Almost like tree roots, laterals in unconventional plays have spread farther and farther since the shale revolution began, weaving their way across multiple basins. As drilling and completions technologies have gradually improved, so has the industry’s ability to do more with less—constantly lengthening those laterals to reach more production zones with fewer wells.
Drilling longer laterals has an obvious upside, but the process comes with some challenges that are both technological and economic.
Evaluating the third mile’s output
The most basic question about adding a third mile to laterals in unconventionals is whether there is enough incremental production to justify the expense of going the extra mile.
Ryan Hill, principal analyst at Enverus, told E&P the potential payback must evaluate the productivity of a well and the ultimate forecasted recovery of the well per lateral foot drilled. The decision hinges on whether the extra mile not only produces significantly more, but that production per foot is at least close to that of a nearby 2-mile well.
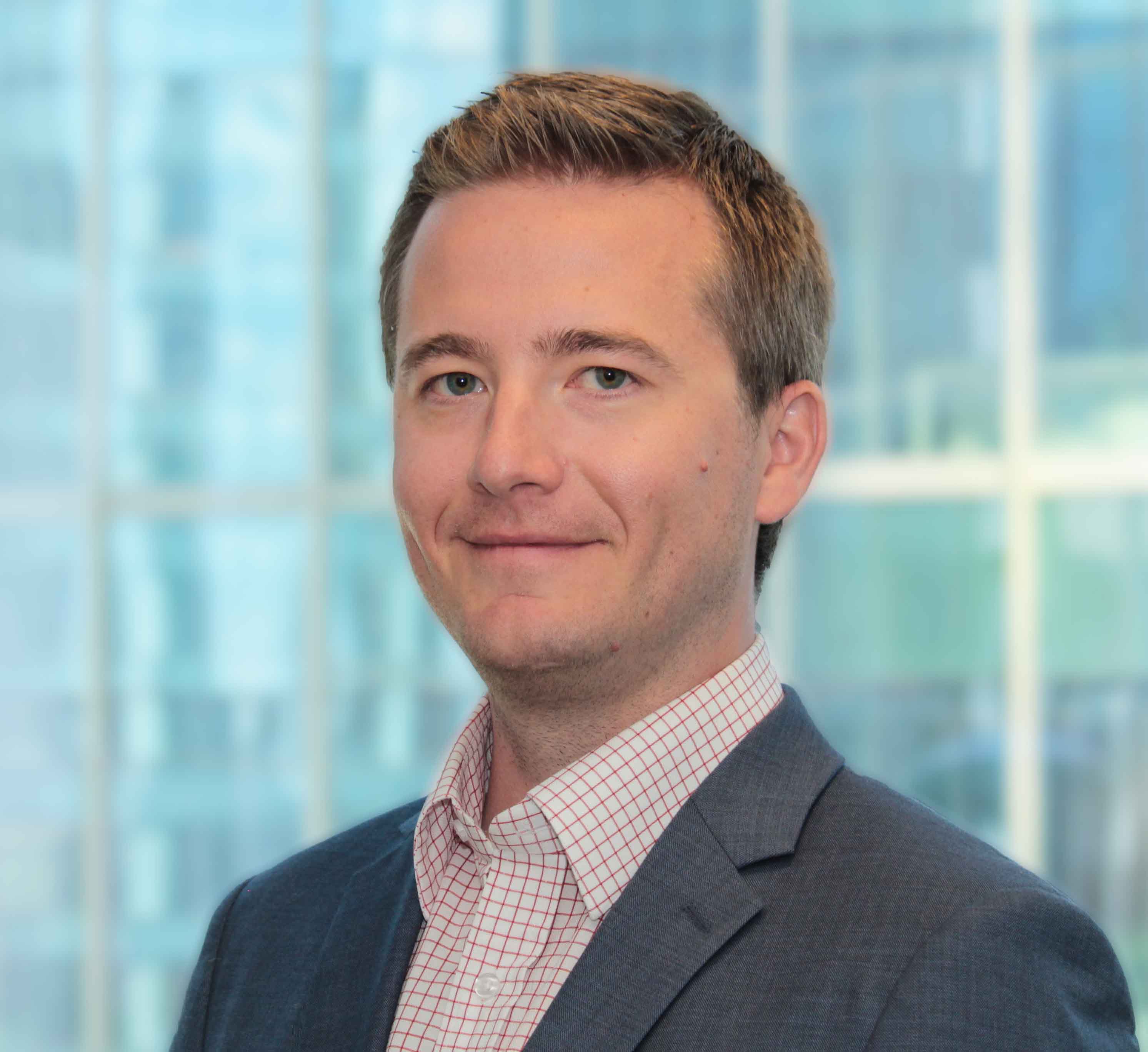
“On that incremental mile, are you gaining or losing productivity per foot relative to that offsetting 2-miler?” he asked.
