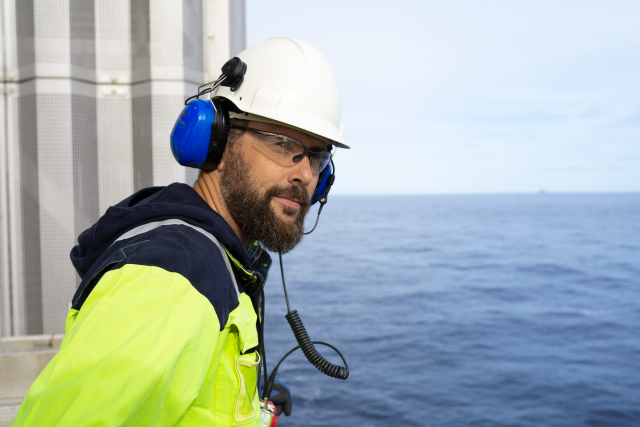
Aker BP has adopted technologies that allow its offshore workers to remain safe while still able to maintain the company’s operations. (Source: Aker BP)
[Editor's note: A version of this story appears in the July 2020 edition of E&P. Subscribe to the magazine here.]
COVID-19 has changed the way the industry operates, in many cases forcing workers from the field into their homes. For an industry that puts a premium on health and safety protocols, many companies have adopted remote working technologies that keep their workers out of harm’s way while also maintaining productivity.
As energy demand slowly picks back up, the oil and gas industry is getting back on its feet after being knocked down by price wars and the pandemic. But as wells get put back on production and rigs are brought back online, the need for workers to remain safe amid a spreading virus remains. Thanks to innovative approaches to remote working capabilities, the technologies exist for companies to chart a new, safe path forward.
Offshore platforms and onshore drilling pads are hotbeds of activity, oftentimes confining hundreds of workers into a small space, many working and living near one another. The very nature of upstream oil and gas operations is being threatened by the COVID-19 pandemic, putting at risk the rig personnel charged with drilling a well and bringing it online.
In April, the U.S. Coast Guard reported that 26 offshore workers in the Gulf of Mexico (GoM) had tested positive for the novel coronavirus. Following that report, the Coast Guard ceased reporting new cases on offshore platforms in the Gulf. Also in April, 74 workers offshore Brazil were confirmed to have the virus. BP, Chevron and Shell are among the companies that have confirmed some of their offshore workers have tested positive for COVID-19.
The outbreak comes at a time when the industry was already working with reduced staffing levels and prioritizing efficiencies amid limited access to capital. The one-two punch of the coronavirus outbreak, which crushed global oil demand, and the price war between Russia and OPEC+ forced operators to, in some cases, completely halt production and lay off thousands of workers as oil prices plummeted to negative valuation.
As oil demand begins to build once again and as operators begin to bring shut-in wells back online and start to initiate new drilling activity, producers and service providers alike are finding ways to keep their workers safe while ensuring efficient operations.
“The COVID-19 pandemic has completely changed the nature of our industry, in addition to disrupting global supply chains and personnel logistics,”said Melisa Ramirez Tovar, Performance Live service manager for drilling and measurements operations with Schlumberger. “With the onset of worldwide travel bans, quarantine requirements and shelter-in-place orders, the normal way of operations became impossible, in particular for staffing well sites with crew and engineers.”

As much of the world has been forced to adopt new technologies in a remote working environment, so too has upstream oil and gas. Operators and service providers are equipping their workers with devices and tools that allow them to work safely from remote locations and have put into practice testing and social distancing measures at their locations in hopes of slowing the spread of COVID-19.
“What we have realized is that [companies] have doubled down on their digital operations,” said Francois Laborie, president of Cognite North America, an international industrial software provider. “They have recognized that the only way to come out a winner out of it is to master these types of solutions. And that was not a given when we started, because these are future programs, and maybe that’s not something that wouldn’t be top of mind, but it has been top of mind. Enabling remote operations can come from the couch, enabling different business models, enabling automation, enabling the use of drones or robots on the platform—all of that places very nicely within the context that we are facing right now, which is both COVID-19 and a need for better efficiency in operations.”
New role of remote operating technologies
In an analysis of industry technology trends issued in May, Rystad Energy noted that in recent earnings calls, companies offered a glimpse into how digital technologies emerged at the start of the downturn.
“Despite recent market events that have forced operators and suppliers to turn their focus toward cash conservation, development on this digital revolution still seems to be relatively robust,” Rystad reported.
