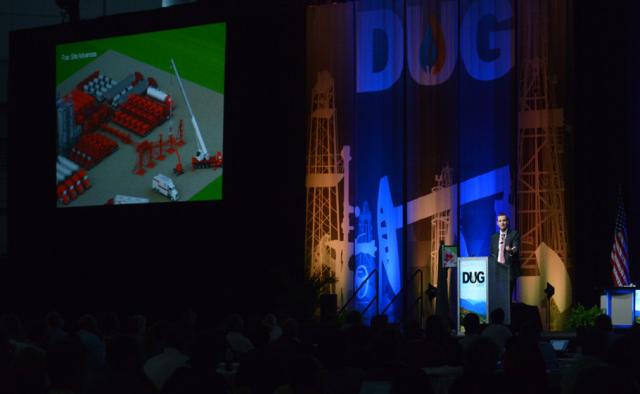
Stephen Ingram, Halliburton’s vice president for Technology Solutions and Innovation, was among the speakers at Hart Energy’s DUG East conference in June. (Source: Hart Energy)
Well stimulation providers are engineering inefficiencies out of the well construction process.
Super extended laterals comprise less than 2% of domestic horizontal wells, but the logistical challenges these wellbores represent can be engineered in ways that will improve completion effectiveness for hydraulic stimulation on all tight formation wells.
Stephen Ingram, Halliburton’s vice president for Technology Solutions and Innovation told attendees at Hart Energy’s DUG East conference in June how alterations in well construction, many originating out of the industry’s recent downturn, are not just improving completion efficiency but are being integrated with new downhole techniques to improve completion effectiveness and promise a smaller, safer wellsite footprint while lowering full cycle costs.
“There are so many opportunities to increase effectiveness, both in terms of cycle time but also effectiveness downhole to lower the cost of each barrel of oil and gas,” Ingram said.
Solutions—no pun intended—include transitioning to powdered chemicals instead of liquids or solvents, containerized proppant handling, mechanization of the wellhead lubricator connection and pressure testing along with the ability to move the lubricator quickly along a row of wellheads without an independent crane.
These innovations shave minutes off each stage decreasing cycle time enough to enable a fracturing crew to complete up to 40 more stages monthly at full utilization, which amounts to one more well per month per fracturing crew.
Downhole innovations include fiber-optic cabling cemented behind casing that employs lasers to track temperature changes and acoustic sensors to measure fluid distribution in each perforation cluster. Algorithms now enable the E&P technical team to use those data to make on-the-fly decisions on how to improve proppant distribution, providing realtime measurement of formation breakdown.
Ingram illustrated his talk with a schematic of a fracture stimulation surface configuration involving an eye-boggling array of trucks, tanks, silos, portable pumps, cranes and wellhead support equipment.
The new well construction techniques are scalable, real and available now—not aspirational—and adapt well to pad development. Changes include containerized proppant boxes, which eliminate the pneumatic tractor trailers that haul ever-larger volumes of fracturing sand to location.
Pneumatic truck proppant delivery was the main inflationary item outside Halliburton’s control during the 2014 boom as traffic backed up on lease roads waiting to offload proppant. At the site proppant was transferred to vertical silos and conveyed along mechanical belts subject to breakdown before blending into the fracture stimulation cocktail.
Containerized last-mile delivery solutions have transformed that process into a closed-loop system that eliminates vacuums, finicky mechanical conveyor belts and reduces silica exposure for employees below the latest Occupational Safety and Health Administration thresholds.
Ingram showed a graphic that presented the well site as a complicated parking lot for fluid storage in the form of tankers, including bulky, costly and potentially dangerous wellsite chemicals, such as acid, and diesel fuel.
The solution involves replacing liquids on site with powdered chemicals, friction reducers, surfactants and clay inhibitors. This reduces weight, bulk and truck traffic for materials that can be made up on site. The availability of dual fuel engines provides an option to avoid diesel storage and refueling while pumps are active.
Ingram challenged E&P companies to rethink the use of acid in completions, which can amount to 1,000 gal to 4,000 gal per stage to initiate formation breakdown. Work in the Bakken, Denver-Julesburg Basin and internationally indicates ultrafine mesh in the initial fracture treatment fulfills the same function in carbonaceous reservoirs and provides lower breakdown pressures and lower average treating pressure, reducing screenouts and cycle time.
Recommended Reading
Queen’s Chess: Changing the Rules
2025-02-28 - There’s a popular response to the inexplicable: “I don’t know. I don’t make the rules.” But what is known with certainty, as shown throughout history, is that we can change them.
Comments
Add new comment
This conversation is moderated according to Hart Energy community rules. Please read the rules before joining the discussion. If you’re experiencing any technical problems, please contact our customer care team.