Hill cited Enverus data showing that the most positive answer involves the long term, specifically in the Permian and in the Bakken.
“You’re not getting the same kind of peak rate” on a lateral normalized basis (per foot), he said. “But we’re seeing pretty comparable forecasted total recoveries. So, what you’ll eventually get out of that well, on a lateral normalized basis, is very close to being in line with two-mile drills, which is quite reassuring.”
A lower peak rate is balanced by a slower decline curve.
With similar per-foot production, it validates the idea that drilling two 3-mile laterals is indeed more cost-effective than drilling three 2-mile laterals.
“The more you have that capital cost savings, the more it pushes you down the 3-mile road,” Hill observed.
This good news only applies to producers that are willing to accept some delayed gratification. Many operators are looking to pay for the well as quickly as possible, therefore pushing for the highest per-foot peak production possible. For those operators, it might make sense to stick with shorter laterals, Hill noted, rather than facing higher up-front costs for the long laterals and slightly reduced peak flow.
Still, there are significant savings in entry costs when longer laterals result in fewer wells drilled. Hill says the cost savings can be “around 15%, even 20%, on a per-lateral-foot basis, just by avoiding those multiple vertical holes to access the horizontal.”
If three is good, why not go further? Hill says Enverus research has shown that Exxon Mobil has drilled at least a few 4-milers. But lateral length limits are set by technology, including production capabilities and, at least for now, 4 miles is about the far end of those abilities.
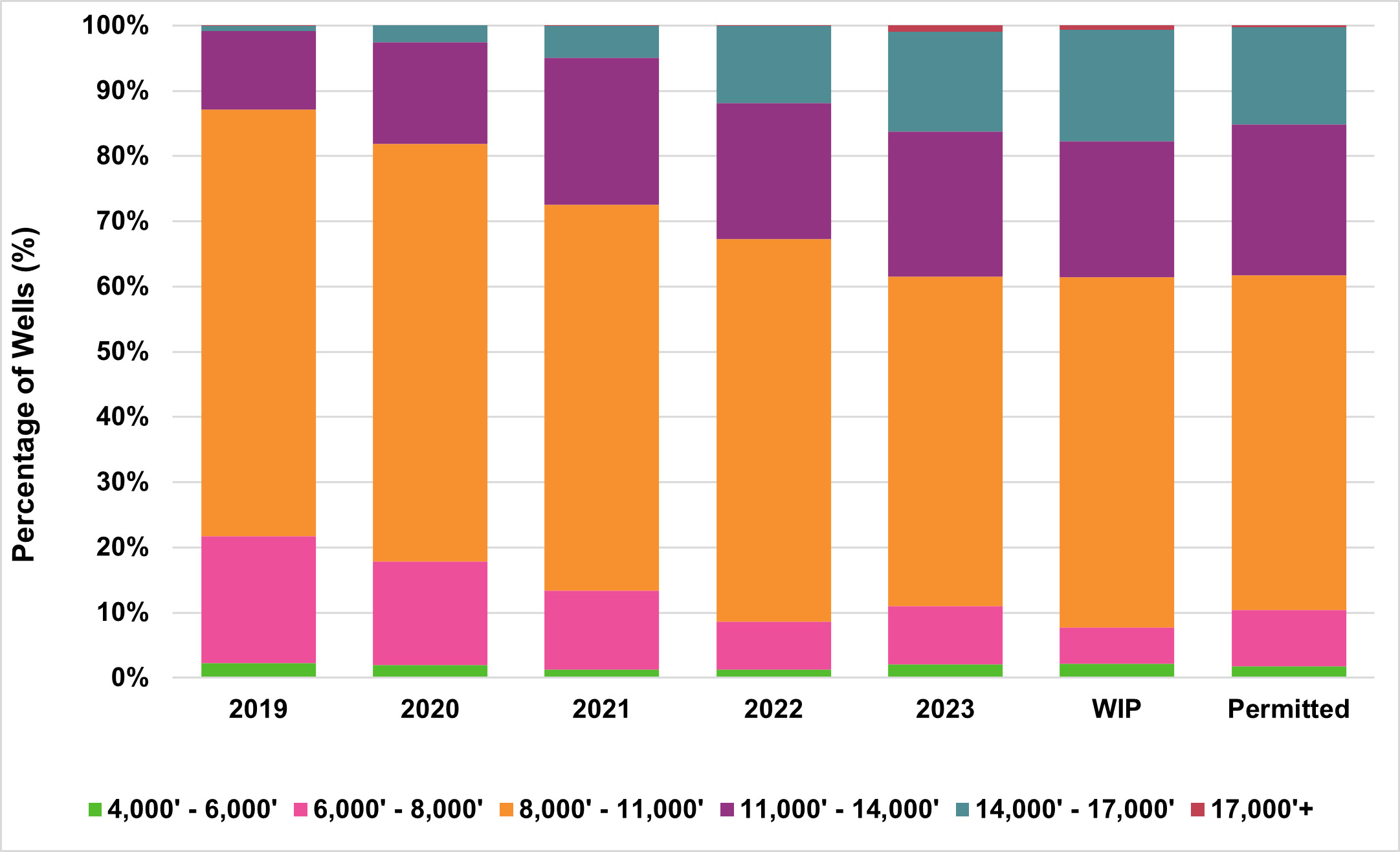
The shape of things to come
Drilling laterals in a fairly straight line is by far the preferred configuration, Hill noted, but there are several reasons drillers sometimes veer off the straight and narrow. Drilling U-shapes and even Ws—“We call it creative drilling”—is “an opportunity to save capital or even execute otherwise uneconomic drills because they would be too short,” he said.
The main reason for creative drilling is lease limitations, he said. A wellbore positioned closer than 2 miles from a lease border limits how far a well can go in that direction. South Texas and the Permian’s Delaware Basin are the main areas where this occurs.
Length and shape are also influenced by regulatory pressures, especially in Colorado, in Hill’s view. That state has passed laws mandating longer separation between well sites and structures, meaning that operators can be forced to drill farther to engage producing zones.
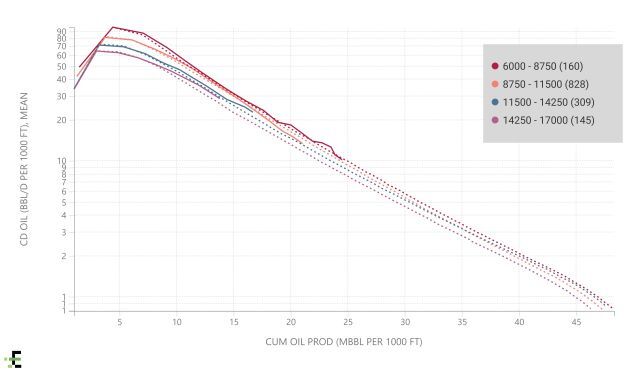
Completion, drilling tech
David Millwee, Patterson UTI’s vice president of drilling performance, told E&P the growth in wellbore length has depended on a number of technological advancements, not just on the drilling side. A major factor has been ongoing improvements in hydraulic fracturing techniques made necessary by the tight formations.
