
Jeremy Workman of NOV, Sola Oluwadare of SLB and Jim Jacobsen of IPT Solutions spoke at a panel during Hart Energy’s SUPER DUG Conference & Expo. (Source: Hart Energy)
Not that long ago, Diamondback Energy President and CFO Kaes Van't Hof was skeptical, to put it mildly, about drilling a 21,000-ft lateral well.
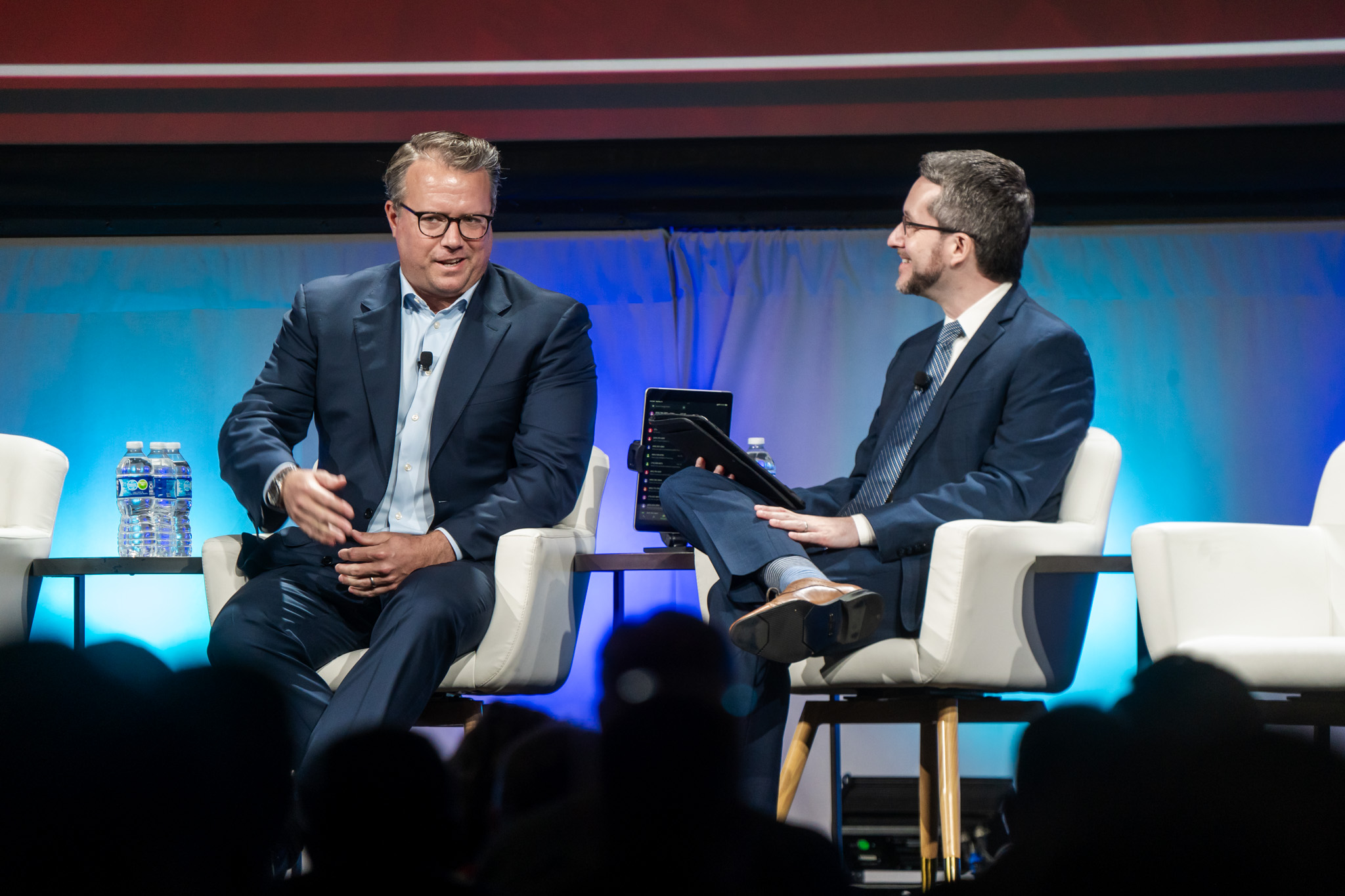
“A few years ago, I said we'll never drill four mile laterals,” Van’t Hof said at Hart Energy’s SUPER DUG Conference & Expo. Now, “here we are, saying we should be drilling four-mile laterals, you know, almost as much as we can.”
Technological advances in the oil patch have come a long way, and drilling has been a less mysterious process than the early days of the shale boom.
