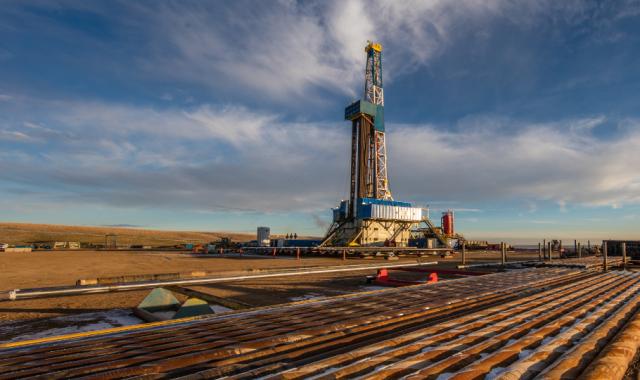
Through Lean manufacturing processes, Hess is continuing to increase efficiency and in turn bring down drilling costs in the Bakken. Pictured is the Nabors B06 Rig drilling a Hess well in December 2015 just south of Tioga, N.D. (Source: Hess Corp.)
It is one of the many 800-lb gorillas that always finds a way to be in the way. Accounting for it has become the norm in scheduling any type of work, be that punching up a spreadsheet, pushing a broom or turning a wrench. It is the wasteful product of inefficiency and poor planning. It is nonproductive time (NPT), and the challenge of eradicating it from the development of oil and gas resources has long been considered an impossible one.
But that view was challenged in 2014 when, through its use of Lean manufacturing, Hess Corp. attained zero NPT on an exploratory well offshore West Africa.
“One of the things I’m most proud of is our use of Lean principles in a deepwater drilling campaign in West Africa,” said Greg Hill, COO of Hess Corp. “We had 10 exploration and appraisal wells to drill offshore Ghana. Seven of those 10 wells were by far among the best wells drilled by the industry in West Africa. In particular, the last well had zero NPT. I’ve never, in 32 years of my being in this business, ever seen that anywhere on the planet.”
The company’s success in Ghana did not come overnight, but through the culmination of lessons learned over the last six years in its onshore and offshore operations. Hess’ shift to Lean—a manufacturing approach developed by Toyota that set the automotive world on its ear—started in 2010 in its Bakken program with the goals of reducing well costs and optimizing well productivity.
The company has since experienced a 62% improvement in spud-to-spud drilling performance in the Bakken—down from 45 days in first-quarter 2011 to 17 days in third-quarter 2015. It has seen a similar improvement in its reduction of drilling and completion well costs by 60%, from $13.4 million in first-quarter 2012 to $5.3 million in third-quarter 2015, according to the company.
For all of the initial success the company had in its Bakken program, the lingering question was could that success be replicated elsewhere? In transferring the principles over to its Utica operations, the company reported that it reduced drilling and completions costs by 41% and 43%, respectively, since application of Lean began there in 2013.
Having found success onshore, the processes have demonstrated similar returns offshore. In those efforts, the company has realized a 40% reduction in lifting and hoisting incidents over two years, a 50% decrease in the turnaround time in Equatorial Guinea, along with zero safety incidents and a significant reduction in construction time at its Stampede project in the Gulf of Mexico.
“For the Stampede project, we have a whole team applying Lean principles on it,” Hill said. “One of the major items to construct is a blast wall to protect the workers in the event of a process safety explosion. The team applied the Lean principles and realized a 40% reduction in the construction time.
“Stampede is a $6 billion dollar project, gross. If I can get a 10% or 20% improvement, these are huge numbers,” he said. “It actually more than offsets anything done in the Bakken because it has such a huge starting point.”
What is Lean?
Being “Lean” carries many definitions, but essentially it is a systematic method for the elimination of waste within a manufacturing system. Hill sees it as the art of doing work efficiently and something more.
“Basically, it’s about building a culture of problem solvers or, as we call it, an army of problem solvers,” he said. “One of the tenets of Lean is that leadership behaviors are everything. For example, a typical Western model of leadership is, ‘I’m the leader. You bring me problems. I solve them because that’s what I do. I’m the leader.’
