pump. It’s all closed loop; so the environmental impact is much lower,” Downey said. “In fact, you could even take your solvent recovery unit and do some additional things on there to further reduce the already limited air emissions.”
As project size increases, efficiency improves. Similar to a gas processing plant, a large-scale operation is highly scalable. The cost per 1,000 cf decreases substantially as plant size grows.
The cost of using SuperEOR in oil production is approximately $17/bbl, making it much less expensive than other EOR methods, Downey said. “Historically, the high cost per barrel and challenges related to gas containment have hindered the success of natural gas and CO2 huff and puff shale oil EOR projects.”
“If you wanted to do a project of 60 wells, the economics for that are going to be better than a project with 10 wells,” Downey told E&P. Operators might break even on a 10-well project after six or seven months, but with a 60-well project using SuperEOR, “you’re looking at a return on investment of seven to 10 times your money and payouts in six to seven months,” he said.
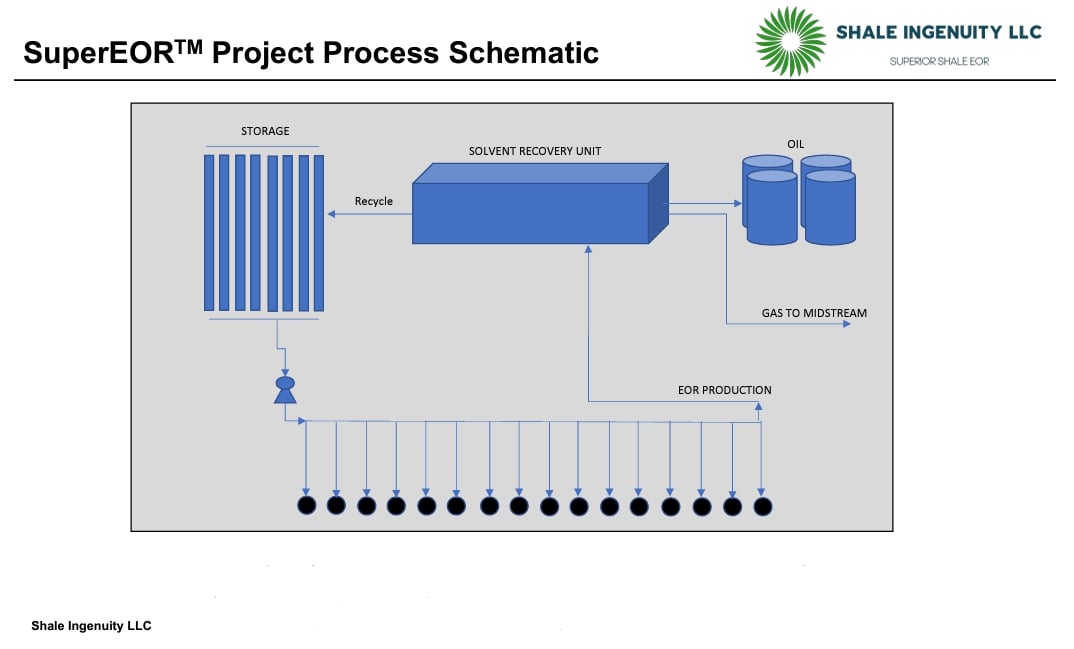
(Source: Shale Ingenuity)
Putting the solution to the test
The new technology has been modeled and tested across various shale plays, including the Utica and Eagle Ford shales, and the Powder River Basin.
A field test in the Eagle Ford demonstrated the efficacy of the solution. According to Downey, using the proprietary solvent enabled a 44% increase in oil recovery and a rise in production from 13 bbl/d to 390 bbl/d in only 10 months. The closest results achieved using traditional recovery methods Downey found was a program for EOG that achieved 35% recovery, but only after five years. Other EOR solutions were unable to reach even that threshold, he said.
Variations on a theme
Shale Ingenuity also developed a technology called UltraEOR that incorporates a technique called Cycle Stim, which uses cyclic hydraulic fracturing to create numerous small shear fractures in the wellbore. This process increases the surface area available for solvent contact, and Downey said he expects this solution to double the oil recovery rates achieved by the earlier product. Although not yet field-tested, the technique has the potential to increase oil recovery by 1,000%, Downey said.
The solution is both versatile and cost effective, Downey explained: “Cyclic stimulation will work on vertical wells, horizontal wells, conventional wells, unconventional wells, oil, gas, low perm, high perm, old wells and new wells. It’s about 20% to 50% of the cost of a typical frack job.”