RELATED
Apache CEO: Longer Laterals Expected as Permian Enters New Era
Despite the ease of development when compared to wellbores of yesteryear, operators are still picky when choosing which areas to develop and how far out their lateral wellbores should stretch.
Ultimately, drilling three- or four-mile laterals is about profitability.
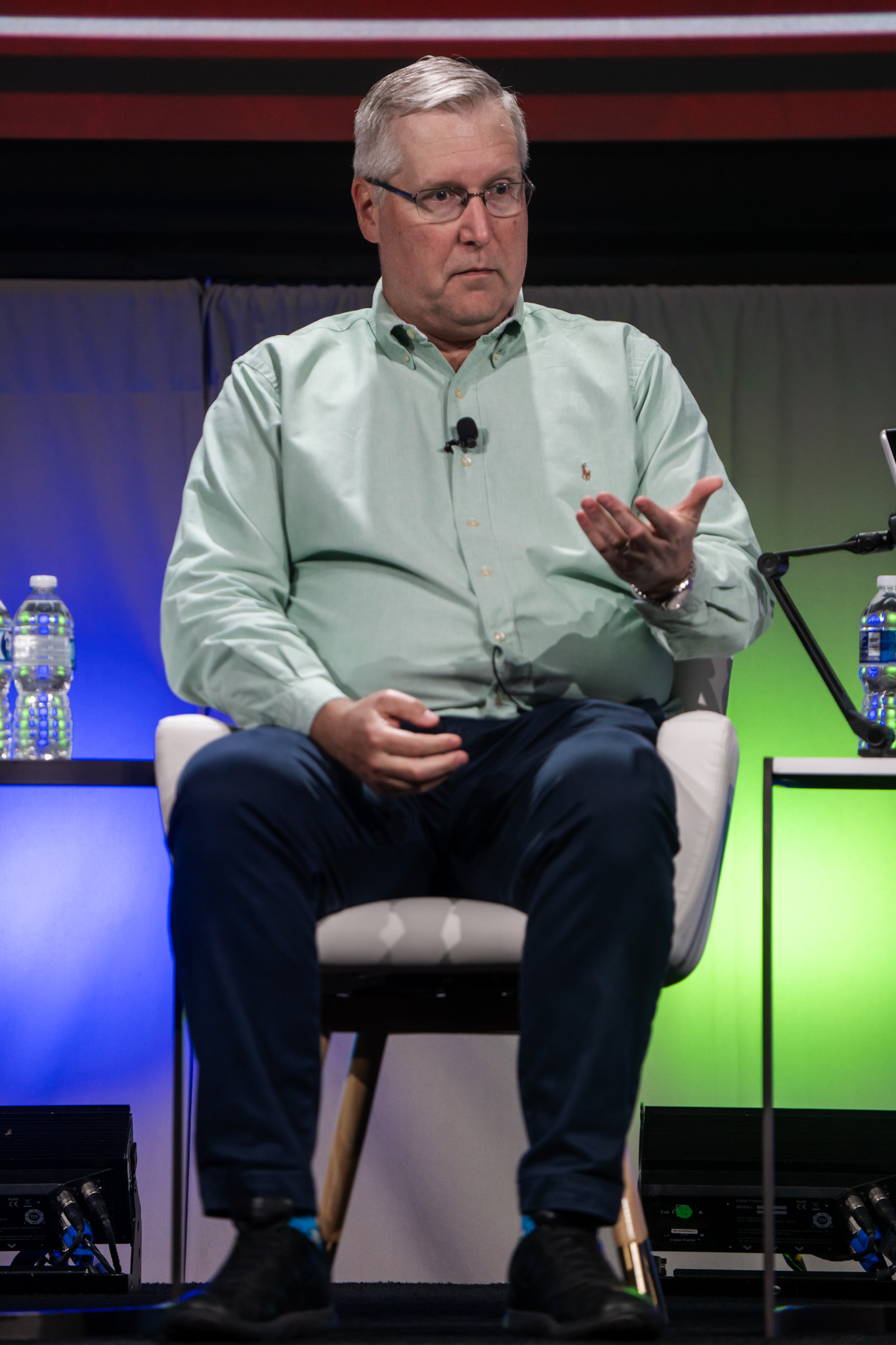
“If the land is available and the opportunity to drill the well is there, it comes down to economics,” Jim Jacobsen, drilling manager for IPT Solutions, said during a conference panel after Van’t Hof spoke. “You need to make sure that you drill a well that the completion team can complete and we can make money doing it.”
Jacobsen’s fellow panelists concurred. Their consensus: one way of increasing the viability of a development is by drilling long laterals, particularly as fewer above ground vertical wells are needed on a pad.
“There is a lot of room to save on building a pad and drilling the well,” Sola Oluwadare, drilling engineer for SLB, told the audience. “The ability to extend the length of the lateral right away eliminates all those additional costs. As technology becomes available for us to be able to extend those laterals and deliver to completion safely, those savings go directly to bottom line.”
