
Lyten’s lithium-sulfur battery pilot plant is located at the company’s Silicon Valley campus. (Source: Lyten)
With natural gas as a feedstock and abundant supplies of sulfur, Stellantis-backed startup Lyten is aiming to take its lithium-sulfur battery technology to the next level.
The San Jose, California, company recently opened its first automated pilot line to produce lithium-sulfur batteries in Silicon Valley.
The chemistry has been around for decades, but the sector has battled the downsides of sulfur: it degrades too quickly, which reduces the battery’s cycle life; and it needs a boost to discharge energy, a must-have for high-performance batteries.
Lyten says its battery technology has overcome those challenges with the incorporation of its 3D Graphene, made via carbon capture with methane or natural gas, into the process.
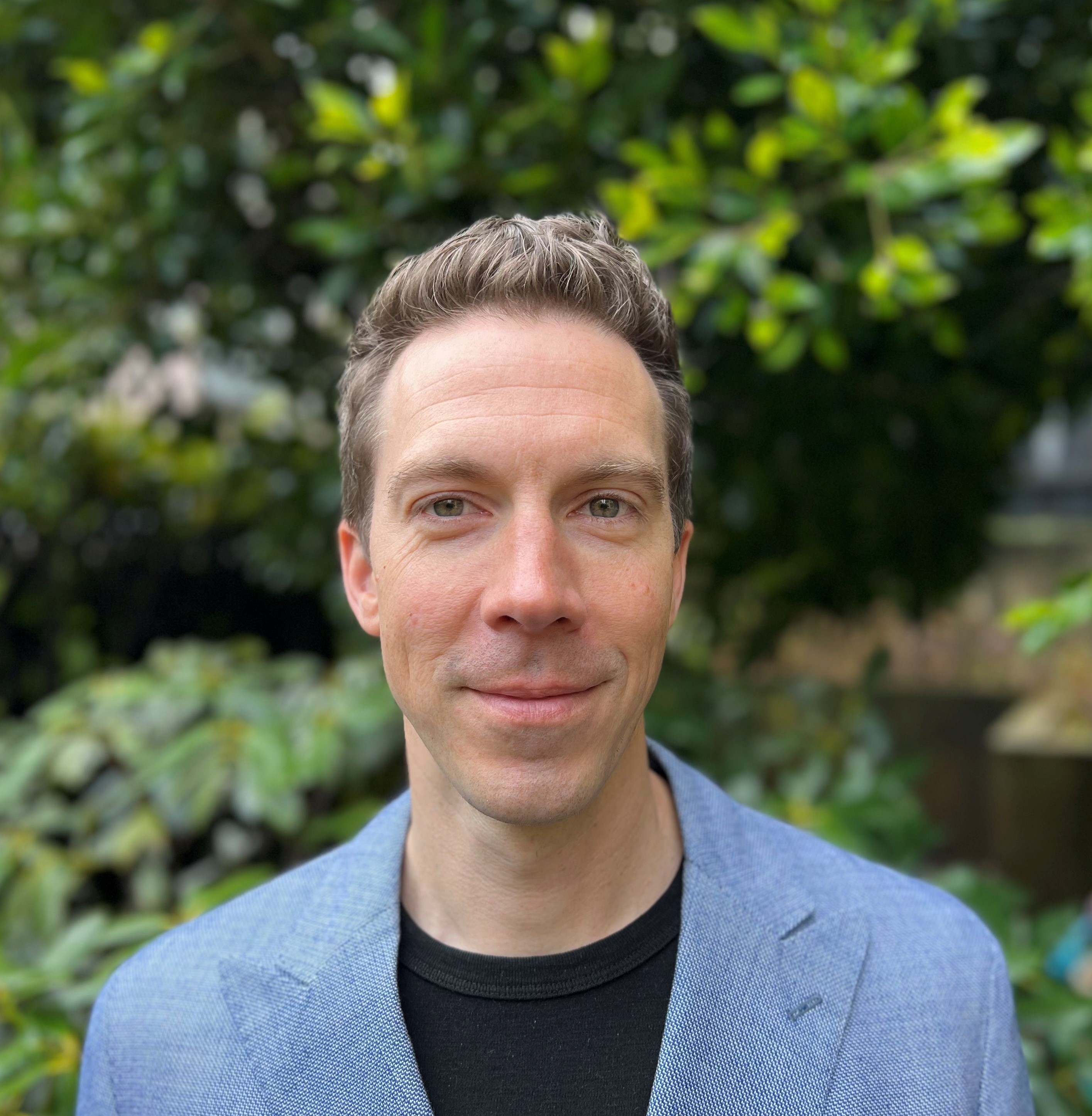
The lithium-sulfur battery doesn’t contain nickel, cobalt or manganese—which are tight in the supply chain. The battery is lightweight and packs a high energy density using materials that include low-cost waste product sulfur and abundant natural gas, Lyten Chief Sustainability Officer Keith Norman told Hart Energy.
“We believe we have a very clear pathway [toward] the lowest carbon footprint EV battery in the world,” Norman said.
Lyten, an advanced materials company, commissioned the lithium-sulfur pilot line as the U.S. and other parts of the world race to slow global warming. Electricity storage technology is seen as key to decarbonization, enabling widespread electrification.
The industry’s recent areas of focus have been on improving battery durability, boosting charge and discharge speeds, increasing power output and enabling recyclability.