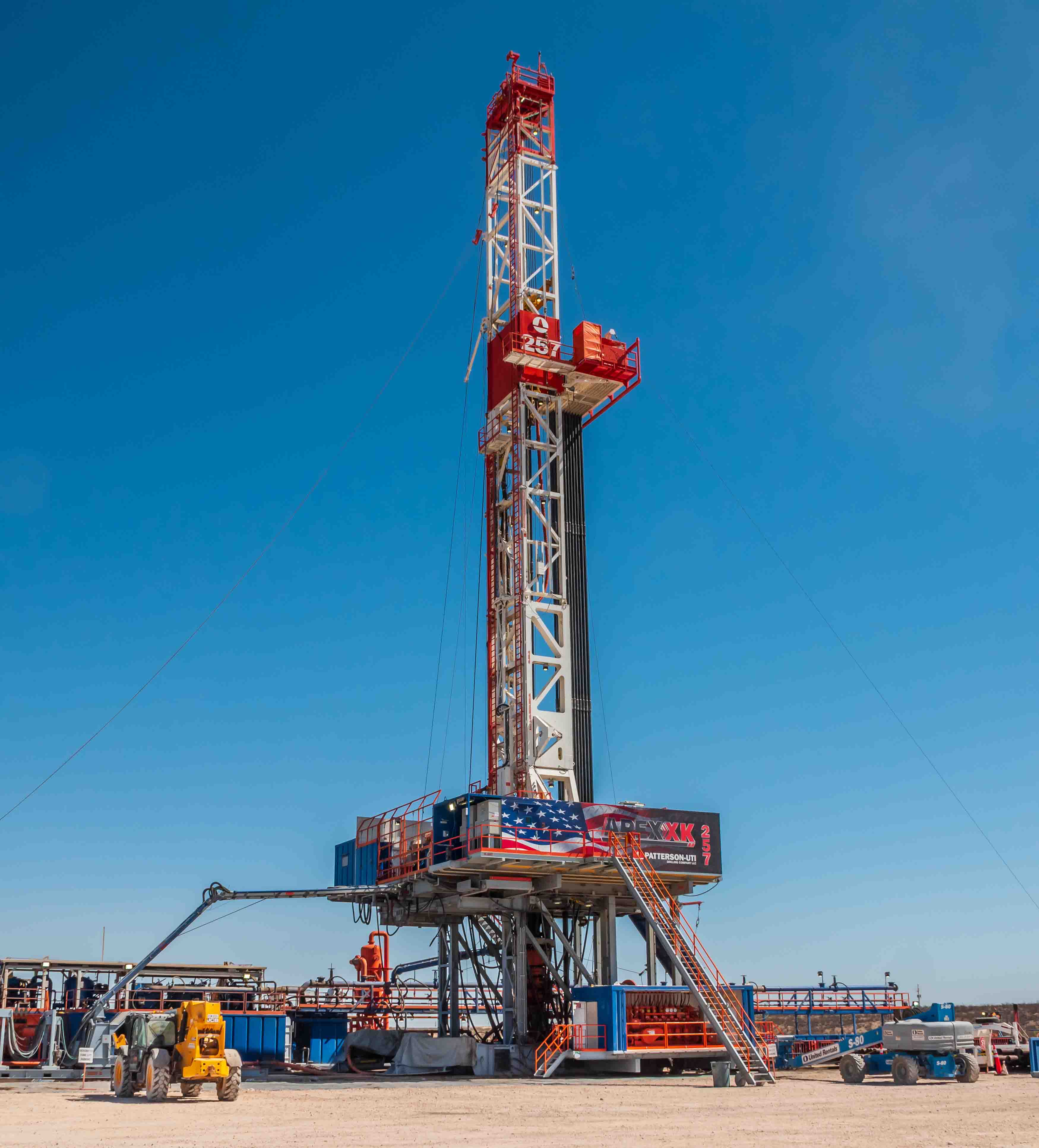
“In 1997, a long lateral was 500 ft because that’s how far they could reach for completions,” he recalled.
