
(Source: huyangshu/Shutterstock.com)
Presented by:

This article appears in the E&P newsletter. Subscribe to the E&P newsletter here.
The vast reservoirs of oil and gas stored under the seafloor offer great opportunities for many operators. However, deepwater drilling operations also present unique well construction challenges, including increased risk of accidents, spills and well control events.
To ensure the safety of both personnel and the asset, mitigating the risks associated with deepwater drilling is crucial, with leakage prevention and pressure testing playing a vital role.
Despite pressure testing being imperative for the success of the project, when using traditional subsea well cementing methods, the process of pressure testing often introduces unique complexities, if it is possible at all, creating a greater chance for accidents to occur.
The conventional methods
The subsea well cementing status quo currently involves the use of the poor boy inner string method and subsurface release (SSR) plug method. The standard poor boy inner string cement job involves running an inner string to within a pre-designed distance of the float shoe and making this up to the running tool. The cement job is then pumped and displaced, leaving a designed shoetrack length to try and guarantee quality cement at the shoe. Alternatively, a landing collar is run at the top of the casing shoetrack, with SSR plugs and darts loaded into the wellhead assembly and cement head respectively. The cement job is then pumped and displaced, and a casing pressure test can be carried out upon plug bump in the landing collar.

The importance of the seals
The sealing reliability of the running tool is imperative. When installed at the wellsite, there is little capability to fully pressure test the entirety of the sealing mechanism prior to running the system from the deepwater MODU.
Therefore, it is crucial that the ball valves as well as other elements, such as the non-productive time (NPT) fittings or o-rings, are all properly sealed for the duration of the running in hole and cementing operations, as any potential leakage could result in a significant NPT event.
There are several mechanisms of mitigation, with some operators applying a dual ball valve setup to de-risk the process. This dual ball valve set up provides secondary protection with the expectation that if the bottom valve has a leak, the top one will provide a sealing capability to continue with the job. In the instance that the leak emanates from the NPT fittings, no such mitigation exists and the issue will not be visible until operations have begun.
Breaking the status quo
DeltaTek’s flagship technology, SeaCure, is a pioneering subsea cementing system, delivering stabbed-in inner string cementing to any casing or liner. The novel system provides a number of risk mitigations to cementing operations as well as a range of major cost and time benefits to drilling and field development operations.
Inner-string cementing involves a drill pipe being run inside the casing and utilized as a conduit to place and displace the cement job; it is generally considered to be a more efficient technique as it allows better control of cement displacement and fluid interfaces.
The conventional cementing processes utilize shoe tracks of cement or plugs and landing collars, with pressure tests to confirm the integrity of the cement job conducted once the cement has set or upon plug bump. SeaCure’s zero shoetrack solution removes the requirement for shoe tracks and eliminates clean out runs entirely, whilst significantly reducing displacement volume and providing Ultimate Cement Placement in primary cementing operations. The zero shoetrack solution also improves drill-out performance, with SeaCure shoes drilling out in an average time of 20 minutes while reducing the risk of BHA and casing ID damage that can occur when drilling out conventional shoetracks. Furthermore, DeltaTek’s SeaCure system is the only industry method of conducting a green cement casing pressure via an inner string, reducing the likelihood of micro annuli formation.
SeaCure brings the age-old strategy of stabbed-in inner string cementing, which has historically only been possible on land wells or platform wells with a surface wellhead system, to the subsea environment.
Removing pressure from pressure testing – the case study
In 2019, DeltaTek was commissioned to support the operations of a deepwater E&P operator in the Mediterranean Sea.
The deployment of DeltaTek’s novel cementing technology allowed the operator to successfully pressure test the casing and running tool, prior to running from a sixth-generation drill ship.
Operating at a water depth of 1750 m, DeltaTek’s SeaCure cementing technology supported the delivery of:
- Pre-installation casing pressure testing;
- Green cement casing pressure test via inner string, prior to running BOP;
- Drill-out optimization;
- Saved bit life;
- Saved mud system from green cement contamination;
- Minimized cement volume pumped;
- Minimized cement contamination; and
- Minimized displacement volume.
The operator had previously faced challenges whilst drilling out the shoetrack of their 20-inch surface casing, as well as experiencing issues related to poor quality cement jobs and pressure testing using conventional techniques.