Both Schlumberger and Halliburton stated in their first-quarter 2020 earnings calls that the current downturn could accelerate the adoption of digital technologies, especially those that enable remote operations.
“Despite being positive news for suppliers offering digital technologies, spending by operators may have been accelerated as a result of COVID-19 instead of actual business needs,” said Daniel Holmedal, energy service analyst with Rystad Energy. “Growth seems to have mostly centered on remote work, while technologies focusing on optimization of drilling and production seem to have hit some speed bumps.”
As Acoustic Data COO Matthew Norgate explained, volatile oil prices have brought an increased focus on reducing costs, which has helped bring the use of remote and digital technologies to the forefront of companies’ operations. However, Norgate said a primary driver more recently behind the push for these technologies has been the inability to deploy temporary personnel to operations locations, where lockdown and quarantine restrictions have made travel, and therefore many field operations, difficult.
“Against this backdrop, we have had to accelerate our development of our remote operations model, utilizing standard packages such as YouTube, WhatsApp and TeamViewer to deliver training and assessment, as well as our own bespoke packages to remotely configure and control our systems for deployment downhole,” he said.
Click here for an E&P exclusive video.
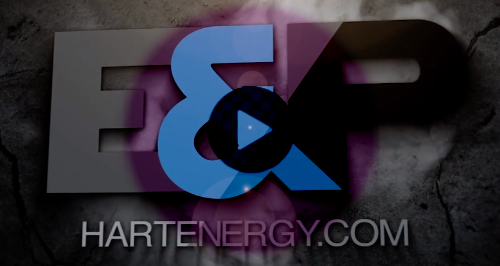
David Seabrook, digital strategy manager with Schlumberger, said over the past three months the company has seen a significant increase in its customers’ need for wellsite remote operations.
“However, it has not only been in wellsite remote operations that we have seen these increases,” he said. “Many of our customers are now using our digital inspection capabilities, which enable them to monitor the testing and take delivery of equipment from our manufacturing centers without being physically present. This inclusion of remote inspection capabilities started to gain momentum over the past two years, and recent events have accelerated this transition resulting in a 15% increase in internal efficiency during execution.”
He added that Schlumberger has seen an increase in the use of its cloud-based DELFI cognitive E&P environment from home.
“For example, one of our enterprise customers accelerated their DELFI environment deployment specifically to address the urgent need of their geoscientists to work from home,” Seabrook said.
In the midst of Europe’s recent shelter-in-place regulations, Norwegian offshore E&P company Aker BP worked with Cognite as project engineers for Aker BP’s pumps supplier Framo Services AS. Framo technicians have been able to monitor the condition of the seawater lift pumps from home using Cognite’s software, live data stream, machine learning and algorithms.
Although recent developments have accelerated the application of such technologies, they are likely here to stay, according to Kjetel Digre, head of operations and asset development with Aker BP. “Because we are all sitting in this awkward situation at home, that creates some special challenges for us,” Digre said. “But in a subtle way this is accelerating the acceptance of new solutions and new ways of working, and also the interest. I think we are really now mobilizing the whole organization to think differently and seek new types of solutions where we don’t have to move ourselves.”
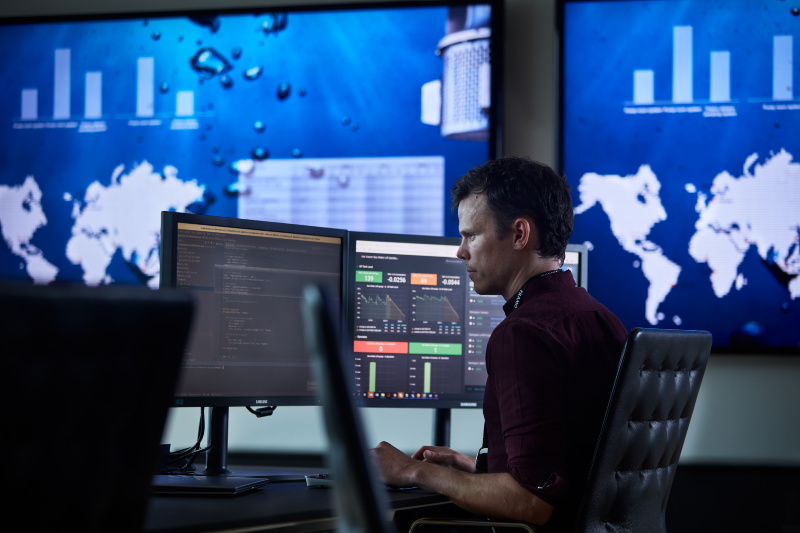
Trond Petter Abrahamsen, managing director with Framo, said adopting the ability to monitor the condition of its pumps from home while travel is restricted saves on costs and provides environmental benefits.
