
Oil and gas companies began looking at digital twins in earnest in the early 2010s. Growth is being spurred by the interest of the industry in tandem with the development of technology, said Miguel Valdez, who serves as vice president of growth at Kongsberg Digital. (Source: Shutterstock)
Early adopters such as BP, Chevron and Shell are expanding their use of digital twins—a virtual representation of physical assets—to shape decisions as simple as automating maintenance orders and as complicated as long-term plant facility roles.
Leveraging the exponentially growing amount of data leads to better and faster decisions. Digital twins can bring data together from across the enterprise. It can increase remote monitoring and eliminate bottlenecks in cross-department information sharing. And, with the growth of generative AI, it can take a set of data and run complex varying scenarios.
Oil and gas companies began looking at digital twins in earnest in the early 2010s. Growth is being spurred by the interest of the industry in tandem with the development of technology, said Miguel Valdez, who serves as vice president of growth at Kongsberg Digital.
“The combined annual growth rate for digital twins is 39 [%], 40%,” Valdez said. “So, it’s a significant market space that’s rapidly growing. Interestingly enough, there’s a significant investment from both the customer side and the technology development side.”
The cost savings, especially in terms of time, are significant. The ability to gather data allowed one client to cut an hour-long daily meeting with 30 to 40 people down to 15 minutes. The time to pull work order data also went from days to hours.
“You’re optimizing how you’re planning and executing work. You’re saving time and reducing the hours you’re paying to your third parties, your service providers,” Valdez said. “You’re optimizing the way you’re running and maintaining your asset that ultimately equates to improved uptime and production. That’s where the dollar and cents come from.”
Kongsberg Digital has launched its Kognitwin offering in the digital twin space. Kognitwin is the digital twin infrastructure for the various operations underneath, providing 2D and 3D virtual representations of industrial assets, equipment and vessels.
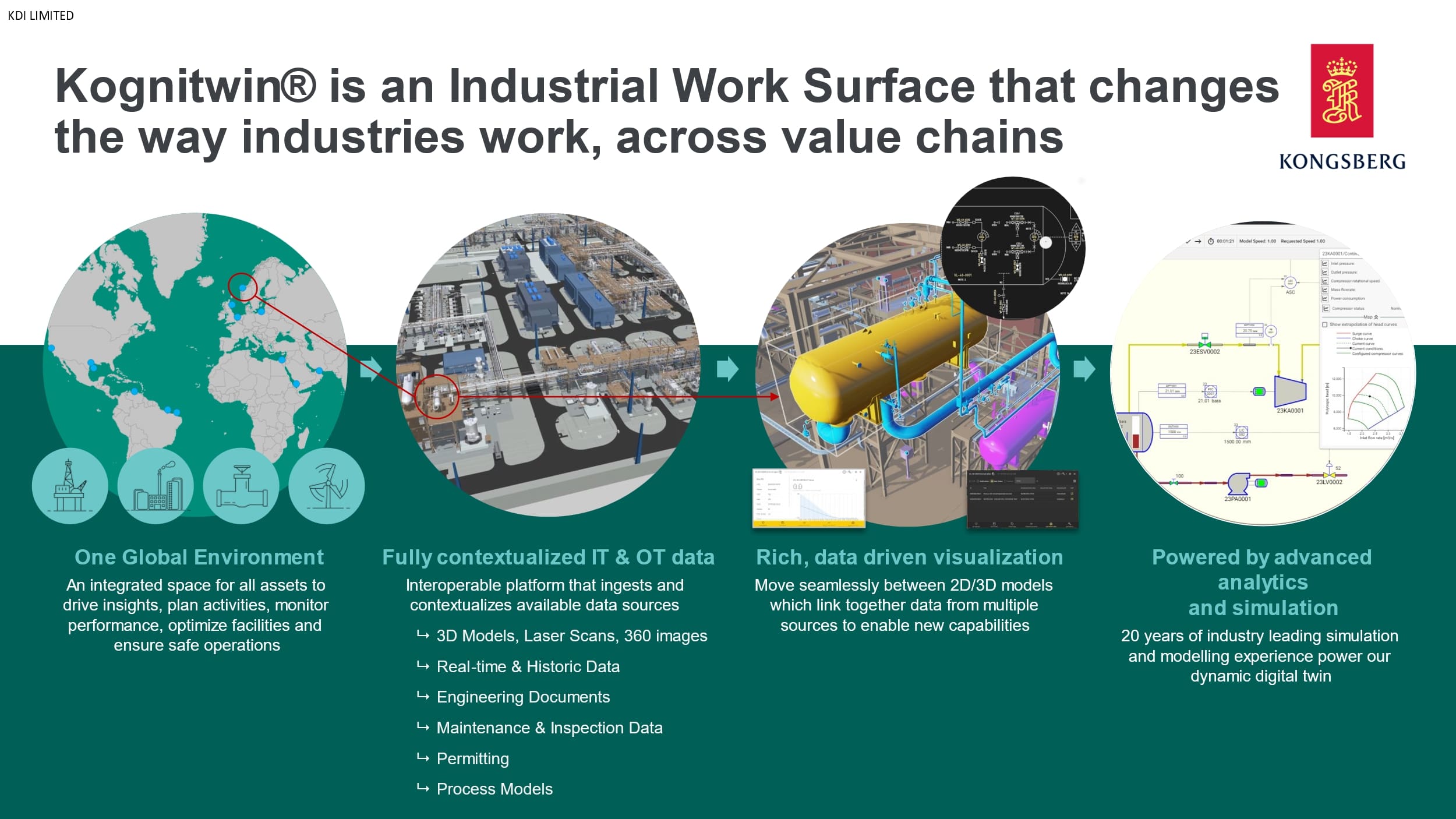
As artificial intelligence and machine learning continue to advance, so do the concept and capacity of digital twins across industries. Companies like Kongsberg Digital, IBM and Siemens are all in the digital space for the oil and gas industry.
Siemens describes digital twins in three spaces: the product digital twin, the production digital twin and the performance digital twin. Others divide the space into four areas: component, asset, system and process twins, with each area having its own focus of actions. Companies typically build from the component level up and out to the enterprise level.
