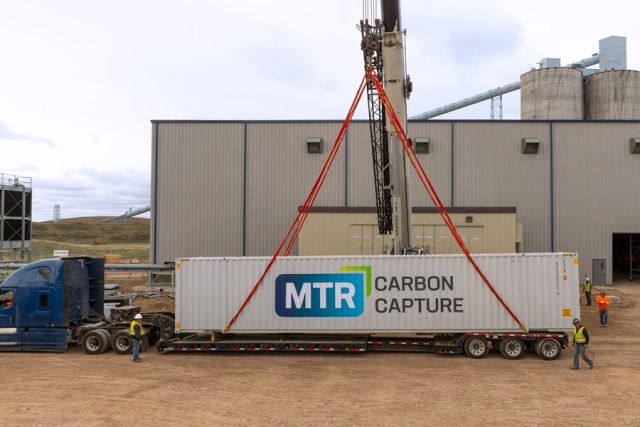
An MTR membrane container is delivered to the pilot plant at the Wyoming Integrated Test Center. The company is testing the technology’s scalability in Wyoming. (Source: MTR Carbon Capture)
What is being called the world’s largest membrane-based carbon capture system is set to go online in September, capturing more than 150 tonnes of CO2 per day from flue gas produced by a coal-based power plant in Wyoming.
Membrane Technology and Research (MTR) Carbon Capture’s full-scale commercial demonstration pilot at the Wyoming Integrated Test Center is targeting a 90%-plus capture rate and assessing the technology’s scalability. The project, which removes CO2 from flue gas produced by Basin Electric Power Cooperative’s Dry Fork Station, is progressing amid continued efforts to cost-effectively lower point source emissions from fossil-based power generation as electricity use rises.
“It’s the pilot at the end of the road here. We’ve been piloting with the Department of Energy and other entities for the last 15 to 20 years,” Paul St. Martin, senior project manager for MTR, told Hart Energy. “We’ve done about eight or so pilots/pilot programs. And this is …the final one to prove our technology. In this case, we’re proving scalability. We’ve proven that our membranes work. Now we’re proving that they work in an industrial setting with industrial-sized equipment.”
Carbon capture is expected to play a crucial role in lowering emissions, considering most U.S. energy consumption comes from fossil fuels. Companies with the bandwidth and capital, further incentivized by the 45Q tax credit, are pursuing such projects.
At the heart of the MTR-led pilot project is the company’s Polaris polymeric membranes.
Proving scalability
The membranes have been used commercially for the last 15 years in many applications to separate CO2 from syngas. In addition to recovering and purifying CO2 for sequestration, Polaris membranes are used for EOR and chemical and industrial applications, according to MTR.
However, “this is a different beast. It’s a low pressure, point source capture, very large volumes,” St. Martin said of the advanced Polaris membrane system. “We’ve designed it differently. The form factor is different.”
Membranes are typically installed in spiral-wound modules. MTR uses spiral-wound modules for industrial processes involving natural gas, hydrogen and petrochemical separation. However, the company instead used a stacked flat sheet membrane module, also called plate-and-frame, for the pilot project to ensure the pressure drop was low across the membrane, St. Martin said. This improves capture efficiency.
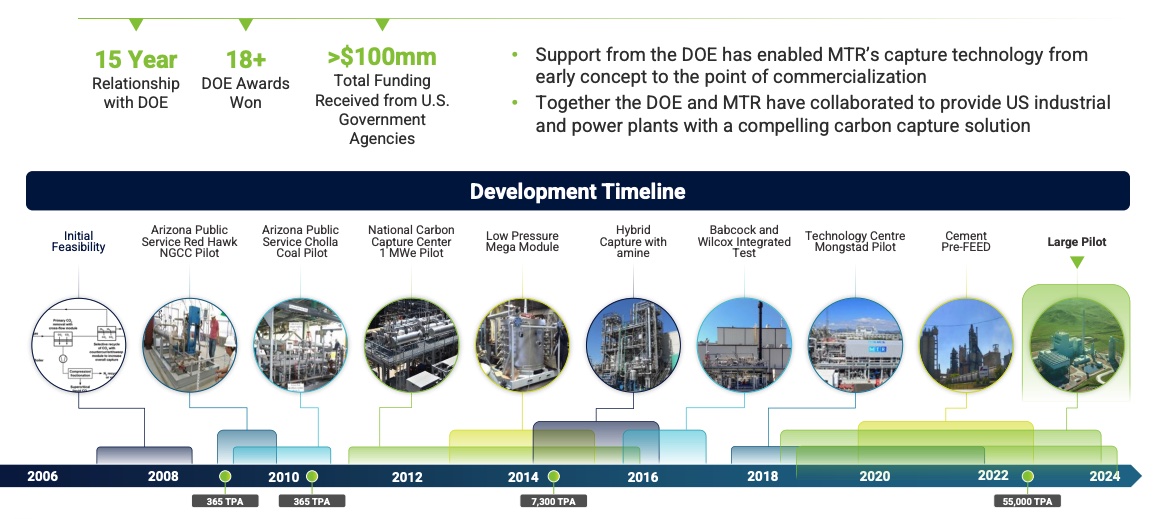
Capturing CO2 can be challenging when its concentration is low in flue gas containing other remnants from combustion processes. Flue gases from coal-fired plants typically have about 12% to 15% of CO2 by volume compared to about 4% to 5% for natural gas-fired plants, according to the National Energy Technology Laboratory (NETL).
Membranes have some advantages over some other capture types such as solvents and sorbents, according to Brett Andrews, president of MTR Carbon Capture.
