
Smart technology can automate manual tasks which promotes greater safety at the wellsite as well as greater efficiency. (Source: Caterpillar Oil & Gas)
The principles behind smart technologies for drilling rigs and engines aren’t astonishingly clever. By way of example, consider an oil patch engine. Run it less and it requires fewer repairs and consumes less fuel.
The trick is in the first part, the “smart.” Fine tuning an engine or a rig to do the same job with less effort, power or worker’s time can require marrying technology together with a hodgepodge of rigs, engines and other equipment of various vintages.
Success includes spotting problems before they creep up, making jobs safer and saving money.
However, as companies strive to modernize their fleets, they face a range of challenges and limitations that can complicate implementation.
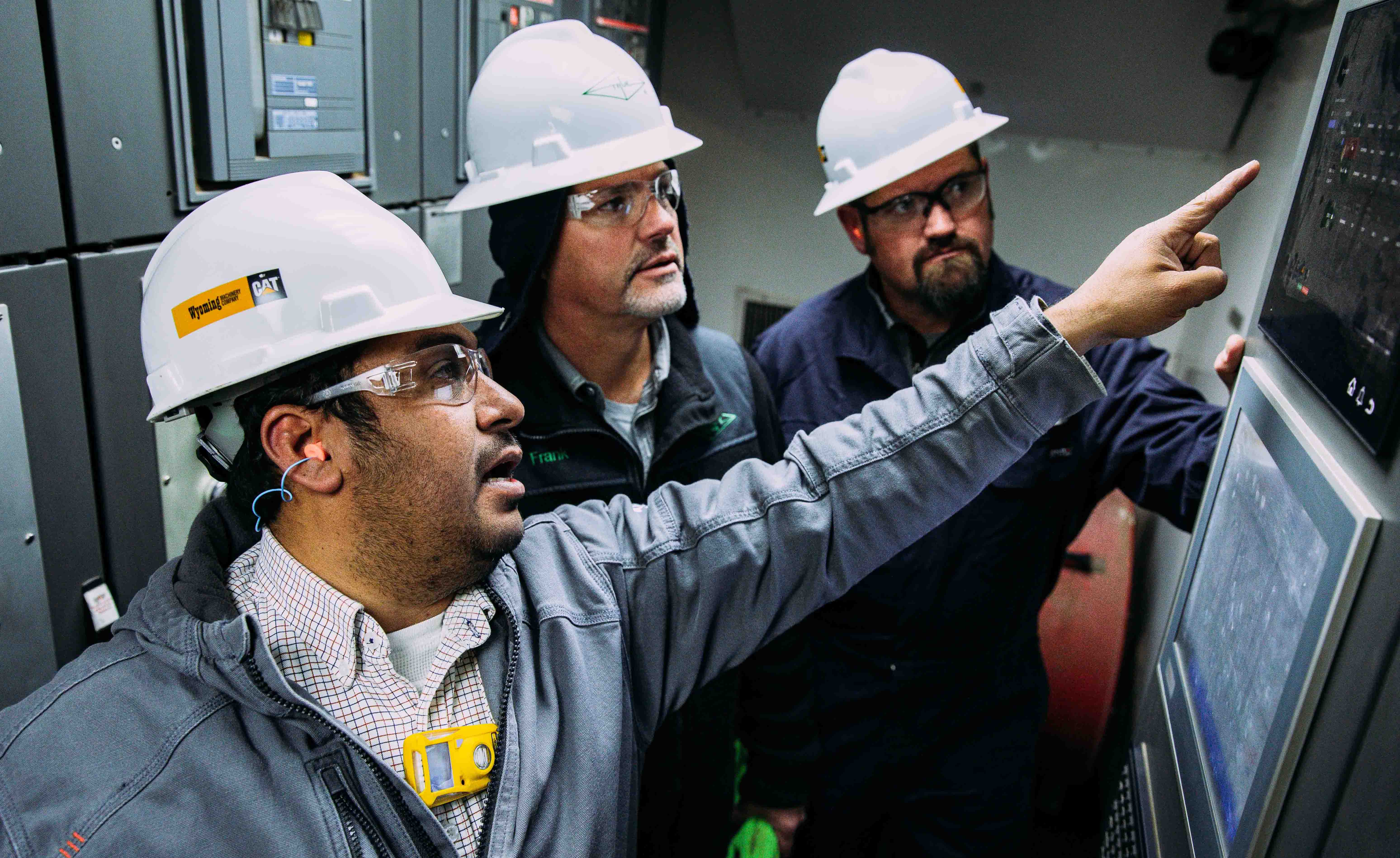
The problem of old, new equipment
Caterpillar Oil & Gas touts the value of having controls on-site and ease of integrating smart technology. Smart Engine Controls are designed specifically for drilling rigs to work with Caterpillar digital products. One of those technologies is the smart Engine Management System (EMS), a fully automated solution that optimizes power management by intelligently managing multiple configurations of engine and generator operations. By turning engines on or off based on real-time demand, the EMS ensures that power is utilized efficiently, reducing fuel consumption and operational costs.