The process uses less fluid and sand, requires no chemicals, and needs fewer people on location to deploy it, Downey said.
The industry has been slow to adopt Cycle Stim due to its complexity and the preference for traditional fracking methods, Downey said, but he is optimistic that the technique’s lower cost and reduced environmental footprint will be compelling reasons to test it in the field. He believes the results will lead to widespread use.
Drivers for change
As the oil and gas industry grapples with the realities of diminishing shale reserves, the emergence of innovative technologies could significantly impact recovery and economics. Advanced extraction methods like these not only promise to rejuvenate aging wells but also offer a more sustainable and cost-effective solution for enhancing production. Although industry inertia may slow widespread adoption in the near term, the potential benefits—ranging from significant increases in oil recovery to substantial environmental improvements—are drivers for change.
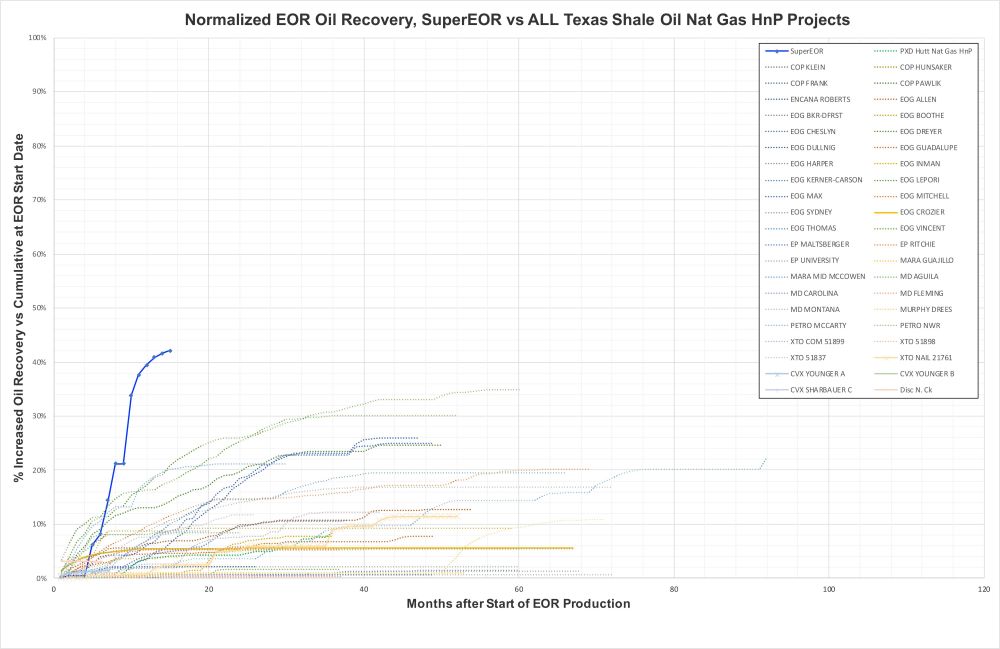
Recommended Reading
Eversource Energy Agrees to Sell Aquarion Water Co. in $2.4MM Deal
2025-01-28 - Eversource Energy plans to use the proceeds to pay down debt and reinvest into its core electric and natural gas businesses.
Tidewater Midstream Closes CA$24MM Alberta Roadway Sale
2025-03-25 - Tidewater Midstream and Infrastructure agreed to sell the roadway network, located around the Brazeau River Complex, to Canadian Resource Roadways for CA$24 million (US$16.8 million).
Golden Gate Capital Completes Stonehill Environmental Sale
2025-03-12 - Private equity firm Golden Gate Capital has completed the sale of energy infrastructure company Stonehill Environmental Partners for an undisclosed amount.
Woodside Divests Greater Angostura Assets to Perenco for $206MM
2025-03-28 - The Greater Angostura field produces approximately 12% of Trinidad and Tobago’s gas supply, said Woodside CEO Meg O’Neill in a press release.
Obsidian to Sell Cardium Assets to InPlay Oil for US$225MM
2025-02-19 - Calgary, Alberta-based Obsidian Energy is divesting operated assets in the Cardium to InPlay Oil for CA$320 million in cash, equity and asset interests. The company will retain its non-operated holdings in the Pembina Cardium Unit #11.
Comments
Add new comment
This conversation is moderated according to Hart Energy community rules. Please read the rules before joining the discussion. If you’re experiencing any technical problems, please contact our customer care team.