
A Halliburton frac crew completes a well in the Midland Basin. Over the past five years, completion designs have evolved to include more proppant loading, longer laterals, higher stage counts and improved understanding of well spacing. (Photo by Tom Fox, courtesy of Oil and Gas Investor)
In the 70 years since the first hydraulically fractured well began commercial operations, the technique’s processes and designs have undergone a sea change—and in some cases a tsunami—that have led to unconventional oil and gas production being the catalyst to the U.S. shale boom.
Both the micro- and macro-evolutions of completion designs toward high-intensity completions have led to a drastic reduction in breakeven production costs. In 2015 North American shale ranked as the second most expensive resource, according to Rystad Energy’s global liquids cost curve, with an average breakeven price of $68/bbl. The average Brent breakeven price for tight oil is now estimated at $46/bbl, according to the May 2019 press release from Rystad Energy.
The cost reductions have not been a result of a single innovation, or even just a few. As Pioneer Natural Resources explained in a paper presented at last year’s Society of Petroleum Engineers (SPE) Annual Technical Conference and Exhibition, design teams must consider more than 20 different design parameters for a well’s completion, including proppant and fluid type and amount, cluster spacing, stage length and well spacing. In addition to the multitude of completion components, the reservoir’s characteristics such as thickness and rock properties must be well understood, as they can change significantly across a field, Pioneer explained.
Mike Mayerhofer, director of technology for Liberty Oilfield Services, cited increasing treatment sizes, the move away from crosslinked gels to slickwater fracs and increasing proppant intensity as the primary drivers behind enhanced well completions.
“The driving point is that the data are showing that the extra incremental oil you’re getting with this more aggressive approach is justifying the cost,” Mayerhofer said.
Halliburton’s senior product champion, unconventional completions, Zachary Walton, explained that the most significant technologies that have played a role in the evolution of enhanced completion designs are those geared toward efficiencies, such as the adoption of pad drilling. Pad drilling, he said, gave rise to a manufacturing type of well design that would produce multiple wells at once on the same footprint.
“This, in turn, pushed the evolution of completion tools by driving cost down due to volume, coming up with new materials for reduced mill-out time, or no mill-out time at all, and increasing the total number of available stage counts,” Walton said. “The whole process is a very unique balance between operational execution and the technology that enables it where one is always pushing the other.”
Bakken
Hess is a leading operator in the Middle Bakken and Three Forks with about 550,000 net acres and an estimated 2019 production to be 135,000 to 145,000 boe/d, according to the company’s presentation at the Scotia Howard Weil Energy Conference in March.
Hess’ financial and production metrics have experienced a marked increase following its move to plug-and-perf (PNP) completion designs and improved well spacing after the price collapse of 2014. The company reported in its December 2018 investor presentation that its adoption of PNP completions is forecast to result in increases in production to about 200,000 boe/d and net present value by about $1 billion.
But as recently as 2017, Hess was utilizing sliding sleeve completions full scale in the Bakken in its efforts to find revenue in the price-depressed market, as Barry Biggs, vice president of onshore, explained.
“We decided to double down on what we’d been working on up to that point of our journey, which was the sliding sleeve completion,” he said. “The technological component of that was adding additional stages. So, back in the 2013 time frame, it was 10 to 15 stages. By 2014 it was 30 stages, and by the time we got to 2017, we were at 60 stages. We really focused on driving the sliding sleeves to its technical limit.”
Biggs said that during that period, Hess worked to drive costs down by about 40% since 2014.
“We were about $4.8 million per well cheaper than our competitors in 2015,” he said.
With a lower cost structure and rebounded prices, Hess continued adding entry points through PNP completion technology to increase production.
“Each area acts a little bit differently in the Bakken,” he said. “There’s no one-size-fits-all. Plug and perf offers the ability to add more entry points, which is the key here.”
