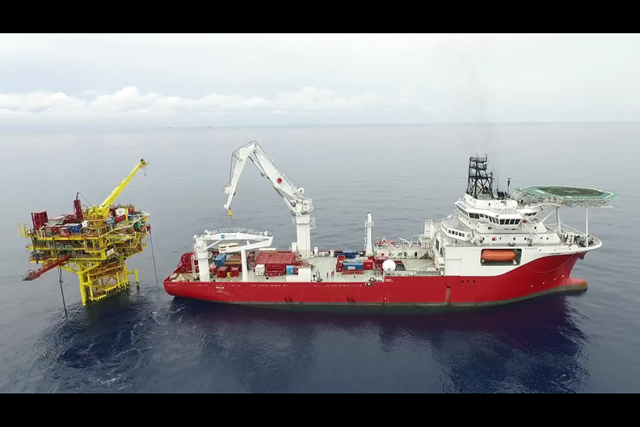
Well intervention operations offshore Malaysia. (Source: Malaysia Petroleum Management (MPM)/Petronas)
In the low oil price environment of the past three years, oil and gas companies have curbed spending and looked to where they could get more out of what they already have.
A project in Malaysia has been ahead of the curve, albeit not without its challenges. In 2013, with declining production rates and a growing fleet of so-called idle wells, Malaysia Petroleum Management (MPM), the part of state-owned oil firm Petronas which regulates upstream petroleum activities in Malaysia, decided to take charge.
The trigger was a realization that some 50% of the country’s well inventory was idle, resulting in a locked-in potential of some 80,000 barrels of oil per day (bbl/d), said Shahril Mokhtar, head of completions at MPM, which is also a partner on some 100 production sharing contracts (PSCs) in the country.
A goal was to arrest Malaysia’s production decline rate, and one of the key activities was a nationwide idle wells management strategy. It was initially a success, with additional production from well intervention activity increasing from 14,000 barrels of oil equivalent per day (boe/d) to 24,000 boe/d between 2013 and 2014. However, this was done at a very high price.
Also, when the oil price dropped, so did activity. Malaysia had up to 28 rigs operating prior to mid-2014. By the end of 2015, it dropped to just six, Mokhtar said.
Operations spending was also cut, and in 2015, production gain from well intervention operations fell from the 24,000 boe/d achieved in 2014 to 16,000 boe/d.
But, there was a deeper problem. Even when spending on well intervention had increased, success rates had only been 65%. “Spending US$100 million and getting only a 65% success rate is not a good way to run business,” said Mokhtar, speaking at a European well intervention conference in Aberdeen earlier this year. The problems were usually due to job failure, inefficiency, value leakage, and subsurface failures, he says.
Back To The Drawing Board
As a result, in 2015, a decision was made to re-assess the idle wells strategy. “MPM had to come up with a strategy to sustain the level of activity for well intervention and improve efficiency,” Mokhtar said. “We came up with a new strategy, called Integrated Idle Wells Restoration (IIWR), with a goal to: improve the success rate to at least 85% (was 65%); increase additional production from well intervention from 14,000 boe/d to 22,000 boe/d, while keeping costs down; and improve operational efficiency to 85%. Half of the latter (operational efficiency) is vessel utilization-related, i.e. the vessel is at dock, on standby, or waiting on weather, etc.”
The work tied in to another program, the nationwide Cost Reduction Alliance (CORAL 2.0) program, which set out to reduce overall upstream industry spending in Malaysia. Under the CORAL program, the Lean Well Intervention initiative was launched with a goal to reduce overall well intervention spending in Malaysia by 3% by 2016 and 10% by 2020.
What happened was perhaps a surprise. “The whole sector worked together and saved US$92 million (25%) within a year,” Mokhtar said. “It made us realize that all this time we were really not very efficient in well intervention.”
So where were the savings made? The biggest proportion of the cost saving (74%) came from just using the right operating model, i.e. using the right conveyance method (coiled tubing or wireline, etc.) and selecting the right equipment for the job, Mokhtar said. Standardizing equipment, removing standby costs, being fit-for-purpose and only mobilizing what was needed accounted for 14% of the savings, while contract management—negotiating better rates, aligning contracts to budgets available, etc. — made up 12% of the savings.
