
(Source: Hart Energy)
This year’s Meritorious Engineering Awards for Innovation (MEAs) recognize 18 technologies for engineering excellence in the upstream energy industry.
Hart Energy’s MEA program highlights new products and technologies demonstrating innovations in concept, design and application.
An expert panel of judges included engineers and scientists from operating and consulting companies worldwide. Judges were excluded from categories in which they or their companies have a business interest.
Artificial Lift
Saudi Aramco and Lex Submersible Pump
Product: Ultra-High-Speed High-Gas-Volume-Fraction Pump (UHS HGVFP)
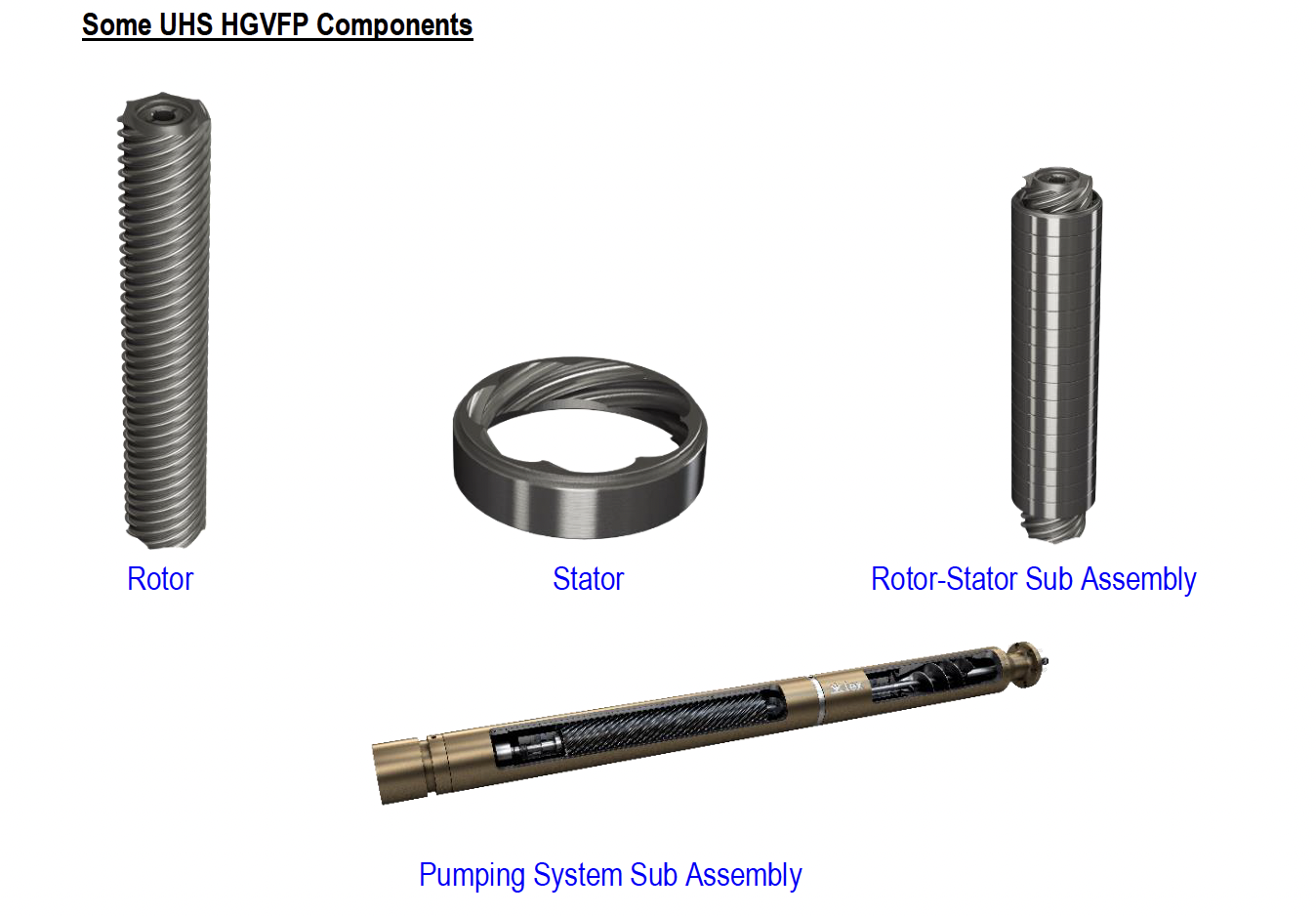
Saudi Aramco and Lex Submersible Pump teamed to create the technology with the lengthy name but effective performance, the Ultra-High-Speed High-Gas-Volume-Fraction Pump (UHS HGVFP).
The innovative pump is touted as a solution for gas-volume fractions (GVF) of up to 90% at the pump intake, enabling a wider production operating range for gas handling in the field. This is critical because higher free gas volumes otherwise reduce oil production from downhole to the surface, also leading to deferred production, motor overheating, excessive vibrations, eventual equipment failure and higher workover expenses.
The conventional multiphase pumps can only handle up to 75% GVF. The UHS HGVFP raises that percentage substantially.
The main pump components are the rotor and stator. The blades on the rotor outer diameter and stator internal diameter are helically shaped. The thread shapes are designed to increase hydraulic efficiency. During operation, gas and liquids are thoroughly mixed to prevent gas-liquid separation that can lead to gas lock in pumps. Axial flow through the pump components contributes to significantly higher gas-handling capability.
Another feature of the UHS HGVFP is its high tolerance to sand. This is facilitated by the larger minimum clearance between the rotor and stator.
Other pump features include incorporating a heat-exchanger system for effective cooling of the downhole motor. This ensures the motor does not overheat and operates at suitable temperatures as the system handles a largely gaseous mixture, which has a relatively low specific heat capacity.
The high-speed operation of the system yields a very compact system with a total length of about 55 ft.
Carbon Management
Caterpillar Oil & Gas
Product: Cat Hybrid Energy Storage Solution
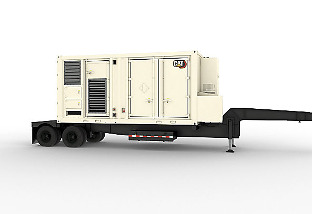
Caterpillar’s new Cat Hybrid Energy Storage Solution allows drillers and operators to use gas as a main fuel source to reduce diesel spend while enabling lower emissions and a lower total cost of ownership (TCO).
This technology suite provides a comprehensive and fully integrated solution that optimizes energy storage, gensets, a bi-directional power inverter and a microgrid master controller to deliver a solution that meets the performance demands of the oilfield while supporting emissions reduction. In a hybrid system that combines the Hybrid Energy Storage Solution and a gas genset, the transient response is even quicker than in conventional, diesel-only rigs.
The technology is versatile and easily integrates with current rig setups, accommodating multiple genset options to provide an optimized power solution. Retrofitting existing equipment can help future-proof assets as new energy sources become available, further enhancing TCO. By leveraging the capability of the fully autonomous gas-hybrid system, which includes the latest genset controls, operators and drillers can access reliable and uninterrupted power, boost fuel economy, reduce engine maintenance and decrease emissions.
This hybrid solution increases uptime and capital efficiency as well, ensuring exceptional performance in the field that provides the flexibility to run on a wide variety of fuel types and withstand the oilfield’s harsh operating conditions. Depending upon site configuration, the technology suite is proven to deliver up to 30% fuel cost savings with natural gas, 85% fuel cost savings with field gas, and up to 81% reduction in nitrogen oxides, according to Caterpillar.
Digital Oil Field
Expro
Product: Centri-Fi Consolidated Controls Solution
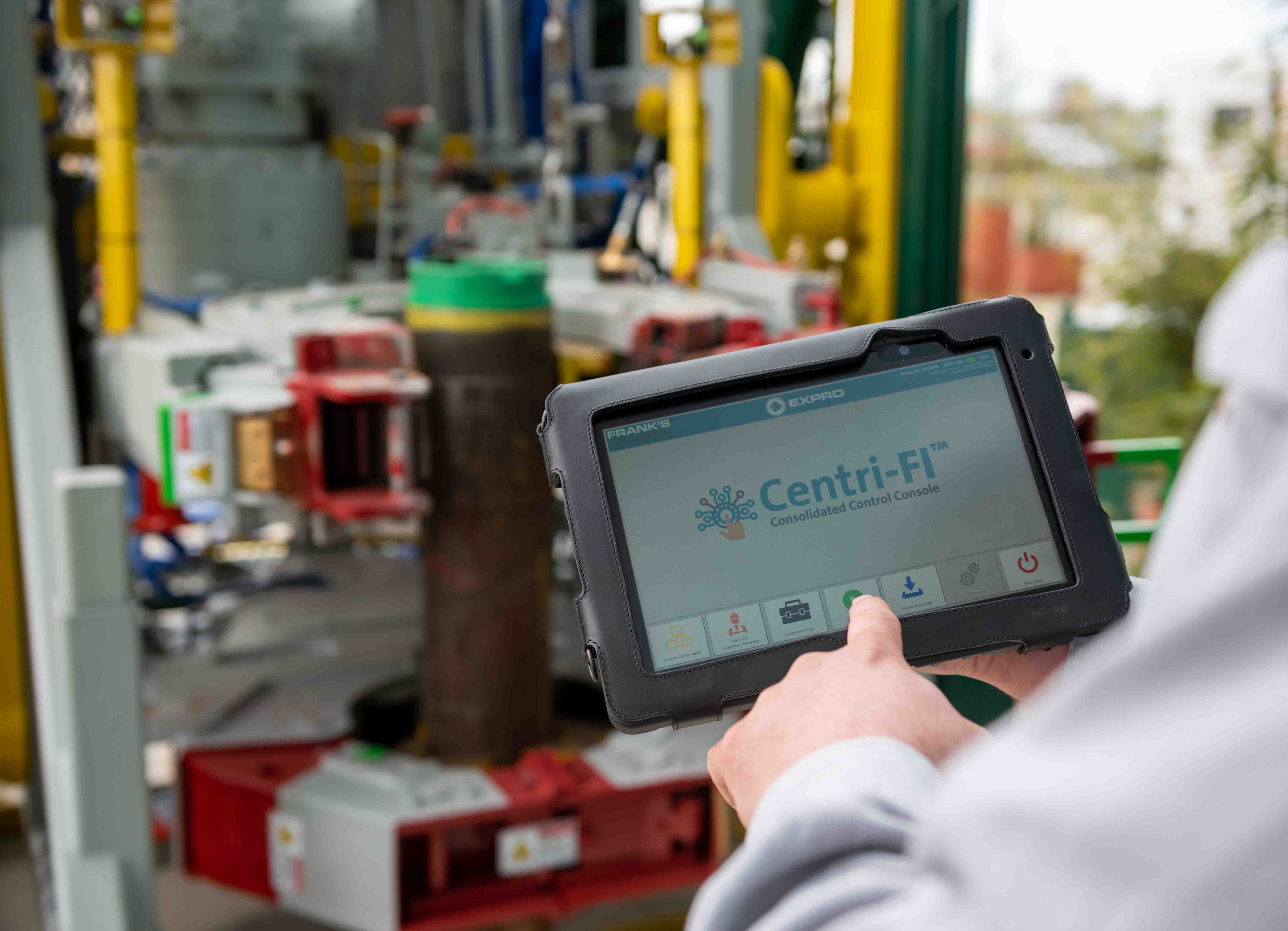
Technological advancements in digitalization, automation and enhanced safety procedures are significantly impacting the petroleum industry for execution, industry adoption and asset management. Segments such as drilling, well intervention and production are already experiencing massive efficiency gains and reduced operational costs from increased safety and digital transformation processes.