“There’s no chemicals. So, there’s no degradation products,” Andrews said. “Amines can degrade into VOCs [volatile organic compounds], which can give harmful pollutants. They require a lot of water whereas membrane doesn’t.”
Amine systems typically require about 400 gallons to 500 gallons per ton of CO2 captured, he said.
Tackling costs
Capture costs vary depending on the CO2 content, Andrews added. “For a steel blast furnace, which has a fairly high CO2 content, typically you’re looking at about $40 per ton,” he said.
However, estimated costs could be as high as $120 per metric ton of captured CO2, according to a 2023 U.S. Congressional Budget Report on CCS, or carbon capture and storage.
Large emission sources—such as from electric power generation and some industrial production, fall on the higher end of the cost range.
When scaled up, MTR’s advanced membrane system featuring higher permeance membranes, lower pressure-drop modules and an optimized design could put CO2 capture costs at $30/tonne, according to the NETL. The agency noted the membrane’s packaging in a containerized form “allows for large numbers of this modular repeat unit to be arranged in future commercial systems at low cost.”
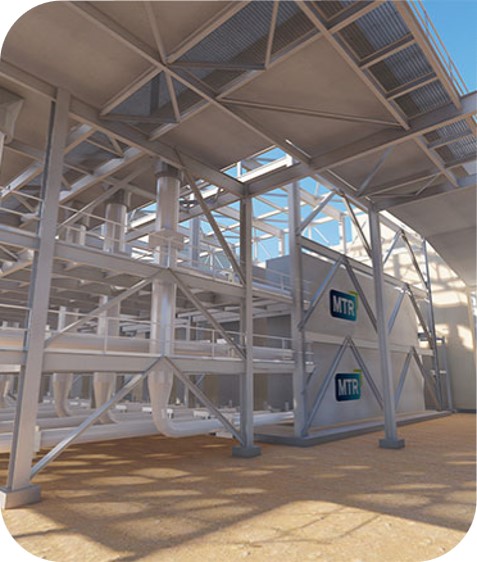
“It is highly selective to CO2 [and] highly permeable, which makes it cost effective,” Andrews said. “A lot of membranes are not because they have lower permeability so you have to compress the flue gas, which means a lot of energy.”
The Polaris membranes have 10 times the CO2 permeance of conventional gas separation membranes, according to an NETL technology sheet on the pilot project.
“A tenfold increase in permeance leads to a tenfold decrease in the required membrane area, which substantially reduces the capital cost and footprint of the capture system,” the NETL said. “These membranes, along with innovative process modifications, address challenges for post-combustion carbon capture.”
Next steps
MTR plans to run the system for about a year and half. The CO2 won’t actually be stored as the pilot only focuses on carbon capture; however, St. Martin said there is a liquefaction distillation process on the backend.
The pilot is using only a fraction of the total flue gas coming from the main stack at the power plant, Andrews said.
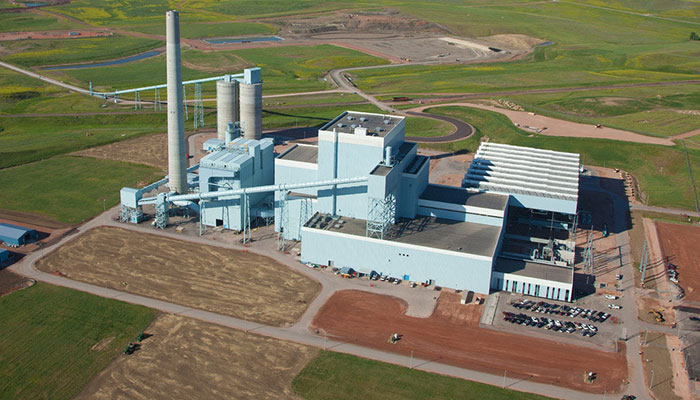
The company announced earlier this year that it was selected for $4.6 million in funding from the DOE’s Office of Clean Energy Demonstrations to develop a FEED study for an integrated carbon capture and storage project at Dry Fork.
Targeting at least a 90% carbon capture rate, the project aims to capture and store 3 million tonnes of CO2 per year. MTR has partnered with the Wyoming Carbon Storage Assurance Facility Enterprise Project, led by the University of Wyoming School of Energy Resources, for sequestering the captured CO2.
Recommended Reading
E&P Highlights: Feb. 18, 2025
2025-02-18 - Here’s a roundup of the latest E&P headlines, from new activity in the Búzios field offshore Brazil to new production in the Mediterranean.
E&P Highlights: Dec. 16, 2024
2024-12-16 - Here’s a roundup of the latest E&P headlines, including a pair of contracts awarded offshore Brazil, development progress in the Tishomingo Field in Oklahoma and a partnership that will deploy advanced electric simul-frac fleets across the Permian Basin.
Petrobras Awards SLB Another Contract Offshore Brazil
2024-12-12 - Petrobras has awarded JV SLB OneSubsea a contract for raw water injection systems a day after Petrobras selected SLB to handle integrated services at its offshore fields.
E&P Highlights: Jan. 27, 2025
2025-01-27 - Here’s a roundup of the latest E&P headlines including new drilling in the eastern Mediterranean and new contracts in Australia.
E&P Highlights: Dec. 9, 2024
2024-12-09 - Here’s a roundup of the latest E&P headlines, including a major gas discovery in Colombia and the creation of a new independent E&P.
Comments
Add new comment
This conversation is moderated according to Hart Energy community rules. Please read the rules before joining the discussion. If you’re experiencing any technical problems, please contact our customer care team.