“Going forward, algorithms and sensor data help us increase uptime, reduce unplanned maintenance and be better prepared for necessary overhaul on the seawater lift pumps,” he said. “The need to visit the platforms to inspect the condition of the pumps is therefore reduced.”
Although it likely has not been a priority in recent months, matters of sustainability and environmental stewardship have begun to play an increasingly key role in upstream operations. Pricing challenges and demand destruction have pushed those concerns to the fringes, but as the industry restarts, the technologies that are now emerging and enabling remote operations could play a key role in environmental, social and governance compliance efforts.
“People don’t focus on it right this minute, but that focus on sustainability was already coming into sharp relief for the sector,” said Jeff Williams, global oil and gas advisory leader with EY. “You combine that with the rise of automation and digitalization and remote work, and I really feel like we have not just the opportunity, but the need to potentially reshape how our industry operates for years to come.”
Technology applications
Even prior to the COVID-19 outbreak that forced field workers into their homes and the implementation of new safety practices that limit exposure to the virus, service providers and operators alike were adopting digital and autonomous technologies that led to greater efficiencies and reduced costs. And while some considered such technologies as nice to have, in many cases they are now must-haves to keep operations up and running.
During the onset of the COVID-19 pandemic, many companies recognized that remote operations would serve as a sustainable operating model to provide business continuity amid global travel restrictions. Tovar said Schlumberger was able to conduct the transition seamlessly due to the maturity of its Performance Live service.
Guandong Jiao, Schlumberger’s Performance Live service manager for wireline operations, cited a number of cases in which advanced operations were carried out by a limited number of wellsite crews performing jobs from their homes or offices. Among those were reservoir evaluation in deepwater Brazil, a directional drilling operation in deepwater GoM, an LWD operation in the Middle East, mechanical intervention operations offshore the U.K. and a complex directional drilling operation onshore in North America.
“Within a two-month period, our drilling and measurements and wireline business expanded the worldwide use of Performance Live service, and by May our Performance Live service was being utilized for approximately 60% of global drilling operations,” Tovar said. “From March to May, our Performance Live engineers covered more than 30,000 shifts—for our drilling and measurements activity—and 2,600 wireline runs, which enabled us to avoid sending more than 600 employees to various well sites.”
Acoustic Data, which specializes in wireless well technology, developed a remote deployment model for its SonicGauge Wireless Monitoring System to overcome travel restrictions relating to COVID-19, according to the company. The tool enables operators to self-install their real-time wireless downhole monitoring system without requiring specialist engineers on site.
“Our operating model enables us to deploy a SonicGauge system for a standard installation without the need for our personnel to leave our U.K.-based technology center,” Norgate said. “This approach allows us to control the environment in which they are working, follow governmental guidelines and also ensure that our customers do not have the concern of accommodating new personnel within locations where social distancing would be problematic.”
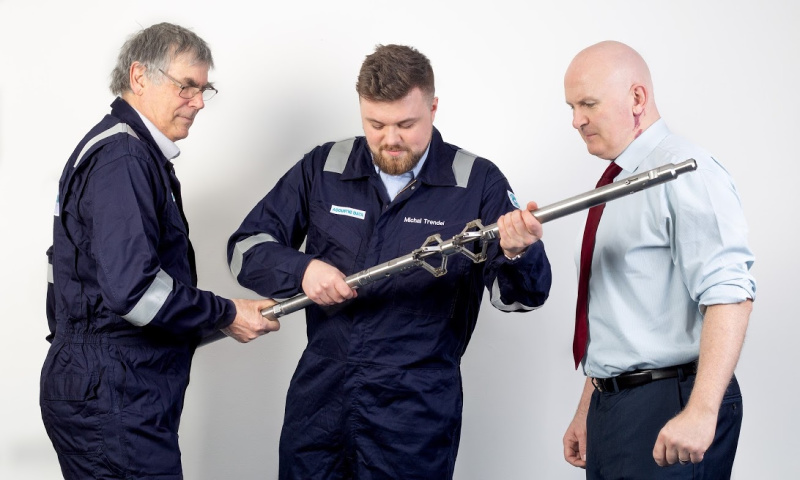
Meanwhile, Wood has adopted Honeywell’s workforce productivity suite, which includes intelligent wearables and video assistant capabilities, among others. Honeywell reports that the technology’s impact ranges from accelerated issue resolution to reduced shutdown time and decreased exposure to hazardous environments.
