Adam Dyess is the director of business development at Hunting Titan.
If we look back at the past 15 years, the unconventional completions sector has seen a tremendous growth in daily stage capacity and operation efficiencies, primarily driven by process and product innovations in the plug and perf space, which consists of isolating and stimulating individual zones in the lateral via wireline perforating followed by hydraulic pumping from the surface.
Step-change advancements in techniques have more than doubled capacities to 20+ stages per day in several basins throughout North America. If you were to visit any multi-well pad wellsite, you could see how various technologies have driven efficiencies and safety by eliminating human interactions.
For example, personnel have been completely removed from several hazard zones near the wellhead where pressurized lines and elevated valves pose safety risks. Automated hydraulic wellhead connections not only eliminate humans from red zones, but also provide time savings of over 50% when stabbing onto the well compared to standard man basket operations.
Similarly, automated valve control systems simplify the thousands of individual valve turns involved in each pad completion. This technology allows digital, remote and seamless well-to-well valve control for the frac operations, which increases safety and provides additional time savings on the well completion.
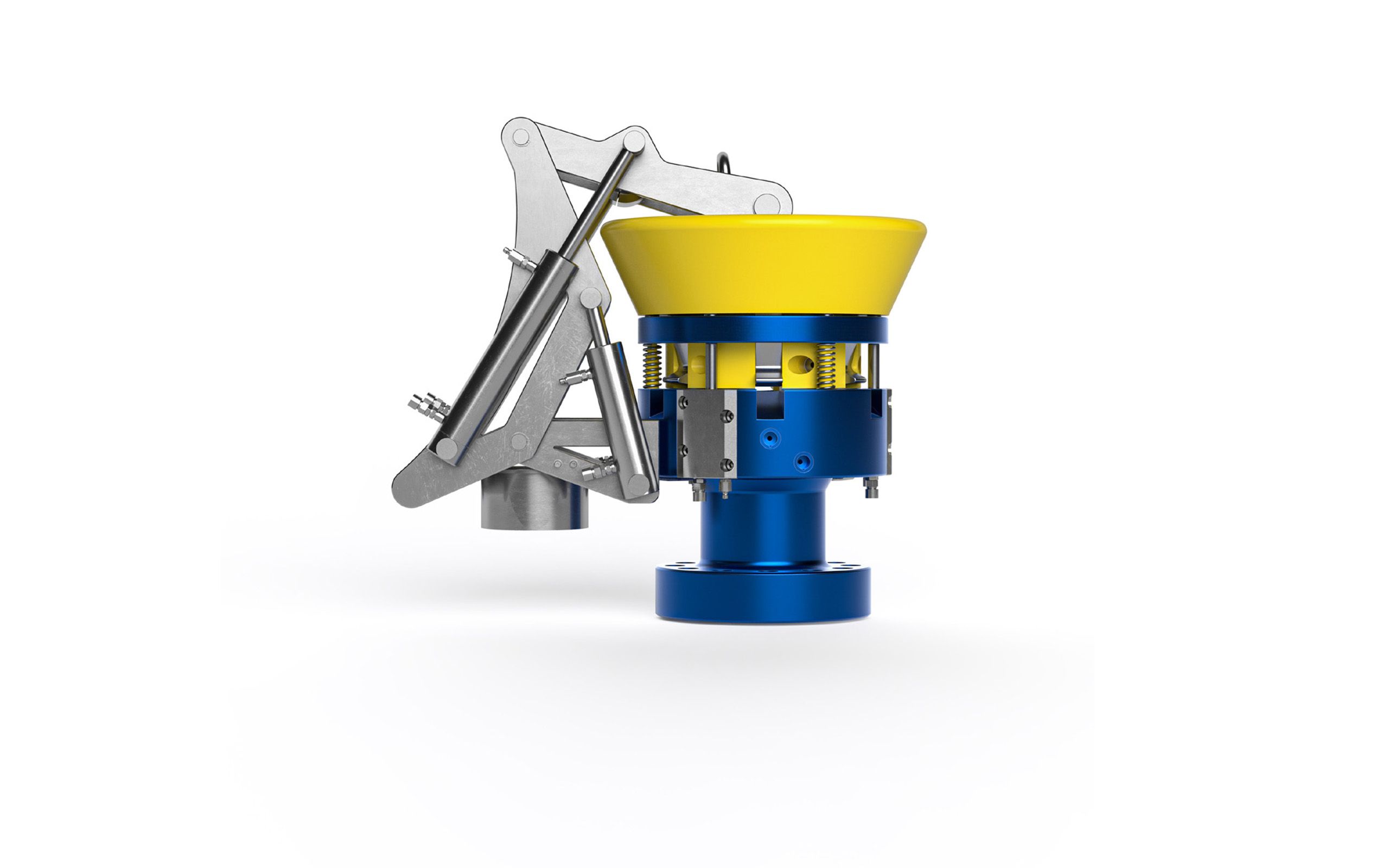
Perhaps the greatest impact to plug and perf productivity is the continued enhancement of simul-frac operations, which has revolutionized resource utilization compared to traditional plug and perf methods. Simul-frac aims to eliminate all non-productive time by fracking multiple wells while simultaneously perforating multiple wells so that the completion process for all wells on the pad is continually progressing.