Expro’s Centri-FI system is an intelligent, digital command and control solution that facilitates tong make-up, handling tools such as elevators and slips operation, completions tool handling, and cement head make-up operations to be precisely controlled and managed via a wireless control tablet. These operations are performed by a single operator, instead of three or four rig personnel.
The Centri-Fi solution is a modular system, allowing multiple, non-harmonized equipment to be integrated and operationally synchronized so that multiple tubulars running operations and pertinent tools in casing and completions operations can be executed. The system can also monitor operational key performance indicators for analyzing operational efficiency and time-capturing for operational expenditure savings.
The technology has validated the full capability of giving control directly to the driller via the driller chair rig integration module, where the driller directs the tubular running operations. This reduces the need for service personnel, thus reducing related operational costs with communication transparency. Centri-FI successfully captures tubular running value drivers through remotely operated tablet operations, resulting in reduced personnel cost and hazard mitigation by enhancing rig floor safety which leads to improved returns on assets and technology innovation.
The overall process is optimized through data analytics and visualization by applying machine learning (ML) and artificial intelligence (AI) methodology. The end goal and proof of added value with the Centri-FI solution is to provide means of a fully automated and autonomous tubular running process that serves as a gatekeeper for multi-party rig equipment and software service providers with the highest level of operational reliability and integrity.
Drill Bits
SLB
Product: AccuStrike Short-Makeup Drill Bit
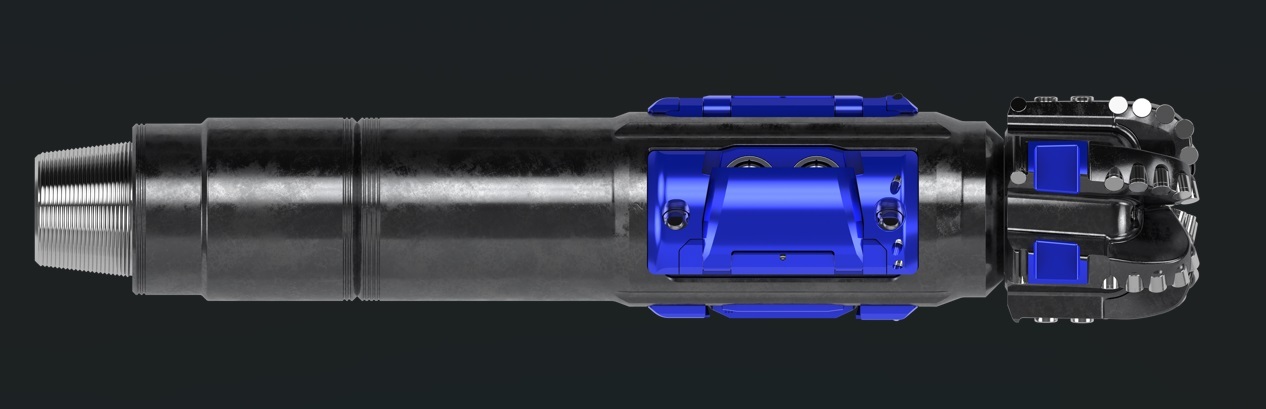
The AccuStrike Short-Makeup Drill Bit improves directional drilling performance. The future of oilfield well drilling incorporates the capabilities of the rotary steerable system (RSS) on a digital platform. For this to be successful, the RSS bottomhole assembly (BHA) must drill the entire planned section and deliver an accurate actual versus planned trajectory. This minimizes the time spent on each well and, subsequently, the well’s carbon footprint.
SLB field engineers described the technical need to disrupt directional results. RSS BHAs call for PDC drill bits, which minimize the distance from the cutting structure to the deflection pads. By minimizing the makeup length (MUL) of PDC bits, SLB can achieve more challenging well profiles while maximizing dogleg capabilities and mitigating tool-damaging shock and vibration. To minimize the length of the PDC drill bit, SLB created a one-piece body design incorporating all aspects of the application. SLB engineering, research and manufacturing experts modified the in-house drill-bit manufacturing process to offer drill bits in steel to face any drilling challenges. The SLB drill-bit cutting structure design optimizes MUL, stability and durability to drive the directional drilling performance of SLB’s PowerDrive Orbit G2 RSS.
Manufacturing and sustaining teams combined expertise and modified the machinery and bit body design with the desired quality. By creating novel fixtures and finite element analysis (FEA) studies, they enabled the breakthrough from the traditional two-piece (bit head and upper section) structure and joining weld. The unique placement of the breaker slot prevents damage to the bit body physical structure and increases operational safety. The process to create the one-piece bit solution initiated with the change to the traditional two-piece drill bit structure and in-depth materials properties, developing the AccuStrike Short-Makeup Drill Bit with efficiency, high quality, and tight tolerance.
Drilling Fluids/Stimulation
Halliburton
Product: BaraHib Trackable Inhibitive System
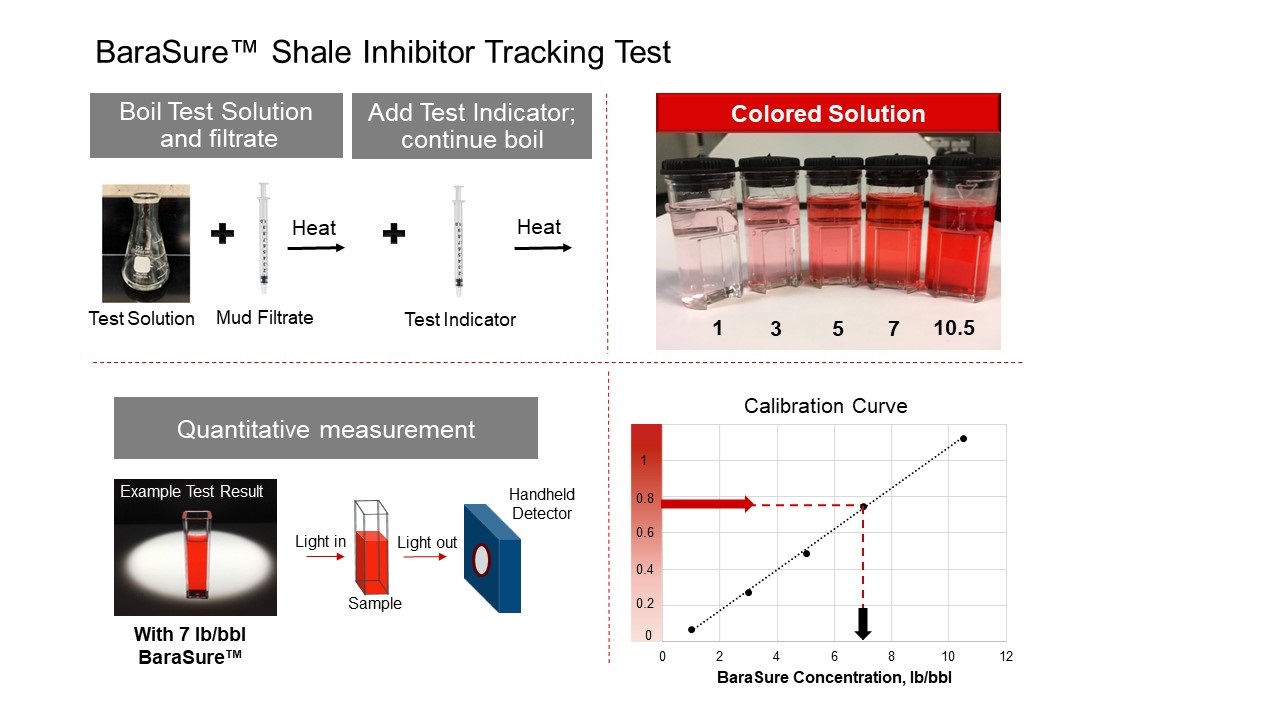
In environmentally sensitive areas, high-performance water base fluids (HPWBF) are suitable alternatives to non-aqueous drilling fluids (NAF). HPWBF rely on shale inhibitors—amine inhibitors and polymeric encapsulators—to achieve drilling fluids performance similar to NAF. Traditionally amine inhibitors have been tracked through mass balance calculations. These inhibitors can deplete faster than indicated by calculations during drilling operations. This can lead to issues such as wellbore instability, stuck pipe incidents, non-productive time, loss of reservoir access and increased well costs for operators.
Halliburton Baroid created the BaraHib Trackable Inhibitive System (TIS) as an HPWBF solution that uses advanced inhibitive chemistry that can be quantitatively measured continuously at the rig site. This unique capability helps operators improve operational reliability and reduce environmental impact, maximizing asset value. In addition, BaraHib TIS provides excellent wellbore stability in various types of clay mineralogy, improved lubricity and maximum hole cleaning in highly deviated and long-lateral wellbore sections. The inhibition framework can be customized to avoid shale swelling, prevent cuttings dispersion through shale encapsulation, and reduce bit-balling tendencies with anti-accretion coating.