“There are many new challenges with operating industrial facilities during today’s difficult times, considering local distancing requirements, HSE protocols and instances where the facility might require a temporary quarantine,” said Honeywell Process Solutions CTO Jason Urso. “Early on, the Honeywell Process Solutions team explored methods to extend our technology to help our customers maintain business continuity. We initially focused on remote operations to assist with sites that were required to reduce staffing. By extending the capability of Honeywell technology, we quickly demonstrated that our Experion control system could enable remote operations in a completely secure way. This capability opened the door for customers to operate with lower staffing on site and augment that staffing with remote support using the Experion Remote Operations software.”
According to Honeywell, the technology has been deployed on offshore rigs in the U.K. North Sea, the GoM and on Alaska’s North Slope as well as at onshore processing facilities in the U.K., U.S., Canada and the Middle East.
Digre explained that for Aker BP to maintain its normal operations through the COVID-19 crisis, it was challenged to find new solutions for remote work.
“Part of the Cognite collaboration has been to equip all of our workers offshore with digital handheld units, and they are using them now to collaborate with contractors, for instance, sitting in Norway or Sweden to be involved and perform their tasks like inspections or modifications remotely,” he said.
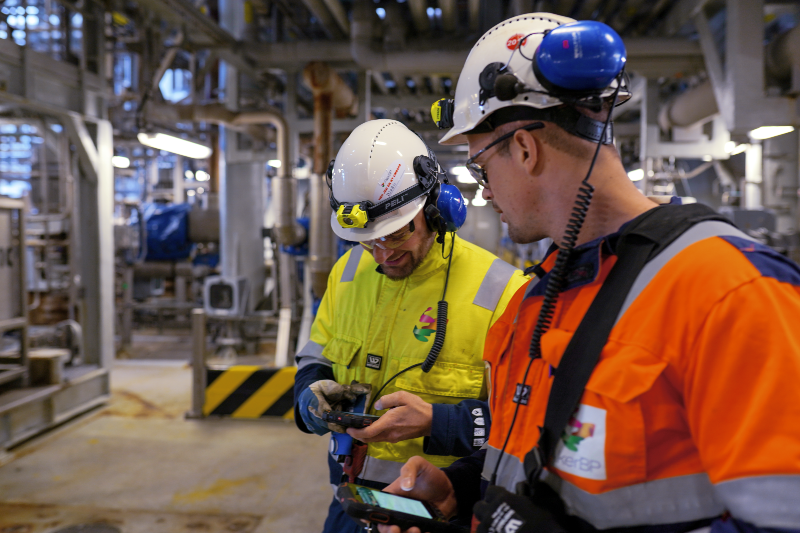
Prioritizing digital
While the COVID-19 pandemic has forced people apart from one another, in many ways the technologies that oil and gas companies are adopting in the wake of the outbreak are serving as a uniting force. Those technologies also are upskilling the industry’s workforce while accelerating a digital transformation that many companies might have been hesitant to adopt.
“Even when clients are talking about operating model changes, needing to get leaner and having potentially smaller workforces, the need for digital continues to be an investment priority,” EY’s Williams said. “We truly believe digitalization is going to accelerate through this downturn, through the recovery, post-COVID and post-price shocks.”
Acoustic Data’s Norgate explained that COVID-19 has driven a change in the way the company executes its field operations, which he said will likely become “the new normal” for the company’s tool deployments around the world.
“Our approach to training and supporting our customers has enabled us to onboard new personnel more quickly, which ensures that we can keep their skills up to date, even if having to isolate at home,” he said. “But most importantly, it has provided a new dimension to the role of our field team through increased customer contact across the operational cycle, providing benefits in both directions.”
Norgate explained that he has noticed many of Acoustic Data’s customers adopting a more collaborative approach to operational execution in the face of the challenges that service companies are facing as it relates to the movement of personnel around the world.
Framo recently signed a long-term contract with Aker BP for offshore pump maintenance, where compensation is determined by the systems’ reliability and performance. Abrahamsen explained that the contract represents “a huge step within digitalization and predictive maintenance,” with digital boards having been developed based on sensor data from Cognite’s Data Fusion system and algorithms from Framo.
“The last months have been a reminder of the possibilities working together in new ways and sharing information that normally has been kept within our client organization,” Abrahamsen said. “By sharing the information through the Cognite platform, we have been able to maintain service level, while at the same time keeping employees safe.”
