The industry’s deep dive into production technology enhancements began with … a deep dive.
“I’d say the first breakthrough was the industry’s decision to actually put the wells on the bottom of the ocean to do subsea wells,” Owen Kratz, president and CEO of Helix Energy Solutions, told Hart Energy.

But far from the last. From the installation of the first subsea trees in the early 1960s, the industry has continually pushed the limits of production tech in the realms of semisubmersibles, artificial lift and automation to extract every hydrocarbon molecule possible.
Kratz, who has been involved in the industry since the 1980s, has served as a director at Helix since 1990 and was the chairman of the board from 1998 to 2017.
The first vessel built specifically to execute well intervention was launched in 1987, he said. Prior to that, drill rigs were the only asset used.
Helix was the first company to implement riser-less well intervention and was a pioneer of the process. However, in the late 1980s, the company could only carry out wireline intervention.
Wireline intervention involves running and pulling tools and equipment into and out of the well with a continuous-length wire mounted on a powered reel at the surface. Typical wireline operations include perforating, logging, pulling, cleaning wells and dumping cement.
While wireline is light, easy to assemble and move, and does not require the application of a drilling BOP or heavy equipment, it isn’t the most effective form of well intervention.
Things turned around in 1998, Kratz said, when a vessel other than a rig was used to deploy a riser for the first time. This allowed coil tubing to be run into the well, which greatly increased what can be done in the well.
The door was now opened to a whole new world of well intervention.
“In ’98, we were the first ones to run a small-diameter high-pressure riser,” Kratz said. “A drill rig uses low pressure; they use the mud and the riser to hold the pressure in the well. What we did was reduce the size of the riser to seven inches, and we took the high pressure all the way back up to the vessel and kept the blowout preventer on the vessel.”
This small-diameter high-pressure riser was run from the Uncle John and, while it yielded mixed results, the job was deemed successful enough for Helix to build around the idea. This led to Helix launching the Q4000, a multipurpose oil field construction and intervention vessel, in 2002.
“[The Q4000] was a relatively small vessel and it was semisubmersible so that the motion characteristics were beneficial,” Kratz said. “We were able to use a smaller vessel for a couple of reasons. One, it also had the first, multipurpose tower. And, it was an open-sided derrick, whereas drill rigs all used Texas towers with V doors. So, there was a great efficiency gain by having a derrick that was open on three sides.”
The Q4000 represented a welcome milestone for both Helix and the energy industry as a whole, but the company has its sights set on a future in which rigs are no longer needed for interventions or decommissioning.

