What’s next in shale technology is just what you might expect: an abundance of data and analytics and AI’s transformative impact on E&P operations.
“There’s a huge buzz about AI as we all know, it’s seen as a trillion-dollar industry,” said Sushma Bhan, non-executive director at Ikon Science, and technical director for data science and engineering analytics at SPE, at Hart Energy’s DUG Executive Oil Conference in November. “There’s a lot of anticipation about the results.”
It’s not just a matter of turning everything over to the machines, Bhan said. It’s about people and machines working together.
“It’s all about automation,” she said. “How we can automate and augment human results, the skills SMEs bring, bringing that together with the automation, so things or actions that can be done in hours or days can be done in minutes.”
Ikon specializes in subsurface applications, rock physics and reservoir characterization.
“If you look at how we take subsurface data and use it in our end-to-end exploration to production, we’re talking about thousands of subsurface data types,” she said. “And the ability to access that data with automation is talking about tremendous saving of time and effort.”
A quick example:
“Let’s say we’re looking at the equipment used previously in a certain area,” she said. “You can quickly access that information and deploy solutions rather than reinventing and searching and spending time. Your time savings can be almost 10x if you’re doing that kind of process.”
AI also offers the power of visualization, Bhan said.
“We have tools where you can quickly bring your predrill data, your pressure data, and integrate it with the real-time in-stream data. We used to create PowerPoints and bring information, and it would take weeks and months. With AI, the efforts have just expedited.
“It’s about saving time, eliminating waste, expediting your decision-making, and the bottom-line impact.”
Push button frac
Halliburton is seeing quick adoption of AI both internally and externally, said Steven Jolley, the Permian Basin technology manager.
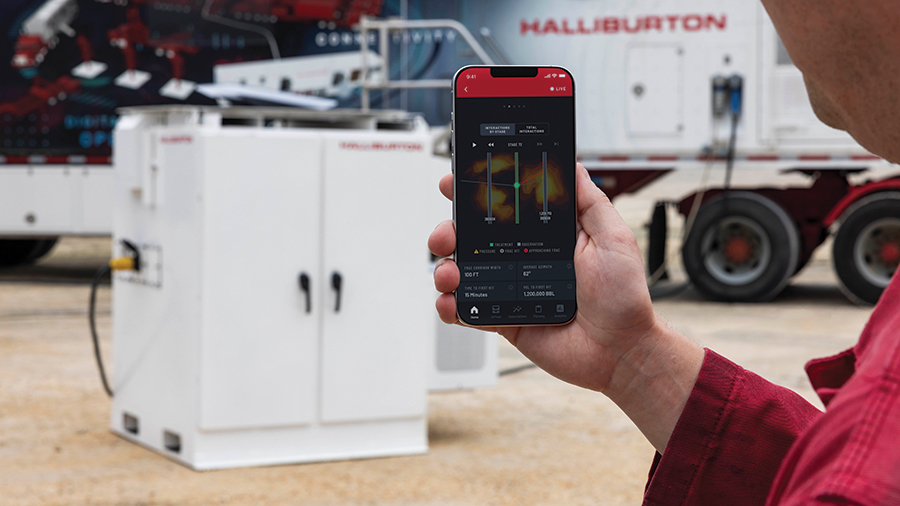
“Most of the ones that we run with today are utilizing AI in some form or fashion,” he said. “They’re looking at reservoir drilling and completion variables to see which type of variables really drive uptake in production.”
The company is also using it regularly.
“In the past six months is where we really started to drive the AI piece for our business,” he said. “We rolled out Auto Frac and Sensori within our business here in the Permian Basin about six months ago.”
The company says Auto Frac is the first automation service that enables customers to execute their fracture design without human intervention.
“Auto Frac is, in simple terms, push button frac,” Jolley said. “You can come in, push a button and let it pump the design as intended without any human intervention. Customers are able to access that from an app-based platform and make changes based on what they see, as well. That’s been huge.”