Digre explained that although Aker BP has worked diligently to adopt and develop digital technologies, automation and remote working capabilities, the current environment and Aker’s internal progressive culture are helping to ensure the company emerges from the crisis in a stronger position.
“We are learning as an organization [and] working differently together, and that is a direct effect of creating new opportunities on how we execute our daily work,” Digre said. “That is not insignificant when you look at the number of people we have. We believe that going through this is not about stopping everything that we have going. It’s really to strengthen our change and improvement programs and doing it even faster. We believe that is the answer to facing this crisis.”
Industry turning point
Although new realities created a challenging new work environment for many companies, the implementation of new technologies could serve longer-term successes. Producers and service providers are finding that they can run their operations efficiently with fewer people by
incorporating existing technologies like remote access, digital twins, and virtual and augmented reality.
“These technologies have been viewed as a nice-to-have option for many manufacturing applications but not necessarily a need—until now,” Urso said. “Remote access, especially, has become much more meaningful in the past few months.”
As Schlumberger’s Seabrook explained, to deliver more efficient and safer operations to the well site with a reduced footprint, companies need to rely on autonomous technologies in the field along with domain and operational expertise in remote operations centers.
“Using automation to eliminate tasks that are repetitive or dangerous enables us to better utilize our people—both in the field and at the remote operations center,” Seabrook said.

As is the case in other aspects of life, some of the changes forced upon the industry during the COVID-19 era are likely to remain permanent. For an industry that has placed HSE protocols as its top priority, new technologies that keep workers safe will continue to emerge, and companies will find new ways to strike the right balance between efficiencies, productivity and profitability.
“We see this as a pivotal time in our industry, and we anticipate remote operations to define a significant part of oil and gas operations going into the future,” Jiao said. “The benefits, both in cost and performance, of this new way of operating means that there is no going back after the pandemic has passed. Therefore, we are focused on accelerating the delivery of technology that supports remote operations.”
SIDEBAR:
Implementing remote operations
It could be conceived as a daunting task to employ technologies such as remote work operations for companies that have yet to begin their digital journey, either through reluctance or lack of means.
Many analysts perceive the adoption of such technologies within the upstream oil and gas industry as an adopt-or-die proposition, putting further pressures on companies searching for ways to survive the multitude of compounding dynamics in today’s industry.
Honeywell CTO Jason Urso offers some guidelines for companies looking to grow their digital platforms and remote operating abilities for their employees.
“It is fundamental to ensure that companies are complying with all local regulations,” he said. “Next, industrial corporations are familiar with detailed risk assessments associated with safety-critical processes. Apply those same risk assessment methods to evaluate the operational risk associated with the crisis. Finally, build a plan to mitigate the most critical risks associated with safety and business continuity. As part of the mitigation steps, look for ways that technology can most effectively address a risk.”
Urso also emphasized remote operations, service and support, and project execution:
- Remote operations: Ensure a remote operations capability is in place in the event rapid de-staffing is required at a site. Deploy and test the capability in advance of needing it. With the technology in place, explore how it can be used for improved efficiency and collaboration.
- Remote service and support: Augment existing staffing with support from suppliers to remotely monitor equipment, moving from more reactive to proactive support. By identifying issues proactively, it allows better resource planning to address issues before they become critical.
- Remote projects execution: Use remote methods to execute projects. Leverage the power of cloud technology and digital twins to carry out project execution without requiring individuals to gather at the site and work directly on the physical equipment.
Recommended Reading
Permanent Magnets Emerge as a Game-Changer for ESP Technology
2024-12-19 - In 2024, permanent magnet motors installations have ballooned to 11% of electric submersible pump installations, and that number is growing.
Novel EOR Process Could Save Shale from a Dry Future
2024-12-17 - Shale Ingenuity’s SuperEOR, which has been field tested with positive results, looks to remedy the problem of production declines.
Small Steps: The Continuous Journey of Drilling Automation
2024-12-26 - Incremental improvements in drilling technology lead to significant advancements.
AI-Shale Synergy: Experts Detail Transformational Ops Improvements
2025-01-17 - An abundance of data enables automation that saves time, cuts waste, speeds decision-making and sweetens the bottom line. Of course, there are challenges.
Microseismic Tech Breaks New Ground in CO2 Storage
2025-01-02 - Microseismic technology has proved its value in unconventional wells, and new applications could enable monitoring of sequestered CO2 and facilitate geothermal energy extraction.
Comments
Add new comment
This conversation is moderated according to Hart Energy community rules. Please read the rules before joining the discussion. If you’re experiencing any technical problems, please contact our customer care team.