“We’re hoping to introduce exciting technology this year,” Kratz said. “Now, it takes a while for the industry to accept new technologies but I think that, especially for decommissioning, we could be in a position to eliminate the need for a rig, on the vast majority of cases, by next year.”
Artificial lift
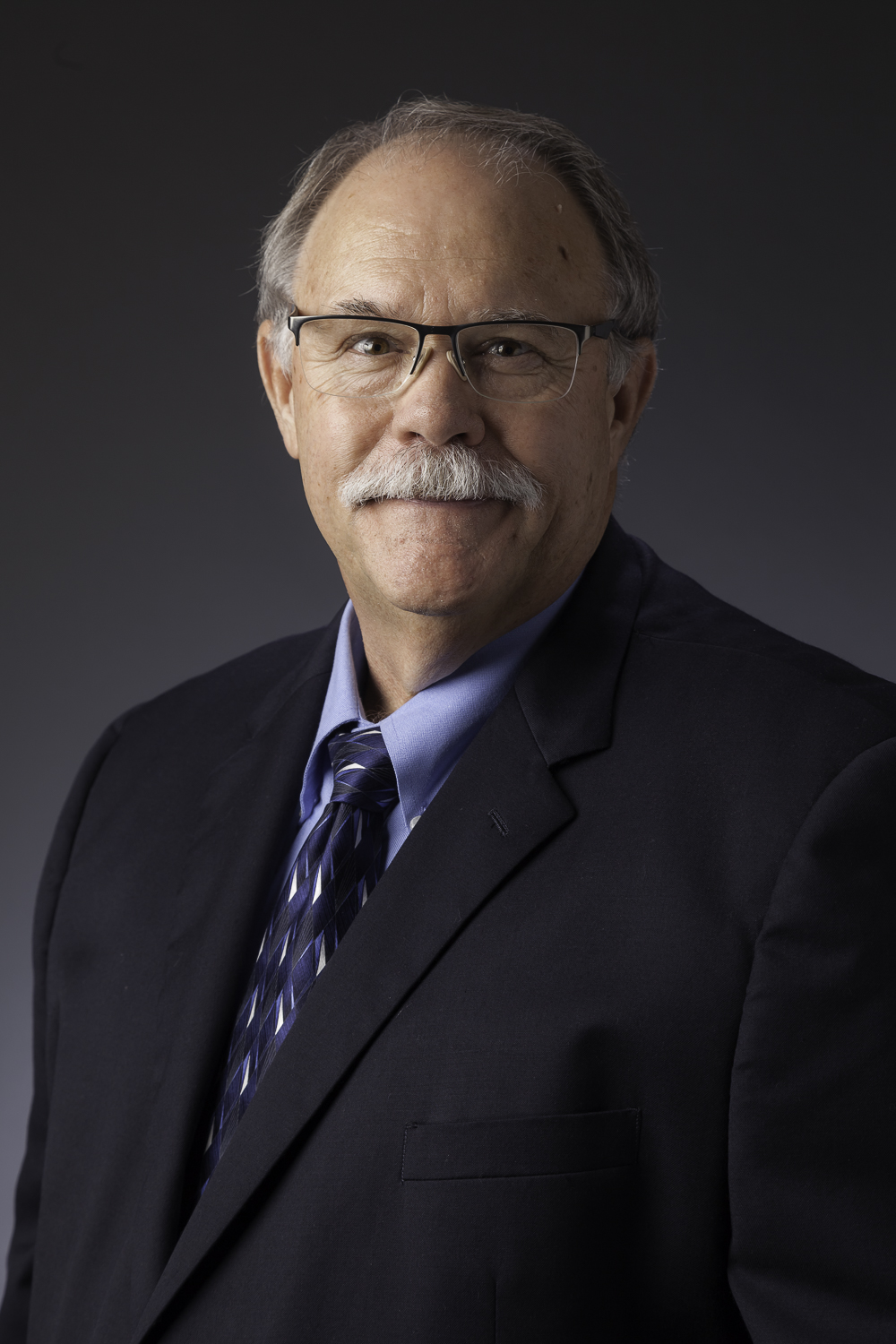
Another way to ensure that the majority of hydrocarbons have been extracted from the well is through artificial lift, a technology that has been around since ancient Egyptians invented the shaduf, a hand-operated device to lift water for irrigation. Closer to this century, the rod pump looks pretty much as it did when it was developed 150 years ago.
“The pump itself, for probably 150 years, has been very similar,” Rodney Sands, business development manager at ChampionX, told Hart Energy. “There are many advantages with the design, so there’s been very little design change. Metallurgically, the design has gotten better, but the basic pump is the one that was used 150 years ago.”

Rod lift is one of the most commonly used forms of artificial lift. The surface-pumping unit of a rod lift system consists of a prime mover (usually an electric motor) and a beam fixed to a pivotal post. This system allows the beam to rock back and forth, moving the downhole components up and down in the process.
Linked rods attached to a downhole pump are connected to the surface unit. The linked rods typically fit inside the tubing and are stroked up and down by the surface-pumping unit. This activates the positive displacement pump at the bottom of the well. Each time the rods and pumps are stroked, a volume of produced fluid is lifted through the tubing annulus and discharged at the surface.
The second most common form of artificial lift is an electric submersible pump, or ESP. An ESP system consists of centrifugal pumps made up of multiple stages connected to a submersible electric motor. The motor is powered by heavy duty cables connected to surface controls. The motor rotates the shaft, which is connected to the pump, and the spinning impellers draw in fluid through the pump intake, pressurize it and lift it to the surface.

But while rod lift and ESPs are two of the oldest and most common forms of artificial lift, “they’re both really quite inefficient in terms of energy input,” said Terry Treiberg, senior engineering advisor at ChampionX. The use of variable speed drives is one of the biggest technology changes in rod pumping, and is now commonly implemented.
“When I first started in the late ’80s, we didn’t hardly have any variable speed drives on rod pumps,” Treiberg said. “Today, there are many companies that standardize on variable speed drives, and those are used to better control the well. If you can change the speed of the motor in different parts of the stroke, you can achieve even greater efficiencies and extend equipment life.”
Changing motor speeds allows operators to avoid many of the problems that can occur during pumping. It enables the operator to precisely slow down the rods if production is not available and minimize rod compression that can happen during the downstroke of the pump.
But while system efficiency is important, the decision to pick a particular form of lift is “very complex,” said Brian Hicks, director of ESP and engineering for ChampionX, because the decision isn’t primarily driven by overall system efficiency.