Chevron took a methodical approach to digital twins. Between 2015 and 2017, the company explored digital and systems engineering approaches, looking to the aerospace and defense industry for inspiration. By 2017, the company was developing its framework for digital twins, identifying key components of analytics, modeling and visualization.
Chevron announced a partnership with MIT in 2020 to further refine its digital strategy. Between then and now, the company has begun rapidly scaling its digital twin deployment, with plans to have 13 of its 28 targeted sites completed by the end of 2024.
Keith Johnson, manager of digital engineering at Chevron, began his career in the company’s facilities design and construction group. Initially, the use of the digital twin was viewed as a way to cut labor costs for the Gorgon and Wheatstone projects in Australia, Johnson said.
“What became apparent was that if you digitize some of the workflows—automated things that were being done by people in engineering contract houses—you could reduce the burden from a cost perspective on the labor side,” Johnson said. “That became an objective in those early days.”
Two other forces soon moved into play, Johnson said. Agile was integrated into company operations, and Chevron launched the creation of its digital scholars program. Suddenly, the use of digital twins in defense and aerospace made more sense to Chevron.
“What were they doing in systems engineering that we weren’t doing in oil and gas?” Johnson said, mentioning Boeing’s use of what would eventually be known as digital twins. “You see these models that they're building and what they're able to do in predicting things and with how they advance their workflow. There's definitely something there.”
Digital twins are a game changer for the industry, especially in workflow management, Valdez said. What used to take hours or days can now take minutes. What used to require a project coordinator, an engineer and a service technician can now be done at the click of a button.
“When you have digital twins, you bring all those sources together,” Valdez said.
Digital twins are at the intersection of modeling, visualization and data, Johnson said. The concept can begin at a basic operational level and then build in layers, ultimately connecting all the functions in a processing plant to give the plant operator a chance to do everything from an early diagnosis of component performance to a fully integrated business decision.
As more systems and data are connected in one digital twin, it becomes easier to make more complicated decisions. For a company like Chevron, most of its digital twin use is currently in the descriptive and diagnostics end of the chart. Even at that nascent level, it’s cut early job walks and the time on turnarounds in certain plants, while maintaining on-site visual validation.
Early job walks are typical for handling the routine maintenance of a plant. Tasks typically involve cleaning and inspecting equipment, assisting in pipe and valve maintenance and performing the minor repairs typical of daily activities.