The key challenges included:
- Hard drilling with dulled bit from cement drilling in shoetracks;
- Mud contamination due to green cement contamination; and
- Pressure testing casing against green cement in shoetracks.
SeaCure delivered low risk, high value cementing operations while ensuring the hydraulic integrity of the casing.
Risk mitigation: Pressure testing seals via top filling air gap (~50psi)
Once the inner string has been stabbed and latched into the shoe, a hydraulic seal has been established at the bottom of the casing. This allows the top filling of the air gap between sea level and the rotary table, with this low pressure test giving the first indication that the system is hydraulically sealing.
This would not be possible with the traditional poor boy inner string method of running a drill pipe “stinger” within a pre-determined distance of the float shoe, as any additional fluid installed in that point would simply drain down through the float mechanism. However, the stabbed-in and latched-in SeaCure system isolates the shoe, allowing the fluid level to be filled to the rotary table.
Regular deepwater MODUs have an 80-90 ft air gap (25-30 m) which, when filled with a sea water gradient, provides a 50 psi hydrostatic pressure test on the casing and inner string. When the fluid level was successfully brought back, the 50 psi hydrostatic has been established on all of the casing couplings and the inner string, bringing confidence that the system is sealing to at least 50 psi.
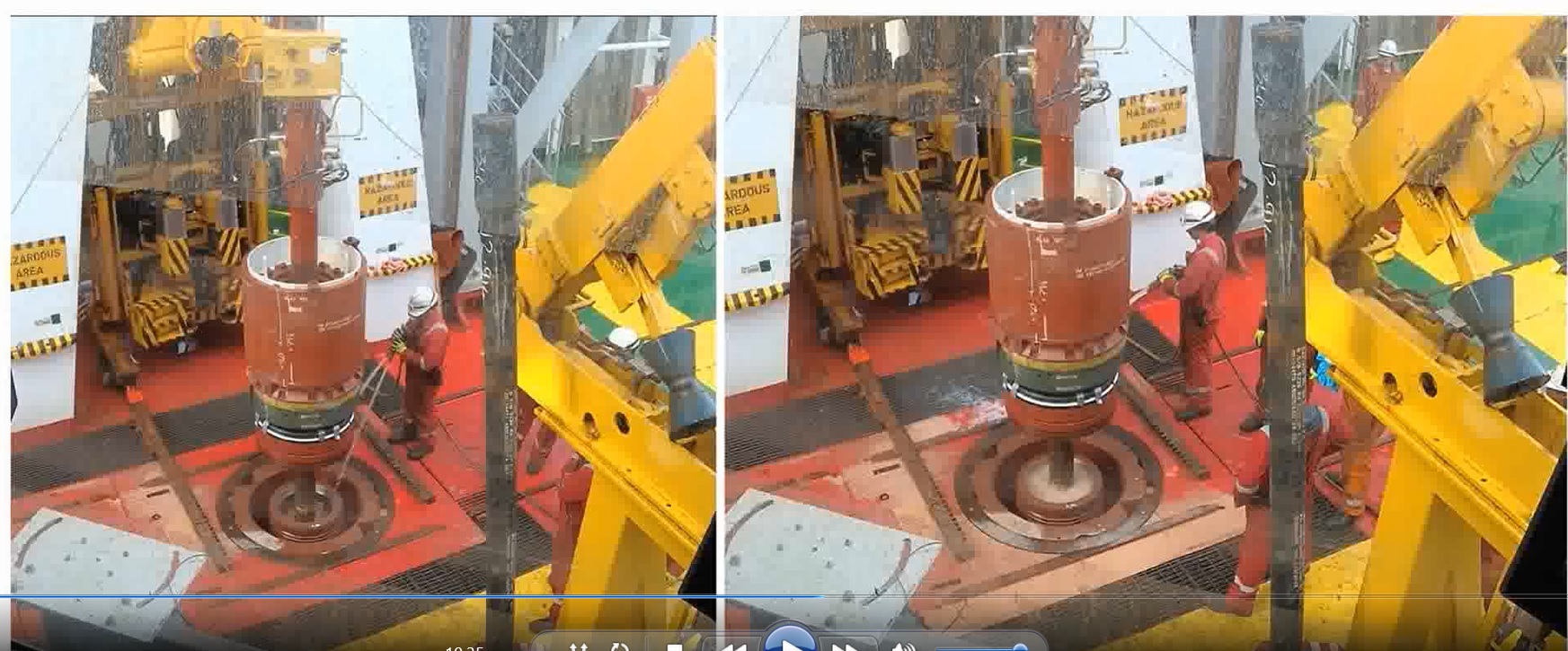
Risk mitigation: Additional pressure testing via test line (~500psi)
Once the high pressure wellhead housing running tool has been installed, the next step involves manifolding in via the ball valve on the running tool and adding additional pressure to the entire casing bore whilst in the offline, or auxiliary, position of a deepwater drillship.
