
After acquiring Plow Technologies, home of the OnPing SCADA platform, PakEnergy looks to enhance its remote monitoring solutions. (Source: Shutterstock)
Two tailwinds have driven the oil and gas industry in the past year: consolidation and efficiency.
During a 12-month period ending in March, E&Ps have seen a remarkable run of consolidation, with more than $250 billion transacted. Service companies have also been following suit with their own deals, as they, too, concentrate on streamlining and improving offerings.
Among the din of M&A, oilfield software companies have also been combining, including PakEnergy, an automation technology company that recently acquired Plow Technologies.
In an industry packed with SCADA applications used to control, monitor and analyze industrial devices and processes, Plow and PakEnergy’s combination might have been easy to miss. But company executives said their combined computing prowess will take oilfield service automation even further.
Plow Technologies’ oil patch offering is the OnPing platform, a cloud SCADA platform for oil and gas applications.
OnPing simplifies the creation and management of automation systems and ensures reliability, accessibility and integration with various devices and systems. With features like drag-and-drop configuration, real-time polling and mobile accessibility, OnPing helps users monitor and control their operations from anywhere, making data more accessible to drive business decisions.
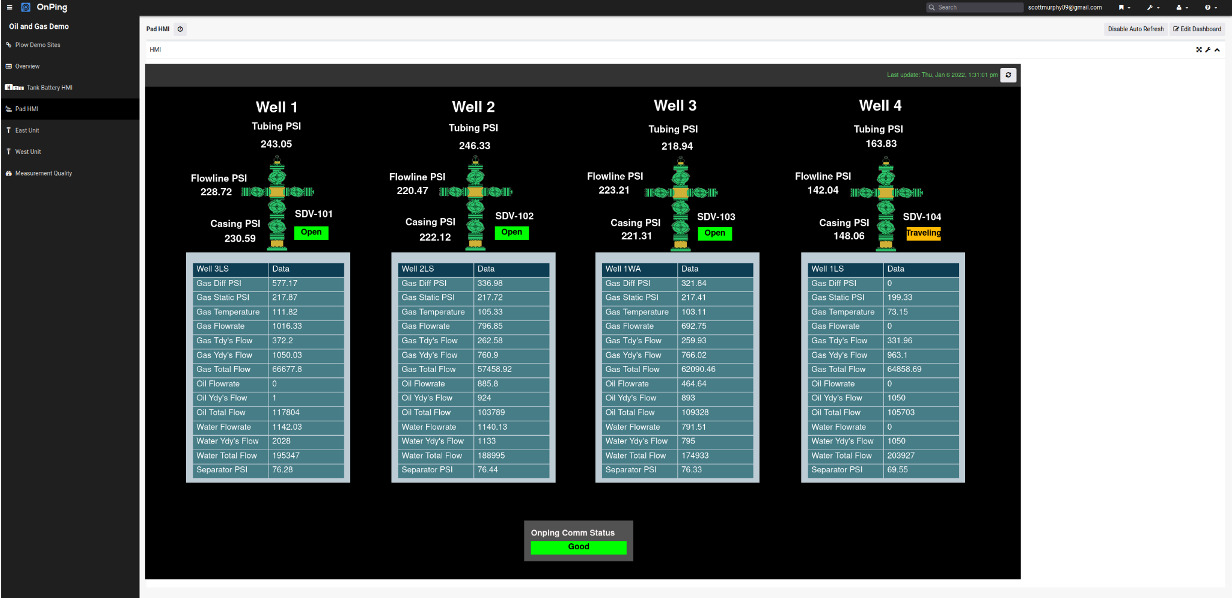
OnPing’s strength is in grabbing data and performing calculations on it.
“One of the things that Pak Production is really good at is change management of change tracking and those side of things. So we just let each thing shine at what it does,” Scott Murphy, co-founder of Plow Technologies, told Hart Energy.
PakEnergy is crafting tools to integrate with SCADA systems as well as augment any manual data entry needed. So while OnPing is designed around real time information, PakEnergy works to help data provide a “richer story,” said Murphy.
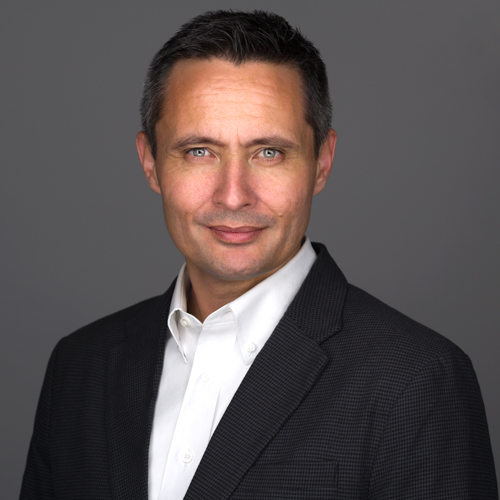
“We have machine information, but there’s obviously a lot more to the wellsite than what the machines are telling you. There’s information about how things need to be allocated, about how different wellsites are set up, about the history of the equipment on site,” said Murphy. “This collaboration is going to allow us to mix that machine information with those other sources of information to tell a complete story of an individual wellsite from the point of view of an operator.”