Formations that contain hydratable shale or mixed layers of reactive clay can lead to wellbore instability issues. The BaraHib TIS tracks shale inhibitor concentration through quantitative measurements instead of the volumetric tracking approach commonly used in the industry. This tracking method accurately measures amine-based inhibitors. As a result, operators can achieve effective shale inhibition improving wellbore stability, maximizing drilling efficiency, and enhancing control over the wellbore.
The BaraHib TIS is engineered to suppress reactive clay hydration, allowing operators to drill longer hole sections and eliminate the need to back ream due to clay swelling. Shear thinning behavior enhances hydraulic horsepower and improves hole cleaning and suspension, maximizing the rate of penetration.
Drilling Systems
Ulterra (Patterson-UTI)
Product: Mitigator
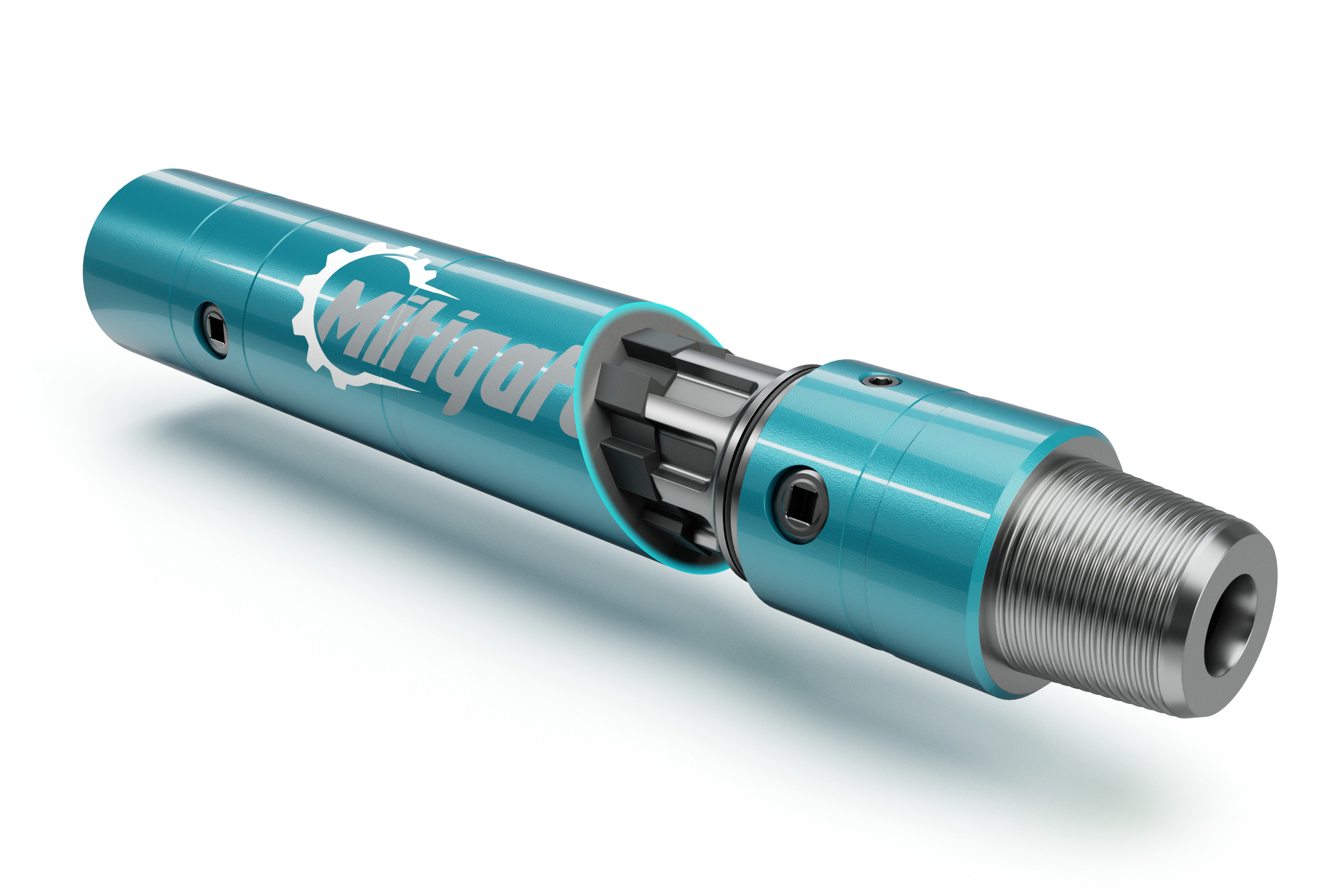
Ulterra’s Mitigator tool addresses a newly identified type of harmful vibration, known as high-frequency torsional oscillation, or HFTO, which is broadly recognized as the root cause of persistent and severe downhole tool failures in the industry. HFTO originates from the interaction between different BHA components, presenting as a harmonic dysfunction characterized by high energy and low amplitude. Ulterra’s engineers recognized this as an opportunity to design a robust, yet simple, short-length solution that would dampen and interrupt HFTO, rivaling longer, more complicated mechanical tools. The novel construction of the tool is focused on durability, and it leverages material science instead of part count to achieve its goals.
The tool is comprised of two primary sections, which are connected by friction plates. The tool is designed around transmission of rotating drive forces through castellations between the two sections, which provide a small degree of angular variance to occur. The tool is injected with Vylon, a proprietary, high-temperature elastomer, to achieve the constant damping effect. The Vylon material is completely isolated from the drilling fluid and particulates to prevent degradation while it disrupts the high-speed vibrations found in HFTO dysfunction.
The Mitigator tool is touted as featuring multiple competitive advantages versus other HFTO-reducing alternatives. The biggest advantage is that the Mitigator tool is short in length, around 3 ft or 1 meter, which is comparable to the length of a standard crossover sub. This offers broad versatility in positioning and utilization, allowing it to be used in various BHA designs and in different parts of the drill string. Secondly, the construction of the Mitigator tool is highly robust, with no real moving mechanical parts and a low overall part count. This reduces possible points of failure and maximizes reliability. Lastly, the Mitigator tool includes provisions for integrating a pair of drilling dynamics sensors, positioned above and below the tool mechanism. This placement quantifies the shock reduction and provides valuable insight into the downhole dynamic environment.
During field testing, the Mitigator tool reduced and dampened harmonic frequencies, qualified by the data collection and condition of BHA components post-run, according to Ulterra. Specifically, costly electronic packages in MWD and LWD tools experienced less frequent failure and therefore increased the mean-time-between-failure in many applications. It was also discovered that this damping and disrupting effect was felt both above and below the tool, proving that it reduced harmonic dysfunction. As the BHA’s overall dysfunctional energy levels decreased, measurements indicated that it also decreased other harmful vibration forms, including stick-slip and lateral vibration. Overall, the Mitigator tool is a low-impact, versatile and reliable solution to a very complex HFTO problem.
Exploration/Geoscience
Halliburton
Product: Agile Field Management
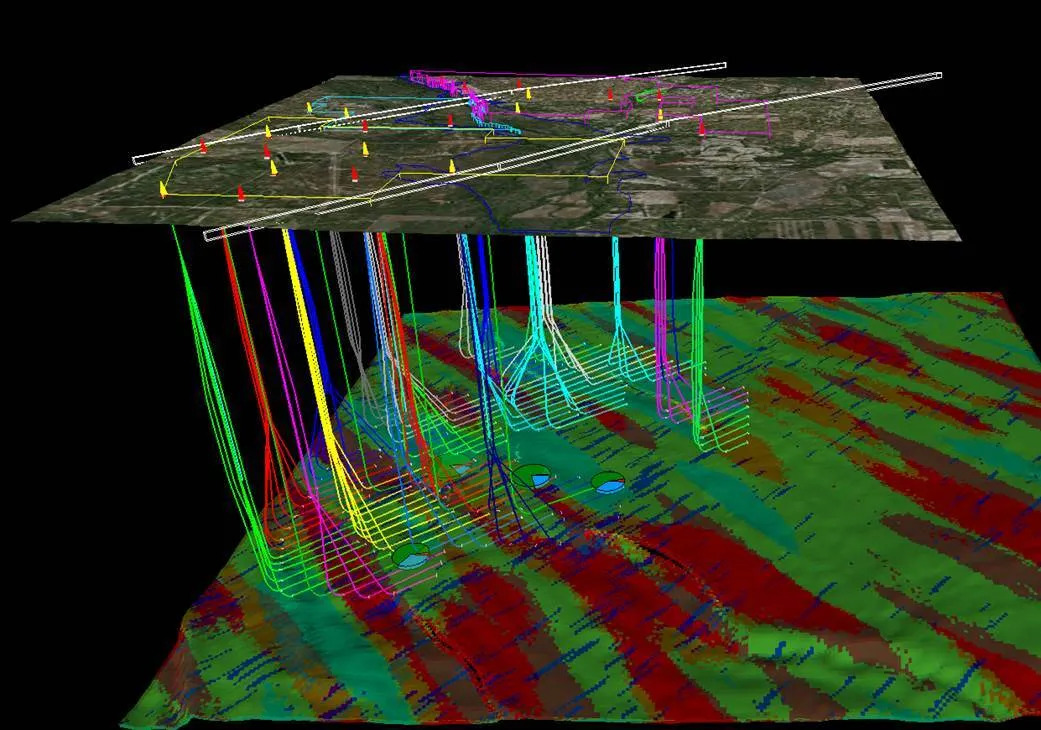
Halliburton Landmark’s Agile Field Management solution facilitates cross-functional insights and a broader decision-making perspective. Asset management teams can leverage multiple teams’ expertise and data-driven insights, enabling a more comprehensive understanding of the business landscape and better-informed decision-making.
Today, oil and gas investment decisions are made based on technical, operational, geopolitical, environmental and financial analyses of the field, and they involve finding a balance between these entities. This requires close collaboration across multiple departments and vendors. This manual field development process can lead to siloed workflows, questionable data management, untraceable decision trails and inaccurate project status.
Agile Field Management, a DecisionSpace 365 solution, solves this key problem by integrating multi-domain data, expertise and automated workflows into an efficient, auditable and unified decision-making environment. The solution enables the creation and visualization of a holistic digital twin that allows domain experts within an asset team to seamlessly work together and evaluate a range of field development configurations. Within the software environment, the project team can collaborate to build field development alternative concepts that the software characterized using an automated system of data-driven key performance indicators that measure parameters such as emissions, risk, economics and technical complexity. By leveraging an innovative mesh architecture to decentralize the ownership of data and decisions, the solution makes data available to everyone at any time across departments.
