
The FIFISH can be equipped with a plethora of tools for subsea work, ranging from a robotic arm to sonar. (Source: QYSEA)
As children, nearly everyone is taught to not judge a book by its cover. This life lesson reaches far and wide and high and low—even as low as 1,150 ft subsea. QYSEA’s FIFISH ROV is the latest lesson in underestimation.
“We are the first compact size underwater robot to achieve full omnidirectional mobility—six degrees of freedom,” Curtis Lee, overseas marketing and development specialist for QYSEA, told Hart Energy. “This is useful for and beneficial for various types of inspections in shipping and offshore and much more.”

Compared to the traditional box-shaped design of most ROVs, the droplet shape of the FIFISH V6 allows for more hydrodynamic capability, Lee said. This shape reduces drag and allows the unit to move against and through currents with greater efficiency and speed. The shape of the V6 also allows for more precise control of the ROV and helps it save energy as it moves more smoothly and no longer has to fight against currents, he continued.
Along with the droplet shape of the ROV, it is quite small with 15x13x5 ⅝-inch dimensions. The V-series models of the FIFISH weigh less than 10 lb, while the Pro W6 model weighs around 50 lb.
Even with its small size, the vehicle is adaptable. It can hold sonar, GPS, additional power supply systems and even integrate a robotic arm, Lee said. Each FIFISH is equipped with a 4K UHD camera, lights as bright as 6000 lumens and a 166-degree field of view.
“In addition to that, we have developed an aerial drone with virtual reality head tracking control. You wear the VR goggles and you can control where the drone looks simply by moving your head,” Lee said.
While there are players with more experience in the subsea market, Lee said QYSEA’s “huge R&D department” has allowed them to make up for any lack of experience. The FIFISH is relatively easy to deploy and can dive up to 1,150 ft while maintaining control against currents up to three or four knots.
“It's a capable, convenient, low-cost tool for inspecting the structures and conditions of your platforms. That includes oil and gas, as well as the offshore wind farms,” Lee said.
Traditional inspections, up to a certain depth, oftentimes need to be conducted by skilled commercial divers, but he believes the FIFISH is a great solution—not replacement—to work together with commercial divers and increase the efficiency of the entire offshore operation.
“For example,” Lee continued, “underwater ROVs like the FIFISH can reduce the risks of basic inspection tests of commercial divers and even make the first dive to ensure there's no issues around the structures.”
