Presented by:
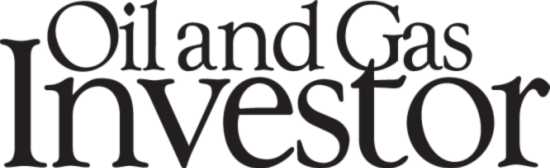
For the first time in what seems like years–certainly, pre-COVID years–a sense of stability has returned to the upstream oil and gas industry. Backed by solid and stable oil and gas prices, as well as tempered growth and spending, producers have seemingly found the sweet spot between generating returns for investors, growing production and navigating the energy transition.
At the core of much of this sustained stability is operational efficiency. Producers have tightened their belts in spending while slowly but steadily growing production. Still, rig counts are far below pre-COVID levels. However, cost savings and lowered capex doesn’t always come from decreased activity, nor does all production growth result from drilling new wells.
Both center around the adoption and deployment of technology applications that are enabling operators to identify more pay, cut down on costs and enable greater efficiencies, which in the end results in a healthier bottom line. According to Rystad Energy, the U.S. shale industry is expected to see $4.2 billion in efficiency gains in 2022.
Advances in drilling technology, a better understanding of the subsurface, automating labor-intensive processes and oilfield electrification have all contributed to improved economics in a resurgent and more stable oil and gas industry.

Going electric
Callon Petroleum Co. operates more than 180,000 net acres in the Permian Basin and Eagle Ford Shale. Senior vice president and COO Jeff Balmer said Callon differentiates itself from its peers through its approach to technology applications, which starts, he said, with field development planning.
“To be capital efficient and optimize your dollar but maximize your recovery, you have to really take a regional aspect approach and then work it all the way down to the well, and in particular for us at the pad level,” he said.
Like most producers, Callon historically relied on diesel power generation to power its well sites. But Balmer explained that by investing capital to connect the company’s operations into the local power grid, not only is the company improving its ESG performance, but it’s also realizing significant cost savings.
“We look at opportunities for items like electrification in the field, which allows us a very controlled, dependable source of power,” he said. “It improves run time on all of our artificial lifting equipment. All of our pump jacks, all of our pump down controllers now utilize a very controlled, very uniform system. And then of course on the emissions side, you are no longer using diesels. So you’re cutting down on your emissions. You don’t have the truck traffic. You don’t have the physical transfer of the fuel on location. And from a savings standpoint, in the Eagle Ford alone, we’re going to save half a million dollars a month in operating expenses.” Balmer noted that transitioning from diesel to electric takes upfront capital, but the payout for Callon came in less than a year. “And then you’ll be making money every single day that you have the infrastructure up and running,” he said. And while Callon has committed to significant implementation of electrification of its producing equipment, the company has also tested the waters on e-frac with a three-well pilot with U.S. Well Services. Balmer said that for this year, Callon will be running “very energy efficient, low-emission frackers.”
Downhole imaging
In many ways, a producer’s fortunes are often only as good as its rock. But improving an understanding of the subsurface, and subsequently the available pay, is paramount to maximizing production and eventually profits.

A focus for many service companies in recent years has been on developing tools and technologies that solve that challenge, and improved downhole imaging is paying off.
Schlumberger Ltd. has deployed technologies that enable multilayer mapping while drilling technologies that allow the operator to optimize geosteering operations and accessing initially bypassed oil or secondary oil targets.
Vera Wibowo, product champion GRM Geology for Schlumberger, explained that reservoir understanding has evolved over the past few decades, beginning with what she described as “reactive geosteering,” then the adaptation of downhole imaging emerging about 25 years ago, transitioning to advancements in geosteering and reservoir mapping.
“The breakthrough came when we had the technology to be able to detect the boundaries of the formation so that we knew exactly where to position the wellbore geologically,” she said.
The latest advancements from Schlumberger are now in downhole geosteering and mapping.
“It helps operators save costs by ensuring that they are in the best part of the reservoir while drilling, maximizing the reservoir exposure,” Wibowo said. “The technology helps the operator to improve the production and the ability to see deeper and then map the multiple layers they don’t see. They are basically placing the well in the best part of the reservoir. All of this is basically reducing the costs and also the risk of the well.”
Rami Yassine, senior vice president of the Drilling and Evaluation Division at Halliburton Co., explained that improved reservoir mapping has coincided with increased reservoir complexity, particularly in international basins. In response, Halliburton has advanced its LWD platforms to offer a better understanding of reservoirs, which improves geosteering and ultimately increasing pay.
Yassine related that an operator in the North Sea recently ran Halliburton’s latest line of LWD technologies and saw significant cost savings through identifying more hydrocarbons in the reservoir.
“They drilled the well, and then post-job, they ran a 3-D reservoir map,” he said. “In that reservoir mapping they were able to identify an additional 400 feet of net pay, so that operator decided to go back in and sidetrack the well that we were on. During that sidetrack, they decided to do it while operating the 3-D reservoir mapping in real time. And while they were doing that, they identified an additional 500 feet of net pay. So that ultimately reduced the overall cost per barrel for that operator just through a sidetrack of a well, and they recovered an additional 900 feet of net pay.”
Yassine said that deep reservoir mapping was something that historically was very limited, but as the technology has improved, so has the understanding of the reservoir.

