[Editor's note: This story first appeared in the 2020 Hydraulic Fracturing Techbook. View the full supplement here.]
Although the magnitude and quantity of disruptive events in 2020 continued to expose its vulnerabilities, the rumors of shale’s death have been greatly exaggerated. The effects of price wars and demand destruction are well analyzed and much discussed, but the slow climb back for the hydraulic fracturing industry is well underway.
E&Ps are finally getting around to completing and putting on production their multitude of DUCs, completions continue to be honed and optimized, and producers are finding the right spacing for their wells after some notable—and costly—trial-and-error experiments.
While R&D budgets, along with thousands of jobs, were slashed over the summer as companies looked to quickly shed costs, the path back to profits and productivity will undoubtedly include greater efficiencies downhole, particularly in the completion phase. The fully automated completion job continues to be the carrot on the stick that service providers are chasing, and the incremental gains toward that goal are showing such an achievement might be possible in the not-so-distant future.
Meanwhile, the energy transition is opening up new opportunities for operators and service providers alike to win back investor sentiment and achieve greater cost efficiencies. These factors add up to an inflection point for the North American shale industry.
“With the possibilities of external cost-cutting—for example, on contracting and leasing—all but exhausted, oil and gas companies now need to look internally,” McKinsey and Co. stated in an August report. “That means reinventing their operating models to improve efficiency and reduce greenhouse-gas emissions.”
New fracturing trends
In an era of consolidation in the fracking market, and intense competition among pressure pumpers, operators have capitalized by optimizing their frac designs. The zipper frac has proven to be a reliable cost-saver, but an emerging technique could cut pumping time in half. Simultaneous hydraulic fracturing, or simul-fracs, is a process in which two horizontal shale wells are stimulated simultaneously with one pressure pumping fleet.
“The real focus right now is trying to do more with less and maximize the efficiency, not necessarily just in operations, but on the capital and operating cost,” said Ian Henkes, senior vice president of operations with NexTier. “The gains will come more on applying these techniques like simul-fracking. In order to have a successful operation for simul-fracking, you need certain things to align. You need the proper well spacing and the proper pad size for this technique to be really effective.”
Henkes said the number of simul-frac jobs over the past year has increased about 15% versus traditional zipper fracs. However, widespread adoption for simul-fracking may still be some time off, as operators hold off on drilling new wells and instead work to complete their DUCs, which Henkes said typically do not meet the requirements for simul-fracs.
“Once we get through the DUC count that we have, which is probably going to take us pretty far into 2021, I think that’s when we’re going to start to see the real transition to more simul-fracking—once the operators start to drill more wells and they design their pads to meet the requirements for simul-fracking.”
With drilling activity only slightly recovering since a near-total shutdown in June, operators have turned to the proliferation of DUCs to maintain or grow production. As Rystad Energy noted in a September analysis of DUC trends, the recovery of fracturing operations in the U.S. is happening mostly as a result of the high inventory of DUCs. On March 27, the U.S. produced 13 MMbbl of oil, which dropped to 9.7 MMbbl on Aug. 28, according to the U.S. Energy Information Administration. That amount had ticked up to 10.7 MMbbl by early October.
Rystad estimates enough DUCs currently exist to sustain operations with the current rig count well into 2021.
“Beyond that, I think that the rig count is going to have to start coming back up to keep the completions activity from dropping after the second quarter,” Henkes said.
Completion designs
One of the primary drivers behind the production gains over the past five years of unconventional development has been the optimization of the well completion stage. Dialing in the right mix of lateral lengths, stage spacing, proppant and fluid pumping helped propel the U.S. to be the world’s largest oil producer. Tighter cluster spacing and the move to slickwater fracs helped increase stimulated rock volume (SRV), and the transition to pumping huge amounts of proppant opened greater amounts of fractures, exposing significantly more oil and gas to the wellbore.
According to Rystad, shale producers were fracturing a little more than 900 ft/d and pumping 1,600 lb/d of proppant in the first quarter of 2018. By the third quarter of 2020, those numbers increased to stimulating more than 1,500 ft/d and more than 2,800 lb/d of proppant.
But there is some indication completion intensities may have leveled off. Rystad reported that since the third quarter of 2017, fluid intensity has hovered at a little more than 40 bbl/ft while proppant intensity has remained between 1,750 and about 1,900 lb/ft.