This enables companies to maintain a standardized, single-reference system to access real-time project insights anytime, anywhere. The solution can quickly test numerous scenarios and hypotheses with an integrated evaluation approach to deliver optimized drainage strategies, production flows and strategic infill well placements for faster and more accurate project delivery and maximized reservoir production. These capabilities help multidisciplinary teams to collaborate and compare the most optimal plan to achieve a common economic goal and fast-track execution using a big-picture view of the asset.
Floating Systems and Rigs
PTS (Production Technology and Services)
Product: Multi-Hull Vessel Design
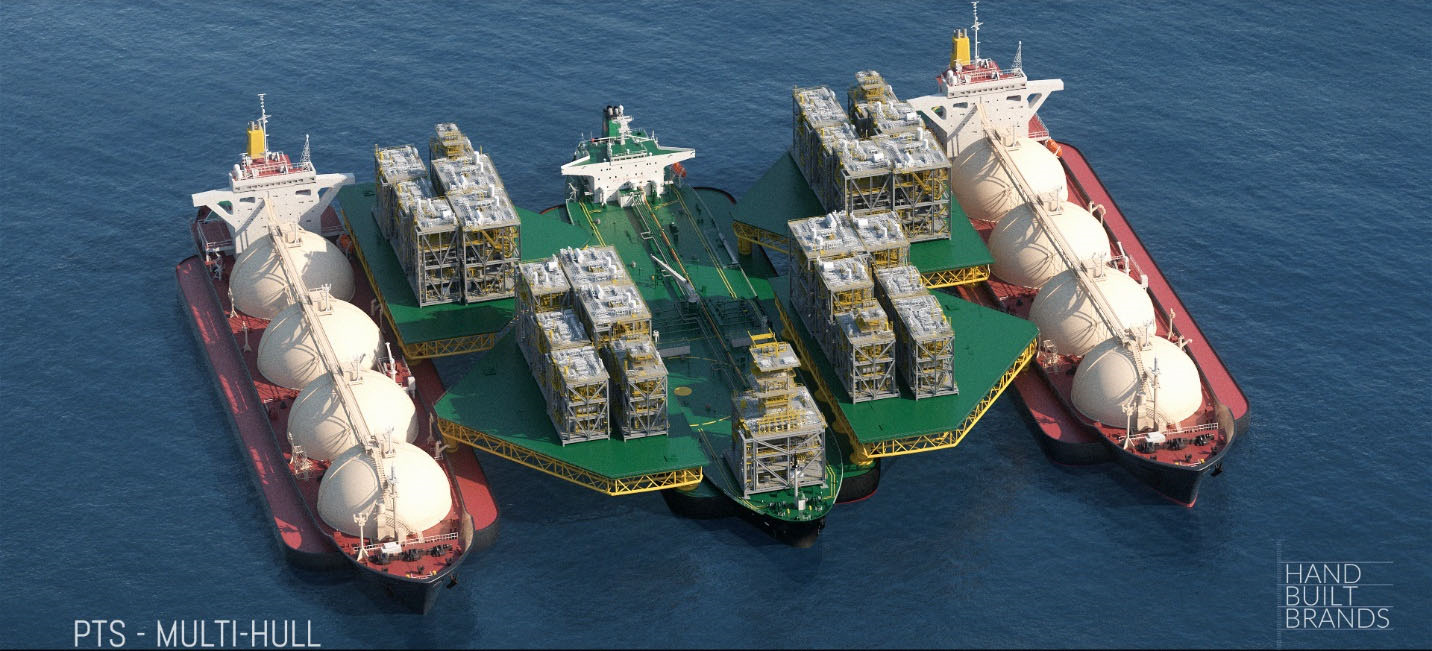
The patented Multi-Hull utilizes articulated connections to join two or more tankers, with the resulting vessel servicing endless possibilities, including FPSOs and FLNG. This novel application of industry-proven connection technology more simply and affordably decouples motions between the hulls and platforms/topsides. The design also expands vessel-configuration possibilities, allowing for more efficient operations and increased liquid storage volume.
The Multi-Hull design for FPSO/FLNG is up to a 30% lower cost to design, build, construct, install and commission than a conventional mono-hull FPSO/FLNG. Because the platforms used on the Multi-Hull design typically have fewer levels than what is normally seen on an FPSO/FLNG, the yard fabrication is much faster, requiring fewer materials and reducing costs. Because the center of gravity is lower, the Multi-Hull design has enhanced stability compared to a mono-hull design, resulting in less penalty on the liquid storage volume.
The Multi-Hull design can result in safer operations due to the expanded equipment layout, which creates less confined equipment and work areas, more space for ventilation and better personnel egress in case of an emergency.
Formation Evaluation
Cordax Evaluation Technologies
Product: LWT-GEN3 Formation Density
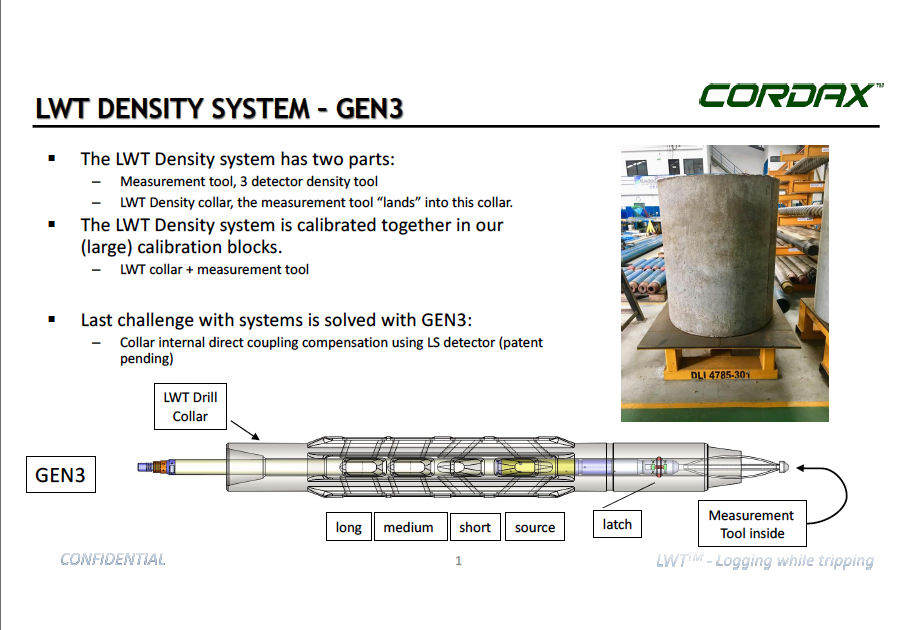
Cordax Evaluation Technologies touts its revolution of the formation evaluation (FE) industry with the deployment of its logging-while-tripping (LWT) technology. LWT is a commercially proven patented FE technique in which industry-quality, open-hole logs are acquired in memory immediately after drilling has been completed, while the drilling assembly is being tripped to surface.
The measurements are made efficiently during tripping, with virtually no risk of losing tools or getting stuck in the hole, thereby minimizing the use of expensive rig time. The inside drill-pipe conveyed LWT formation evaluation process has fewer inherent risks than wireline conveyance, thru-the-bit or logging-while-drilling (LWD) methods. These industry-recognized applications incur greater rig-time and significantly increase lost-in-hole (LIH) risk as tools must be exposed to the open-hole environment to acquire the data.
Currently, the measurement portfolio of LWT is formation resistivity, formation density, neutron porosity, gamma ray and spectral gamma ray. For the last 20 years or more, formation density open-hole measurements have been recorded by using a pad type device. The detectors and source are placed in the pad surface, the pad is pressed against the borehole wall and the formation electron density is measured and converted into formation density. Traditionally, this pad type measurement device is lowered into the well using wireline. With the wells becoming highly deviated and horizontal, the industry placed the detectors and source on the outside of an inline-drilling stabilizer and emulated a drilling pad type device called LWD tools. The measurement challenge with the LWD tools is sensor-wellbore contact (pad contact) and depth control.
Cordax developed its LWT-GEN3 Formation Density measurement system consisting of an LWT-GEN3 Drill Collar and three-detector measurement tool. The LWT-GEN3 Drill Collar is placed in the normal drilling BHA and is full-bore and has no electronic or nuclear sources while drilling. When the well is drilled and stable, the three-detector measurement tool is pumped from surface to the LWT-GEN3 Drill Collar and latches in place. When the drill pipe is tripped to surface, the formation density is measured and recorded in memory. At surface, the time-based memory data is merged with depth and a depth-based formation density data is ready for delivery.