This methodology has led to 50% gains in stage capacity compared to traditional plug and perf techniques. Moreover, the advent of electric pumping units with more reliable and higher horsepower has enabled single fleets to pump multiple wells, further reducing costs and environmental impact. The combination of e-pumping fleets and simul-frac has enabled record U.S. production with decreased drilling activity in recent years.
Advances in automation
Constraints still exist in the overall plug and perf process that inhibit ideal utilization rates as the industry strives to reach continuous 24-hour pumping. The post-COVID labor force in the services sector has led to stagnant operational efficiencies since 2022. Skilled labor shortages, high turnover and inexperience have generated huge inconsistencies in service operations, which is a recipe for quality issues and down time.
It is imperative that the collective industry—which includes producers, service companies and product companies—address the variabilities inherent to manual processes by advancing automation. Digital tools and automated solutions reduce operating costs in the industry by streamlining processes, enhancing accuracy and optimizing resource allocation.
One key to mitigating the labor issues is automating the preventive maintenance of strained equipment and processes. For frac, the latest e-pumps feature state-of-the-art sensory systems and data acquisition equipped with machine learning capabilities. This technology allows for the predictive maintenance required to reach continuous pumping for the entirety of the well pad completion.
On the perforating side, smart perforating systems feature addressable switch technology that allows top to bottom wireline tool string interrogation, status reports and troubleshooting aid prior to deployment into the well. The most advanced switch system can output the functional condition of each perforating gun’s detonator and even the plug setting tool’s power charge. This technology has prevented over 60% of suspect initiators from being run in hole, saving hundreds of hours associated with mis-run non-productive time every year.
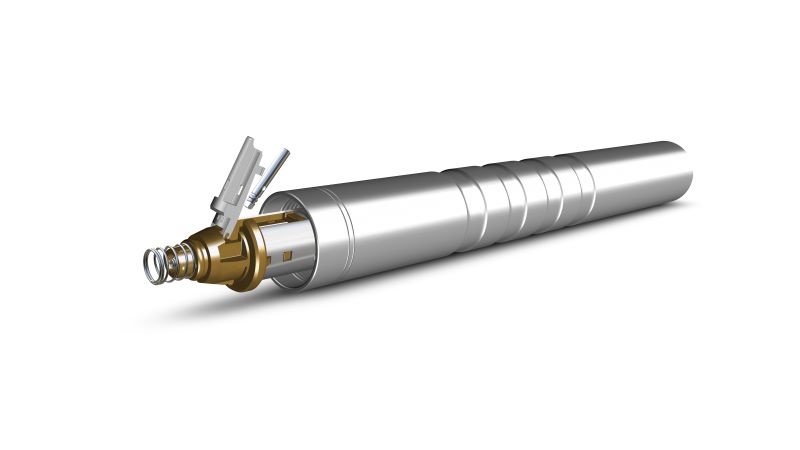
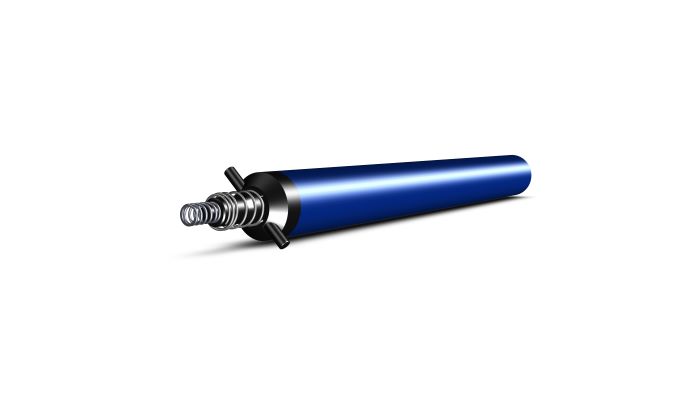
While previous automation initiatives have focused on the frac side, recent developments have focused on wireline perforating operations. E-pumping units have been paired with electronic winches to create closed-looped automated pump-down systems that substitute the insufficient human reaction times with instantaneous pump and winch controls.
