In the shale era, electric submersible pumps (ESPs) have become the workhorse of the beginning phase of a well, which is its most productive. New types of ESPs using highly efficient permanent magnet motors (PMMs) are gaining acceptance for their ability to boost production along a shale well’s production decline curve.
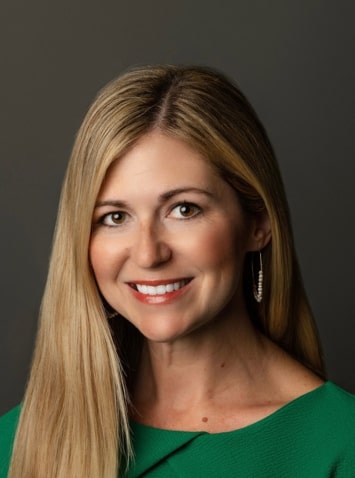
As wells age and production drops, gas production rises, creating gas-locking issues. These are being addressed by contra-helical pump systems designed to reduce gas locking. Baker Hughes and Extract Production, an NOV company, are advancing the industry in these and other areas.
PMM energy savings, efficiencies make them a viable option
For almost a decade, developers have known that powering ESPs with PMMs instead of traditional induction motors (IMs) can cut po
wer consumption and reduce the size of equipment inserted downhole. Early-day drawbacks included the shorter run life of PMMs and safety concerns due to the possibility of generating electrical charges when not running. So, PMMs remained under the radar while developers who saw their potential continued to improve them.
In the last few months, PMMs have become a hot commodity, said Dana Meadows, Baker Hughes’ artificial lift portfolio director. In 2023, the company’s PMM, branded as Magnefficient, accounted for only 3% of Baker Hughes-installed ESPs. This year, PMM installations have ballooned to 11% of ESP installations, and that number is growing.
Three reasons for sudden growth
There are multiple drivers for this increase, Meadows said, including improved safety devices, concerns about power grid overloads and the need to extend the economic life of producing wells. Baker Hughes has spent the last three years developing a complete system involving PMMs, the E2000 ESP and variable speed drives.
Because the magnets are permanent, they require less electricity to run. Officially, Baker Hughes says power savings are in the 10%-15% range, although some clients have seen cost reductions of up to 26%. This results in a lower operating cost for the well and more barrels of oil produced per day, Meadows said.
For many operators, PMM energy efficiency is as much about reducing loads on the already strained power grid and boosting ESG scores as it is about saving dollars. Power company fees for running new lines can run into tens of thousands of dollars and involve weeks of delays. By replacing IMs with PMMs, producers often can add more wells without incurring major infrastructure costs, Meadows noted, pointing out that the reduced power demand can also increase daily production.
“One operator said the power savings is great, but they’re able to get more out of the well per horsepower than they were able to out of IM because they previously had been maxed out on the power grid,” she said.
PMMs also enhance safety because the same permanent magnets that reduce power
requirements can generate current of their own when an installed pump is shut off, allowing the crude oil above it to flow back the crude oil above it to flow back into the hole. Unrestrained, that flow can cause torque to be transferred from motor to pump, or vice versa, in both clockwise and counterclockwise directions in some instances.
“If the motor is not restrained and you spin the shaft, that generates electricity because of the permanent magnets,” Meadows said. “That can create a hazard if someone is operating at the surface or handling the cable.”
To prevent the reverse spin, Baker Hughes developed a mechanical device that requires no wireline to operate it or a pin to pull when the pump is installed. It is designed with two clutches, one that allows the torque to transfer from the motor to the ESP in only one direction. It can free spin in operating mode, but it cannot rotate in reverse, which eliminates the action that can generate a dangerous power surge.
Meadows stressed that the company still urges operators to continue implementing existing safety measures as a fail-safe.
Simpler installation compared to older-model pump assemblies is another attractive factor, she said. With the older Flex ER, three pumps were required per well. The E2000 system requires only two pumps, which cuts 26 ft from the string.