HSE
Extract (NOV)
Product: Mechanical Shaft Lock (MSL)
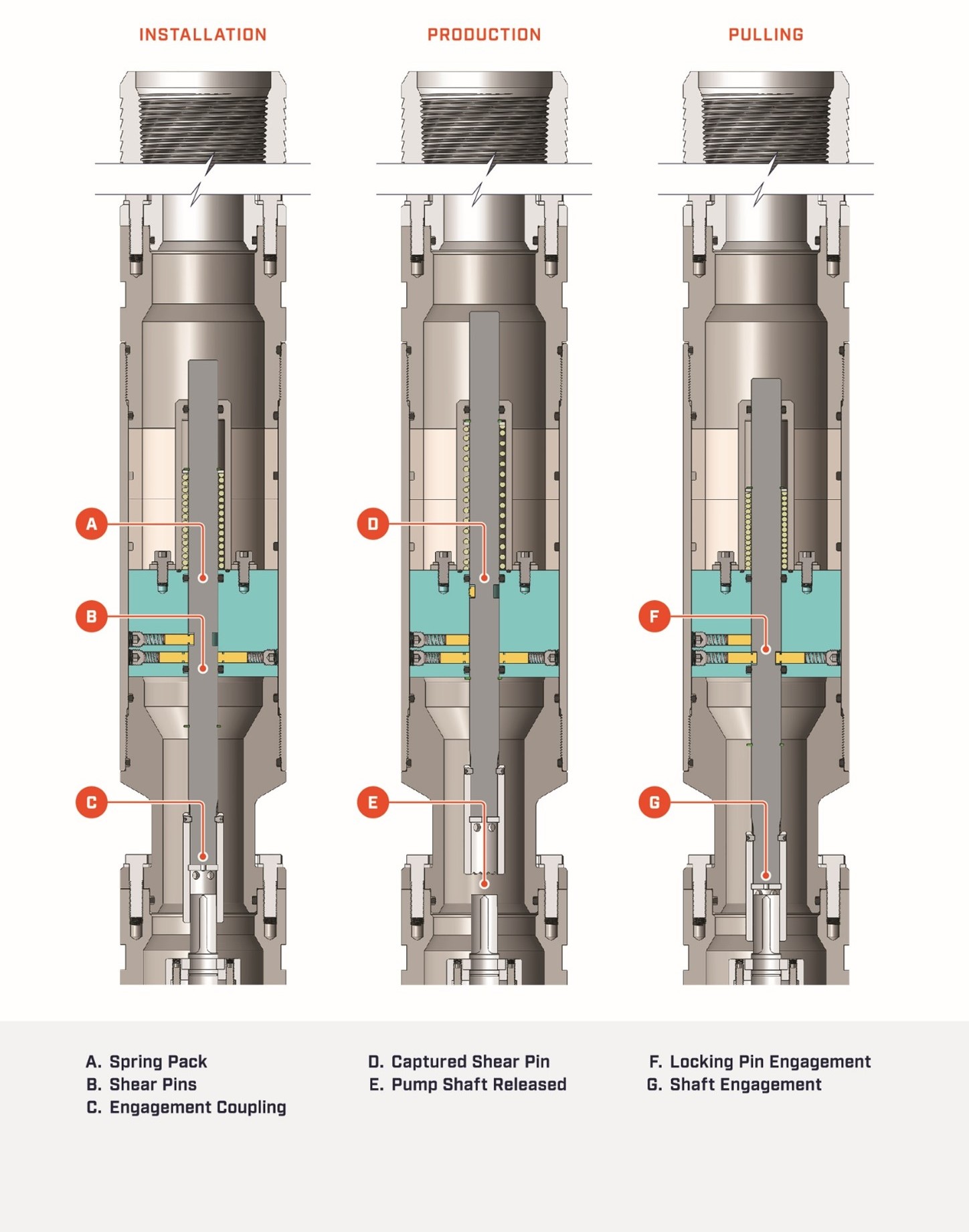
The introduction of the Mechanical Shaft Lock (MSL) for permanent magnet motors (PMM) in oil and gas production represents a potentially game-changing advancement in safety and efficiency. This innovative method aims to address the significant safety risks associated with PMMs, particularly the potential generation of lethal voltages when the shaft rotates, making it a critical development for the industry.
The MSL functions as a fail-safe mechanism to prevent voltage generation during the installation and pulling of electric submersible pump (ESP) strings powered by PMMs. By physically securing the shaft with shear pins, the MSL prevents rotation due to downhole pressures, ensuring the safety of field technicians. Importantly, the MSL is designed to be automatically unlocked by the motor’s force during normal operations, providing a seamless transition to production mode. Compared to existing safety procedures, such as shunting and tubing blocking, the MSL offers a more reliable and effective solution, eliminating the potential for unplanned rotation and voltage generation. Field testing of the MSL has demonstrated its effectiveness, with successful shearing and reset of the safety pins during installation and pulling processes, confirming its functionality as a fail-safe method. Furthermore, the MSL’s deployment across multiple wells with various oil and gas operators has demonstrated the MSL’s efficacy in ensuring safety and preventing hazardous conditions. Its implementation not only enhances safety, but also streamlines operations by eliminating the need for secondary services to remove tubing blocks.
The MSL is intended as a significant leap forward in safety and innovation, positioning the industry at the forefront of safe PMM operations. Its development reflects a collaborative, people-first culture, fostering an environment that prioritizes safety and innovation. The MSL aims to revolutionize safety procedures for PMMs, offering a simple, secure and effective solution to prevent hazardous voltage generation, ultimately ensuring a safer working environment for all involved. The solution addresses critical safety concerns associated with PMMs, and aims to establish a new standard for safe and efficient PMM operations.
Hydraulic Fracturing/Pressure Pumping
Lonestar Completion Tools
Product: LONEstart Toe Valve

After setting and cementing the lateral in an unconventional well, injection must be established. There are several methods and products that can be used to establish injection and allow the ability to circulate tool strings into the well. One of the more common methods is through the use of a toe valve, which is a sliding sleeve type of tool that is located in the shoe track of the lateral. Toe valves serve two primary purposes: they allow the operator to conduct a regulation-required casing test and they open to allow circulation into the formation.
Standard toe valves use rupture disks as the primary method for activation. These rupture disks act as a barrier between wellbore pressures and an atmospheric chamber. Upon reaching the desired casing pressure, the rupture disk bursts and floods the atmospheric chamber with wellbore fluid and pressure. This pressure then acts over a piston and forces it to open. Generally, there are secondary shear devices located in the piston to prevent premature opening if there is a leak in a seal or rupture disk. Premature opening can lead to catastrophic issues during the cementing job. These shear devices must be accurately installed based on the wellbore conditions (hydrostatic, temperature, desired opening pressure). Additionally, seal integrity of the toe valve (specifically of the atmospheric chamber) are critical to the overall success of the tool installation and activation.
Generally, there are three reasons why toe valves fail. The typical failure mode is either the toe valve becomes unable to open or opens prematurely. Seal leakage can lead to premature flooding of the atmospheric chamber. This typically happens on the high-pressure dynamic seals on the ID of the valve. An inadequate cement wipe job may leave cement or cement stringers present in the shoe track and toe valve. And problems can arise from incorrect setup or assembly in the field, i.e., rupture disk selection and/or appropriate number of shear devices.
The LONEstart toe valve was designed to mitigate some of the typical issues encountered with toe valves. The unique design allows the valve to be assembled from only three pieces of material. Most standard toe valves have at least four pieces (top sub, housing, sleeve and bottom sub). The LONEstart’s integral top sub/piston design eliminates the need for external shear devices as well as 50% of the high-pressure dynamic ID seals found on most standard toe valves. This is achieved by leaving a small shear plane that connects the piston to the top sub. Lastly, the smooth bore ID and optimized piston design generate much higher opening forces than most standard toe valves, ensuring opening even if there is cement residue present in the shoe track.
IOR/EOR/Remediation
Locus Bio-Energy
Product: AcidBoost
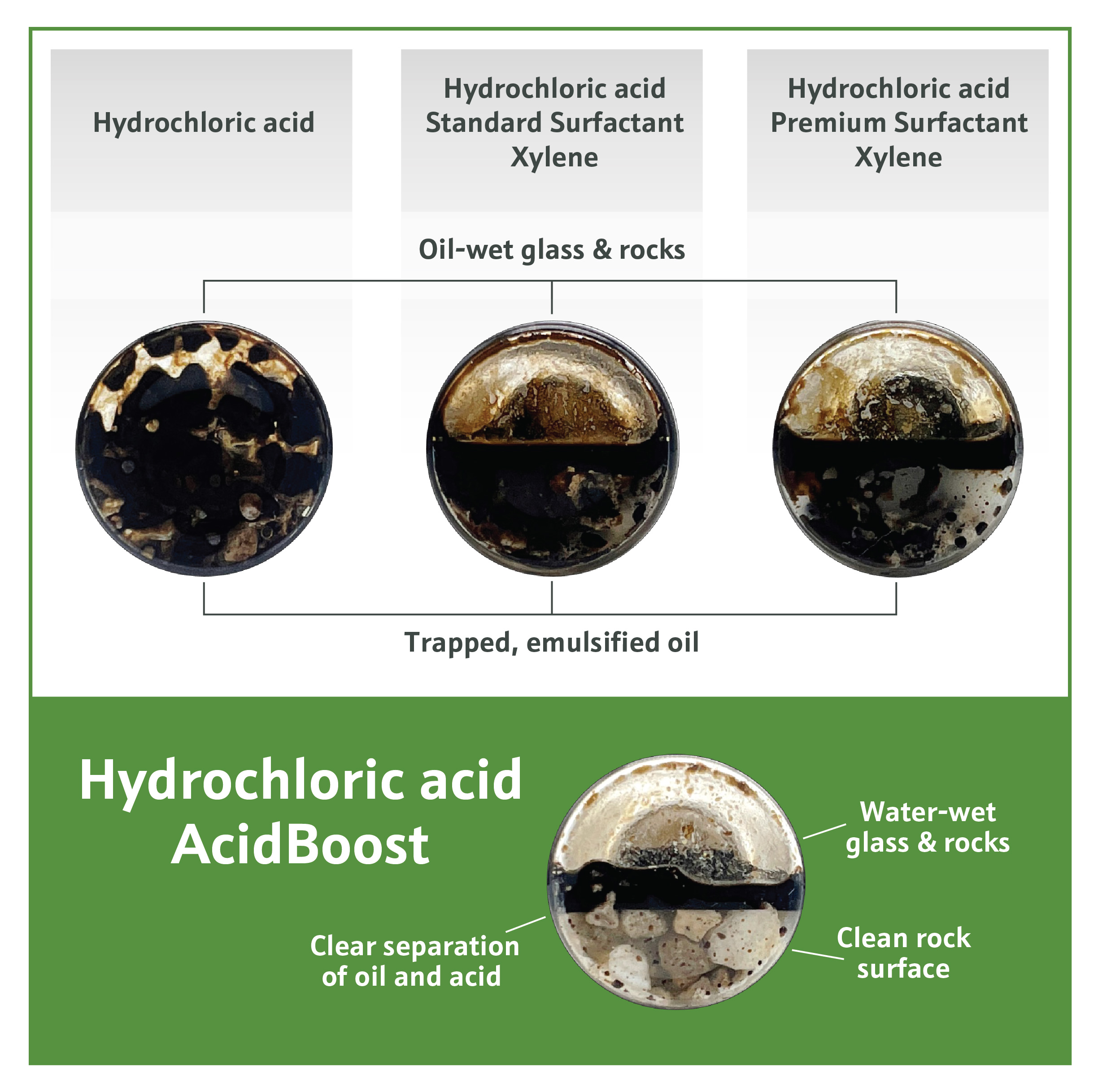
Utilizing wellbore remediation with acid-based fluid systems is essential for removing carbonate scales, controlling iron deposition and eliminating formation damage to restore production rates. Traditional remediation processes include multiple ancillary additives that complicate transportation, handling and job execution, which increase HSE risks.