However, access to certain critical materials and processing infrastructure is lacking in the U.S.
Rising demand
The U.S. forecasts global demand for critical minerals could jump as high as 600% in the coming decades as demand surges for production of batteries, electric vehicles, solar panels and wind turbines. Demand for lithium and graphite could increase by as much as 4,000% with a rise in EV batteries.
To help meet the anticipated need, the U.S. has moved to supercharge the sector, rolling out favorable policies and billions of dollars in incentives to spur development via the Bipartisan Infrastructure Law and Inflation Reduction Act.
“Even as we build the industry here, you still have some very, very clear pinch points that come through the Asian market and much of that through China in terms of having access to the minerals supply chain,” Norman said.

With most of the processing technology running through Asia, getting access to enough materials makes scaling domestically challenging. It’s something Lyten intends to overcome by using natural gas and sulfur to make lithium-sulfur batteries.
He acknowledged the chemistry is difficult.
“Anybody that tells you it’s not hard is not actually doing it,” he said. “But the benefits are so significant, if we are successful at doing that.”
The company projects the cost of materials for lithium-sulfur batteries is 50% lower than conventional lithium-ion chemistries. It says the batteries are twice as energy dense, allowing for greater storage, and have a cycle life of more than 800 charge cycles.
“The demand signal is very strong if we are able to deliver on the parameters,” Norman said.
Entering commercial mode
Located inside Lyten’s 145,000 sq ft Silicon Valley campus, the pilot plant has a nameplate capacity of 200,000 lithium-sulfur cells per year. The company plans to begin commercial delivery of the cells by year-end 2023 to early adopter customers.
The cells are being produced in a range of pouch and cylindrical form factors to meet customer requirements.
“Our battery works extremely well for stationary storage applications, but we're a super lightweight battery that’s really great for mobility,” Norman said.
The company, however, is not ready to feed an EV line due to the pilot plant’s capacity.
Focus is on applications that require high performance, long cycle batteries with a higher density. These include satellites and electric vertical takeoff and landing vehicles and satellites. The technology can be validated as the company looks to scale up.
Lyten has U.S. government and private contracts in place for batteries for satellites, drones and other applications in which significant recharges and charges aren’t needed, he said.
The plant is also testing Lyten’s equipment as the company moves toward building its first gigafactory next year. With a less than 5-gigawatt capacity at a yet-to-be determined site in the U.S., the gigafactory will be big enough to feed a line of heavy-duty vehicle trucks or perhaps a small line of EVs, Norman said.
Backed by Stellantis, the company behind automotive brands that include Chrysler, Dodge and Maserati, Lyten has quarterly deliverables to hit when it comes to energy density, cycle life and other performance parameters for the lithium-sulfur batteries.
The battery’s low cost and light weight could help drive down the cost of EVs, Norman said. He noted that weight impacts efficiency, safety and overall carbon footprint. “That’s really critical to get to a net -zero vehicle,” Norman said.
Creating a new market
Sourced from natural gas, Lyten’s 3D Graphene is a key ingredient of lithium-sulfur batteries.
The company uses its proprietary reactor technology to transform methane into carbon and hydrogen. The carbon, by Lyten’s website, is permanently sequestered in the form of 3D Graphene. Lyten has described it as a “supermaterial that starts a cascade of decarbonization impacts, like lightweighting materials and creating higher energy density batteries.”
“It’s like a gluten-free chocolate chip cookie that tastes better than an actual chocolate chip cookie,” Norman said.
The graphene can be formed in different ways, depending on the application. While it helps increase the energy density of batteries, 3D Graphene can be infused into polyethylene for added strength but at a lighter weight.
“We’re taking that same material to lightweight composites and plastics,” Norman said.
Lyten said the patented technology also improves the sensitivity of active and passive sensor arrays.
Given that 3D Graphene is sourced entirely from natural gas, the fossil fuel could become a decarbonizing material, enabling new applications and possibly creating a new market for natural gas feedstock, Norman said.
“We see that being a really important storyline as we bring this material to market,” he said.
Recommended Reading
Northwind Midstream Puts Delaware Basin Plant Expansion in Service
2025-03-13 - Northwind Midstream, backed by Five Point Energy, plans to continue growing its gathering and processing and amine treatment facilities.
Kinder Morgan to Build $1.7B Texas Pipeline to Serve LNG Sector
2025-01-22 - Kinder Morgan said the 216-mile project will originate in Katy, Texas, and move gas volumes to the Gulf Coast’s LNG and industrial corridor beginning in 2027.
WaterBridge Starts Open Season for Produced Water Pipeline
2025-04-01 - Water midstream company WaterBridge plans to develop transport capacity out of the Delaware Basin.
Canadian Province Gives Environmental Warning to Pipeline Project
2025-03-19 - The Prince Rupert Gas Transmission Project is a 497-mile project that would ship up to 3.6 Bcf/d of natural gas to an LNG facility on the Canadian west coast.
Apollo Acquires BP’s Gas Pipeline Stake for $1B
2025-03-23 - BP Pipelines holds a 12% interest in the Trans-Anatolian Natural Gas Pipeline (TANAP), which transports natural gas from Azerbaijan across Turkey.
Comments
Add new comment
This conversation is moderated according to Hart Energy community rules. Please read the rules before joining the discussion. If you’re experiencing any technical problems, please contact our customer care team.