“Actually, Lean turns that upside down. It says, ‘The role of the leader is actually to facilitate the problem-solving process with his team of workers’ because the best person who knows how to fix something is the person doing the work; very rarely is it the supervisor. That’s as much about a leadership model as it is about anything else,” he explained.
“It’s all about creating that culture that allows the workers to feel like they can contribute their ideas, and they’re involved in improvement. That’s why when you decide that you’re going to implement Lean, it takes a long time because it truly is a cultural journey. It’s not just picking up a book and training everybody in tools. If you don’t have the leadership culture behind
that, it will fail. It’s only a question of when,” he cautioned.
“There are principles to follow. It also is a culture of continuous improvement where everybody works to eliminate waste from the process. Waste is public enemy No. 1,” he said.
“A big part of it also is a standard of work with an emphasis on transparency in measurement. We measure safety, quality, delivery and cost,” he said. “It’s great to measure it, but you need a rigorous management process to look at those measurements to find areas of improvement in that standardized process.”
Establishing standards, gaining efficiencies
The need for standardization and collaboration are just two of the many drums being beaten currently by the industry in this “lower for longer” market climate. Lean, with its emphasis on both, is a natural fit to meeting these needs. It is through the standardization of processes, systems and components that the greatest efficiencies are found.
“I believe one of the Achilles’ heels of the oil industry is that everything is bespoke. You talk to our contractors, and they will say that one of their biggest frustrations is that there’s just not much standardization in our business,” Hill said. “The only way that Lean manufacturing can work effectively is through standardization of the work. Only then can you improve upon a standard.”
According to Hill, for the industry to realize across-the-board efficiency gains, a much higher level of standardization is needed.
“My hope is that is that the industry uses this downturn as a means to really focus on the inefficiencies that have been built into this business as a result of a rapid upturn caused by the U.S. onshore,” he said. “There was a lot of inefficiency that crept into the system. Lean is one way to address it. It is the way Hess is doing it because it works extremely well.”
Through Lean, Hess found a way to survive the lean times present during a market downturn. The company’s willingness to endure a journey of cultural change should contribute to its future longevity. It is a journey that experts have said takes years. For those daring enough to take the first step on their own journey, Hill offered the following advice.
“Don’t underestimate the challenge. Focus, at least initially, on the company leadership. Are they wired to thrive in a Lean environment?” he said. “Stick with it as it will be frustrating. But you will be shocked, amazed and surprised at the level of improvement that can be accomplished.”
Recommended Reading
ADNOC Contracts Flowserve to Supply Tech for CCS, EOR Project
2025-01-14 - Abu Dhabi National Oil Co. has contracted Flowserve Corp. for the supply of dry gas seal systems for EOR and a carbon capture project at its Habshan facility in the Middle East.
Partnership to Deploy Clean Frac Fleets Across Permian Basin
2024-12-13 - Diamondback Energy, Halliburton Energy Services and VoltaGrid are working together to deploy four advanced electric simul-frac fleets across the Permian in an effort to enhance clean and efficient energy solutions in the region.
Tracking Frac Equipment Conditions to Prevent Failures
2024-12-23 - A novel direct drive system and remote pump monitoring capability boosts efficiencies from inside and out.
ProPetro Agrees to Provide Electric Fracking Services to Permian Operator
2024-12-19 - ProPetro Holding Corp. now has four electric fleets on contract.
E&P Highlights: Dec. 16, 2024
2024-12-16 - Here’s a roundup of the latest E&P headlines, including a pair of contracts awarded offshore Brazil, development progress in the Tishomingo Field in Oklahoma and a partnership that will deploy advanced electric simul-frac fleets across the Permian Basin.
Comments
Add new comment
This conversation is moderated according to Hart Energy community rules. Please read the rules before joining the discussion. If you’re experiencing any technical problems, please contact our customer care team.