This proves that every casing coupling has been properly made up and is hydraulically sealing. It also validates that the secondary seals for the cement job of the casing running tool itself, which are now redundant, have been pressure tested to more than they would be required to during the subsequent pressure testing operations.
This operation involved testing the casing and running tool to 500 psi, which marked the first application of SeaCure in a greater than hydrostatic pre installation casing pressure test setting.

The result
The deployment of DeltaTek’s SeaCure cementing system allowed the operator to move the sealing mechanism from the wellhead down to the shoe in this deepwater application.
The stabbed-in inner string technology provided an optimized solution and delivered value through providing the capability to fully pressure test the casing prior to running in hole, as well as allowing for a post cement job casing pressure test on green cement via the inner string.
The project was delivered on time and within budget, with zero NPT observed. The zero shoetrack solution also allowed a rapid and reliable drill out with the SeaCure compatible shoe drilling out in just six minutes, saving rig time and removing the risks associated with the drill out of conventional shoetracks.
The technical highlights of the project included:
- 500 psi casing pressure test before running the string subsea;
- 2700 psi post cement job test on green cement;
- No mud related conditioning time or cost for cement contamination;
- Bit drilled to TD and was graded 1-2 after pulling out of hole; and
- No BHA failures in next section.

The ultimate cement placement technology of the future
Launched in 2015, DeltaTek’s disruptive innovations, including the full Cure range and ArticuLock, were created in response to the growing requirement for simple, cost-saving and value-adding products.
Bringing efficiency to operations is a priority for the oil and gas industry and advances in drilling technologies are proving essential for optimizing production, reducing costs and reaching untapped reservoirs.
As we begin to unlock these challenging reservoirs, the need for innovation as well as collaboration between industry stakeholders remain fundamental to deliver results and optimize production into the future.
About the author: Tristam Horn is the CEO of DeltaTek.
Recommended Reading
Phillips 66 Buys EPIC’s Permian NGL Midstream Assets for $2.2B
2025-01-07 - Phillips 66 will buy EPIC’s NGL assets, including a 175,000 bbl/d pipeline that links production supplies in the Delaware and Midland basins and the Eagle Ford Shale to Gulf Coast fractionation complexes.
CNX’s $505MM Bolt-On Adds Marcellus, Deep Utica in Pennsylvania
2024-12-05 - CNX Resources CEO Nick Deluliis said the deal to buy Apex Energy underscores CNX’s confidence in the stacked pay development opportunities unlocked in the deep Utica.
Talos Sells More of Mexican Subsidiary to Billionaire Carlos Slim
2024-12-17 - Talos Energy has agreed to sell another 30.1% interest in subsidiary Talos Mexico to entities controlled by billionaire Carlos Slim, whose companies also own at least 24% of Talos Energy’s common stock.
Constellation Bets Big on NatGas in $16.4B Deal for Calpine
2025-01-10 - Constellation Energy will acquire Calpine Corp. in a $26.6 billion deal, including debt, that will give the pure-play nuclear company the largest natural gas power generation fleet.
After Big, Oily M&A Year, Upstream E&Ps, Majors May Chase Gas Deals
2025-01-29 - Upstream M&A hit a high of $105 billion in 2024 even as deal values declined in the fourth quarter with just $9.6 billion in announced transactions.
Comments
Add new comment
This conversation is moderated according to Hart Energy community rules. Please read the rules before joining the discussion. If you’re experiencing any technical problems, please contact our customer care team.