AcidBoost is a biosurfactant-based microemulsion designed to simultaneously simplify and improve acid remediation by enabling operators to use a single-acid additive, significantly enhancing performance compared to traditional multi-stage solvent packages. Laboratory testing on oil-saturated carbonate samples validated the superior efficacy of AcidBoost over conventional acid-remediation additives, according to Locus Bio-Energy.
These tests revealed that an acid-only solution left oil trapped between the rocks, creating an oil-wet environment and emulsified hydrochloric acid (HCl). Adding 8% xylene to the HCl solution resulted in slight improvements in oil removal, but the surfaces remained oil-wet and the liquid emulsified. However, substituting xylene with a lower, more effective dosage of AcidBoost (3%) led to remarkable results, according to Locus Bio-Energy. AcidBoost efficiently stripped oil from all surfaces and between rock samples, creating a distinct separation between the oil and the acid solution, enhancing the acid’s reactivity with the carbonate, and leaving the surfaces water-wet, positioning AcidBoost as a BTEX-fee alternative to xylene. Consistent results were observed when AcidBoost was compared to micellar surfactants, other industry-standard acid-compatible microemulsions, and combinations of surfactant with xylene in similar tests. These laboratory tests suggest that, in practical applications, AcidBoost can lead to improved acid efficiency and increased oil production with the elimination of additional surfactant, solvent and anti-sludge agents. The robust detergency power of the biosurfactant technology in AcidBoost ensures more efficient oil removal from reservoir rocks, optimizing the surface for acidizing.
Locus Bio-Energy touts AcidBoost as a revolutionary product that leverages biosurfactant technology to streamline wellbore remediation. It simplifies the process by combining the functions of multiple chemicals and multiple stages into a single, efficient application. This not only reduces operational complexity but also minimizes HSE risks associated with handling and pumping large volumes of solvents and other additives. The technology’s performance in laboratory tests suggests significant potential for improving acid treatment efficiency and oil production in real-world applications. AcidBoost’s ability to create a water-wet state and prevent emulsification enhances acid reactivity and penetration, offering a more effective remediation solution.
Machine Learning and AI
Nabors Industries and Corva
Product: Predictive Drilling
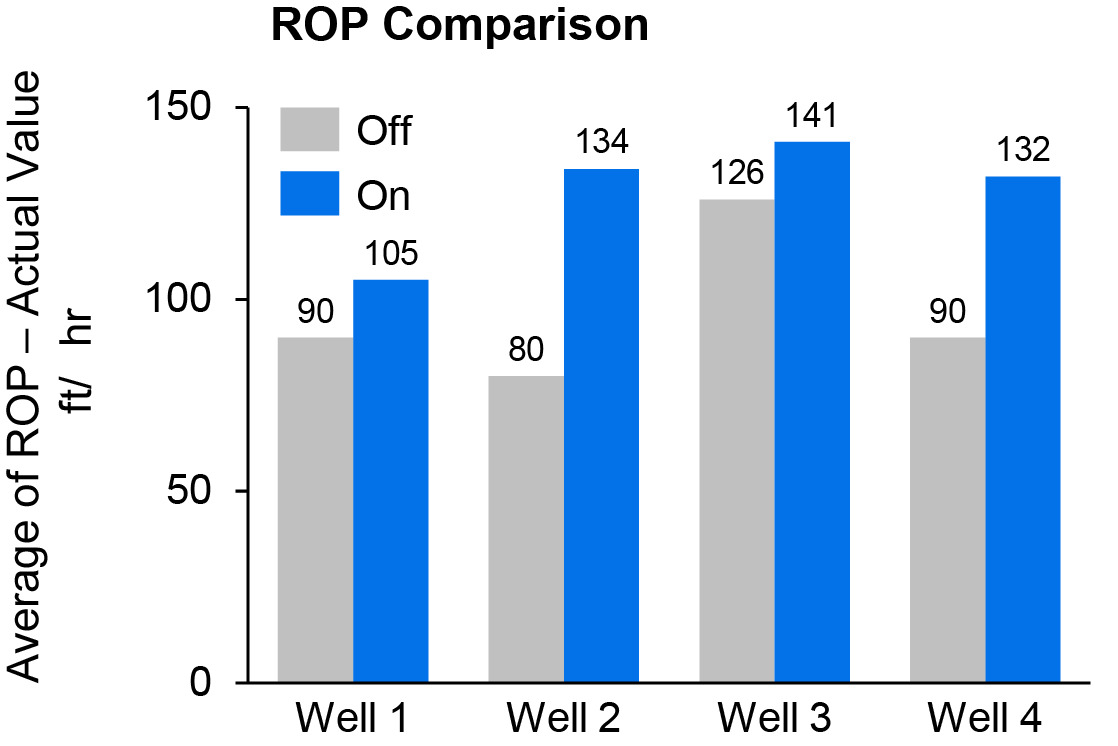
Nabors Industries and Corva made waves in the drilling automation and AI/ML worlds with the announcement of their strategic collaboration. By connecting Corva’s industry-leading Predictive Drilling application to Nabors’ universal rig controls and automation platform—SmartROS—the duo promoted a whole new level of intelligence and performance to “smart” drilling rigs. Not just to Nabors rigs, but to any drilling contractor.
Joining one of the world’s largest drilling contractors with the leading energy software-as-a-service (SaaS) providers creates a transformative opportunity for closed-loop drilling automation. The initial focus is to deliver the lowest cost per foot drilled by employing an ML-based rate-of-penetration (ROP) optimizer while reducing dysfunctions. Named “Predictive Drilling”—this optimizer enables remote control of rig site auto driller setpoints through a seamless cloud-to-cloud connection, without the need for any additional rig upgrades. The ROP optimizer was developed by Corva, and Nabors developed an application programming interface (API) to receive control setpoints (ROP, WOB, Differential Pressure, RPM) from the optimizer. These setpoints are synchronized between Cloud and Edge, then to the human-machine interface (HMI), ensuring reliable connection via a heartbeat mechanism.
An enhanced auto driller system was deployed to improve setpoint control. While drilling the lateral section of a well, the closed-loop automation can save drillers about 5,000 manual interactions with the HMI to change set points. In recent deployments, Predictive Drilling automation technology performance has surpassed that of manual drilling practices with standard auto-drillers. At 70% or more utilization of Predictive Drilling, operators achieve a 15-20% improvement in on-bottom ROP, reduced shock and vibration and completed the lateral section in a single bit run, according to Nabors.
Another key impact to the industry is the capability for remote changes. Traditionally, most digital deployments happen at the edge, which requires field personnel going to the rig to operate the software. Another advantage of cloud deployment is a faster upgrade pace with new versions being continuously developed and deployed during operations without the need for additional human presence at the rig. Both capabilities combined significantly minimize the need for onsite intervention, reducing driller fatigue and allowing them to focus on other critical tasks for ensuring safe drilling operations.
Marine Construction and Decommissioning
Baker Hughes
Product: Agnostic Tooling
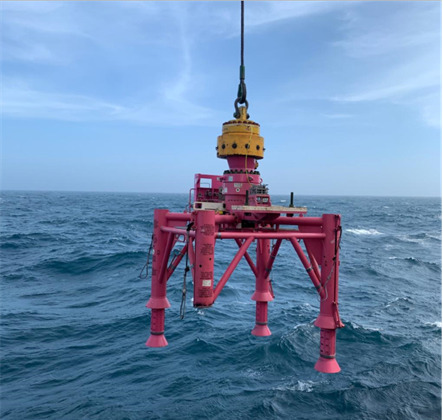
Agnostic Tooling is an innovative methodology used to maximize tools adaptability reducing risk exposure and cost with an attractive lead time. It assesses essential functionality and uses commonality between tools to simplify and improve design and, thereby, reduce tooling needs. Its success can be highlighted by past project accomplishments and lessons learned. A key challenge within life-of-field operations is securing tooling sets across different well types from various original equipment manufacturers (OEM), a timely and costly process.
Despite the different OEMs, there are common mating features for tooling to interface with. Baker Hughes' “Swiss Army Knife” of agnostic tools targets an operator’s total requirement with the minimum number of tools needed. This innovative approach to tooling uses a modular design, whereby tooling can be adapted to multiple well types and the functionality targeted to specific operational requirements. This methodology reduces the quantity of tools required, improves capability and lowers emissions. By design, the agnostic tools are not limited by the original OEM specifications as they can be simplified and modularized resulting in an efficient and economically beneficial process.
For example, one area of simplification is to use standardized guiding and landing of the intervention tooling on the subsea equipment. In addition, given the operational challenges when planning offshore campaigns on multiple wells, working with just one supplier of the intervention tooling package allows for more flexibility in case of required reprioritizations or rescheduling.
One key area of success for this approach is in support of decommissioning, which will hit an average of $15 billion, peak in 2035, and is the subject of increasing regulation to comply with end-of-life plug-and-abandonment. The novelty in agnostic tooling is the modular approach to tooling from different OEMs’ subsea equipment, reducing the total number of tools needed via tooling standardization and, therefore, the overall campaign cost with a single point of contact. In discussions with operators, there is a real benefit to standardization in tools across well sets to reduce the amount of tooling required to perform field operations and subsequently maintenance requirements, simplify the design acceptance process, and to minimize interface equipment with common top and bottom connections.