These automated systems use machine learning to optimize pump rates and line speeds during the lateral trip to save time, horsepower and fluids on every stage. The superior response time of the automated pump-down units prevent unintentional pump offs that lead to costly fishing operations.
New perforating technology was recently launched that integrates the software-driven shooting power supply, data acquisition and switch software into a single wireline panel, such that the entire perforating process is automated. Each perforating stage program for the entire pad completion can be uploaded into the system prior to or during trip in hole.
Once pumped down to bottom, the wireline technician can simply push a button to start the automated perforating process. The system will check switches, arm guns, calculate winch speed and fire precisely on depth while pulling out of hole, without any manual input from the user.
Since the shooting power supply links with the data acquisition, the panel can automatically log and annotate perforation depths on the log record, which eliminates the manual shot confirmation. This real time shot verification, as well as the other various surface and downhole data channels, are also available to stream to remote monitoring dashboards.
The perforating panel calculates the ideal winch speed during the perforating process, which can be communicated in real time to existing automated winch controllers, meaning the technician could potentially focus on monitoring all activities rather than manually handling the winch. Over the past year, this technology has eliminated several of the failure modes caused by human error, such as shooting the wrong gun or off-depth perforations, overpowering and damaging downhole electronics and unintentional initiations due to inadvertent power application.
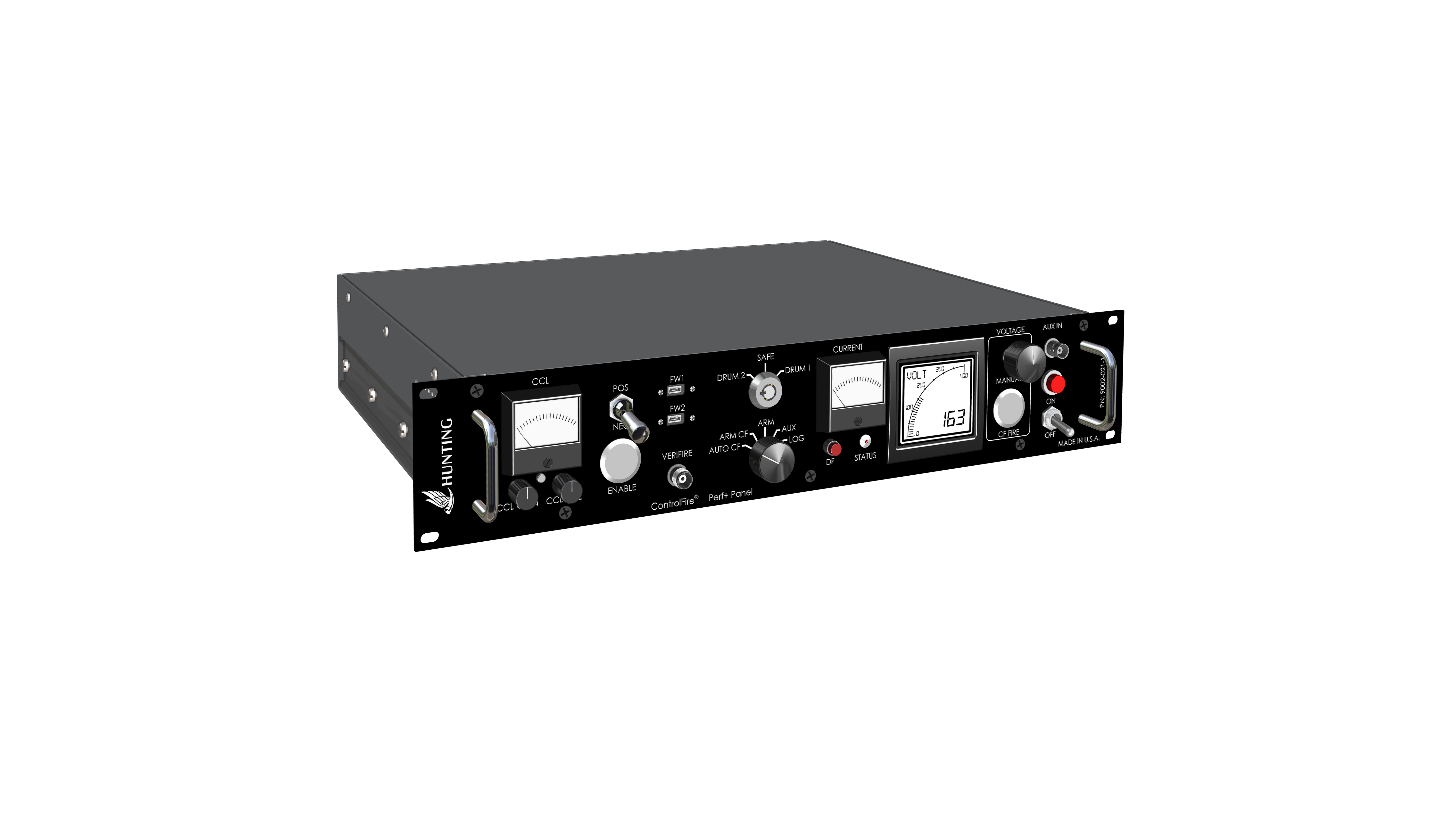
The path to full utilization