Industry software can be tailor-made to a fault. OnPing offers users a more seamless experience that doesn’t require repeatedly logging in to various different applications. OnPing, executives say, also offers flexibility, speed and reliability that the existing hodgepodge of software platforms may not.
“Most oilfield SCADA systems got started in some application… so it’s really good at displaying midstream data or really good at displaying some set of oilfield stats,” he said. “But what you’ll see is that they start to get stressed out whenever you move away from that view.”
OnPing, which started as an automation product working for “10 or 11 different companies,” said Murphy, helps operators navigate the chaos that comes from fulfilling different jobs.
Working for a variety of companies with different demands for their online SCADA systems developed OnPing’s ability to work with any of those environments. This flexibility enables OnPing’s speedy operations.
“So what [OnPing] allows [operators] to do is stay within a single application to get not just the high-level granular contextual information, but also that the story that really generates true actionable insights all within a single application,” said Paul Marino, general manager of production at PakEnergy.
OnPing’s speedy operations also enhance its reliability, executives said.
“We are huge believers that the best way to have a system that is always right is to make it so that when you find something wrong, you can fix it as fast as humanly possible,” Murphy said. “You’ll never see something in OnPing where you see it wrong and have got to wait for these seven templates to get fixed before we can make an adjustment. Instead, you can make an adjustment right there and then worry about the template afterward and that just makes things right more than it’s wrong.”
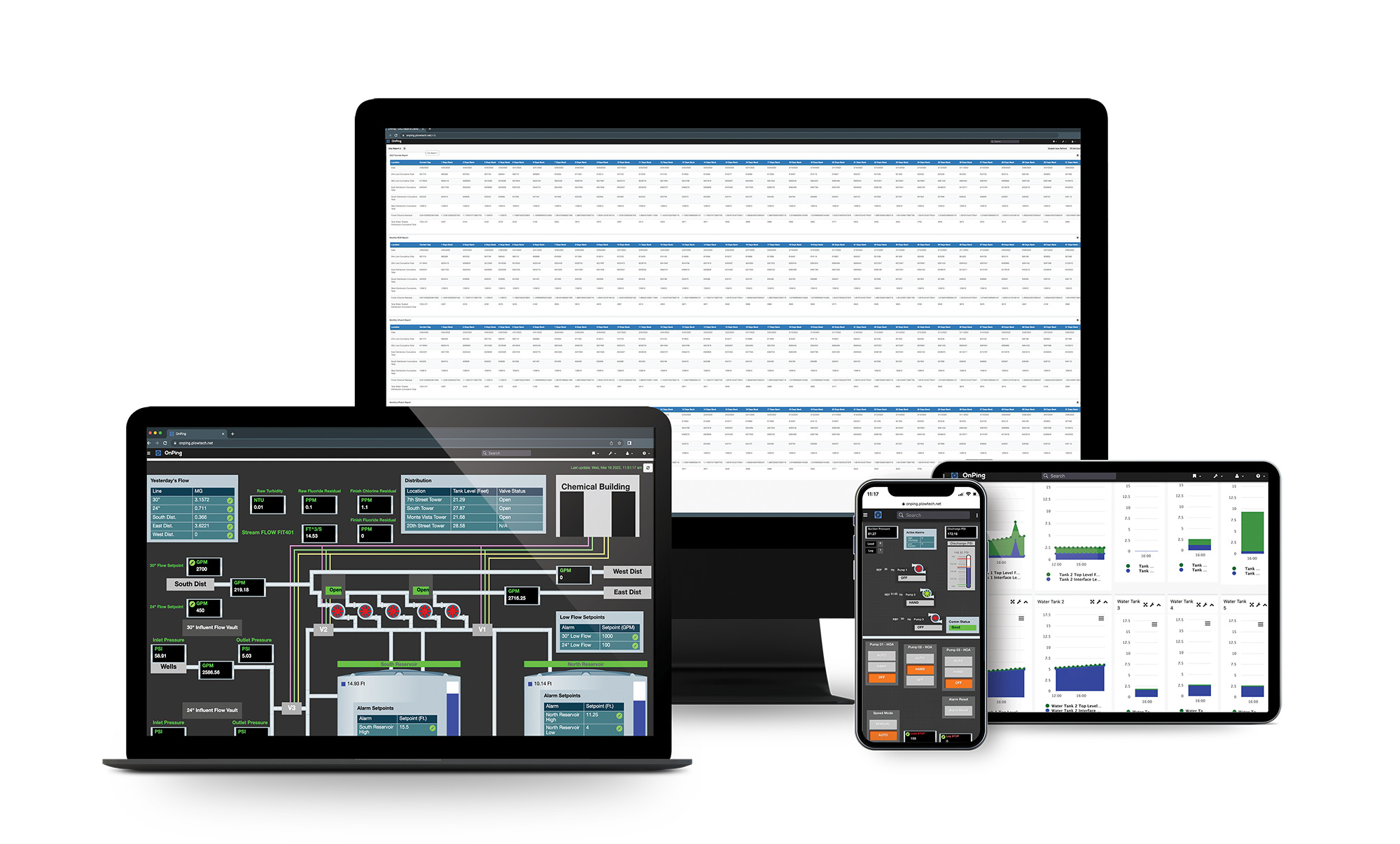
OnPing in action
The flexibility, speed and reliability of OnPing prompted Oklahoma operators familiar with the platform to refer it to a private operator in West Texas that had too many “hands in the kitchen.” With disparate automation systems, the situation was confusing, Murphy said.