Non-fracturing Completions
Halliburton
Product: Dual-Trip Intelligent Completion with the Auris Integrity Checker system and the Fuzion-TJ control-line-equipped telescoping travel joint
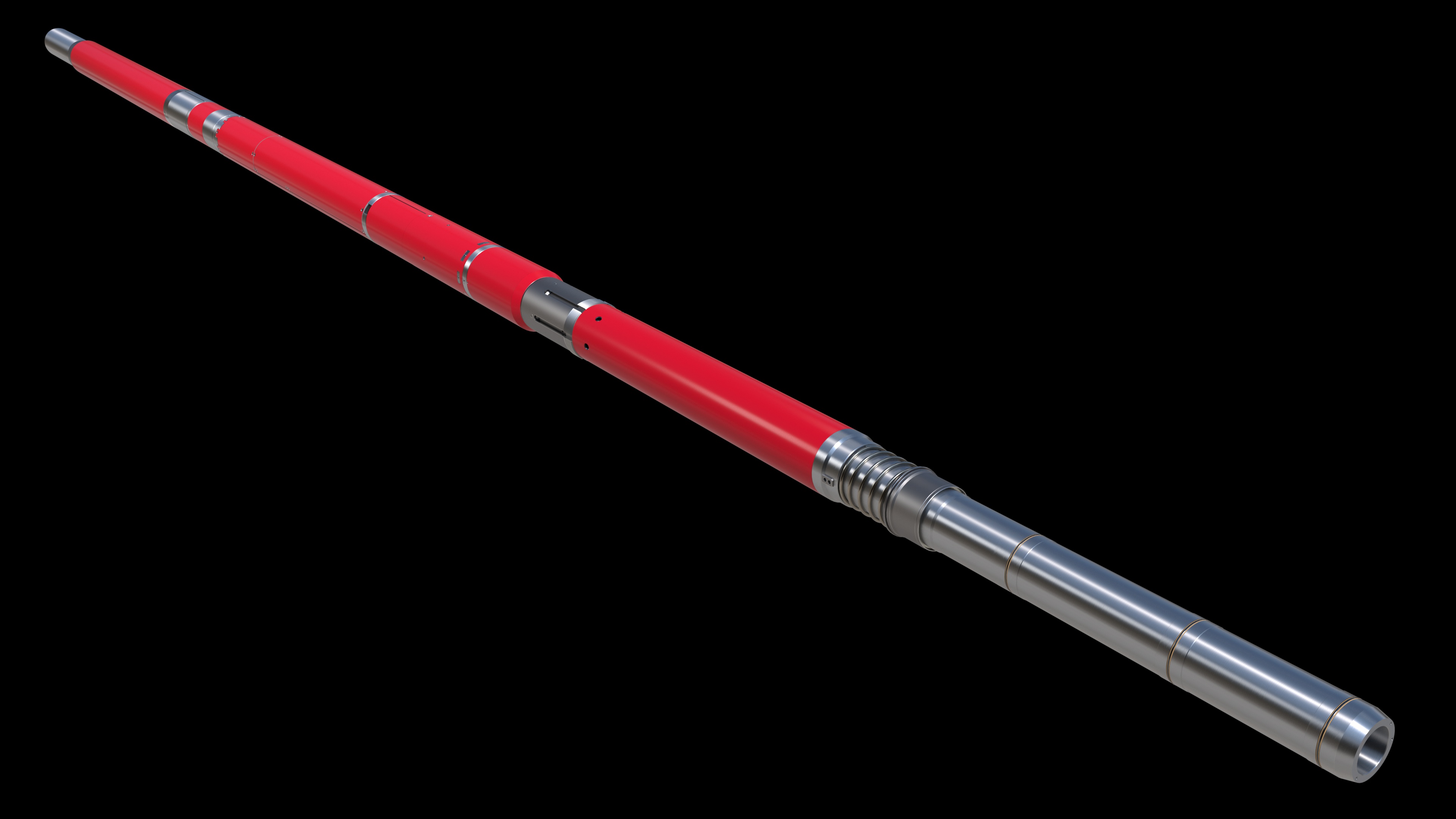
Since the first SmartWell system installations in the late 1990s, downhole wet-mate technology has evolved to allow operators to run dual-trip completions in deeper and/or higher incline wells, as the upper and lower completions can now be run separately. Two-trip completions offer many benefits, such as the capability to perform workover operations early in well life or in system remediation later. Dual-trip systems allow retrieval of faulty devices for maintenance disconnected from the SmartWell system and allow it to be left intact with no requirement to release or cut production packers.
One option allows SmartWell system deployment using drillpipe and an interface to the lower receptacle. This configuration permits quick SmartWell system deployment because no control lines are run along the drillpipe, which reduces time necessary for clamp installation. This is beneficial in fluid-loss situations and reaching depth quickly can reduce fluid use. Dual trips are viable options in wells where the SmartWell system must be run on heavyweight drillpipe. A key challenge with drillpipe deployment is that the upper string is isolated from hydraulic and electric lines. So, if a control line is damaged in a restricted well entry point, or has sustained damage in an openhole section, the operator is unaware until the drillpipe is disconnected and returned to surface and the upper completion with the control lines is reconnected to the lower system. In deep water, this could mean several days of rig time and non-productive time attributed to retrieval of the upper and lower completions to replace the damaged control line or entire lower completion.
Halliburton has developed two key technologies that enable dual-trip SmartWell completions for deepwater subsea wells: the Auris Integrity Checker system and Fuzion-TJ control-line-equipped telescoping travel joint. The Auris system offers acoustic verification via an interface to the lower completion that allows remote system integrity confirmation using a bidirectional signal from the surface via drillpipe. The acoustic telemetry uses the field-proven Dynalink telemetry system backbone. Once the acoustic signal arrives near real time to the downhole module, the system pressure tests control lines to confirm no leaks in the hydraulic system. It can also read the entire string of permanent downhole gauges to confirm no electrical system damage has occurred. Thus, the Auris Integrity Checker system helps operators de-risk dual-trip completions before the next stage of deployment.
The Fuzion-TJ travel joint is run on the second trip when the upper Fuzion-EH receptacle is mated to the lower receptacle to connect the upper completion and lower SmartWell completion. The Fuzion-TJ travel joint offers 7.25 in. hydraulic lines and 1.25 in. electric lines or TEC with the capability once pressure released to stroke up to 20 ft. The integrated control-line coils allow hydraulic and electrical bypass downhole, and the keyed mandrel design allows torque application along the full stroke of the travel joint. Dual-trip SmartWell completions would not be possible without the Fuzion-TJ travel joint in deepwater subsea wells where flexible space out is necessary.
Onshore Rigs
Canrig Drilling Technology (Nabors)
Product: Sigma Top Drive
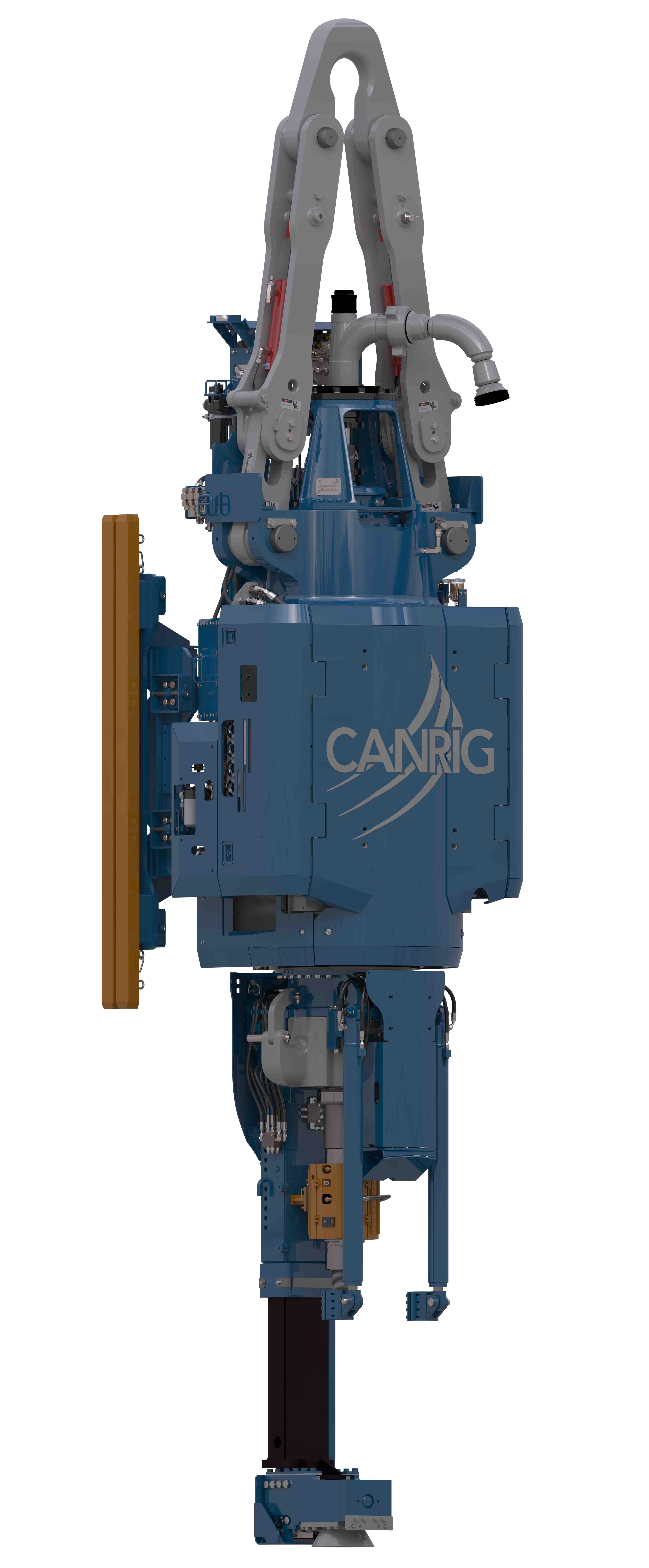
The pursuit of longer lateral wells has emerged as a megatrend in drilling, especially within the U.S., where the expectation is to drill more than 4-mile laterals. This shift has propelled the demand for top drives equipped with unparalleled torque and horsepower capabilities, paving the way for Canrig’s Sigma Top Drive. Canrig has been delivering best-in-class top drives for over 40 years, but recently commercialized the Sigma Top Drive. With a focus on increasing reliability and torque capacity, Sigma aims to revolutionize drilling and maximize output and efficiency, while maintaining safety standards.
With automation and performance being huge drivers in today’s operations, Canrig developed the Sigma Top Drive. This next-generation top drive is completely reimagined to endure the harshest drilling conditions while operating with the highest continuous torque in its class, able to drill 75,000 ft-lbs and support super-long laterals. Sigma provides more power, performance and torque density than ever before, enabling greater automation and remote-control capabilities—both at the surface and downhole. The Sigma, currently equipped with Nabors smart suite of software, offers seamless integration and automatic control. This empowers the driller with more consistent and precise control over both directional and horizontal drilling operations. The top drive also features advanced technology and preventative maintenance capabilities that monitor machine health, usage and diagnostics, ensuring increased reliability and a significant reduction in the overall cost of ownership.
