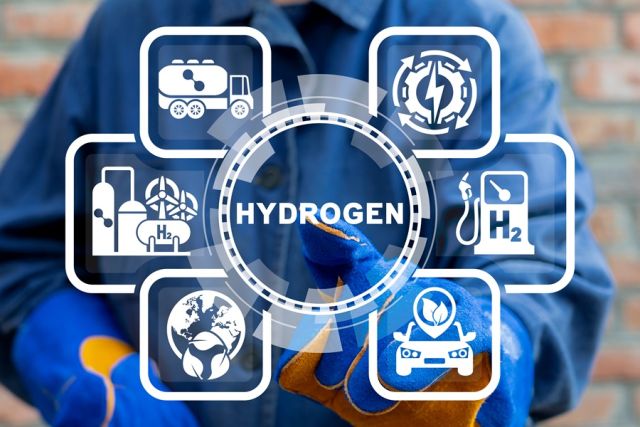
Wisconsin-based Advanced Ionics, backed by BP and Repsol, has developed a new class of electrolyzer that uses process or waste heat already present at industrial facilities to help lower costs and electricity needs. (Source: Shutterstock.com)
A BP- and Repsol-backed startup is advancing technology that aims to lower the cost and amount of electricity needed to split water molecules to produce hydrogen.
Advanced Ionics is nearing the end of two pilot projects—one with Repsol and another with the U.S. Department of Energy’s (DOE) Advanced Research Projects Agency-Energy (ARPA-E) to bring its electrolyzer technology closer to gigawatt-scale production.
To boost its competitiveness with other forms of energy, including fossil fuels, efforts are underway to lower costs associated with producing electrolytic hydrogen. The steps are being taken amid ongoing moves to lower greenhouse gas emissions. Hydrogen is considered an attainable solution given its high energy density, versatility and lack of CO2 emissions.
Hydrogen is produced via various techniques and feedstocks that include water electrolysis using electricity from renewables and steam methane reforming or autothermal reforming with natural gas. Each form comes with a different carbon intensity and price tag.
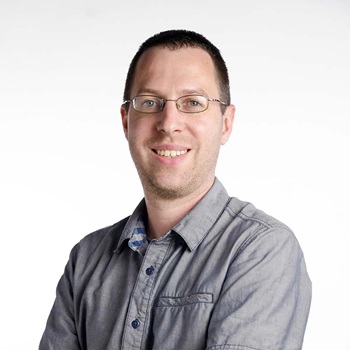
“The things we have under our control are the ability to use cheap electricity to make hydrogen or use less electricity, and what we do at Advanced Ionics is we enable people to use less electricity,” Advanced Ionics CEO Chad Mason told Hart Energy.
Wisconsin-based Advanced Ionics has developed a new class of electrolyzers that uses process or waste heat already present at industrial facilities to help bring down costs. The water vapor electrolyzer, called Symbion, is made using materials and steel that are widely available.
“We designed an electrolyzer that can be integrated into industrial processes, into a refinery, much in the same way you currently take methane, do steam methane reforming on site, make the hydrogen, feed it to the processes that need it,” Mason said. “We’re basically going to be doing the same thing with electrolysis in a very effective manner. … It’s important to do this with abundant materials, easy to build systems, easy to integrate balance of plant.”
Symbion electrolyzers use process or waste heat with temperatures from 100 C and higher, which helps reduce electricity costs.
The electrolyzers can be scaled and use off-the-shelf components such as stainless steel and nickel instead of expensive catalysts like platinum or iridium.
Targeting lower costs
Electrolysis, the process of splitting water into hydrogen and oxygen with electricity from renewable and nuclear resources, can be carried out with a variety of electrolyzers. Each type has different operating requirements. Some electrolyzers require large amounts of electricity, ceramics or catalysts.
Today, thermal conversion of fossil fuels—mainly by steam methane reforming—is the dominant lowest cost method of hydrogen production; but the method emits about 10 kg of CO2 equivalents per kg of hydrogen produced on a lifecycle basis, according to the DOE. While hydrogen from clean and renewable energy sources emit less, costs can be more than $5 per kg.
The U.S. aims to reduce the cost of clean hydrogen by 80% to $1 per kg by 2031.
“Electricity use accounts for more than 70% of green hydrogen production costs,” according to BP. “Advanced Ionics’ electrolyzer stack requires less than 35 [kilowatt-hour] kWh per kilogram of produced hydrogen compared to more than 50 kWh per kilogram for typical electrolyzers. This lower electricity requirement could make green hydrogen accessible for less than $1 per kilogram at scale.”
