As drilling technology evolves, so do expectations.
A half-century ago, drill bits were expected to wear out quickly. POOH, or pulling out of hole, was a frequent occurrence. Uncertainty about wellbore placement was common. Drilling was also a very hands-on activity, which raised the potential for accidents.
“The expectation 50 years ago was that it took a long time to drill a well,” Andy Hendricks, chairman of the International Association of Drilling Contractors and president and CEO of Patterson-UTI, told Hart Energy. “Drill bits didn’t last very long. You had multiple trips in and out. You would run multiple casing strings. Everybody accepted that it would take a long time to drill a well. I used to work in Venezuela when it took 420 days to drill a well.”
And as the types of wells the industry drilled changed, new tools were necessary.
“Fifty years ago, it was all about vertical wells, and then it became directional wells, and then directional turned into horizontal, and then all the tools for drilling those wells changed,” Hendricks said.

From the drill bit at the end of the bottom hole assembly (BHA) to the world of data and heavy computing to optimize well placement in real time, technology has progressed alongside changing drilling needs.
Sure, drill bits still wear out, but they are more durable than ever, as are other ruggedized components on the BHA. While-drilling technologies provide insights into downhole conditions to reduce the need to pull out of hole. Rotary steerable systems (RSSs) minimize uncertainties around wellbore placement.
Innovations like the iron roughneck and automated handling made operations safer. Artificial intelligence and the ability to quickly access data are helping to make drilling more efficient.
These and other technological advances mean drilling a mile a day in certain formations is expected, fewer people have hands-on roles in drilling operations, and driller’s cabins are starting to move away from the drill floor.
Drill bits

Bobby Grimes, reliability consultant at Baker Hughes, said drilling engineers “have a love-hate relationship with drill bits because they can make you a star or, if you tear one up or have issues with it, you can not look so good.”

A lot of technology goes into drill bits, from materials science for the metal and elastomer seals and cutting materials, to the engineering of the overall bit design, he said.
“We’re torturing drill bits. They’re the tip of the spear. We apply relatively high weights on the bit and RPMs (rotations per minute) to the bit” while drilling through various rock types for many thousands of feet, he said. “They have to be structurally strong enough to be able to handle these high loads and RPMs over long distances.”
Drill bits with tungsten carbide inserts—initially developed to drill the hardest formations—had their heyday in the 1970s and 1980s. The late ’70s saw the introduction of the polycrystalline diamond compact (PDC) bit, which uses industrially-synthesized diamonds for the cutting elements. PDC bits, initially capable of drilling only the softest formations, showed potential for directional drilling, which was taking off in the 1980s due to the advent of directional drilling with mud motors, Grimes said.

“Today, about 80% of all footage drilled is with PDC bits. They’re really the workhorse in the industry now,” he said.
In 2010, Baker Hughes introduced its Kymera hybrid drill bit, which combines roller cone and PDC technology into a single bit.
While-drilling technology
The advent of logging while drilling (LWD) and measuring while drilling (MWD) technologies gave drillers visibility into the wellbore, which sped up drilling operations and enabled the avoidance of hazards, André Trébucq, strategic business manager for Halliburton’s Sperry Drilling Services, said.
Before LWD and MWD, “there were two options. Either the drilling phase was completely blind, or it was extremely slow.”

If the goal was to not drill blindly, it was necessary to drill a portion, pull the drillstring out of hole, run measurement tools on a wireline, pull the wireline, and return the drillstring downhole to resume drilling, he said.

“If there’s multiple causes to do that during a well interval, then that takes several days, essentially. So, if we do make the decision to go ahead blind, then we don’t know if we’re drilling on target. We don’t know if we are in the correct formation. We don’t know if we’re near another well,” he said.
Sperry launched the first LWD technology in 1984 for gamma and resistivity logging, followed by porosity in tools followed, making it possible to see ahead of the bit in real time, he added.
“Look ahead” technology is a newer arrival on the while-drilling technology scene, Trébucq said.
Directional control
When RSS technology came along in the late 1990s, it brought benefits like better drilling performance, higher quality wellbore and more accurate well placement, Lei Fang, director of drilling services at Baker Hughes, said.