That’s led to operational efficiency for Chevron, but Johnson admits many traditional plant employees were skeptical before seeing the technology in action.
“Digital twin was used as a cuss word or a negative word in the early days because the traditional facilities engineers saw it as a fad,” Johnson admitted. “They thought it was going to be something that was going to be short lived, and there wasn’t really something there.”
Johnson’s team was only three people at the time, but they stayed the course. They had the headwinds of Chevron’s new commitment to technology. The scope of the digital twin in the early years, Johnson admitted, was fundamental.
“When we were looking at it, we were saying, ‘How are we going to analyze what we are seeing?’ So, this became the foundation inside of Chevron,” Johnson said. “There were no industry definitions. There was no alignment on what this meant for oil and gas. We just evaluated what we were being told and said, ‘This is the business problem that the digital twin is solving.’”
So, early in the implementation, that was demonstrated as monitoring the function of a pump, Johnson said. Eventually, that pump would be folded into the larger complexity of a system, an asset and the entire enterprise. Johnson compares the earliest iteration of this deployment to the Commodore computer, referring to the 8-bit home computer introduced in 1982.
“We said, ‘We’re building this first version of the Commodore computer, and we’re handing this out to 21 sites in 3 years. That became the plan. That’s what we got funded for, and this is what we are currently doing,” Johnson said. “We’ll have 13 of the 28 sites done by the end of the year… Combined with the (remote Agile) strategy, it’s really unlocked the value of digital twins for as many sites as possible in the same technology stack.”
The foundation of the digital twin work at Shell means putting “the right data in the right hands at the right time, in the right place,” Koren Dixon said during a recent broadcast about digital twin technology.
Dixon, a transformational change manager at Shell, said the company is moving the digital twin forward in efforts such as cleaning data and creating work packages as well as finding new ways to model data to improve decision making within the plant.
If the uses of Kognitwin can be compared to the 2011 movie Moneyball—the story of the underdog Oakland A’s using digital analytics to field a winning baseball team on the cheap—then Grant Christie would be Kongsberg Digital’s Peter Brand.
Christie was at Booz Allen Hamilton when NASA restructured its operations in the face of massive budget cuts. He saw easy parallels between aerospace and oil & gas. The challenge has been moving people from linear to digital thinking, Christie said.
“What’s been easy to apply it to is, ‘I need this analytic. I would like this simulation of a plant. I need an isolation plan. Wouldn’t it be great to digitize?’” Christie said. “We’re thinking about this in a very linear way. That’s what we currently do.”
The complicated part is stepping back and making more 3D decisions, ones that incorporate data of varying values and usefulness, Christie said. It’s bringing information across silos and into the larger context so that bigger decisions are better decisions.
Christie describes it as merging two frameworks: one focused on strategic metrics and the other on long-term goals. In that way, high-quality decisions are made.
“I can integrate data and apply digital analytics, and I can apply AI to enhance my alternatives or the analysis,” Christie said. “Then I can right click and turn that into execution, and then I can see the results of execution. Did what I tried have an effect, and did I affect it?”
Recommended Reading
Phillips 66’s NGL Focus, Midstream Acquisitions Pay Off in 2024
2025-02-04 - Phillips 66 reported record volumes for 2024 as it advances a wellhead-to-market strategy within its midstream business.
Pinnacle Midstream Execs Form Energy Spectrum-Backed Renegade
2025-02-03 - Renegade Infrastructure, led by Permian-centric Pinnacle Midstream developers Drew Ward and Jason Tanous, have received a capital commitment from Energy Spectrum Partners.
Argent LNG, Baker Hughes Sign Agreement for Louisiana Project
2025-02-03 - Baker Hughes will provide infrastructure for Argent LNG’s 24 mtpa Louisiana project, which is slated to start construction in 2026.
Williams Cos. COO Dunn to Retire
2025-03-13 - Williams Cos. COO Micheal Dunn was crediting with helping the company focus on a natural gas strategy.
CPP Wants to Invest Another $12.5B into Oil, Gas
2025-03-26 - The Canada Pension Plan’s CPP Investments is looking for more oil and gas stories—in addition to renewable and other energies.
Comments
Add new comment
This conversation is moderated according to Hart Energy community rules. Please read the rules before joining the discussion. If you’re experiencing any technical problems, please contact our customer care team.