With 30% fewer parts than a traditional top drive, its compact design allows for deeper setback and racking capacity and safer operations. Along with its liquid-cooled motor, the Canrig Sigma Top Drive has no condensation or overheating, reducing failures and noise pollution. It is also supported by Nabors’ Rigline 24/7 team, which provides customers with an expert at their disposal, whether in the field, at a remote operating center or at the office.
Subsea Systems
Mocean Energy and Verlume
Product: Renewables for Subsea Power—Blue X and Halo
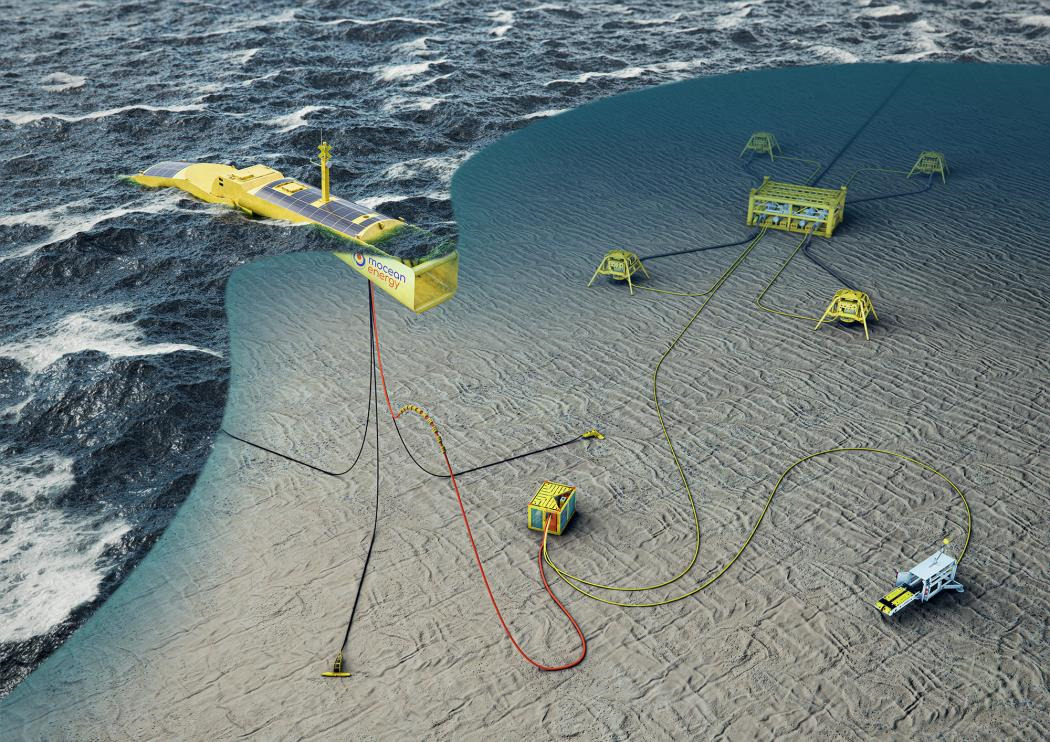
Renewables for Subsea Power (RSP) is a first-of-its-kind joint industry project bringing together Scotland’s expertise in oil and gas operations, ocean energy and subsea energy storage to advance the decarbonization of offshore activities through innovation.
Deployed 3 miles off the east coast of Orkney, Scotland, in February 2023, the 10-kilowatt (kW) Blue X ocean energy converter—built by Mocean Energy—was connected without any cables back to shore to a 150-kW-hour Halo underwater battery developed by intelligent energy management specialists, Verlume. This $2.5 million, 13-month program demonstrated how green technologies can provide reliable low-carbon power and communications to subsea equipment in offshore microgrids, removing the need for expensive subsea cables, which are carbon intensive with long lead times.
Reliable, renewable ocean power was supplied to subsea electronics modules provided by Baker Hughes, and a resident autonomous underwater vehicle garage provided by Transmark Subsea. In addition, the project participants also included Harbour Energy, Serica Energy, Shell, TotalEnergies and PTTEP, each of whom invested in and were closely involved in the program. There also was significant public sector support from the Net Zero Technology Centre, the European Marine Energy Centre (EMEC) and Wave Energy Scotland.
The RSP project addresses a huge industry challenge—providing reliable, clean power and communications to remote locations at sea in applications such as carbon capture and storage and decommissioning. The technology is ready to be deployed commercially, with projects in the North Sea and elsewhere expected in the next two years. Paving the way in the energy transition, the RSP project demonstrates a renewable solution available now to facilitate larger-scale offshore renewable decarbonization projects, and to contribute toward operator and industrywide net-zero targets.
Water Management
Saudi Aramco
Product: World’s First Produced Water Management Project for Extreme Salinity Unconventional Frac Flow-Back Produced Water
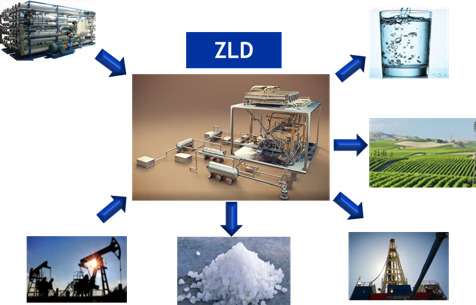
Zero Liquid Discharge (ZLD) produced water management technology desalinates field-produced water by transforming its ionic properties and delivering a high-value end product. The solution features a custom-designed pretreatment system to remove residual hydrocarbons/hydrogen sulfide (H2S) and a dynamic vapor compression (DyVaR) unit for salt removal from hypersaline oilfield produced water.
The pretreatment system relies on a chemical scavenger to lower the dissolved toxic H2S from produced water, while induced-gas floatation utilizing nitrogen gas was used to remove dispersed hydrocarbons. The pretreated produced water is then processed in a DyVaR unit to effectively remove salts from produced water. The DyVaR system, equipped with novel “cyclones,” accomplishes water evaporation at a mild temperature of about 80-90 C. The water vapor is then condensed to generate high-quality, low-salinity water. The reject brine is continuously recycled to mix with feed-pretreated produced water to achieve up to 70%-80% water recovery. The concentrated salts obtained from ZLD technology can be either processed further for mineral recovery, or directly used to formulate high-density drilling fluids and lost circulation material (LCM) slurries, which achieves zero-waste discharge into the environment to truly demonstrate a 100% circular economy.
ZLD produced water management solution is a great example of the kind of sustainable innovation that the industry must develop, deploy and adopt going forward. It allows water produced as a byproduct of the hydrocarbon extraction process to be treated and recycled for different applications including waterflooding, IOR/EOR, unconventional gas fracking and crude oil desalting. Aramco touts ZLD as a win-win technology—a win for the environment by minimizing produced water/wastewater disposal volumes and conserving groundwater/injection water, and a win for oil and gas recovery due to the reuse of treated produced water for injection into the reservoir and hydraulic fracking. ZLD treated water also can be used as a valuable water resource for irrigation to indirectly lower-carbon emissions into the environment. ZLD water also serves as excellent quality water resource to generate green hydrogen to promote the energy transition within the oil and gas industry, according to Aramco.
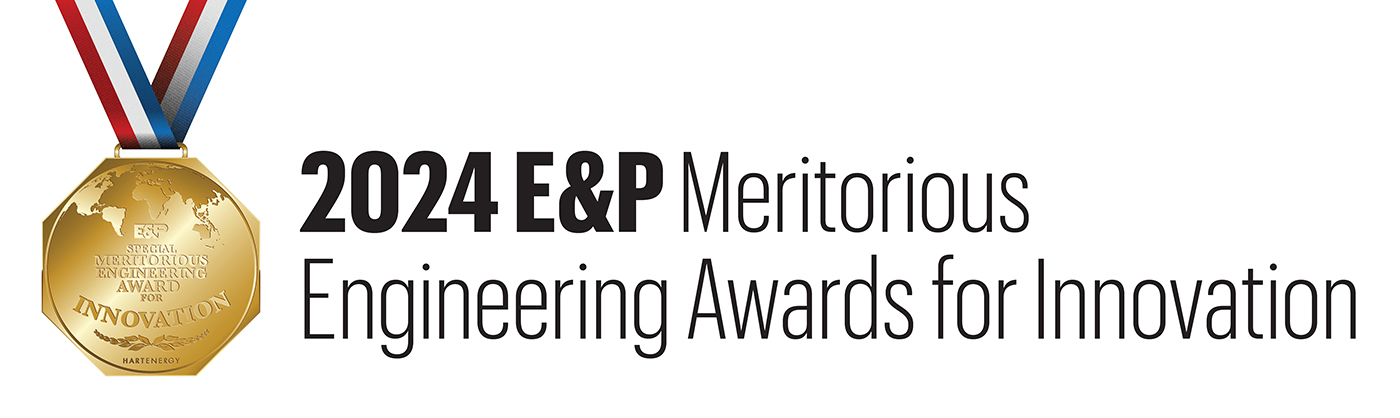
Recommended Reading
Utica Oil’s Infinity IPO Values its Play at $48,000 per Boe/d
2025-01-30 - Private-equity-backed Infinity Natural Resources’ IPO pricing on Jan. 30 gives a first look into market valuation for Ohio’s new tight-oil Utica play. Public trading is to begin the morning of Jan. 31.
Utica Liftoff: Infinity Natural Resources’ Shares Jump 10% in IPO
2025-01-31 - Infinity Natural Resources CEO Zack Arnold told Hart Energy the newly IPO’ed company will stick with Ohio oil, Marcellus Shale gas.
CPP Wants to Invest Another $12.5B into Oil, Gas
2025-03-26 - The Canada Pension Plan’s CPP Investments is looking for more oil and gas stories—in addition to renewable and other energies.
Riverstone’s Leuschen Plans to IPO Methane-Mitigation-Focused SPAC
2025-01-21 - The SPAC will be Riverstone Holdings co-founder David Leuschen’s eighth, following the Permian Basin’s Centennial Resources, the Anadarko’s Alta Mesa Holdings and the Montney’s Hammerhead Resources.
Utica Oil Player Ascent Resources ‘Considering’ an IPO
2025-03-07 - The 12-year-old privately held E&P Ascent Resources produced 2.2 Bcfe/d in the fourth quarter, including 14% liquids from the liquids-rich eastern Ohio Utica.
Comments
Add new comment
This conversation is moderated according to Hart Energy community rules. Please read the rules before joining the discussion. If you’re experiencing any technical problems, please contact our customer care team.