Zipper fracs, simul-fracs, trimul-fracs and eFracs are all terms that reflect the increasing pressure for speed, efficiency and environmental responsibility in completion procedures. Finding ways to simplify and enhance operations continues to be a motivator for a number of companies, including Liberty Energy and NexTier Completion Solutions, which recently became part of Patterson-UTI.
For Liberty Energy, eFracs were a positive step, but the company realized that to deliver real energy and location efficiency, modifications would need to be made. Meanwhile, NexTier was focusing on improving pump monitoring to reduce costly downtime by predicting and preventing most failures before they happen.
Taking performance to the next level
Liberty Energy’s new digiPrime system drives frac pumps directly from an ultra-efficient, natural gas-powered engine which, in a recent field test, saved roughly $20 million in fuel costs per year per frac fleet. Moving to a natural-gas powered engine sounds like a simple solution, but making the transition required the company to overcome significant engineering challenges.
Pivoting from diesel and its associated cost and greenhouse gas (GHG) emissions to power frac pumps was one thing for Liberty’s president, Ron Gusek. But doing it with eFracs, which involve using natural gas to generate electricity, then turning that electricity back into mechanical power in electric frac pumps, while a good first step, still seemed roundabout and drill-pad-space greedy.
Connecting piston-based natural gas engines directly to frac pumps would boost efficiency by reducing the energy loss inherent in changing gas from one form to another. So, direct-drive would minimize fuel use and shrink the frac equipment’s drill site footprint by reducing power generation needs. Yet making the prime mover, an MTU 16V 4000 16-cylinder natural-gas engine, drive a pump directly instead of a generator required some creative engineering.
Unlike a vehicle engine, a standard well site generator drive motor has no throttle because a generator needs consistent speed to provide constant power levels. It is designed to run at 1,500 rpm or 1,800 rpm exclusively. Because of this, if the controller detects any load change, it could shut the engine down.
Directly driving a pump does involve shifting gears on the transmission as the pump’s load changes.
“That causes the engine a real challenge,” Gusek said. “When you change gears, you’re asking the engine to do more work, but the rpms aren’t allowed to drop. The (engine controlling) computer is not prepared for that change when it comes. It’s not delivering enough fuel to the engine, so the rpms would fall out of the acceptable range and the engine would stall or shut down.”
Smoothing out the load change was the key. “We effectively had to fool it into being prepared for more horsepower,” he said. This way, the controlling computer would deliver enough fuel and oxygen to accommodate the load change without shutting down the engine.
The Liberty solution, called digiPrime, takes advantage of the fact that the MTU 16V 4000’s drive shaft connects the pump at its back and includes a small generator under the cooling system at the front.
Some careful load coordination makes this work.
Controlling the generator’s load has the effect of managing the engine’s total load. About 20 seconds before shifting gears, the exact amount of the increase in horsepower is known to the system. At that point, Gusek explained, “We have the generator start to put incremental load on the engine. We can add an extra 200-300 horsepower of load requirement there. We can do that over 10 or 15 or 20 seconds so the engine is now very comfortably settled into this next step. Then we can shift gears, and at that very instant, we can turn off the generator. So, the engine sees a very gradual increase in load, and it settles in at this new place.”
Efficiencies extend throughout the process. According to Gusek, the engine itself is among the industry’s most fuel-thrifty, checking in at 44% heat efficiency—significantly more than a standard gasoline engine’s mid-30s level. Being direct drive, it also eliminates the energy loss inherent in going from mechanical to electrical and back again, which is the case with standard eFrac systems.
Smaller footprint
Older units were limited to 2,000 hp to 2,500 hp on a trailer, but this one reaches 3,000 hp, Gusek said. “It’s basically a two-for-one swap in term of the amount of horsepower we can get on a single trailer.” This reduces the amount of equipment space required on site.
Replacing older Tier 4 engines, which use 25% diesel and 75% natural gas, with an engine that uses 100% natural gas, might lead to the assumption that eliminating diesel would increase natural gas use. But Dusek reports that, due to its extremely high efficiency, the engine actually uses less natural gas.
Saving time and energy
The digiPrime units have only been in the field since early 2024, so there is no data yet on yearly energy cost savings. However, based on estimated figures using 2023 prices for diesel and natural gas, Gusek estimates that a fleet using 100% digiPrime could save around $20 million dollars versus the older mixed-fuel eFrac fleets.