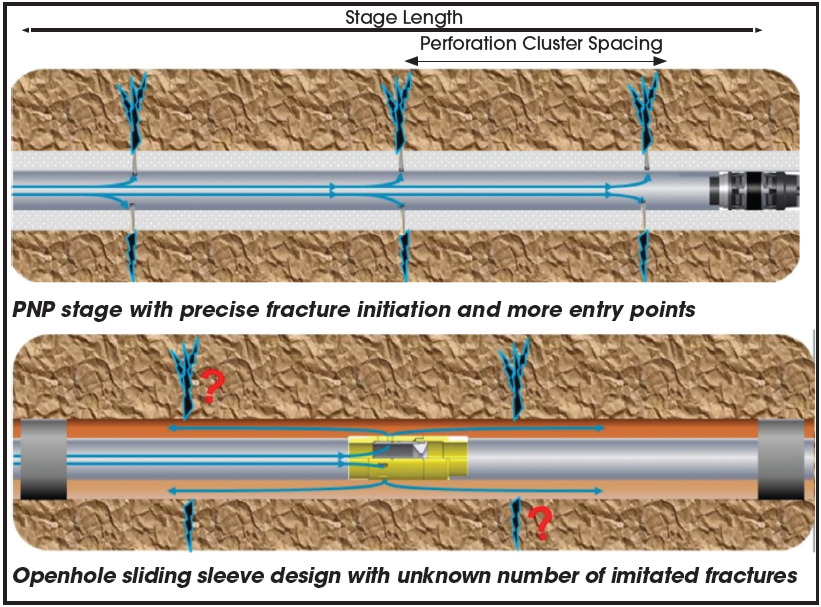
In addition to stage spacing and the shift to PNP completions, Hess has substantially increased its proppant loading design. Biggs said that in about 2014, when Hess was moving from 25 stages up to 60, its completion designs included about 70,000 lb per stage of proppant. That amount has more than tripled to as much as 280,000 lb per stage.
“So that puts us in the 8-million- to 12-million-pound loading across the well now, compared to as low as the 3.5 million we were doing back in about 2014,” Biggs said.
He added the company primarily uses 40/70 mesh sand, and while it has employed some uses of 100 mesh, it has yet to adopt the finer proppant types fully.
Hess also has shifted away from crosslinked gel frac fluid from previous completion iterations, Biggs said, while also bypassing slickwater fracs, which have been in favor for much of the shale industry over the past few years.
“We have really been focused over the last three or four years on a high-viscosity friction reducer [HVFR], and we’ve been very successful with that,” he said. “Some people have gone with the slick water, but we’ve stayed with this HVFR that we perfected in the Utica and brought it back to the Bakken.”
While operators in many North American shale basins have the flexibility to experiment or apply extended, or even “super long,” laterals—sometimes up to 4.8 km (3 miles)—drilling regulations in North Dakota limits well lengths based on drilling spacing units (DSU). The State of North Dakota set DSUs at 1,280 acres, which effectively limits laterals to 3,048 m (10,000 ft).
According to an SPE paper by Liberty Oilfield Services, average lateral lengths in the Bakken and Three Forks have essentially remained constant at about 2,590 m (8,500 ft).
Biggs said Hess has also mostly avoided problems with parent/child well interactions, despite seeing some pressure responses between wells. He said the company’s well spacing design in its core acreage averages about 152 m (500 ft) between wells, whereas others in the region are at about 243 m (800 ft).
“As we moved forward, we’ll be testing different spacing designs,” he said. “We’ve taken the tack that tight spacing generates the highest value, not necessarily per well, but per DSU at that 500-ft spacing.”
Biggs said finding the right completion formula could improve Hess’ noncore acreage position on a scale with its core acreage.
“In terms of sand loading, the number of entry points and well spacing, all of those variables interact here,” he said. “And we’re trying to find the right recipe in each of those areas to pull our Tier 2 and Tier 3 acreage into Tier 1.”
Haynesville
Goodrich Petroleum controls a combined 23,000 acres in the Haynesville core with proved reserves in those plays of about 13 Bcm (471 Bcfe). The company’s annual production has grown from about 849 cu. m /d (30,000 cfe/d) in 2017 to an estimated 3,964 cu. m /d (140,000 cfe/d) this year, according to its fourth-quarter 2018 investor report.
Robert Turnham, president and COO of Goodrich Petroleum, explained that when the company began developing the Haynesville, its completion designs were based on short laterals and small amounts of proppant. Goodrich’s original completion designs featured 1,402-m (4,600-ft) laterals, 1,000 lb/ft of proppant loading, 91-m to 137-m (300-ft to 450-ft) frac intervals and cluster spacings of 15 m to 21 m (50 ft to 70 ft), and a hybrid design of gel and slickwater frac fluid. The result, Turnham said, was underperforming wells.
“A much wider interval with much less proppant per foot was creating much poorer stimulation,” he said.