But despite all the advancements the EMS affords operators, not all drilling rigs are created equal, Steven Youssef, senior account manager at Caterpillar, told Hart Energy.
“Drilling is one of the oldest industries, so when operators want to incorporate newer technologies to their older rigs, they have to consider how feasible it is to retrofit their existing rig,” he said. “Meanwhile, newer rigs may have compatibility issues depending on the existing control systems and infrastructure.”
This can create hurdles, as operators strive to improve efficiency on-site and navigate the complexities of integrating advanced technologies into established infrastructures.
Building for the oil patch
The oil and gas sector operates in some of the world’s most challenging environments, from extreme temperatures to corrosive atmospheres. Smart technologies must be purpose-built to endure such conditions. Developers have to build adaptable tools to account for high heat, freezing temperatures and dusty environments to ensure reliability and performance.
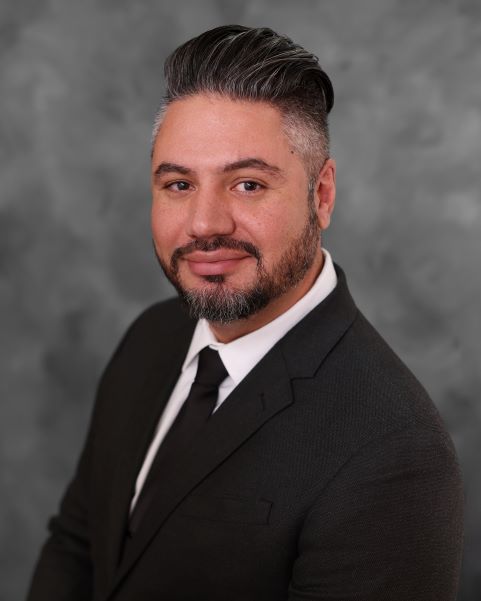
“The robustness of OEM systems like the Cat engine controller lies in in their engineering, which ensures that they continue to perform in the field. …You take it a step further by field testing it on-site, in real conditions,” Youssef said. “Then you can monitor key engine metrics in real time and make sure that the system is making adjustments to ensure optimal efficiency and reliability regardless of those external conditions.”
Traditional operational methods often require personnel to be in close proximity to potentially hazardous equipment.
By reducing the need for human intervention—tasks like the manual inspection of equipment and operating engines—smart technology minimizes risk and allows operators to monitor systems remotely. Instant alerts for overheating or underperformance enable swift responses, further safeguarding personnel and equipment.
“Operators can leverage smart logic through things like HMI [human machine interface], where it allows them to remote control and monitor equipment from a remote location,” Youssef said. “The HMI screen provides real-time insights into the equipment status, how it’s running, how it’s performing and any issues” that arise.
And while these improve operational safety, implementing smart technology can yield financial benefits.
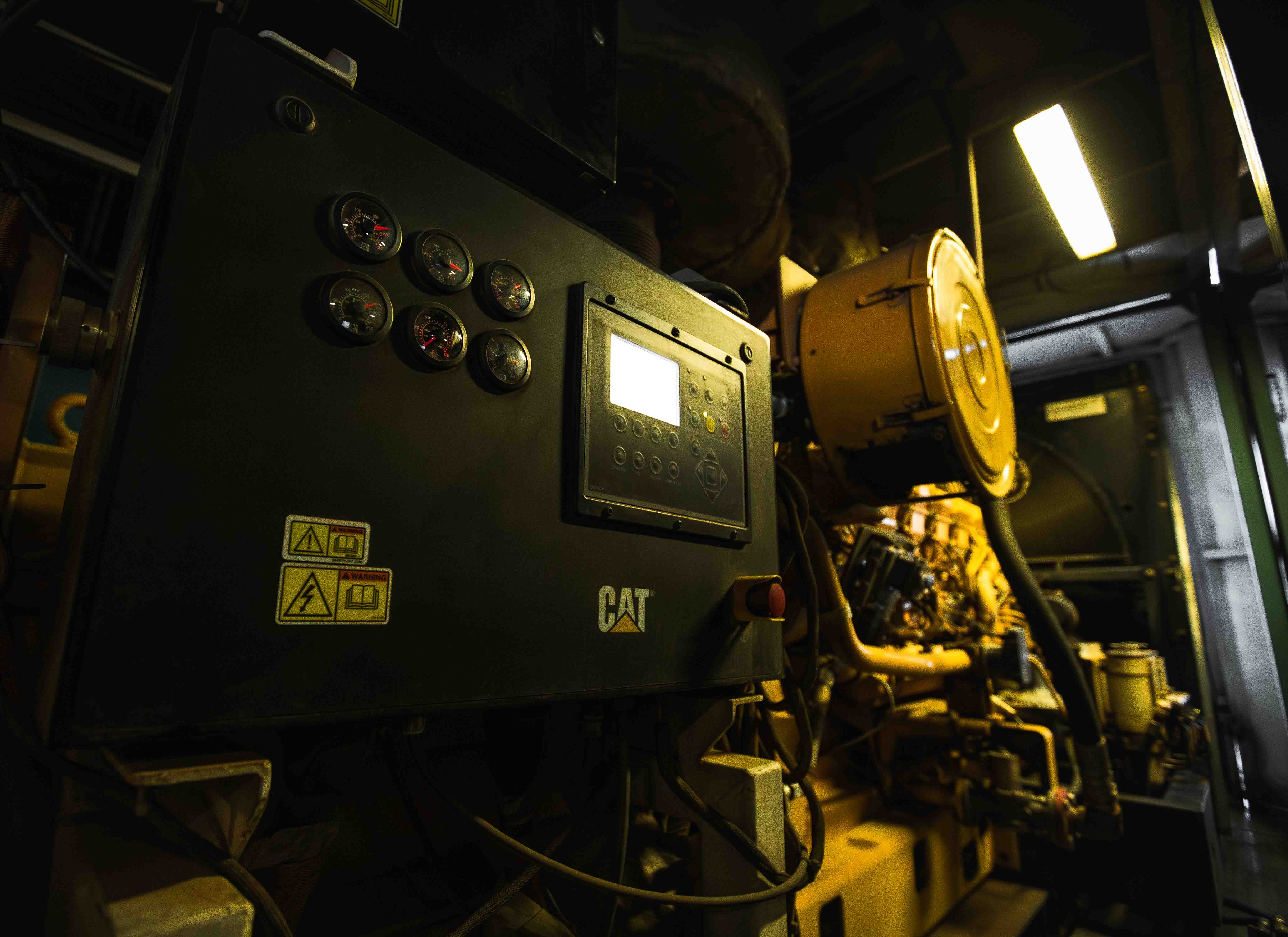
Shaving off costs
Companies using smart technologies usually see reduced maintenance expenses. Engines that run fewer hours use less fuel, as an example.
With optimized operations, the frequency of overhauls and repairs decreases, extending the life of field equipment. Operators using Smart EMS have reported reductions in engine runtime of up to 25% and fuel consumption decreases of 10%, Youssef said. Such improvements translate directly into cost savings, enhancing the bottom line while maintaining performance standards.
Caterpillar’s latest offerings, such as the Gen 2 Dynamic Gas Blending (DGB) system, are also geared toward resolving customer challenges, he said.