“Part of [the decision] is around the time value of money and how quickly operators want to produce the reservoir over the potential life of the reservoir,” Hicks said. “You’re balancing the early production versus the full lifecycle potential production.”
Operators must find a balance between meeting economic requirements and meeting certain technical factors. The complexity of the process increases with horizontal wells because of the added mechanical stress on the equipment.
With new wells, operators seek to access more of the reservoir, Hicks said. As they drill their lateral, they follow the natural geology.
“When operators fracture [the well], fluid starts to come into the wellbore and it travels through this hole that has all these direction changes,” he said.
As a result of the various changes in direction, the dynamics of the fluid moving into the wellbore are constantly changing. For example, slugs of gas accumulate on the high side of undulations in the horizontal section of the wellbore. When those slugs break free, they flush through the wellbore and hit the pumping system. Pumps need to be able to adequately handle this rapid change of fluid composition or risk becoming damaged.
New materials are being tested to find ways to lessen the stress on the pumping equipment and decrease the pump’s chances of failure.
“Material science is advancing quickly in the industry overall and, even outside of oil and gas, there are learnings regarding different coatings, different metals and different elastomers that may improve the ultimate reliability and performance of the equipment,” Hicks said.
There has also been a push to incorporate automation, machine learning and artificial intelligence into artificial lift to increase efficiency.
“We can get data back much more quickly and store more data than we’ve ever had the ability to do before,” Hicks said. “Being able to store data and retrieve it faster, we can do a much more in-depth analysis. In the last five years, the big advancements have been in the progression of analysis.”
While Hicks does admit that there is a long way to go, real-time adjustment can mitigate a lot of the artificial lift’s inefficiencies. ChampionX is working on embedding new sensors into its equipment to gain more real time analytics and use automated processes to adjust and enhance operations.
This may be the age of the energy transition to cleaner fuels, but the industry will be heavily reliant on automation and machine learning to get there.
“Looking towards the future, there is an energy transition happening, but every data source forecasts a substantial need for oil and gas in the future. There may not be as much capital to develop the fields as there was in the past, given the competition for capital amongst all these different energy sectors,” Hicks said. But, “it’s incredibly important to produce the oil and gas fields that you have or any new ones that you bring into production as efficiently as possible."
Recommended Reading
Expand Lands 5.6-Miler in Appalachia in Five Days With One Bit Run
2025-03-11 - Expand Energy reported its Shannon Fields OHI #3H in northern West Virginia was drilled with just one bit run in some 30,000 ft.
Ring May Drill—or Sell—Barnett, Devonian Assets in Eastern Permian
2025-03-07 - Ring Energy could look to drill—or sell—Barnett and Devonian horizontal locations on the eastern side of the Permian’s Central Basin Platform. Major E&Ps are testing and tinkering on Barnett well designs nearby.
Hibernia IV Joins Dawson Dean Wildcatting Alongside EOG, SM, Birch
2025-01-30 - Hibernia IV is among a handful of wildcatters—including EOG Resources, SM Energy and Birch Resources—exploring the Dean sandstone near the Dawson-Martin county line, state records show.
Formentera Joins EOG in Wildcatting South Texas’ Oily Pearsall Pay
2025-01-22 - Known in the past as a “heartbreak shale,” Formentera Partners is counting on bigger completions and longer laterals to crack the Pearsall code, Managing Partner Bryan Sheffield said. EOG Resources is also exploring the shale.
E&Ps Pivot from the Pricey Permian
2025-02-01 - SM Energy, Ovintiv and Devon Energy were rumored to be hunting for Permian M&A—but they ultimately inked deals in cheaper basins. Experts say it’s a trend to watch as producers shrug off high Permian prices for runway in the Williston, Eagle Ford, the Uinta and the Montney.
Comments
Add new comment
This conversation is moderated according to Hart Energy community rules. Please read the rules before joining the discussion. If you’re experiencing any technical problems, please contact our customer care team.