
Drilling mud, along with samples of recovered water and oil and pellets generated by the process. (Source: Hart Energy)
A company taking “waste not, want not” to heart has developed a vacuum-assisted oil recovery process that makes it possible to reuse drilling mud.
The technology, which emerged from the construction industry, recovers used drilling fluid and water and generates fuel pellets. Nova Scotia-based R3 Environmental Systems, a subsidiary of Municipal Group of Companies, started developing the process in 2017, and in 2022 the Vacuum Assisted Pure Oil Recovery process received OTC Spotlight on New Technology recognition.
R3’s process heats used drilling fluid under a vacuum to evaporate out the oil and water fractions before condensing them and separating them into hydrocarbon and water products. Circulating the used fluid under heat and 20 mm to 40 mm of mercury lowers the boiling point—speeding up the distillation process and reducing the energy required to boil off the oil, said Patrick Rooney, director of manufacturing for Municipal Group of Companies.
Normally, he said, the recovered fluids would boil off at temperatures as high as 350 C.
“We’re boiling it off at 170 degrees Celsius, so therefore we’re not cracking” or degrading the oil, he said. “We’re pulling off just the virgin oil.”
He said the process makes it possible to use one part of recovered oil to heat the system while leaving two parts of recovered oil available for resale or further reuse.
“We're actually burning the oil in our industrial heaters,” Rooney said.
The recovered distilled water contains no chlorides, he added.
“The water could go back for a new formulation because being distilled water, there's no more chlorides in it. They could actually use that again to reformulate drill mud or use it in the process somewhere else. And in lots of places where water is scarce, it's very valuable to get the water back,” he said.
'200 mistakes ahead'
Jerry Scott, general manager for R3 said the amount of water in the mud affects the speed of the process.
“It takes a lot of energy to burn off the water. So if there's a lot of water,” the process takes longer, he said.
On average, the system can treat about two tons of used drilling fluid per hour.
Scott said the company started looking for a way to extract oil from drilling mud without cracking some years back. There are, he said, other technologies that can extract the oil, but rather than returning virgin quality oil, it’s degraded.
Rooney said the company investigated a number of technologies before choosing a path to pursue.
“Dyson never invented the cyclone. He's just the first one to put it in a vacuum,” Rooney said. “We looked at these different technologies and one of the ones that fascinated us was distillation.”
But pumping sludges under a vacuum posed some problems.
“Sludges are hard to pump in the first place. They’re abrasive,” he said.
Scott said pump vendors were not receptive to the concept.
“We had a lot of pump vendors even refusing to quote us once we told them the operating conditions,” he said.
Through a series of test projects, R3 was able to test different types of pumps and refine the system to include a combination of peristaltic pumps with high heat hoses and lobe pumps.
“We're better than the competition right now because we're 200 mistakes ahead of them,” Rooney said.
The process has been used offshore Newfoundland and Labrador for a year.
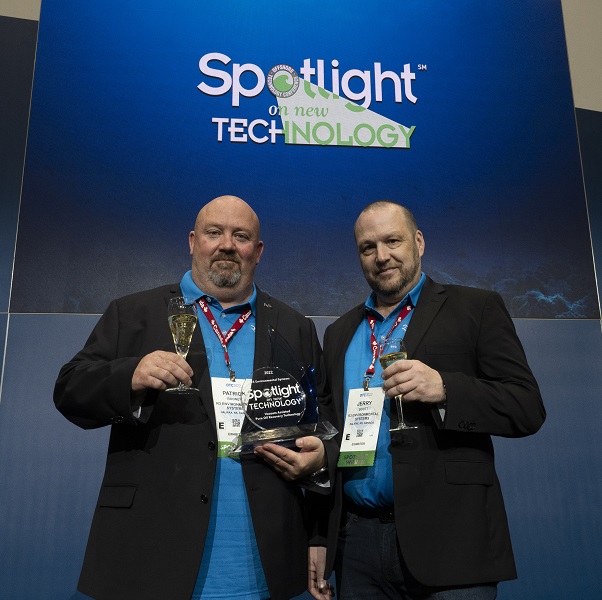
“We have good recovery rates for the oil in the water,” Rooney said. “That’s gone very well with multiple different types of mud.”
And while the process returns virgin oil and reusable water, it also creates fuel pellets, which can be used in cement kilns or industrial furnaces.
“Ideally, we'd like to make a fuel pellet that someone can use,” Scott said.
However, Rooney said, not all regions or operations are set up to use the resulting pellets.
He said the company is now working to make the process “highly mobile” to allow it to be used in remote locations where supply of drilling fluids is more difficult and recovered oil would be useful.
“The oil could be reused over and over and over again. So as long as it comes back to us as waste, we could reproduce the same base oil that could be over and over because we're not degrading it,” he said.
The whole process, Scott said, reduces the carbon footprint of operations.
“Typically to drill one well, we can save them about 400 tons of CO2 emissions,” he said. “It’s a start.”
Recommended Reading
Then and Now: 4D Seismic Surveys Cut Costs, Increase Production
2025-03-16 - 4D seismic surveys allow operators to monitor changes in reservoirs over extended periods for more informed well placement decisions. Companies including SLB and MicroSeismic Inc. are already seeing the benefits of the tech.
AI-Shale Synergy: Experts Detail Transformational Ops Improvements
2025-01-17 - An abundance of data enables automation that saves time, cuts waste, speeds decision-making and sweetens the bottom line. Of course, there are challenges.
Diamondback in Talks to Build Permian NatGas Power for Data Centers
2025-02-26 - With ample gas production and surface acreage, Diamondback Energy is working to lure power producers and data center builders into the Permian Basin.
Momentum AI’s Neural Networks Find the Signal in All That Drilling Noise
2025-02-11 - Oklahoma-based Momentum AI says its model helps drillers avoid fracture-driven interactions.
Digital Twins ‘Fad’ Takes on New Life as Tool to Advance Long-Term Goals
2025-02-13 - As top E&P players such as BP, Chevron and Shell adopt the use of digital twins, the technology has gone from what engineers thought of as a ‘fad’ to a useful tool to solve business problems and hit long-term goals.
Comments
Add new comment
This conversation is moderated according to Hart Energy community rules. Please read the rules before joining the discussion. If you’re experiencing any technical problems, please contact our customer care team.