“The value that our customers are seeing is understanding the true boundaries of their reservoir and allowing them to adjust their reservoir models accordingly,” he said. “Historically, imaging of the reservoir was limited to a few feet from the wellbore. Now, we’re able to see close to 300 feet. So it has allowed our customers to better understand their reservoir. In addition, it has allowed more efficient geosteering across the reservoir for accurate well placement to maximize the production. And that has ultimately improved the amount of recoverable reserves the operators can have.”
Drilling advances
Few stages of the well life cycle have seen more technological advancements in recent years than drilling. With improved geosteering, MWD and LWD applications and fully autonomous drilling rigs, the time it takes to drill miles-long horizontal wells has gone from weeks to days.
“Operators are extremely aware that new technology will come at a price, but it will only be applied and adopted if it’s going to achieve the targets of lowering the overall cost of completing sections and drilling wells,” said Hesham Darwish, Schlumberger product champion of casing drilling and reamers for well construction. “And we’ve seen over the years how these advances have brought up efficiency and significantly reduced the number of days and times to drill wells.”
Schlumberger’s casing-while-drilling technologies allow operators to simultaneously case the section of the hole while drilling, which helps eliminate downtime during the drilling process.
“So, in the conventional methods you have to drill the hole first, and then wait for it to be cased, you need to do a certain number of steps that includes tripping out of hole,” Darwish said.
“Challenges are faced in the drilling section, which results in high nonproductive time, unplanned costs and delays, and they happen due to the time exposure between drilling the section and casing it,” he said. “Those challenges can happen due to different reasons; could be pressure gradient, unstable formation, losses or gains that happened while drilling, and those issues get even more complicated when we are facing challenging directional profiles which require the right mitigation plan in order to avoid nonproductive time delays and unplanned cost.
“[Casing drilling] provides assurance that every foot drilled is cased and secured. All the down time and the wait time associated with pulling out of the well, conditioning, reaming, casing and running are all eliminated in that case.”
Yassine said that autonomous drilling capabilities have provided more consistency in drilling, more predictability and more reliability. One of Halliburton’s drilling automation tools drives itself downhole without surface interaction, which allows it to use high-frequency measurements downhole to maintain trajectory and deliver the proper wellbore placement.

“Compared to a legacy approach, which was always surface commands and multiple commands to the downhole tools to adjust trajectory as needed, now with that downhole automation, tools have the ability to just run on their own,” Yassine said. “Think about it as a more advanced Tesla; consider it with the downhole intelligence essentially, running the system and having high-frequency sensors. It can really consume a lot of downhole data and adjust at a high frequency because of advancements that we’ve put into electronics and automation.”
Balancing investments vs. costs
As the oil and gas industry has moved to prioritizing free cash flow over a productionat-all-costs mentality, investments in new technology applications are at risk. Profits now are given back to shareholders, and money is being invested in simply maintaining production at single-digit percentage growth from year to year.
“But the role of technology and the importance of continued investments and innovation is paramount to operational success,” Balmer said.
“The technology aspect is the differentiator,” he said. “But it’s an appropriate level of applied technology. It isn’t where you’re trying to come up with correlations that don’t make any sense. And I think where we as an industry are going is having the type of the people that are evaluating technology and then the implementation of that technology. You don’t have to be the first one to have an autonomous drilling operation or a nobody-onsite completions operation. You just want to be able to leverage those technologies when they are proven.”
Recommended Reading
Sabine Oil & Gas to Add 4th Haynesville Rig as Gas Prices Rise
2025-03-19 - Sabine, owned by Japanese firm Osaka Oil & Gas, will add a fourth rig on its East Texas leasehold next month, President and CEO Carl Isaac said.
E&P Highlights: Jan. 27, 2025
2025-01-27 - Here’s a roundup of the latest E&P headlines including new drilling in the eastern Mediterranean and new contracts in Australia.
CNOOC Makes Oil, Gas Discovery in Beibu Gulf Basin
2025-03-06 - CNOOC Ltd. said test results showed the well produces 13.2 MMcf/d and 800 bbl/d.
E&P Highlights: April 7, 2025
2025-04-07 - Here’s a roundup of the latest E&P headlines, from BP’s startup of gas production in Trinidad and Tobago to a report on methane intensity in the Permian Basin.
Hibernia IV Joins Dawson Dean Wildcatting Alongside EOG, SM, Birch
2025-01-30 - Hibernia IV is among a handful of wildcatters—including EOG Resources, SM Energy and Birch Resources—exploring the Dean sandstone near the Dawson-Martin county line, state records show.
Comments
Add new comment
This conversation is moderated according to Hart Energy community rules. Please read the rules before joining the discussion. If you’re experiencing any technical problems, please contact our customer care team.