
(Source: Leonid Ikan/Shutterstock.com)
Presented by:
Editor's note: The full version of this article originally appeared in the February issue of E&P Plus.
Subscribe to the digital publication here.
Effective tank vapor gas management is a critical component for achieving environmental performance goals and improving wellsite safety. The current practice of flaring tank vapors produces emissions of greenhouse gasses (GHGs) and volatile organic compounds (VOCs), increasing permit requirements and negatively impacting ESG performance.
This article covers three primary methods of managing tank vapors and analyzes their relative advantages with respect to achieving environmental goals, impacts on operational processes and economics.
Tank vapor management methods
Flaring at upstream oil and gas production sites has come under increased scrutiny. A report released in 2020 by the Railroad Commissioner of Texas Ryan Sitton estimated that 5% of producing wells in Texas lack access to pipelines, and the gas volumes flared in Texas in 2018 have been estimated at 650 MMcf/d.
Although occurring in lower volumes, flaring of high-Btu tank vapor is also common, even at sites connected to gas pipelines. Factors driving tank vapor volumes include pressure reductions (flash vapor), working and breathing effects, and recovery of truck loading vapors. Flaring these NGL-rich vapors generates emissions of regulated substances and represents a significant loss of economic value. It is common for multiwell pads to generate upward of 300 Mscf/d of tank flash gas—an energy equivalent of 120 bbl/d.
There are three primary methods of managing these low-pressure vapors: flaring, partial capture before the storage tanks and full capture from atmospheric storage tanks.
Flaring
Flaring of site vapor usually requires a low-pressure flare or enclosed combustor device (ECD). These devices often have a destruction rate of VOCs exceeding 95% (typically 99% for C1-C3 and 98% for C4+), and the primary combustion products are CO2, water and NOx.
VOCs and NOx are precursors for ozone formation in the presence of sunlight. Because ozone is a federally regulated “criteria pollutant,” flaring at large production facilities in regions designated by the EPA as non-attainment for ozone may require the operator to secure a Title V air permit, which is time-consuming and expensive.
There are a number of reasons to use flares or combustors, with low capex being the most common. Oxygen contamination in the atmospheric tanks is another reason since pipeline tariffs usually specify no more than 10 ppm of oxygen in sales gas.
Partial capture
An alternative to flaring is to use a vapor recovery tower (VRT) to capture as much of the vapor as possible prior to liquids entering atmospheric storage tanks, avoiding oxygen ingress. VRTs generate incremental revenue from capturing a portion of the otherwise wasted gas product.
VRTs are not without their drawbacks. Variability in vapor flow presents several challenges. Vapor volumes are a function of well production volumes, oil composition and temperature, surface equipment, and operating pressures, among other factors. In addition, liquids separation is never perfect, and oil volumes in produced water tanks also generate flashing vapor.
The problem of flow variability can be seen in Figure 1, which estimates flows at several different points in separation at an eight-well pad. A common design issue is that VRTs are initially undersized. The lack of capacity results in low retention time, which lowers capture efficiency.
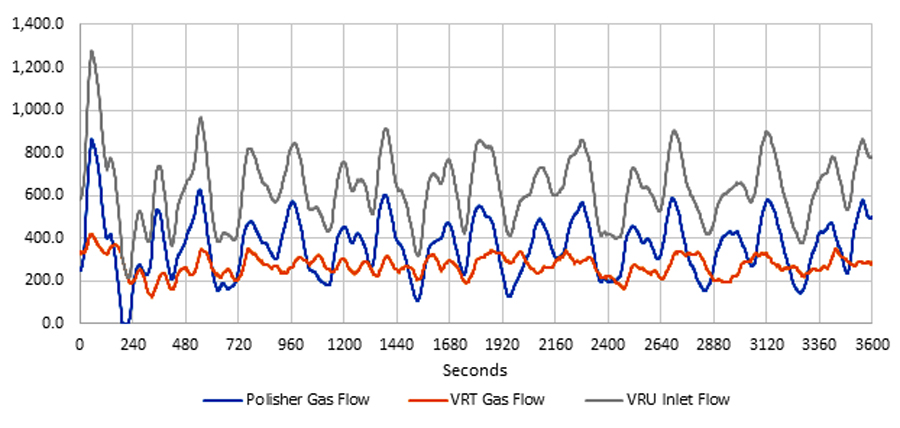
Since the VRTs only process the oil, flash vapor from produced water, working and breathing vapors in the tanks, and tank truck vapors have to be handled separately and are typically flared. Field data indicate that VRTs commonly capture 60% to 80% of the total low-pressure vapor volume at a pad.
Full capture
Total capture of low-pressure vapor requires recovery from the storage tanks. Limiting the effectiveness of tank capture methods, however, is the presence of oxygen in the tank headspace. As previously noted, oxygen levels are typically restricted by pipeline specifications.
One method for managing oxygen levels in storage tanks is the use of a gas blanketing system. Gas blanketing systems have been used for many years to mitigate explosive risks and have had some success in meeting pipeline limits for oxygen. Modern blanketing systems employ pressure transmitters, solenoids and programmable logic controllers.
However, maintaining the sequential system of pressure set points in a modern gas blanketing system in ounces per square inch is challenging. The increased operational complexity often requires operators to dedicate maintenance personnel specifically to the setup, maintenance and repair of tank hatches, vapor recovery units (VRUs) and flare/ECD inlet valves.