The motors also are more compact, with PMMs coming in at 27 ft-28 ft instead of the IM’s 52 ft. With this total length reduction of around 50 ft, installation and service become more manageable.
Meadows said producers appreciate the advantages. “With a shorter, lighter system, they said they were able to get closer to the production zone than they were originally able to,” she said.
Longer life for the PMM comes in two forms. The first is advances in rotor and stator durability, which enable the PMMs to run longer. The E2000 and its wider efficient production range stretches from 3,100 bbl/d to 100 bbl/d. Because most ESPs only operate efficiently down to 300 bbl/d, the new system significantly pushes back difficult and costly decisions on next-step lift systems. This has the additional effect of extending a well’s profitable life.
Integrated gas processor reduces ESP gas locking
It is no secret that shale wells produce prolifically on ESPs for about the first year of life. Then, gas production rises to the point that the ESPs begin to lock up and must be continually stopped and restarted. All of this reduces pump uptime and production rates—and the starting and stopping creates electrical jolts that can shorten pump life. This is costly both in dollars and in lost production during downtime.
Traditional gas handlers and separators help, but they become less efficient as gas-to-liquids (GTL) ratios rise through the production life of the well. This results in higher gas void fractions (GVFs), the percentage of free gas versus gas that remains in the liquid, all of which create problems for ESPs.
To overcome this, Extract Production introduced its Integrated Gas Processor (IGP), designed to seamlessly replace gas handlers and separators. It uses a pair of contra-helical pumps to reduce the amount of free gas flowing through the ESP.
According to the company, in one application, the IGP boosted oil production by 153% and gas production by 224%, and reduced the GLR by 14% and pump intake pressure (PIP) by 11%. The IGP also has been shown to reduce gas locking by up to 50%.
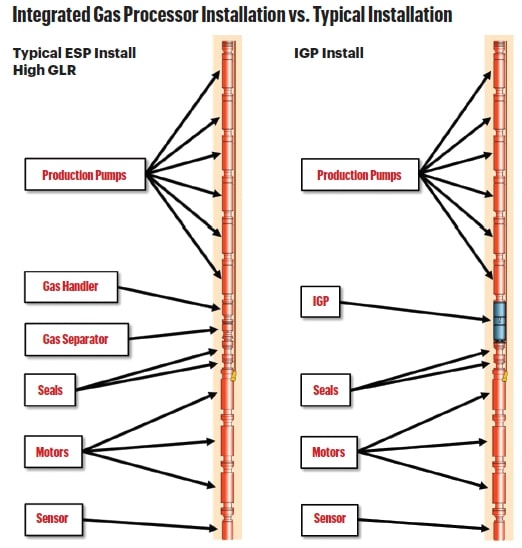
How it works
In a downhole assembly, the three-module IGP is installed immediately before the pump in place of the traditional gas handling equipment.
James Rhys-Davies, Extract’s engineering director, said from the bottom up, the IGP starts with a high-volume intake where the mixed-phase oil and gas enters. “The first module is the contra-helical pump stage that helps homogenize the fluid. Next is the dual-chambered separator module that separates the gas from the liquid, sending the gas into a casing flowing annulus and the liquid into the ESP,” he said.
The third stage offers three options for compressing the remaining gas.
“We try to separate as much of the gas into the annulus as possible, but there’s always going to be a little gas left over in the liquid stream. So, when we separate the gas into the annulus and it goes up the casing and out into a casing flowline, any remaining gas in the liquid goes up through the tubing string, where it is separated at the surface,” he explained.
This assembly separates the intake ports from the separator ports, Rhys-Davies said. “We think that’s helping to eliminate or reduce the recirculation. On a normal gas separator, that’s about a 1- or 2-foot separation, but we’ve got about 8 feet of separation, and that helps to let the gas go up the way and not to come back in.”