As around-the-clock pumping becomes more and more possible with automated technologies, the interdependency of frac and wireline processes becomes more pertinent. It is feasible for the digital valve and wellhead controllers used by frac teams to communicate with the perforating system and winch controller of the wireline unit.
Full plug and perf automation and continuous pumping involves collaboration among several stakeholders, from products providers to service companies. Ideally, compatible controllers will use machine learning to automate all valves, connections, winch, pumps, shooting panel and data acquisition so that all plug and perf processes are seamlessly integrated and run at maximum capacity.
Recommended Reading
US NatGas Storage Withdrawal Beats Expectations
2025-03-13 - Natural gas demand comes in slightly higher than usual, despite warming weather, in the Energy Information Administration’s weekly report.
BP Resets to NatGas as Energy Transition Takes a Backseat, CEO Says
2025-03-12 - BP CEO Murray Auchincloss said the company’s strategic shift will focus on natural gas and “the time has come for the Haynesville.”
Arc Resources to Supply Exxon with LNG Offtake from Cedar LNG
2025-03-11 - Exxon Mobil Asia Pacific Pte. Ltd. has agreed to buy 1.5 million tonnes per annum of ARC Resources’ LNG offtake from the Cedar LNG Project when the facility begins commercial operations.
ChampionX’s Chemical Application Breaks Up Waxy Blockages
2025-03-11 - The ChampionX system, called ParaClear, offers a custom solution based on site characteristics to move waxy crude through pipelines.
What's Affecting Oil Prices This Week? (March 10, 2025)
2025-03-10 - Prices were weighed down by concerns about economic growth, in part, because of more tariffs being imposed by the Trump administration, and OPEC+ reiterating that its production cuts would start unwinding in April.
Comments
Add new comment
This conversation is moderated according to Hart Energy community rules. Please read the rules before joining the discussion. If you’re experiencing any technical problems, please contact our customer care team.