As processes expanded over the years, drillers grew their own abilities accordingly. Laterals slowly extended to 2 miles, then three, and today they are approaching 4 miles in some areas.
“What made you go from a 2-mile lateral to a 3-mile lateral? Well, completions people figured out how to frac that third mile efficiently; so let’s go out there and drill it,” Millwee said. “Every time we find a technical limit, we identify how to engineer improvements, implement the changes, and continue to move forward.”
Early improvements involved increasing hydraulic horsepower capability for drilling rigs. That is because increased flowrates and pressures required additional pumping capacity and raising pressure limits to 7,500 psi instead of the industry standard 5,000 psi. Additional torque requirements were next, requiring higher torque drill pipe, upgraded top drives and high-performing mud motors.
Some of the recent progress he sees includes new drill cutters making larger depth of cut, more powerful mud motors coupled with rotary steerables “so you don’t have to slide and keep rotating the pipe,” enhanced precision in rig control systems, process automation, and more.
All of these can inform decisions about overall lateral well length. Limiting the number of downhole trips is another factor.
“The fewer times you re-enter the production zone, the better,” Millwee said.
The ability to use just one bottomhole assembly (BHA) or minimal BHAs, depending on the play, is crucial. Every time the equipment trips out of a production zone and reenters it, the risk of problems increases.
“If we’re drilling a 4-mile lateral and there’s a BHA failure at 3.5 miles, sometimes they don’t drill the extra half mile,” he said.
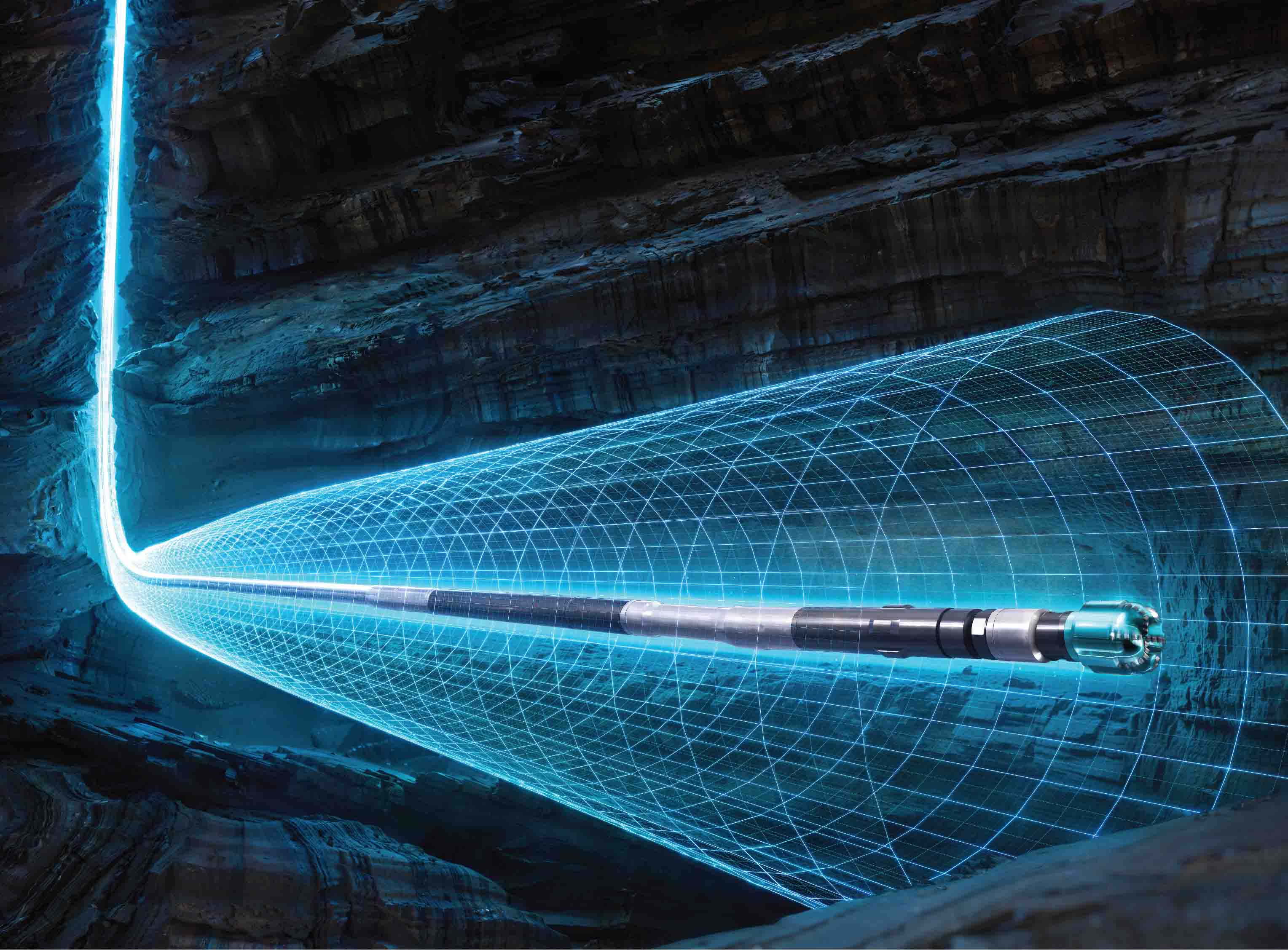
Tier 2 acreage