Swedish-owned energy company Vattenfall is taking advantage of the size of the FIFISH, having commissioned FIFISH to inspect nuclear plants. GE has also used the FIFISH to inspect hydropower turbines, as it is the only inspection tool small enough to fit in the compact spaces around the turbines.
Still room for improvement
Although the FIFISH presents many solutions for subsea problems, QYSEA is still determined to improve its system.
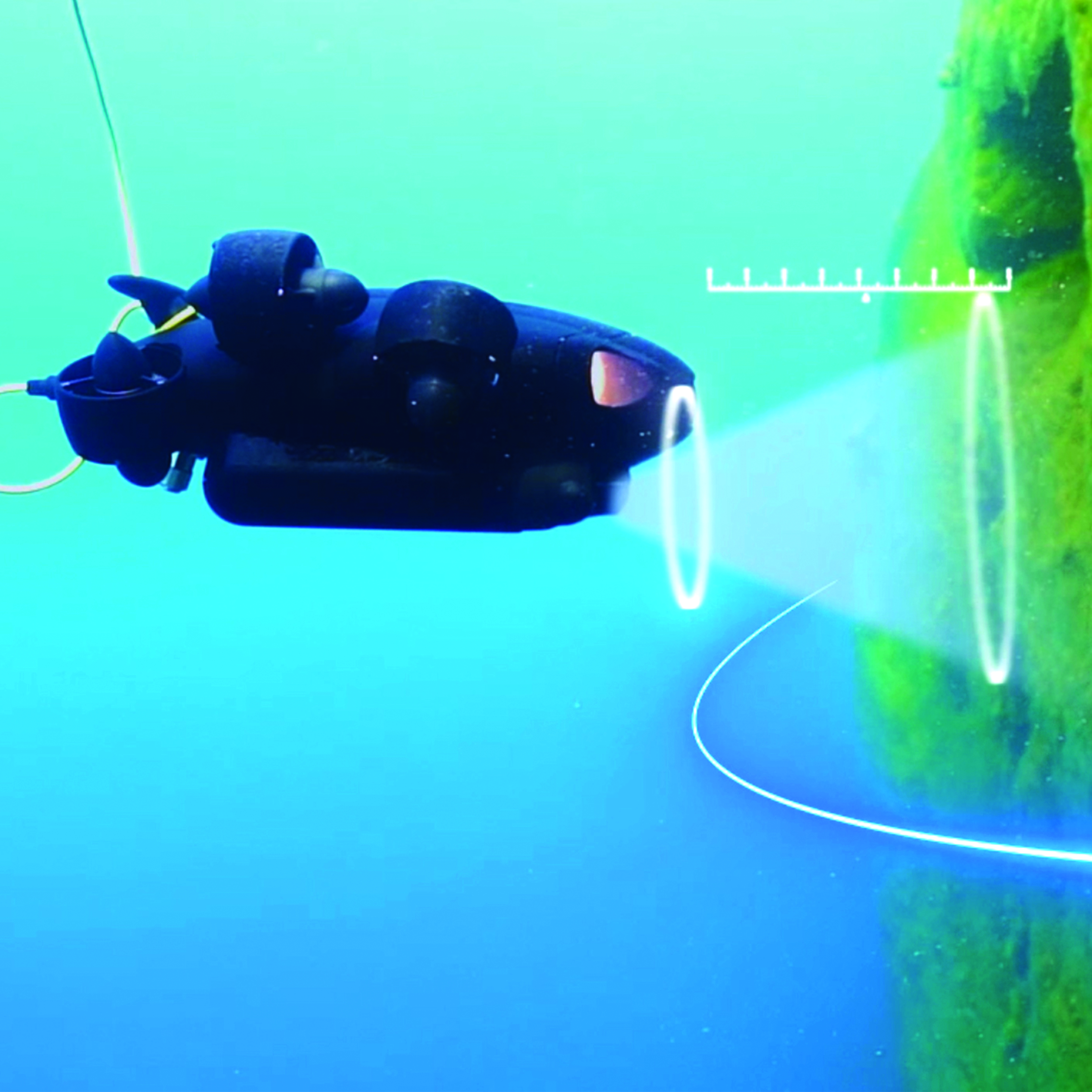
“There are a lot of industry bottlenecks that we are trying to break through. Right now, developing wireless underwater drones is very difficult. The signal is very weak in underwater conditions, which is why you see many ROVs always have to be wired underwater,” Lee said. “Creating an effective wireless underwater control is something we're working on. We’re trying different types of technologies to make long distance, deep sea wireless remote control possible.”
QYSEA aims to add more artificial intelligence (AI) into their vehicles, enabling them to adapt more easily to currents and transform the industry as a whole.
“We want to change the way light work class ROVs are seen. Traditional light work class ROVs weigh thousands of kilograms and are box-shaped for effectiveness against deep sea currents,” Lee said. “We're working on a much lighter version that can fight currents of up to five or six knots using AI technologies and adaptive algorithms to sense where the waves are coming from and using models to fight against the current. Operating out deep at sea without sacrificing time and size are the big problems we're working to solve for the industry.”
Recommended Reading
Enchanted Rock’s Microgrids Pull Double Duty with Both Backup, Grid Support
2025-02-21 - Enchanted Rock’s natural gas-fired generators can start up with just a few seconds of notice to easily provide support for a stressed ERCOT grid.
E&P Highlights: April 7, 2025
2025-04-07 - Here’s a roundup of the latest E&P headlines, from BP’s startup of gas production in Trinidad and Tobago to a report on methane intensity in the Permian Basin.
US Drillers Cut Oil, Gas Rigs for First Time in Three Weeks
2025-03-28 - The oil and gas rig count fell by one to 592 in the week to March 28.
McDermott Completes Project for Shell Offshore in Gulf of Mexico
2025-03-05 - McDermott installed about 40 miles of pipelines and connections to Shell’s Whale platform.
E&Ps Pivot from the Pricey Permian
2025-02-01 - SM Energy, Ovintiv and Devon Energy were rumored to be hunting for Permian M&A—but they ultimately inked deals in cheaper basins. Experts say it’s a trend to watch as producers shrug off high Permian prices for runway in the Williston, Eagle Ford, the Uinta and the Montney.
Comments
Add new comment
This conversation is moderated according to Hart Energy community rules. Please read the rules before joining the discussion. If you’re experiencing any technical problems, please contact our customer care team.