RSS, as an alternative to drilling with mud motors, reduces the risk of pipe sticking or buckling during drilling operations and improves hole cleaning, he said, because RSS makes it possible to continuously rotate and circulate.
“Due to better instrumentation, we have much more precise directional control in RSS that leads to a number of benefits,” Fang said. “You can drill a smoother wellbore, which translates to improved ROP as well.”
RSS and its ability to more precisely control the drilling trajectory also helps with better reservoir access, he said.
“Because you can better control the well trajectory, you can access thin sections of reservoir that otherwise would be very difficult” to maximize reservoir contact, he said.
The predecessor of RSSs was an automated vertical drilling system funded by the German government for use in deep geological research, Fang said. Baker Hughes further developed the technology, ultimately releasing the industry’s first RSS, AutoTrak, in the late 1990s. This advancement made the current era of geosteering possible.
Automation advances
The drilling industry has embraced mechanization and automation to improve performance and safety, Hendricks said, noting there has been a major effort of late to create software that will control drilling.
“There’s so many things that can go wrong” just setting the drill bit back on bottom, he said. “If you go too fast, you can damage the drill bit, you can break off a cutter, you can stall the motor out and tear up the elastomer on the inside of the motor, and nobody wants to have to trip out of the well when you’re in the middle of a three-mile lateral in West Texas,” he said. “Every time you make a connection, you want it to be repeatable in the best way possible. And automation of the existing drilling systems allows you to repeat the best process over and over again.”
Starting in the mid-’70s, the iron roughneck, which torques connections together, made it possible to remove some of the operational risks of drilling, although adoption was slow.
“That was a big breakthrough around the drill floor. Of course, it didn’t hit hard until the ’90s,” and only around 2004 “became normal,” said David Reid, NOV’s chief technology officer. “The iron roughneck got people’s hands off of drill pipe, and that was the big win, really saving fingers and lives.”
In 1982, Varco, which later became part of NOV, launched the top drive.
“That changed the industry. That changed everything,” Reid said.
The top drive created the ability to drill with a 90-ft stand of pipe, rather than the typical 30-ft sections, which sped up the drilling process. It also provided the ability to ream backwards, paving the way to cleaner well walls while continuing to build a long section.
“Drilling with stands was very new to the industry. So, from an efficiency standpoint, it was faster. But most importantly, from an applied torque standpoint, having the load of a big machine on top that could apply direct torque into the string allowed us to actually build the horizontal wells that we wanted to do and start doing directional. Without that, you wouldn’t have been able to do it,” he said.