Meanwhile, Leen Weijers, vice president of engineering with Liberty Oilfield Services, said one of the big macro changes across the different shale basins is the evolution of stage spacing.
“One of the biggest things we have seen as a company and as an industry has been letting go of the stage intensity criteria that was really key over the last decade,” he said. “On average, our industry went from 500 ft per stage to maybe 200 ft per stage over a period of about eight years or so. Now, that stage intensity criteria has relaxed a little bit, and they’re going to 250 ft or so per stage.”
Weijers added that Liberty has specifically focused on being more efficient in creating perforation clusters that lead to enhanced production. In limited-entry perforation, or extreme limited-entry perforation, changing the cluster design to fewer perforations with more clusters per perforation can lead to increased production.
Mike Mayerhofer, Liberty’s director of technology, echoed the importance of achieving longer stage lengths and pumping less stages while also maintaining the same cluster spacing.
“There is a lot of effort going on right now from companies trying to figure out the perforating strategies to make sure that the fracture treatment distributes the fluid and proppant as evenly as possible into all of the stage clusters (can be as high as 25 clusters per stage),” he said. “Some advanced modeling of fluid dynamics in the casing attempts to figure out the impact of shooting the perforation hole up through the casing or down through the casing or angled, and how that affects the distribution of the proppant through each cluster. Some of the supermajors are running these types of models right now.”
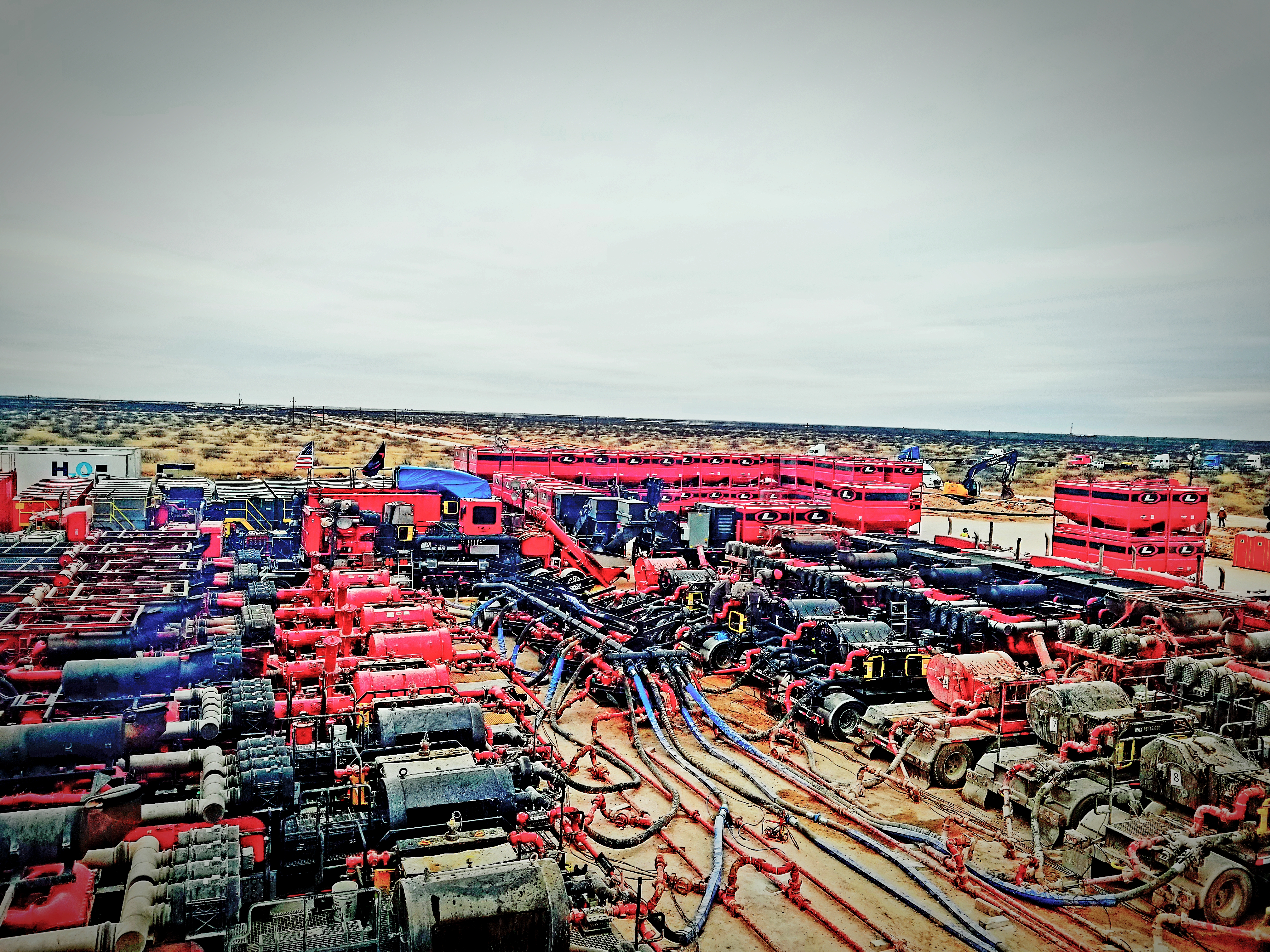
Amid the current oil and gas environment, Henkes added that it is unlikely many companies will look to experiment with new completion designs and instead continue to apply proven practices.