A large part of the success was based on using an integrated model, promoting collaboration and risk sharing. “The integrated model was something we hadn’t done before,” Mokhtar said.
Going To Work
The first major IIWR project was a nine-month continuous well intervention project with EnQuest. The objective of the project was achieved with 94% time working on well, with just 4% non-productive time and 2% waiting on weather. “Those are the types of efficiencies we want to see,” Mokhtar said. “Previously, it was 60% (time working on well).”
In another project last year, an 11-well start-up campaign, from two platforms, two vessels were deployed under an integrated project. “It wasn’t in the tender, but the proposal came in for two vessels to work concurrently and to do the work within 50 days using walk-to-work capability,” Mokhtar said. “This kind of set up has never been seen in Malaysia before.”
Mokhtar highlights that these are integrated projects, and not just bundling services. To work, this approach needs risk sharing. Historically, 50% of a project cost was marine-related, because if the slickline was down or coiled tubing stuck for two weeks the vessel would still have to be paid for. Now, in an integrated project, if a tool is down, everything is down, Mokhtar said. “It’s a single-package rate (solution-based), if you have one or two vessels, etc.
“You cannot expect to get same result from doing same things. We have changed how we work and the results shows that it is working,” he continued.
Results
Since the IIWR project started in 2016, the well intervention success rate has improved to 86% (from 65%), operational efficiency has improved to 94% (from 60%), and a production gain factor of 10 has been achieved, Mokhtar said.
In IIWR year one, only one project was completed (with EnQuest), but activity has been building. In 2017, three operators (EnQuest, Hess, and Shell) ran three campaigns using two packages. This year eight companies are running a total of 13 campaigns, with 13 packages being mobilized, Mokhtar said.
Furthermore, Shell completed the first subsea decommissioning work in Malaysia this year. The country will also see its first subsea stimulation campaign from a vessel this August, with Murphy Oil Co.
However, MPM isn’t resting on its laurels. It’s keen to see techniques that were dropped when the oil price fell, such as plugging and abandonment for sidetrack/infill well drilling, and hydraulic workover units come back in to use.
Mokhtar said other technologies, that haven’t been used for some time, are coming back, such as: fibre-optic coiled tubing; perforation, cement and wash (PWC); down hole cameras; and coiled tubing catenary (last used in 2014, and due to be used again in May this year). Work is also starting into full decommissioning of fields under IIWR.
With success, there’s also risk. “One concern now, as activity ramps up, is health, safety and the environment,” Mokhtar said.
You can be sure it will be on MPM’s target list.
Recommended Reading
Scout Taps Trades, Farm-Outs, M&A for Uinta Basin Growth
2024-11-27 - With M&A activity all around its Utah asset, private producer Scout Energy Partners aims to grow larger in the emerging Uinta horizontal play.
E&P Consolidation Ripples Through Energy Finance Providers
2024-11-27 - Panel: The pool of financial companies catering to oil and gas companies has shrunk along with the number of E&Ps.
Utica Oil E&P Infinity Natural Resources’ IPO Gains 7 More Bankers
2024-11-27 - Infinity Natural Resources’ IPO is expected to provide a first-look at the public market’s valuation of the Utica oil play.
Exclusive: Trump Poised to Scrap Most Biden Climate Policies
2024-11-27 - From methane regulations and the LNG pause to scuttling environmental justice considerations, President-elect Donald Trump is likely to roll back Biden era energy policies, said Stephanie Noble, partner at Vinson & Elkins.
FERC Gives KMI Approval on $72MM Gulf Coast Expansion Project
2024-11-27 - Kinder Morgan’s Texas-Louisiana upgrade will add 467 MMcf/d in natural gas capacity.
Comments
Add new comment
This conversation is moderated according to Hart Energy community rules. Please read the rules before joining the discussion. If you’re experiencing any technical problems, please contact our customer care team.