Reid said the driller chair, unveiled in the early 1990s, was the first digital integrated control system for drilling operations.
“Before that, we were doing integrated control systems, but they were just push-button integrated stainless steel units. And then suddenly we had this drilling chair, which hasn’t changed that much since then,” Reid said.
The shift to alternating current (AC) control for rigs allowed software to control the rigs and made it possible to layer on automation, Hendricks said.
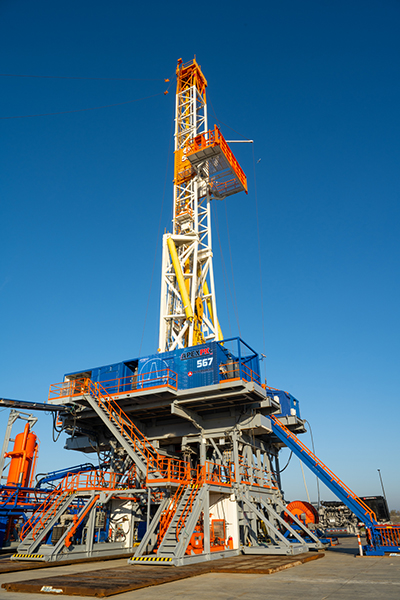
Rigs can now walk to relocate themselves on multi-well pads. And the speed at which that happens is faster than ever due to evolution in the rig structure design.
“Land rigs used to take two weeks to move. Now it takes two days from one pad to another, and it’s because of the design of the structure. It disassembles and goes back together easier than it used to,” Hendricks said.
Offshore changes
Offshore drilling operations have also become faster and safer and entered deeper waters as technologies arrived and evolved. The offshore drilling rig environment, where the drilling packages are fixed on the vessels, has lent itself to a continued evolution of mechanization and automation of riser pipe and drill pipe handling, for safer and efficient operations, Hendricks said.
The integrated column racker, a computer-controlled machine that tripped pipe without humans having to directly handle the pipe, came on the scene in the mid-1980s, Reid said. Automated pipehandling on deck soon followed, as did legislation in some countries, such as Norway, that required pipes up to 20 inches be handled by pipehandling systems rather than humans, he said.
Dynamic positioning came along in the 1970s, paving the way for drilling operations from drillships and semisubmersibles, rather than floating rigs that must be moored, Hendricks said.
“That was a huge upgrade,” he said.
Subsea blowout preventer (BOP) technology has evolved from purely hydraulic to combinations of hydraulics, electronic controls and data systems to make them safer and more reliable.
For quite some time, offshore drilling was limited to about 5,000 feet due to a couple of technology hurdles, including the need to be able to close a BOP in under a minute, Reid said.
“Use of fiber optics was actually what enabled it,” he said. In 1997, “The Diamond Clipper was the first to go out into the deeper water sphere.”
And fiber optics, combined with the modern-day multiplexer (MUX) which allows both analog and digital signals to travel along a communications pathway, opened up the possibility of drilling in 10,000 ft water depth, he said.
Remote control
As the industry continued to aim for safer operations and better performance, it automated activities, turned to industrial robots and developed more ways to carry out operations remotely.
At NOV’s Navasota, Texas, facility, the company has replaced humans on the rig floor with robots that “do all the work of humans, and they do it the way humans do,” Reid said.
The driller’s cabin has also been removed from the rig floor at the Navasota facility, he said.
“There’s no vibration distracting (them),” Reid said. “The first couple of days, the drillers were saying they missed the feel, and then on the third day they realized that the vibration and all the noise was actually bad for their focus.”
Over the last 50 years, Hendricks said, the technology that has come into the industry has made operations safer and more efficient.
“It’s allowed us to reach formations that we could never reach 50 years ago,” he said. “Fifty years ago, you could drill a deep vertical well but it was going to take a long time. Today, we can drill a vertical well pretty fast.”
And now horizontal drilling is also fast and efficient, achieving drilling rates of about a mile a day.
“I think, going forward in the onshore basins, you’re going to see more connections between what we do in drilling a horizontal well and how we design the hydraulic fracturing completion, how we make decisions on how we’re going to fracture based on drilling information and data and parameters that makes that process even more efficient and more productive, which can lead to improving the overall production of the wells.”
Recommended Reading
BP’s Eagle Ford Refracs Delivering EUR Uplift, ‘Triple-Digit’ Returns
2025-02-14 - BP’s shale segment, BPX Energy, is seeing EUR uplifts from Eagle Ford refracs “we didn’t really predict in shale,” CEO Murray Auchincloss told investors in fourth-quarter earnings.
DUCs Fly the Coop: Big Drawdowns from the Midland to Haynesville
2025-02-14 - The Midland Basin depleted its inventory of excess DUCs the most last year, falling from two months of runway to one during the past year, according to a report by Enverus Intelligence Research.
Shale Outlook Eagle Ford: Sustaining the Long Plateau in South Texas
2025-01-08 - The Eagle Ford lacks the growth profile of the Permian Basin, but thoughtful M&A and refrac projects are extending operator inventories.
Aethon Dishes on Western Haynesville Costs as Gas Output Roars On
2025-01-22 - Aethon Energy’s western Haynesville gas wells produced nearly 34 Bcf in the first 11 months of 2024, according to the latest Texas Railroad Commission data.
Lone Star State of Mind: Rockcliff Energy III Sets Sights on Texas Shale Assets
2025-03-05 - Rockcliff Energy III Executive Chairman Alan Smith and CEO Sheldon Burleson have their Quantum Capital-backed company’s Texas-sized ambition focused on the western Haynesville and the Eagle Ford.
Comments
Add new comment
This conversation is moderated according to Hart Energy community rules. Please read the rules before joining the discussion. If you’re experiencing any technical problems, please contact our customer care team.