“Lateral lengths seem to have stabilized across the board to between 7,500 ft and 10,000 ft,” he said. “There is a benefit in having ultralong laterals, which have the potential to lower the cost per boe. The flip side, though, is it can be a higher risk in terms of drilling, running casing and cement.”
Well spacing
Among the most closely watched oilfield transitions is that of well spacing. In efforts to drain as many hydrocarbons from their acreage as possible, producers pushed the limits of pad designs and the number of wells those pads could hold, sometimes more than 10 wells per pad.
But as well interference problems emerged and frac hits began to show production degradation, the industry hit the brakes. Concho’s “Dominator” project, which featured 23 wells on a single pad, served as the warning sign after the company acknowledged they placed the wells too close. The fallout was immediate. Concho’s share price fell 22% in a single day, resulting in more than $4 billion in single-day market value loss.
Compounding the issue of well spacing is the need to appease the potentially conflicting desires of operators, engineers and investors, and the goals of targeting either returns or total value.
“There is definitely a lot of effort now, especially as companies slow down their completions, where companies are looking at their well spacing issues,” Mayerhofer said. “Some companies have spent quite a bit of money to do diagnostics to evaluate production interference between wells. There is no question in a lot of areas that wells are communicating. We’re taking some communication into account, but are the economics still favorable for that well spacing? If they are not OK, if the wells’ production deteriorates too much based on interference, then they start relaxing the spacing.”
At this year’s Unconventional Resources Technology Conference, Rystad Energy presented the findings of a well spacing analysis of nearly 7,000 wells in the Permian Basin. Rystad analyzed well spacing and productivity measured by IP 180/ft, which Rystad explains as reported IP over the first six months divided by the perforated lateral length of well in the sample.
The analysis generally revealed that production declines occurred when the number of wells per section totaled more than six. For example, in the Midland Basin Wolfcamp, pads with six wells per section produced an IP 180 of 14.9, an amount that steadily dropped on pads with an increasing number of wells, down to an IP 180 of 12.7 on pads with 10 or more wells.
Similar production trends were identified, particularly in the Delaware Wolfcamp and Bone Spring in Lea County wells. One outlier, however, was in the Delaware Wolfcamp in Reeves County. There, six-well pads produced IP 180s of 19.1, increasing as the number of wells per section increased, up to IP 180 of 22.8 for nine-well pads.
Still, Rystad derived that upspacing in the Permian would likely lead to better production.
“We conclude that the range of six to eight wells per standard spacing unit is the most popular and also the optimal for most landing zones and areas of the Permian Basin,” Rystad reported. “There are a few cases of well productivity and rate of return deterioration before the number of wells per unit reaches six. There are also a few cases of no significant interference for 10 wells per section, yet those cases are typically accompanied with low proppant intensity.”
The service industry has been hard at work adopting technologies and tools that can either predict when well interference issues may occur, or lessening the impact of frac hits. Weijers explained that one such tool is Liberty’s WellWatch system, which provides offset well pressure measurements.
Analyzing offset well pressures is emerging as a tool to limit far-field fracture growth and provide indicators to potential well interference issues. Weijers said Liberty’s recent acquisition of Schlumberger’s OneStim frac business will enable Liberty to enhance its well interference mitigation efforts.
“Schlumberger has a variety of fiber technologies, called Broadband, with some of it intended to work as a far-field diverter so we can distribute fracture growth more equally over different perforation clusters,” he said.