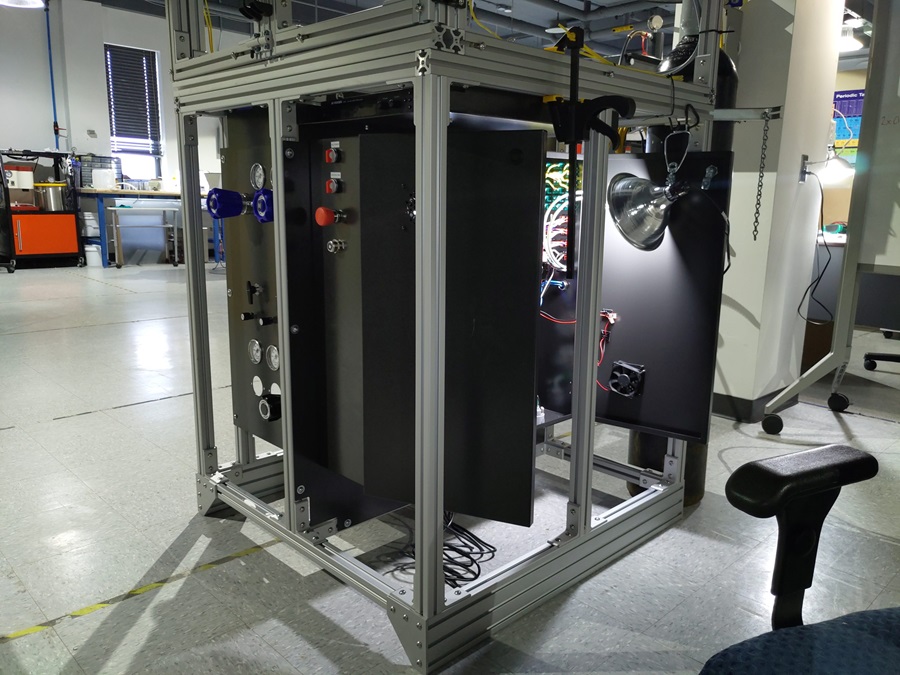
Whether the electrolyzer technology helps make electrolytic hydrogen cost-competitive with other forms of hydrogen—including blue hydrogen—depends on a variety of factors. Geography is one.
“I always tell people pick your location and then I’ll pick the numbers for you. It gets down to what’s that price of that electricity from the renewables that you have,” Mason said. “If you’re in Texas and you do a combined wind and solar project, you can have quite low-cost electricity, which will get you below $2 per kilogram hydrogen wholesale that gets fed into the unit. You can even do the math and find a path towards below a dollar per kilogram. But it is challenging. You need a variety of circumstances to line up in the right way.”
Blue hydrogen also must check a lot of boxes to be cost-effective and decarbonized, he added, noting needed proximity to CO2 storage.
“I think blue hydrogen’s generally been quite overhyped for what it can do,” he said. “I think the proof is in the pudding, but time will tell.”
Next steps
The company plans to announce another project with a large oil and gas major soon, Mason said.
“We’re going to be progressively stepping up in size. So, going from a single small stack to progressively larger stack and then stacks,” Mason said. “These will be done in demonstration and pilot scale systems. … Eventually, we will be commercializing these in the second half of the decade.”
The Repsol project allowed the company to show it could deliver the first stack, or a collection of stacked electrolytic cells connected that make up the core of an electrolyzer. The ARPA-E project allowed the company to progress up in electrolyzer size to prove ability, reliability and performance, Mason said. “Then, we’ll march onward from there.”
Mason’s approach has been shaped in by part his childhood growing up on the family farm in North Dakota. His upbringing gave early exposure to the importance of hydrogen for fertilizers, fuels and chemicals. The industries are among the company’s targets.
Looking forward, he sees the greatest opportunity for growth for hydrogen in green steel and green ammonia.
“Green ammonia, of course, we already have existing uses of ammonia in ammonium and nitrate-based products that go into fertilizers, explosives and all sorts of other chemicals downstream,” Mason said. “With steel, this is really a market that’ll go from zero to 100 at some point as you replace coal and coke as the, let’s call it, reducing medium that’s used to convert iron ore to iron. Basically, you do that with hydrogen.”
Like others, Mason pointed out what appears to be a transition underway for hydrogen from hype to reality.
“I think the hype is dying down now, and people are starting to get more clear-eyed about the things that are needed to deploy real projects that actually reach final investment decision,” he said. “The vast majority of hydrogen projects that are being proposed right now are not reaching FID [final investment decision], and you have to ask why. Well, a lot of those projects don’t actually pencil out. And part of the reason they don’t pencil out is they need lower cost hydrogen. And that’s basically what we're attacking head on.”
Recommended Reading
Phillips 66’s NGL Focus, Midstream Acquisitions Pay Off in 2024
2025-02-04 - Phillips 66 reported record volumes for 2024 as it advances a wellhead-to-market strategy within its midstream business.
Rising Phoenix Capital Launches $20MM Mineral Fund
2025-02-05 - Rising Phoenix Capital said the La Plata Peak Income Fund focuses on acquiring producing royalty interests that provide consistent cash flow without drilling risk.
Equinor Commences First Tranche of $5B Share Buyback
2025-02-07 - Equinor began the first tranche of a share repurchase of up to $5 billion.
Q&A: Petrie Partners Co-Founder Offers the Private Equity Perspective
2025-02-19 - Applying veteran wisdom to the oil and gas finance landscape, trends for 2025 begin to emerge.
Chevron Makes Leadership, Organizational Changes in Bid to Simplify
2025-02-24 - Chevron Corp. is consolidating its oil, products and gas organization into two segments: upstream and downstream, midstream and chemicals.
Comments
Add new comment
This conversation is moderated according to Hart Energy community rules. Please read the rules before joining the discussion. If you’re experiencing any technical problems, please contact our customer care team.