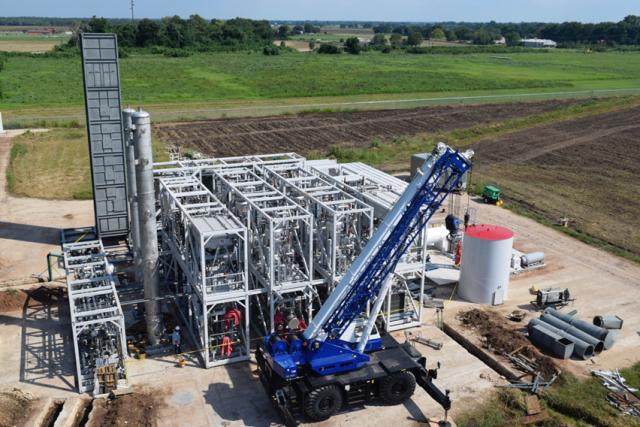
This commercial plant comes in modules that fit easily into standard shipping containers. (Source: INFRA GTL Technology)
Ever-growing demand for hydrocarbon assets takes gas exploration to areas far removed from the market. Almost one-third of known gas reserves are considered to be stranded. For the most part, the reason is economic rather than technological. It costs too much to extract and transport gas to the customers.
Companies are looking for different ways of monetizing such assets. LNG represents one such possible solution. LNG technology does certainly help to bring natural gas to the market. However, the cost of gas liquefaction, transportation and regasification is significant; moreover, this process does not add value to the original product. Irrespective of the shipping distance, the product remains the same, but its cost to the end user is increasing.
Fischer-Tropsch synthesis represents an interesting alternative to such applications. This is a catalytic process that converts synthesis gas (a mixture of carbon monoxide and hydrogen) into synthetic hydrocarbons— crude oil, lubrication oils and synthetic fuels. Fischer- Tropsch synthesis originates back to the 1920s, when German scientists Franz Fischer and Hans Tropsch succeeded in producing hydrocarbons out of coal. Seventeen coal-to-liquid plants were built in Germany before and during World War II. At the time the technology was very expensive and yielded many byproducts.
Since then such companies as Shell and SASOL have improved the technology efficiency and focused on converting natural gas into hydrocarbon products, known as gas to liquids (GTL). The process continues to attract attention primarily because it allows companies to add value to natural gas and produce transportation fuels and motor oils worth much more than the original feedstock. High-quality GTL products contain no sulfur, generate lower emissions and are readily biodegradable.
Having so many advantages, GTL technologies are still plagued by high capital cost and a large footprint, mainly due to the fact that the classical Fischer-Tropsch process produces wax that needs to be sent to hydrocracking and other refining processes.
New catalyst technology
INFRA GTL Technology, an international company based in Houston, came up with a pelletized catalyst where multicomponent catalysts are impregnated by cobalt nano-particles. The catalyst is highly productive and very stable, offering at least two years of useful life without rejuvenation. It is bifunctional; the Fischer-Tropsch reaction is accompanied by cracking and other processes, which allows users to produce liquid light synthetic oil straight from the Fischer-Tropsch reactor without a wax stage and without any byproducts.
INFRA’s GTL technology involves only two stages: oxidation of natural gas to synthesis gas and obtaining clear synthetic crude oil.
Incoming feed gas passes through a series of inlet pretreatment and prereforming vessels. The function of these vessels is to remove sulfur and convert heavy hydrocarbons to methane. Synthesis gas is produced through either steam methane reforming or auto-thermal reforming.
The Fisher-Tropsch block contains two stages. The Fisher-Tropsch reaction is carried out at constant temperature as cooling water is circulated on the shell side to preserve the reaction at isothermal conditions.
The final product—liquid synthetic oil—contains diesel and gasoline fractions only (with a large proportion of jet fuel fraction). It can be easily upgraded into gasoline, diesel or jet fuel. There is no waste or byproducts.
As a result, the capital cost of a GTL plant decreases by at least 50% as compared to similar technologies. Operating costs go down significantly as well. For large-scale plants capex could be as low as $25,000/ bbl of daily installed capacity, and opex would be close to $3/bbl. Consequently, INFRA’s technology makes production of synthetic oil economically feasible, ensuring that the GTL process is profitable as a rule and cost-competitive with oil refining. Also, the elimination of hydrocracking and upgrading stages allows operators to reduce the plant footprint and to manufacture compact, modular and easily transportable GTL units.
Excess energy is recovered and used to generate enough electricity for the entire GTL plant. Fischer- Tropsch water, produced as part of the synthesis of hydrocarbons, is clean enough to be put back into the process. Thus, plants built with INFRA’s technology are self-sufficient in utilities.
Stranded and remote gas fields can benefit from such self-sufficient, low-cost, compact and modular design. With the help of this GTL technology, high value-added products—synthetic oil or liquid motor fuels—can be produced onsite and brought to the market using the existing oil infrastructure (pipelines, tankers or railways).
INFRA’s technology has been tested in full-cycle pilot plants that have been operated since 2010. By year-end 2016 INFRA plans to start up its demonstration plant in Wharton, Texas.
This first-of-its-kind commercial 100-bbl/d plant is built in pre-engineered standardized easily deployed modules in the dimensions of standard shipping containers. The whole plant fits into 14 skids that have been fully equipped in the assembly shop and delivered to the site ready for the installation and startup.
The compact design-intensified steam-methane reformer fits two modules. The reformer comprises a box-type radiant furnace and convection section. The reformer is capable of producing 2.5 tons of synthesis gas per hour. A prereformer can be provided for heavier hydrocarbons. Fixed-bed tubular reactors filled with proprietary catalyst are designed inside two modules and carry out a two-stage process Fischer-Tropsch synthesis. Gas cleaning, sulfur removal, synthesis gas conditioning and auxiliary equipment also are included.
The advanced design enables fast installation, startup and commissioning, dramatically reducing construction costs and allowing clients to turn their plant over to production quickly.
INFRA’s technology is easily scalable and offers very good economies of scale, which will help to improve the economics of remote gas field development significantly. To the extent that the technology can be applied to eliminating gas flaring, it also can reduce the environmental impact of oil and gas industry developments.
Recommended Reading
Expand Energy Picked to Join S&P 500
2025-03-10 - Gas pureplay Expand Energy will be elevated on March 24 from its position in the S&P MidCap 400 index.
Ovintiv Names Terri King as Independent Board Member
2025-01-28 - Ovintiv Inc. has named former ConocoPhillips Chief Commercial Officer Terri King as a new independent member of its board of directors effective Jan. 31.
Elliott Nominates 7 Directors for Phillips 66 Board in Big Push for Restructuring
2025-03-04 - Elliott Investment Management, which has taken a $2.5 billion stake in Phillips 66, said the nominated directors will bolster accountability and improve oversight of Phillips’ management initiatives.
Liberty Energy Appoints Arjun Murti to Board
2025-01-23 - Arjun Murti has over 30 years of experience as an equity research advisor.
Magnolia’s Board Adds Ropp as Independent Director
2025-01-07 - Alongside his experience in oil and gas operations, R. Lewis Ropp has a background in finance, capital markets and investment management, Magnolia Oil & Gas said.
Comments
Add new comment
This conversation is moderated according to Hart Energy community rules. Please read the rules before joining the discussion. If you’re experiencing any technical problems, please contact our customer care team.