“The DGB Gen II is a game changer in diesel displacement, setting a new standard for what this technology can achieve. Operators now have the ability to upgrade their existing assets while maintaining peak performance and, as an added benefit, reducing emissions compared to traditional fumigated systems,” he said. “Customers utilizing the DGB Gen II have reported diesel displacement rates of up to 70%, making it a significant advancement in efficiency and sustainability.”
The blending system allows for natural gas as a fuel alongside diesel, fostering improved environmental sustainability while lowering fuel costs. Advancements including port injection and sophisticated software systems can help operators maximize efficiency in dual-fuel operations.
As the oil and gas industry embraces smart technology, operators are keeping a close on their wallets while using modernization to add efficiencies. Rather than investing heavily in new equipment, smart solutions allow companies to upgrade and optimize their existing assets. By extending the life of drilling equipment and minimizing the need for major repairs, operators can maintain competitiveness without sacrificing safety or performance.
The integration of smart technology on drilling rigs is not without challenges. However, the benefits—enhanced safety, reduced costs and improved efficiency—far outweigh the hurdles.
Recommended Reading
Diamondback in Talks to Build Permian NatGas Power for Data Centers
2025-02-26 - With ample gas production and surface acreage, Diamondback Energy is working to lure power producers and data center builders into the Permian Basin.
Pair of Large Quakes Rattle Texas Oil Patch, Putting Spotlight on Water Disposal
2025-02-19 - Two large earthquakes that hit the Permian Basin, the top U.S. oilfield, this week have rattled the Texas oil industry and put a fresh spotlight on the water disposal practices that can lead to increases in seismic activity, industry consultants said on Feb. 18.
AI-Shale Synergy: Experts Detail Transformational Ops Improvements
2025-01-17 - An abundance of data enables automation that saves time, cuts waste, speeds decision-making and sweetens the bottom line. Of course, there are challenges.
E&P Highlights: March 3, 2025
2025-03-03 - Here’s a roundup of the latest E&P headlines, from planned Kolibri wells in Oklahoma to a discovery in the Barents Sea.
PrePad Tosses Spreadsheets for Drilling Completions Simulation Models
2025-02-18 - Startup PrePad’s discrete-event simulation model condenses the dozens of variables in a drilling operation to optimize the economics of drilling and completions. Big names such as Devon Energy, Chevron Technology Ventures and Coterra Energy have taken notice.
Comments
Add new comment
This conversation is moderated according to Hart Energy community rules. Please read the rules before joining the discussion. If you’re experiencing any technical problems, please contact our customer care team.