After gas prices in 2014 fell from $6/MMBtu to about $3.50/MMBtu, Turnham said Goodrich looked to test different stimulation methodologies. The result was longer laterals, higher proppant loading, a shift to exclusively slickwater fluids, tighter frac intervals and closer cluster spacing.
“It became clear that if you tightened your intervals and increased your proppant, that would make a huge difference,” he said. “So we tested all the way to 10,000-ft laterals and 5,000 lb/ft of proppant and less than 100-ft (30-m) intervals, and clearly that combination made the best wells drilled to date in the Haynesville.”
Turnham noted, however, that the higher-density completion design also came with a higher cost.
“Then the question is how to tweak that so you’re not only getting a superior reserve but also generating the highest rate of return,” he said.
Goodrich’s current completion design now features on average 2,286-m (7,500-ft) laterals with 4,000 lb/ft of proppant and cluster spacings of between 4.8 m and 6 m (16 ft and 20 ft). Turnham said the transition away from gel to slick water has resulted in better cracking of the rock in the frac intervals.
“The goal here is near-wellbore stimulation versus wing length reach away from the wellbore, because the farther out you go, the more the likelihood that the frac is going to close up on you,” he said. “You’re just not going to capture as much of the gas that’s in place unless you tighten up the intervals. And that’s what we’re seeing—higher recoveries from better stimulation.”
Although Goodrich tested 3,048-m laterals, Turnham said the company settled on the shorter 2,286-m wells at least in part to more consistently drill on budget. Replacing mud motors or drilling tools is more costly with longer laterals as a result of the time it takes to retrieve and replace the tools, he said.
“By the time you come up to the surface and get back down to drilling, it could add three days to your drill time,” Turnham said. “Every day costs you $75,000 to $100,000, depending on what tools you have in the wells. So, it’s not that you have risk drilling from 7,500 ft to 10,000 ft, it’s that you have a higher probability that you could exceed your budget or estimate to drill that well.”
In addition to fine-tuning the parameters of its completion design, Turnham said Goodrich has also begun to implement dissolvable plugs into its operations. He said the company first utilized dissolvable plugs in its operations in the Tuscaloosa Marine Shale in 2013 through about 2015.
“For the technology back then, those plugs were not as good as the plugs are now, and in the early days dissolvable plugs might not have kept a grip or hold when you’re fracking,” he said. “They might not dissolve properly, or they might create this emulsion that would mix with your clays and sands.”
Turnham said the modern dissolvable plugs Goodrich applies hold and are easier to clean out. In addition, he added Goodrich, like many other operators in the Haynesville, has turned almost exclusively to PNP completions rather than sliding sleeves.
“It’s a better methodology to ensure that you’re stimulating equally over an interval through your perforation,” he said. “We’ll put 35 perforations over a 100-ft interval, and if you pump your fluid at 2 bbl/min per perforation, you’re equally distributing the fluid out over those perforations, and therefore, we think you get a more uniform completion than if you just had a sliding sleeve that basically opens up the interval.”
Midcontinent
Chaparral Energy is a pure-play Stack/Merge operator that reported 14,400-boe/d Stack production in 2018, an increase in production of 52% over 2017. According to the company’s May investor report, Chaparral’s drilling and completion costs in the Osage and Meramec are just more than $800/lateral ft, about $200 less than the average cost per lateral foot among its peers in those plays.
Similar to Goodrich Petroleum, and a host of other operators, one of the primary goals in the company’s completion designs is to optimize near-wellbore stimulation, said Jim Miller, Chaparral’s senior vice president of operations.
“Our stimulation job has changed quite a bit over the last several years,” he said. “Instead of trying to reach out and touch someone with the frac job, we’re trying to create a more complex near-wellbore fracture.”
To improve conductivity, Chaparral employs cemented liners and low viscosity frac fluids with 100 mesh proppant, a change from the 40/70 and 30/50 sands and cased and cemented wellbores the company initially utilized in the Stack. Josh Walker, Chaparral’s vice president of completions and operations, said thinner frac fluids combined with finer-mesh sands and minimal chemicals and acids are easier to place within the fracs.
“It’s hard to place a decent concentration of 40/70 or 30/50 [proppant] with really thin fluids,” he said. “You open up your options when you’re placing 100 mesh, and so we’ve gone away from any viscous fluids.”
Chaparral is also among the operators that have found improved results deploying diverters in its completion operations to achieve improved cluster efficiencies. Walker said Chaparral has improved its understanding of diverting agents and their impact on cluster efficiency through the use of fiber optics over the last few years.