OnPing provided the operator remote access to customized control and feed data into PakEnergy’s field data capture solution.
“We were able to get all of their data just to be super clean and reliable at the point, so that company then had an exit and were actually purchased by a larger company,” Murphy said.
Data issues, along with emission detection and regulatory compliance, aren’t uncommon for smaller operators that don’t have the same capabilities as better funded, larger operators.
Smaller operators often don’t have the luxury of standardizing a particular solution for emissions or regulatory compliance. For example, a solution for one set of equipment might not work for another, Marino said.
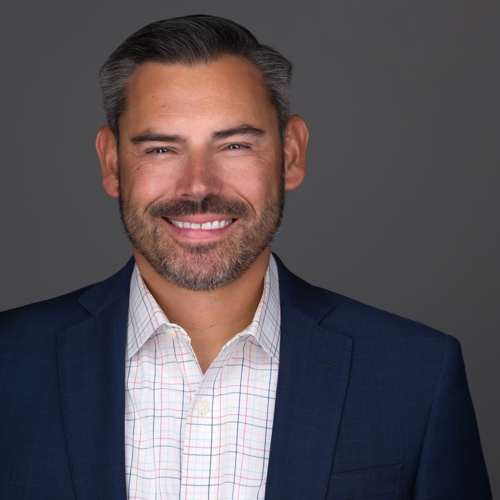
OnPing can help smooth that out, removing the need to send someone to the field to detect or capture emissions data that in turn are manually sent up the chain.
“You’re able to respond much quicker to those things to ultimately help them reach their goals,” Marino said. “We see this as bringing the modern technology stack and the tools that larger operators have to the smaller operators.”
Despite only recently being acquired by PakEnergy, the collaboration between Plow and PakEnergy is a “proven integration,” said Murphy—one that’s been used by multiple operators for years.
And while the PakEnergy-Plow collaboration may have just started officially, Murphy already has his eyes set on the future for PakEnergy.
“I’m excited about allowing some of this machine data to take even more advantage of the well information and other pieces of Pak Production, and deepening our integration with other parts of the Pak family of tools like the accounting pieces or some of the land pieces. We can really just build a full portfolio that’s available back up and down the value chain.”
Recommended Reading
Trump Administration to Open More Alaska Acres for Oil, Gas Drilling
2025-03-20 - U.S. Interior Secretary Doug Burgum said the agency plans to reopen the 82% of Alaska's National Petroleum Reserve that is available for leasing for development.
Electron Gold Rush: ‘White Hot’ Power Market Shifts into High Gear
2025-03-06 - Tech companies are scrambling for electrons as AI infrastructure comes online and gas and midstream companies need to be ready, Energy Exemplar CEO says.
Halliburton, Sekal Partner on World’s First Automated On-Bottom Drilling System
2025-02-26 - Halliburton Co. and Sekal AS delivered the well for Equinor on the Norwegian Continental Shelf.
TGS to Reprocess Seismic Data in India’s Krishna-Godavari Basin
2025-01-28 - TGS will reprocess 3D seismic data, including 10,900 sq km of open acreage available in India’s upcoming 10th Open Acreage Licensing Policy (OALP) bid round blocks.
Artificial Lift Firm Flowco Prices IPO Above Guidance at $427MM
2025-01-15 - Flowco Holdings priced its IPO at $24 per share, above its original guidance. The oilfield services firm will begin trading on the New York Stock Exchange on Jan. 16.
Comments
Add new comment
This conversation is moderated according to Hart Energy community rules. Please read the rules before joining the discussion. If you’re experiencing any technical problems, please contact our customer care team.