Weijers said it was important to understand differentials in fracture growth and how to better design every perforation cluster to distribute proppant and fluids that are being pumped downhole.
“I think there is great synergy between Broadband and our WellWatch diagnostic well interference measurements to ensure our customers that SRV is maximized in the space between wells, but that any unnecessary and excessive overlap between fractures from different wells is avoided,” Weijers said.

Automation/digitalization
While drilling operations have seen the most momentum and adoption in the automation space, well completion automation still proves to be mostly elusive. And simply due to the nature of technology adoption in the oil and gas space, it is unlikely full frac automation will take place overnight. Instead, microevolutions are occurring along the way, ones that in and of themselves may only solve a single completion challenge, but from a macro perspective serve as a brick in the wall.
Jon Walters, vice president of advanced analytics, controls and digital with National Oilwell Varco (NOV), explained that taking a holistic approach to designing a well’s life cycle could serve to enable more automation abilities in the completions space.
“When you’re talking about frac efficiencies, we assume those completions are contained within the completions world,” he said. “But are there decisions made during the drilling process that also have an impact on the completion process? As we develop our internal data aggregation platforms and our completions portfolios, we look to see if there are any overall holistic efficiencies that we can begin to stitch together.”
Walters said one of the processes most readily adaptable to machine learning automation and that can offer the most immediate tangible return is condition-based monitoring, which he called the “Holy Grail” of machine learning.
“When a failure of a valve or seat happens, we can come back with terabytes of data, and our scientists can identify the failures and expand the amount of time before the failure so that we can collect those data,” he said. “That’s where we’re investing a lot of our machine learning resources and data science resources.”
The Achilles heel for frac jobs and completions is nonproductive time (NPT), whether it be caused by operational inefficiencies or equipment failure. The management of equipment health can ultimately save a company millions, as NexTier’s Henkes said.
“Every piece of equipment that we have in the field right now on frac, wireline and pumpdown is transmitting real-time data,” he said. “We have equipment specialists, engineers and maintenance personnel with a lot of experience who monitor this information. We built an automated alerting system that notifies our equipment health technicians in our NexHub.”
Since NexTier implemented its NexHub alert system, the company has recorded more than $6 million in savings.

Any step along the automation path begins with data collection, and the proper application of those data. In the most tangible way, data collection can help keep people off the well site, Walters said. Instead, they can be located more safely in an office environment where they are then provided with actionable information from data collected minutes prior, whereas in the past those same data could be days or even weeks old.
Scott Hall, NOV product line manager, added that data gathered during the early portions of the well’s planning and construction—such as geosteering data, drilling information like ROP and gamma data—can all be merged and applied to optimize the frac and completions job.
“There is so much complexity in an automated frac job,” Walters said. “There are parts of that we are focusing on. We are trying to boil it down to today, tomorrow and not necessarily the future. The challenges our customers have today are different than they were six months ago and 12 months ago.”
Recommended Reading
After Big, Oily M&A Year, Upstream E&Ps, Majors May Chase Gas Deals
2025-01-29 - Upstream M&A hit a high of $105 billion in 2024 even as deal values declined in the fourth quarter with just $9.6 billion in announced transactions.
US Energy Corp. Closes Divestiture of East Texas Assets
2025-01-07 - U.S. Energy Corp. said proceeds from the divestiture will be used to fund the company’s industrial gas project in Montana.
Obsidian to Sell Cardium Assets to InPlay Oil for US$225MM
2025-02-19 - Calgary, Alberta-based Obsidian Energy is divesting operated assets in the Cardium to InPlay Oil for CA$320 million in cash, equity and asset interests. The company will retain its non-operated holdings in the Pembina Cardium Unit #11.
Sources: Citadel Buys Haynesville E&P Paloma Natural Gas for $1.2B
2025-03-13 - Hedge fund giant Citadel’s acquisition includes approximately 60 undeveloped Haynesville locations, sources told Hart Energy.
Will TG Natural Resources Be the Next Haynesville M&A Buyer?
2025-03-23 - TG Natural Resources, majority owned by Tokyo Gas, is looking to add Haynesville locations as inventory grows scarce, CEO Craig Jarchow said.
Comments
Add new comment
This conversation is moderated according to Hart Energy community rules. Please read the rules before joining the discussion. If you’re experiencing any technical problems, please contact our customer care team.