“That’s been one of the driving factors in finding a diverting agent that actually works, and that’s been one of the things the whole industry has been looking for over the past six or seven years,” he said.
Walker said the early diverters designed with polyactic acid or fibrous materials were not as effective as current designs.
“The TTS [Thru Tubing Solutions] pods are the first thing we’ve found that actually do what they’re designed to do, which is to plug up that major runaway fracture,” he said. “So that’s how we mitigate risk, because we’ve added a few clusters per stage and we mitigate the potential of decreased cluster efficiency with a diverting agent.”
In addition to applying diverters more so than in previous completion designs, Chaparral is now testing dissolvable frac plugs to use in place of traditional plugs. Walker said dissolvable frac plug technology has improved over previous iterations while the costs have come down to a point where their use is more justifiable.
“[Dissolvable plugs] would help a whole lot in the Stack,” he said. “It’s less of an issue where you’ve got all the pressure in the world, but if you can find something to help mitigate the risk of drill out, it’s a big step.”
Also similar to other operators, particularly in the Stack. Chaparral has reevaluated its well spacing plans to avoid potential parent/child well interference. The company has tested well spacing designs at its Denali, Foraker, King Koopa, Hennessey and Jester units as well as at some of its nonoperated units.
During the fourth quarter of 2018, Chaparral brought online its first operated partial spacing test in Kingfisher County, Okla. Chaparral CEO Earl Reynolds said during the company’s fourth-quarter 2018 investor call that the five-well King Koopa test included three Meramec and two Osage wells and was drilled in a section with an original Meramec parent well.
“We did not see any hydraulic communication between the infill wells, which is a good sign that our frac was contained to near-wellbore as per our design,” Reynolds said. “Another sign of the frac design effectiveness is the fact that the parent well has successfully returned to its pre-infill production rate.”
Reynolds said those results give the company confidence in its frac design and spacing plan as it moves toward full-section development. Walker explained that design has evolved and the company now believes it can successfully develop three or four wells per drillable bench. Miller added that Chaparral has introduced, when economically feasible, repressuring and refracturing parent wells.
“When you start looking at repressuring the parent wells, that’s an additional cost to the job,” Miller said. “To make those wells economic, you have to include that cost to repressure the parent [wells]. If we can do that, and improve your child wells, then we feel like we’re better off.”

Marcellus-Utica
In March Appalachia operators Blue Ridge Mountain Resources and Eclipse Resources merged to form Montage Resources. The merger resulted in, among other dynamics, a focus on improving the economics, and subsequently the returns, of its well designs. The former Eclipse Resources made headlines for its “super long” laterals, which averaged 5,600 m (18,375 ft). In 2017 the company set the world record for the longest lateral at 5,882 m (19,300 ft), or 6 km (3.7 miles).
But now, under the Montage Resources moniker, those lateral lengths have tapered off a bit, said Douglas Kris, vice president of investor relations.
“What you’ve seen more recently with regard to the new company is a reigning back in terms of lateral length, and it’s due not to the inability to drill out that far or the degradation of recovery,” he said. “It’s more driven by the market environment these days, which is focused on generating cash flow quicker.”
According to a company investor report, Eclipse’s wells averaged about 4,694 m (15,400 ft) in length in 2018. This year that distance has been reduced to an average of about 356 m (11,700 ft), a decrease of 25%. The result has led to a reduction in cycle time of about 20% from 220 days to about 175 days, which, as Kris explained, improves the return to capital.
“If you drill four 20,000-ft [6,096-m] laterals, you’re talking nine to 11 months from when you spud until you start to see cash flow,” he said.
Also driving economic returns has been the company’s evolving plan for proppant loading and stage spacing. About two years ago, Eclipse was loading proppant at about 3,000 lb/ft with stage spacings of 45 m to 61 m (150 ft to 200 ft), Kris said.
“What we’ve learned is that the stage spacing is probably correct in roughly that 200-ft spacing, but the proppant loading is closer to 2,500 lb [per foot], and not over 3,000 lb [per foot],” he said. “Because with each pound you’re getting a diminishing return, and you’re not necessarily getting additional EUR for the incremental sand that you’re putting down there.”
Such a design, however, is not applied uniformly throughout an entire well or a well pad, Kris explained.