Sensori is a fracture monitoring service that lets operators evaluate well performance. It’s also app-based.
Data from Sensori and elsewhere have led to changes in the field. Operators have been upsizing their spacing to take advantage of their fracture complexity, Jolley said.
In December, SLB introduced an autonomous drilling system called Neuro, sort of a Waymo for drillers. The company deployed Neuro to drill a lateral in Ecuador.
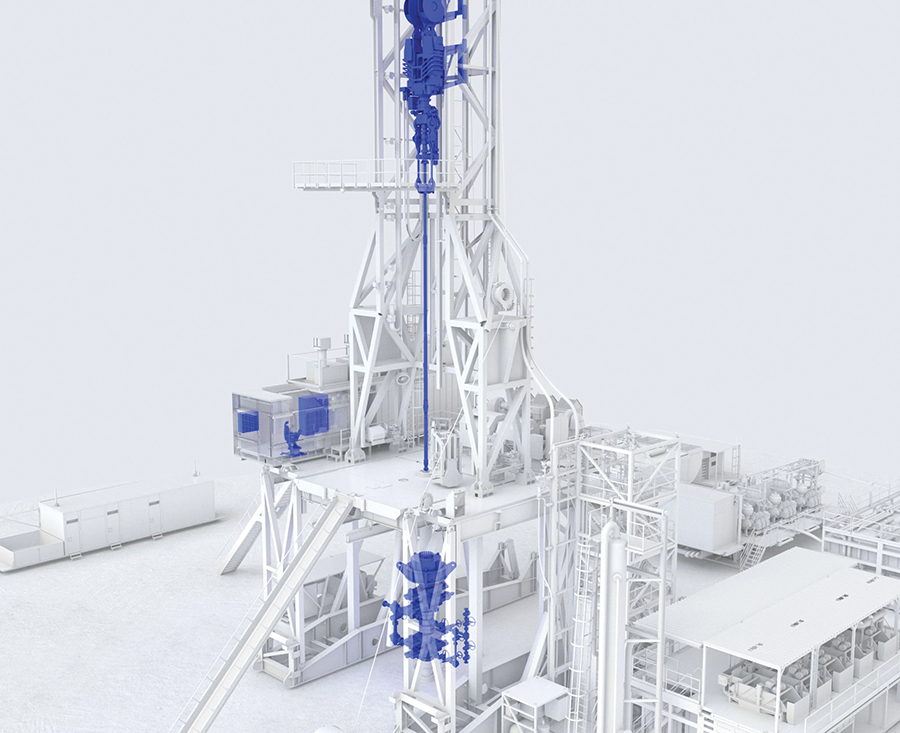
“The system automatically selects the best route for drilling the well based on high-fidelity downhole measurements, bringing the well trajectory in line with the real-world conditions of the reservoir,” said Jesus Lamas, SLB president of well construction.
Jeff Beach, vice president of reservoir performance at NexTier, said at the conference that his company is using fiber-optic technology with a customer “to find that balance of how much sand we’re going to put in place versus that spacing, so you can have a wider spacing and put more sand per stage, or closer spacing and reduce that amount of sand.”
“There’s a balance point for each particular operator in that respective basin,” he said. “Leveraging the fiber-optic technology and then the offset well monitoring is certainly a way to maximize that.”
Other companies are finding value in data as well. Ricky Kostner, Permian Basin regional manager for ChampionX, said it’s making the team smarter.
“We’re running all of our analytical data that we’re capturing after completion or after a drilling event or just during production in general, feeding that back through the machine learning models,” Kostner said. “It’s expediting decision-making, it’s allowing our customers to expedite decision-making. It’s a huge competitive advantage that we’re seeing.”
Kostner also noted the changes in well spacing.
“With increased density and smaller spacing, we definitely see increased activity of frac hit,” he said, when fracking in a new well affects an existing well. That “affects us chemically, it affects the whole operation all the way to the pipeline and the produced fluids that are coming back up.