And as Van’t Hof noted, lateral wells are getting extremely long.
“To me, these four mile laterals are a necessary evil,” Jacobsen said. “If you are doing these four mile laterals and you are seeing a linear production increase with each extra section of land that you drill, then it’s worth the time and money, but if you’re seeing diminished recovery with longer laterals, then at some point it’s going to become more cost effective and enable more recovery if you just drill another well.”
RELATED
New Permian Math: Vital Energy and 42 Horseshoe Wells
Friction is a drag
Despite the savings a lateral well can bring, all that glitters in the oilpatch isn’t (black) gold. One of the new challenges faced in the field, said Jeremy Workman, executive coil tubing salesman for NOV, is something seemingly inherent to longer length lateral wells: friction.
“In the past decade, there’s a lot of new challenges that we used to not face, one of them obviously being lateral lengths going out another mile plus,” he said. “It ultimately boils down to friction and that starts at the beginning in the wellbore.”
As the length of a horizontal well is increased, its contact with the reservoir increases, which increases the well’s resistance to flow and negatively impacts well productivity. Increased friction also increases the hydraulic horsepower that affects drilling costs. And while friction causes a host of issues by itself, it is not the only issue that can plague a lateral well.
The nature and shape of a lateral well lends itself to cuttings buildup. Inefficient cuttings removal out of the wellbore results in increasing drag and torque, stuck pipe, lower ROP and premature bit wear. While these issues can be solved by cleaning out the wellbore, the extended length of three and four-mile lateral wells make that process much more difficult. A way to mitigate these issues is through the implementation of coil tubing.
Workman said that by using a larger coil, it is easier to transfer weight deeper in the well, thus limiting circulating pressure. But that approach, too, can pose problems, as the increased size of the coil makes it harder to transport a reel with enough tubing string to reach the entire extended well.
Much technological development in the past five years to 10 years has enabled longer lateral wells. While those advances have been important to the industry, Oluwadare believes that a change in risk tolerance is what’s needed to drive lateral wells to greater success.
The more operators are willing to push their limits, even at the risk of breaking some of the tools they use, the more profit and progress they will see, he said, especially if the revenue from recovered oil is used to make up for the losses incurred by ruined equipment.
“There needs to be an inherent change in risk tolerance and some of the tools that are available for us to manage it as well… It’s going to be an inclusion of technology, a change of behavior automation, inclusion, dysfunction management, to help us actually drive this to better efficiency.”
Four-milers’ competitive edge
Diamondback Energy isn’t leaping into the four-mile laterals, but the company sees them becoming more common in lower-tier areas in the Permian Basin.
For now, Diamondback Energy is averaging 12,000-ft laterals for the next few years, Van’t Hof said. But as the company starts to explore more in the Wolfcamp D and Upper Spraberry through its pending acquisition of Endeavor Energy Resources, Diamondback’s acreage will start to get blockier in some areas. That should lead the company to extended lateral lengths.
Van’t Hoff said probably 150 locations to 250 locations can be stretched to 15,000-ft laterals from 10,000 ft.
“Generally, down the line, you're going to have to move towards three-mile laterals, four-mile laterals for these secondary zones to be competitive,” he said.
Recommended Reading
Digital Twins ‘Fad’ Takes on New Life as Tool to Advance Long-Term Goals
2025-02-13 - As top E&P players such as BP, Chevron and Shell adopt the use of digital twins, the technology has gone from what engineers thought of as a ‘fad’ to a useful tool to solve business problems and hit long-term goals.
PrePad Tosses Spreadsheets for Drilling Completions Simulation Models
2025-02-18 - Startup PrePad’s discrete-event simulation model condenses the dozens of variables in a drilling operation to optimize the economics of drilling and completions. Big names such as Devon Energy, Chevron Technology Ventures and Coterra Energy have taken notice.
Kelvin.ai the 'R2-D2' Bridging the Gap Between Humans, Machines
2025-03-26 - Kelvin.ai offers an ‘R2-D2’ solution that bridges the gap between humans and machines, says the company’s founder and CEO Peter Harding.
Momentum AI’s Neural Networks Find the Signal in All That Drilling Noise
2025-02-11 - Oklahoma-based Momentum AI says its model helps drillers avoid fracture-driven interactions.
Halliburton, Sekal Partner on World’s First Automated On-Bottom Drilling System
2025-02-26 - Halliburton Co. and Sekal AS delivered the well for Equinor on the Norwegian Continental Shelf.
Comments
Add new comment
This conversation is moderated according to Hart Energy community rules. Please read the rules before joining the discussion. If you’re experiencing any technical problems, please contact our customer care team.