Eliminating diesel should also extend run time between overhauls.
Gusek said diesels require overhauls about every 25,000 hours, and he estimates that the natural-gas-only unit could more than double that run time, creating further cost savings. Without performance data, however, “It’s way too early for us to tell,” he said.
Boosting runtime
Deep and continuous digital monitoring of a motor’s condition—engine rpm, engine temperature, oil temperature, transmission pressure—makes it possible to identify conditions that are likely to presage a failure. Armed with that knowledge, NexTier Completion Solutions’ team gets ahead of most issues, rightly timing preventive maintenance and creating a smooth path to orderly servicing and replacement.
The NexTier monitoring system, known as Insights, has significantly extended equipment run times and virtually eliminated failures, according to Director of Digital Operations Kevin Sutton.
The monitoring system consists of wireline, power solutions and other pieces of equipment. By comparing current pump conditions to its extensive historical database, the system boils down alerts to a red, amber and green (RAG) system. Sutton calls it “our biggest tool” in avoiding failures.
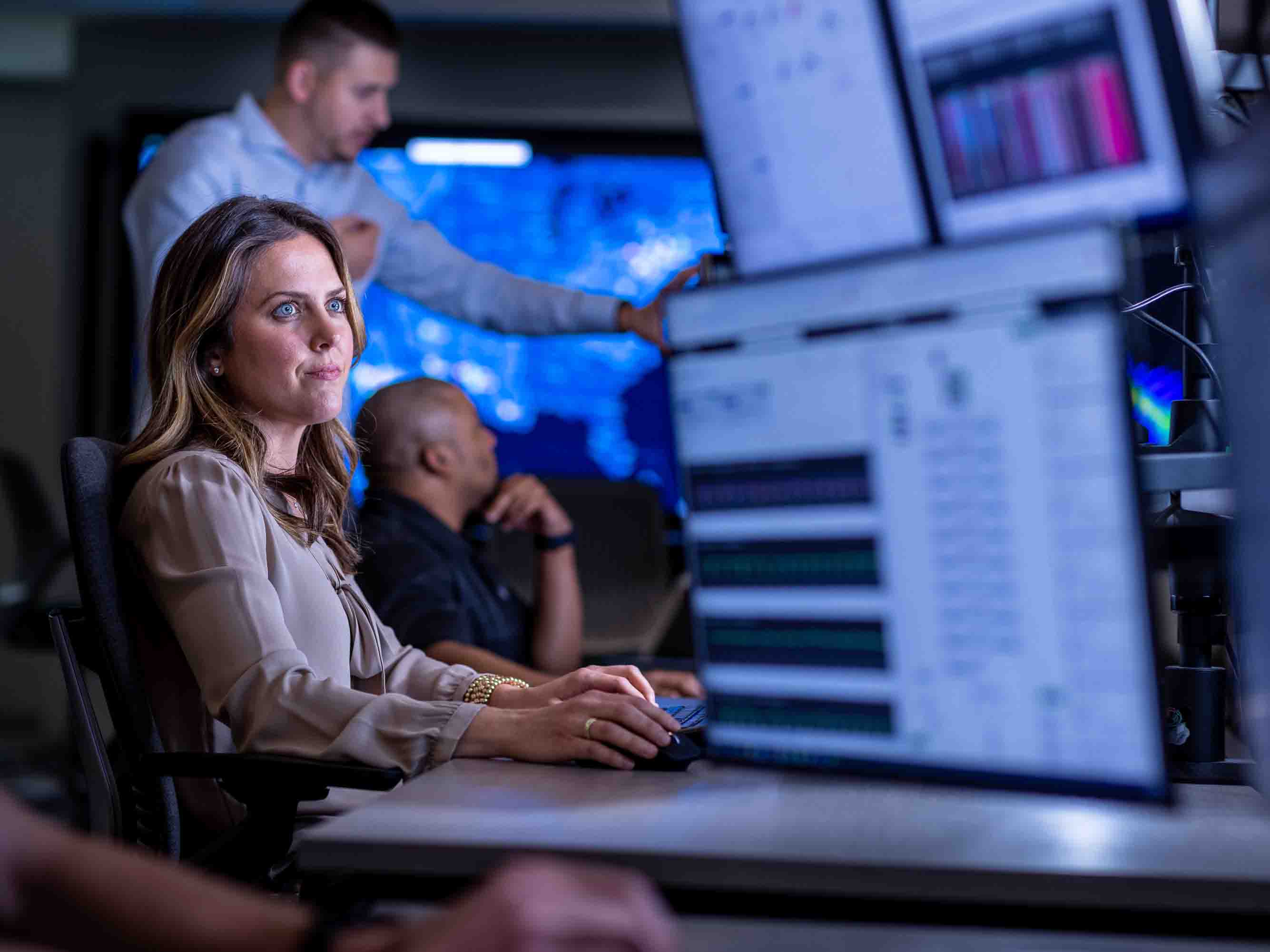
Green means all systems are go. A change to amber would occur, for example, if a normal operating level of 100 rpm to 150 rpm was slightly exceeded but not in a dangerous range. A rate of 150 rpm to 170 rpm is not ideal, Sutton said, “but is not going to be incredibly detrimental to the component. That’s what we call our amber area.” Should the level exceed 170 rpm, the alert moves to red. “That’s where we recognize that there’s going to be potential damage to the component if it continues,” he explained.