While lateral footage has grown by several factors since the early days of unconventional drilling, the yearly increase is incremental at about 350 ft per year, according to Matt Mayer, senior product manager for TGS Well Data Products.
He noted an upward trend with a peak of estimated ultimate recovery (EUR) around 2016 that is slowly coming back down, which TGS has partially attributed to lower-tier acreage or infill drilling with parent-child well interaction.
He sees necessity as a motivating factor behind the move to longer laterals. With most Tier 1 acreage already drilled, this could be a way to get more out of wells drilled in Tier 2 acreage. There is no geological reason for the third mile to be different from the first two in terms of production.
Efficient use of rig time could also factor into the mix.
“If you only have (a rig) available for a certain time, it’s probably more efficient on a per-foot-of-productive-interval basis to drill longer laterals than it is to drill a lot of shorter ones,” Mayer told E&P.
One factor de-risking the longer laterals could involve technological improvements in LWD tools, he observed, adding that today’s tools are more reliable and more accurate than ever before.
Avoiding downhole collisions
With the increase in longer laterals—and laterals as a whole in the crowded Permian Basin—avoiding collisions becomes as much of an issue downhole as it does on oilfield roads. Drilling rig giant Helmerich & Payne (H&P) sees a way to steer clear of these buried conflicts, Andrew Pare, H&P’s manager of geophysics and technology development, told E&P.
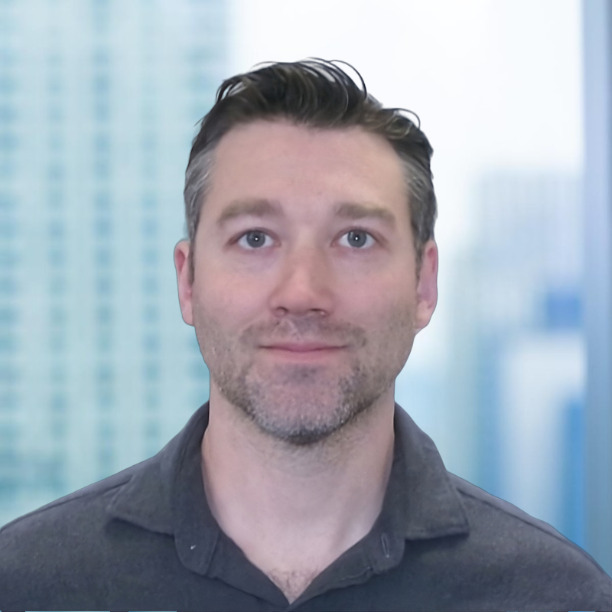
Pare is not aware of any cases where three-mile laterals have actually collided in the Permian due to most companies’ awareness of the issue and adoption of strong anti-collision policies. But he listed some ways the extended laterals can still destroy value.