“What we’ve found is that like rock stimulates better with like rock,” he said. “So if you see something in the rock characteristics that would result in a stage at 250 ft [76.2 m] as opposed to 200 ft because the rock characteristics are the same across the entire stage, then the proppant gets put away evenly in that entire stage. Whereas if you just had a 200-ft stage and you had different rock characteristics throughout the stage, your proppant is going to get placed more in one area and not the other. You won’t get the full effect of the cost that you’re putting down there.”
Part of the success of Eclipse’s super long laterals, at least in terms of production, was the ability to push proppant into the reservoir so far from the spud location, an effect of improved fracture fluid applications and the adoption of mostly 100 mesh sand, Kris said.
“We moved away from the crosslinked gels, which is what we used initially in 2013 and 2014,” he said. “We’ve moved away from that to more slick water, and we’ve found that to be much better and much more beneficial for the life of the well and the preservation of the reservoir.”
The high pressures of the Appalachian Basin often present challenges when applying technologies and tools that have proven successful in lower-pressured environments. Among those are dissolvable plugs. Kris said Montage has only moved into the testing phase for dissolvable plugs but is hesitant for widespread adoption.
“I think part of that is just the trepidation in Appalachia just because of the rock characteristics,” he said. “You’re a lot deeper and the pressure is a lot higher, especially in dry gas. We haven’t had any issues, but we’ve seen some issues from other operators with whom we have a working interest. So we’ve never holistically used it for an entire lateral.”
Future of completions
Montage’s inclination to cut back on its lateral lengths, along with similar signs in nearly all shale basins, is an indication the industry might be seeing an end to the continuation of higher-intensity completions. Operators and service companies are beginning to see diminishing returns from increasing proppant loading, extending laterals even farther and setting frac stages closer together. Meanwhile, frac hits resulting in lost production are causing companies to reevaluate their well spacing plans.
“This year is probably the first time that we’re seeing it’s a lot more stabilized with proppant,” said Riteja Dutta, senior production manager of analytics and engineering at Drillinginfo. “In fact, in some areas it’s even dropped a little bit from an average of about 2,000 pounds per foot in 2018 to now we’re at about 1,800 pounds per foot in certain areas. And apart from controlling costs, the dynamic of well interference has also changed the conversation of how intense those fracs are.”
Liberty’s Mayerhofer explained that investors are now looking for companies to improve their profit margins and become cash-flow positive, which drives cost reductions and, subsequently, modified completion designs.
“I think people have taken their foot off the gas pedal a little bit,” he said. “When we do our Big Data studies, we definitely see that as you go larger and larger on treatment sizes, we see production has diminishing returns.”
Halliburton’s Waltong explained that the limits on completions are an indicator of an evolution in technology. That evolution, he said, will likely lead to newer approaches to future completion designs.

“[Operators] find that they now are pushing the technology and, by association, the whole operational process to its limits,” he said. “These kinds of litmus tests on existing technology, along with the introduction of Big Data and digitalization in the oil field, provide indicators on where technology and processes can improve and what types of innovation are needed to be pushed forward. These pushes can sometimes lead to a new completion approach, new technology, new processes or a collaboration of each.”
Recommended Reading
Jericho to Start Data Center Business on Oklahoma Gas Assets
2025-04-01 - Canada’s Jericho Energy Ventures says it will deliver on-site natural gas to power future campuses.
Cella Mixes Two Approaches to Keep CO2 Solidly Underground
2025-04-01 - Cella, a startup in partnership with Halliburton, injects CO2 into basaltic reservoirs, where it reacts and hardens.
‘We’re Not Going Anywhere’: Sabine CEO on Haynesville Growth, M&A Talks
2025-04-01 - Sabine Oil & Gas CEO Carl Isaac shares insight into the company’s addition of a fourth Haynesville rig and future development plans in the play, in this Hart Energy Exclusive interview.
TG Natural Resources Wins Chevron’s Haynesville Assets for $525MM
2025-04-01 - Marketed by Chevron Corp. for more than a year, the 71,000-contiguous-net-undeveloped-acreage sold to TG Natural Resources is valued by the supermajor at $1.2 billion at current Henry Hub futures.
Sempra Plans to Sell Assets, LNG Stakes to Invest in Utilities
2025-03-31 - Infrastructure company Sempra Energy is preparing for major growth coming in electrical demand by selling assets to raise capital.
Comments
Add new comment
This conversation is moderated according to Hart Energy community rules. Please read the rules before joining the discussion. If you’re experiencing any technical problems, please contact our customer care team.