NexTier technicians oversee the tool 24/7 from a remote monitoring center. Depending on the issue, the repair team might remove a pump and replace a part or a fluid. Before the pump is returned to service, it is tested to make sure the performance issue was appropriately resolved. Pre-reinstallation verification assures that repairing one component did not create an unintended consequence elsewhere and that the original repair was performed correctly.
Repair testing also extends to larger jobs in which the pump is taken to the shop for major repairs or an overhaul. In-shop digital testing ensures the repairs were made, the pump was properly reassembled, and all is in good order before the pump goes back to the field.
It’s about (run) time
Continuous monitoring allows anomalies to be identified and addressed before performance or safety becomes an issue.
“If we want to pump, let’s say, for 1,000 hours, and we notice something look a little bit odd or different or not normal, we can say, ‘let’s pull that pump out, let’s do a couple of preventive maintenance steps on it,’ and only be offline for about an hour or so,” Sutton said.
Accumulated knowledge also informs proper preventive maintenance (PM) schedules, which Sutton said is “the truly ideal situation, keeping ahead of all maintenance before any failures occur.” Once PM intervals are set, they are continually compared to RAG alerts. If certain components are regularly failing, it may be time to update the schedule, he said.
This data also informs equipment design, allowing the company to identify areas that might need to be re-engineered for greater durability.
Continuous monitoring has already proven its value in the field, Sutton said. “With the development of this Insights program, we’ve seen a 110% increase in engine life cycles. Power end life cycles have gone up 125% and transmissions, which seem to be the toughest, have gone up 65%.”
Recommended Reading
Murphy Shares Drop on 4Q Miss, but ’25 Plans Show Promise
2025-02-02 - Murphy Oil’s fourth-quarter 2024 output missed analysts’ expectations, but analysts see upside with a robust Eagle Ford Shale drilling program and the international E&P’s discovery offshore Vietnam.
Chevron Targets Up to $8B in Free Cash Flow Growth Next Year, CEO Says
2025-01-08 - The No. 2 U.S. oil producer expects results to benefit from the start of new or expanded oil production projects in Kazakhstan, U.S. shale and the offshore U.S. Gulf of Mexico.
CPP Wants to Invest Another $12.5B into Oil, Gas
2025-03-26 - The Canada Pension Plan’s CPP Investments is looking for more oil and gas stories—in addition to renewable and other energies.
Talos Selects Longtime Shell Exec Paul Goodfellow as President, CEO
2025-02-03 - Shell veteran Paul Goodfellow’s selection as president, CEO and board member of Talos Energy comes after several months of tumult in the company’s C-suite.
Artificial Lift Firm Flowco’s Stock Surges 23% in First-Day Trading
2025-01-22 - Shares for artificial lift specialist Flowco Holdings spiked 23% in their first day of trading. Flowco CEO Joe Bob Edwards told Hart Energy that the durability of artificial lift and production optimization stands out in the OFS space.
Comments
Add new comment
This conversation is moderated according to Hart Energy community rules. Please read the rules before joining the discussion. If you’re experiencing any technical problems, please contact our customer care team.