“We’ve got frac protect programs that we put in place with our customers to help offset the impact of these events,” he said. “We see larger spacing largely being a benefit to try to find that optimal place where you’re not going to get the frac hit events and the communication between wells.”
M&A’s impact
The wave of consolidation in the Permian is also increasing efficiencies as operators create larger continuous lease holds.
“The continuous acreage makes things much more efficient,” Jolley said. “You see more of a manufacturing environment there. Anywhere where you have a lot of activity in one place and you can be a part of that development, you’re going to learn a lot more about the reservoir, the completion design, all of those things.”
The advantages of scale are far-reaching, Beach said. “It enables you to bring in techniques, simul-frac or trimal-frac or what we may refer to as remote simul-frac, where you can have the horsepower on one location and through pipeline completing wells on an adjacent pack.”
Under the surface, lateral length may be nearing a peak at about 4 miles, at least until innovation allows further extension.
“Four miles, that’s a long way,” Jolley said. “We continue to push the limits, innovate with technology. Going beyond 4 miles, you’re taking on quite a bit of risk. You’ve got to push the drill pipe that far, the casing connections have got to last through the torque and force to get to that length as well. So, there’s definitely some complexities to get around.”
ChampionX’s Kostner said the longer laterals bring in more variables.
“I think about the change in pressures and temperatures and some of the molecular things that are going to happen with that fluid on the way up,” he said. “Knowing that in the design package before we go take on the capital and get the equipment going is going to be essential.”
“We see operators that deal with some of the mistakes that were made early on,” he said. “I just think extending the lateral length is going to exacerbate those issues whether it’s from a lift perspective or a chemical perspective.”
One more item on the shale development list is water management, a part of the industry that has evolved from tanker trucks operated by mom-and-pop businesses to dedicated pipeline infrastructure built by companies like Aris Water Solutions and Deep Blue.
“This basin is producing just a tremendous amount of water and it’s got to go somewhere,” Aris CEO Amanda Brock said at the conference. “If you don’t have a place for the water to go, it impacts production.”
As the cost of disposing produced water increases, the demand for more innovations increases as well. Concerns that injection wells are causing more seismic activity are adding to the scope of the problem.
Some of the answers are recycling, beneficial reuse and extraction of useful minerals like lithium—not one solution but many.
“Everybody in our space is trying to figure it out,” said Robert Norton, chief commercial officer for the water management company Deep Blue.
Recommended Reading
Chevron Buys 15.4MM Shares of Hess Stock on Open Market
2025-03-17 - Chevron Corp. reported that between January and March 2025 it purchased about 5% of Hess Corp. shares, according to a Securities and Exchange Commission filing.
TG Natural Resources Wins Chevron’s Haynesville Assets for $525MM
2025-04-01 - Marketed by Chevron Corp. for more than a year, the 71,000-contiguous-net-undeveloped-acreage sold to TG Natural Resources is valued by the supermajor at $1.2 billion at current Henry Hub futures.
Abu Dhabi’s Mubadala Buys Stake in Kimmeridge Shale Gas, LNG Ventures
2025-04-10 - Mubadala Energy, owned by Abu Dhabi’s sovereign wealth fund, is buying a stake in Kimmeridge Texas Gas (KTG) and Commonwealth LNG as the United Arab Emirates company makes an entry into U.S. shale.
Oxy, Looking to Cut Debt, Sells D-J Minerals to Elk for $905MM
2025-03-23 - Elk Range Royalties bought 250,000 net royalty acres in the Denver-Julesburg Basin for $905 million from Occidental Petroleum, which is looking to shed debt after last year's acquisition of CrownRock.
Will TG Natural Resources Be the Next Haynesville M&A Buyer?
2025-03-23 - TG Natural Resources, majority owned by Tokyo Gas, is looking to add Haynesville locations as inventory grows scarce, CEO Craig Jarchow said.
Comments
Add new comment
This conversation is moderated according to Hart Energy community rules. Please read the rules before joining the discussion. If you’re experiencing any technical problems, please contact our customer care team.