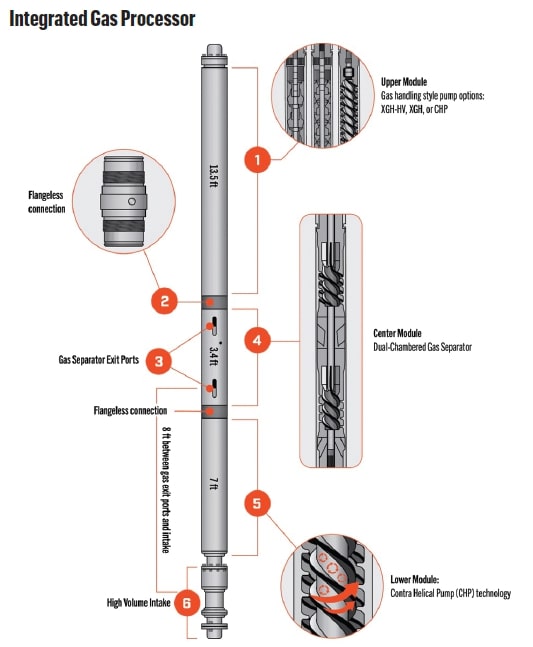
When to lift and separate
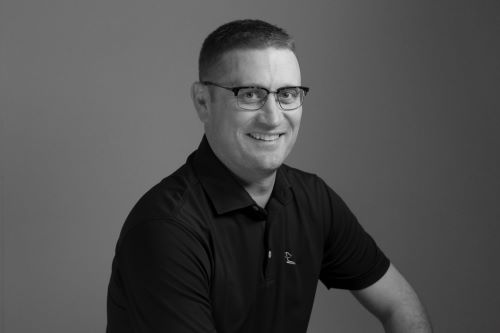
Gas separators of any sort are rarely installed in a new well, said Extract’s Chris Osburn, vice president of the artificial lift product line. “There’s usually little gas to worry about for the first six months to 12 months, and the IGP’s flow rate is limited to 4,000 bbl/d, so it could slow down a prolific well’s initial production.”
When the IGP is installed at the start, he noted, it usually is in Midcontinent wells. “They’re not as prolific, and don’t hang on as long as Permian Basin wells,” he said. In those cases, including IGP at the beginning eliminates the need for a workover to install it later.
Osburn added that, due to the tendency toward high sand content in early production in Permian wells, most producers do not want to rush the installation of any extra equipment that could be damaged by sand.
In the field
A recent installation, in which Extract replaced a competitor’s 3000 pumps and gas separators with the IGP and Extract 3000 pumps, yielded some significant results. Due to increased pump uptime and improved gas separation, the producer saw oil production rise by 153%, gas by 224% and water by 316%. The GLR dropped by 14%, and the PIP was reduced by 11%, showing that the pump operated more efficiently.
With the significant decline curves in older unconventional wells, numbers like these translate into significant improvements in profitability.
Recommended Reading
Magnolia’s Board Adds Ropp as Independent Director
2025-01-07 - Alongside his experience in oil and gas operations, R. Lewis Ropp has a background in finance, capital markets and investment management, Magnolia Oil & Gas said.
Talos Selects Longtime Shell Exec Paul Goodfellow as President, CEO
2025-02-03 - Shell veteran Paul Goodfellow’s selection as president, CEO and board member of Talos Energy comes after several months of tumult in the company’s C-suite.
Expand Appoints Dan Turco to EVP of Marketing, Commercial
2025-02-13 - Expand Energy Corp. has appointed industry veteran Dan Turco as executive vice president of marketing and commercial.
Expand Energy Picked to Join S&P 500
2025-03-10 - Gas pureplay Expand Energy will be elevated on March 24 from its position in the S&P MidCap 400 index.
Devon Energy Announces Changes to Executive Leadership Team
2025-01-13 - Among personnel moves, Devon Energy announced John Raines and Trey Lowe have been promoted to senior vice president roles.
Comments
Add new comment
This conversation is moderated according to Hart Energy community rules. Please read the rules before joining the discussion. If you’re experiencing any technical problems, please contact our customer care team.