A second option for tank capture is the use of an oxygen removal unit downstream of the tanks. Instead of attempting to find and control the myriad sources of O2 ingress, this technology removes all oxygen from the entire vapor stream and ensures all of the site vapor meets pipeline requirements. This equipment typically has 99%+ uptime with the capture efficiency of the entire system limited primarily by the VRU.
There are a number of functional similarities between capture with a VRT and capturing directly from the tanks, but there are also some key differences (Figure 2).
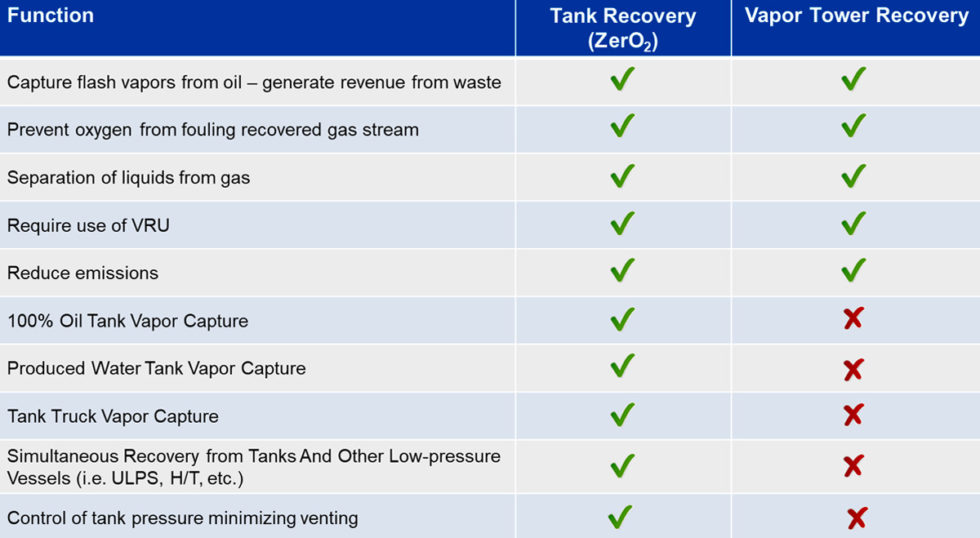
Comparison of capture methods
Emission profiles for the three capture methods were estimated using a volume of 300 Mscf/d. The estimate was prepared using a recovery efficiency of 75% for partial capture, a flare destruction rate of 98% and VRU uptime of 95%.
The results demonstrated that tank capture incorporating oxygen removal equipment downstream of the storage tanks resulted in the lowest emissions of GHGs and regulated substances.
Case studies
A major independent producer operating in the Powder River Basin evaluated vapor capture via a VRT versus tank capture using oxygen removal equipment. In the trial, each configuration was run for nearly 80 days, and vapor that was not captured was flared.
Results gathered by the producer are summarized in the table below.
The tank capture method resulted in a 37% reduction in flaring and incremental sales of rich-Btu gas. The tank capture method also employed a scrubber upstream of the oxygen removal unit, resulting in a 3% increase in crude oil sales as compared to the VRT case.
The operator estimated that the NPV of the tank capture configuration was approximately twice that of the VRT.
In another case study, Shell installed oxygen removal units at its central processing facilities in 2018 to reduce low pressure vapor flaring. While Shell has not disclosed the economics generated by the 32 units, the company reported that the resulting reduction in flaring reduced methane emissions in 2020 by the equivalent of 32 metric tonnes from 2018 levels.
In a 2020 case study, an operator in the Denver-Julesburg Basin discovered that the routine flaring of tank vapors was resulting in emissions levels requiring expensive and stringent air permits. Installation of oxygen removal equipment and capturing vapor directly from the tanks was credited with a 94% reduction in flared volumes. The value of the captured gas assuming a value of $2.50/mcf exceeds $23,000 monthly.
Conclusion
Emerging technologies for capturing tank vapor gas provide operators the opportunity to significantly mitigate flaring. Tank capture using oxygen removal equipment has proven to generate the greatest emissions reductions from all sources, with favorable economics and improvement in safety for operators and site equipment.
Recommended Reading
NatGas Shouldering Powergen Burden, but Midstream Lags, Execs Warn
2025-02-14 - Expand Energy COO Josh Viets said society wants the reliability of natural gas, but Liberty Energy CEO Ron Gusek said midstream projects need to catch up to meet demand during a discussion at NAPE.
NatGas Prices, E&Ps Take a Hit from DeepSeeking Missile
2025-01-28 - E&Ps such as Expand Energy and EQT Corp. saw share prices drop on news of less power-intensive AI, but analysts predict the natural gas market will rebound as LNG exports and overall power demand continues to increase.
Bottlenecks Holding US Back from NatGas, LNG Dominance
2025-03-13 - North America’s natural gas abundance positions the region to be a reliable power supplier. But regulatory factors are holding the industry back from fully tackling the global energy crisis, experts at CERAWeek said.
FERC Chair: Gas Needed to Head Off US Grid’s ‘Rendezvous with Reality’
2025-03-13 - Federal Energy Regulatory Commission Chairman Mark Christie is pushing natural gas to feed U.S. electrical grids before a “rendezvous with reality” occurs.
US LNG Exports May See EU Demand Drop-Off, Asian Surge
2025-03-27 - Ukrainian peace talks could end with Russian gas back on the market, Poten & Partners analysts said.
Comments
Add new comment
This conversation is moderated according to Hart Energy community rules. Please read the rules before joining the discussion. If you’re experiencing any technical problems, please contact our customer care team.