“If survey accuracy is not addressed, then the wells will drain the reservoir with less efficiency but with high certainty. So, that’ll be very common if the decrease in survey accuracy is not addressed,” he said.
Such laxity could lead to a rise in “frac hits” as laterals grow to 3-mile lengths. “In rare cases, the laterals may collide in dangerous and destructive ways,” he said.
Before drilling starts, H&P technicians “take extremely precise magnetic field inclination and declination measurements with survey instruments” to refine the producer’s existing in-field referencing magnetic model, which was built with “less-accurate airborne measurements.” This is based on the direction of the earth’s natural magnetic field in relation to true north.
Pare said many current tracking methods become less accurate as the lateral passes the two-mile mark, and accurate data is necessary to precisely locate existing production.
Previous locating methods involved sending a gyro downhole, but that means drilling must stop while data is obtained. Plus, the longer the lateral, “the harder it is to push the sensor out into the lateral,” he noted.
H&P’s system gathers the data before drilling starts to better inform the planning process, he said.
The long run
The long and short of the decision leans on the industry’s ability to drill and frac efficiently at greater distances from a single well site. Perhaps someday drilling activity will be measured in feet drilled as well as in rig counts to more accurately represent the potential for new production.
The sky may not be the limit for lateral length growth—technology and lease configuration are today’s issues—but reports of laterals exceeding 50,000 ft are coming from the Middle East, where national borders are the only geographical restriction. In the interest of managing drilling costs by getting more rock exposure with fewer entry points, laterals will likely grow as far as the machinery and the economics will take them.
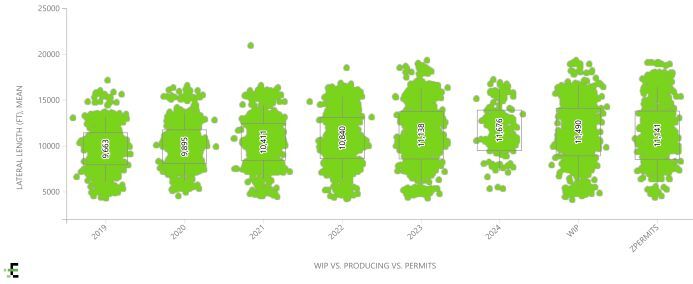
Recommended Reading
Enchanted Rock’s Microgrids Pull Double Duty with Both Backup, Grid Support
2025-02-21 - Enchanted Rock’s natural gas-fired generators can start up with just a few seconds of notice to easily provide support for a stressed ERCOT grid.
ADNOC Contracts Flowserve to Supply Tech for CCS, EOR Project
2025-01-14 - Abu Dhabi National Oil Co. has contracted Flowserve Corp. for the supply of dry gas seal systems for EOR and a carbon capture project at its Habshan facility in the Middle East.
McDermott Completes Project for Shell Offshore in Gulf of Mexico
2025-03-05 - McDermott installed about 40 miles of pipelines and connections to Shell’s Whale platform.
DNO Makes Another Norwegian North Sea Discovery
2024-12-17 - DNO ASA estimated gross recoverable resources in the range of 2 million to 13 million barrels of oil equivalent at its discovery on the Ringand prospect in the North Sea.
Baker Hughes: US Drillers Keep Oil, NatGas Rigs Unchanged for Second Week
2024-12-20 - U.S. energy firms this week kept the number of oil and natural gas rigs unchanged for the second week in a row.
Comments
Add new comment
This conversation is moderated according to Hart Energy community rules. Please read the rules before joining the discussion. If you’re experiencing any technical problems, please contact our customer care team.