
Franek Hasiuk (far left), a geologist at the Sandia National Laboratories, moderates a NAPE technical session Feb. 5 featuring Devon Energy’s Tony Pugliano, University of Texas at Austin’s Ken Wisian, Grounded Energy’s Galen Huling and Vallourec’s Andrew Cassidy. (Source: Hart Energy)
If Devon Energy geochemist Tony Pugliano had a magic wand to wave in energy, he would create areas where companies could produce oil and gas and extract critical minerals from brine with geothermal energy onsite—all at one location.
Galen Huling, a consulting geologist for Grounded Energy, would have everyone’s water tested to pinpoint lithium resources without going through data-gathering hassles experienced today.
And Ken Wisian, associate director of the Environmental Division of the University of Texas at Austin’s Bureau of Economic Geology, would cast a spell to advance more early commercial projects to prove the value and scalability of renewable energy projects like enhanced geothermal systems.
“We need to show everyone out there with actual producing systems it works,” Wisian said. “And with that, a potential for scale up is just immense.”
The aspirations may not be farfetched given exploration, drilling and other synergies have brought the subsurface oil and renewable energy worlds together in the quest for cleaner, reliable and affordable energy. Talk focused on geothermal, lithium and hydrogen when the experts gathered for a technical session at the NAPE Summit in Houston.
A revolution is already happening in geothermal, according to Wisian. Nearly all geothermal energy is from hydrothermal producing natural fluids that are hot, he said, but “the revolution is coming from producing your own geothermal system, engineering your own system and extracting the heat from the rock itself.”
Low temperature geothermal
Advances in oil and gas drilling technologies are being put to use in the geothermal sector, making it cheaper to drill to depths needed to access rock that is hot enough to generate power. Innovation has also enabled the conversion of power at lower temperatures, he said.
“Until now, you generally had to go west of the Rockies to find a hydrothermal system. Now there are projects kicking off east of the Rockies in nontraditional geothermal areas, including a handful of projects here in Texas,” Wisian said, adding that North America is the world’s epicenter of the geothermal revolution.
The lag time between oil and gas technology moving into the geothermal space used to range between two years and two decades, he said. But the metaphorical lightbulbs finally started coming on about five years ago when cross-sector technology applications emerged.
“The increases in drilling speed which reduced the cost, the ability to control fracture generation, to case through difficult geometries, those are probably the biggest single driver,” to enabling geothermal anywhere, he said.
Efficiency improvements on the generation side are among the drivers, he added, singling out work by Ormat Technologies. The company uses advanced binary cycle systems that can convert low-temperature geothermal heat into electricity.
“We think that geothermal anywhere is going to be competitive with other power sources pretty quickly. Conventional hydrothermal already is,” Wisian said.
Hot pursuit
Devon Energy is among the companies active in geothermal energy with investments in companies such as Fervo Energy, which applies distributed fiber optic sensing, horizontal drilling and multistage well completion to its geothermal wells.
“Internally, we’re also looking at geothermal characterization across the United States, but primarily in the western U.S.,” Pugliano said. “In addition to that, we are looking at some low temperature geothermal potential in our currently owned oil and gas assets, primarily in the Williston Basin and in South Texas.”
Whether the geothermal target is a sedimentary basin where most oil and gas reserves are located or a volcanic system depends on the goal, he added. For sedimentary basins, lower temperature geothermal systems can be used to generate power for localized oilfield operations. But when the target is generating grid power for a larger-scale plant, the focus is likely more on the Western U.S.
“We have a lot of potential, especially in places like Utah, Nevada, California, Idaho. We have some significant sources of heat in those places,” Pugliano said. “We do have less data. It’s a little higher risk. There’s a lot of unknowns, but I think there’s more upside for larger scale general potential and you’re getting into the superhot geothermal potential as well.”
Devon is also characterizing and evaluating critical mineral projects, primarily lithium, Pugliano said. The company is scrutinizing oilfield brines, the Salton Sea, Great Basin and the Smackover Formation in Arkansas. Lithium is used in battery energy storage systems and electric vehicle batteries.
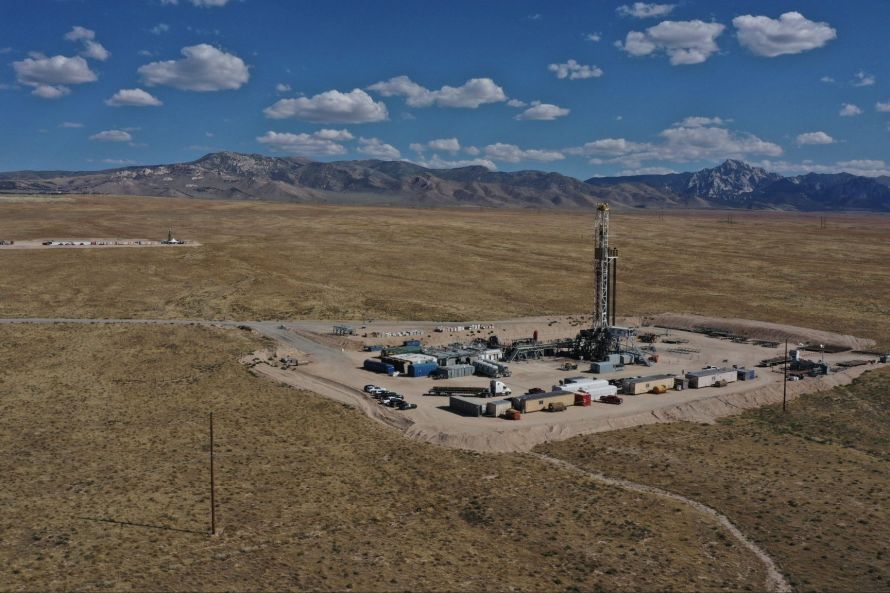
Lithium
Arkansas’ Smackover has attracted interest from critical mineral extraction companies and oil producers such as Equinor, Exxon Mobil and Occidental Petroleum. There, direct lithium extraction (DLE) technologies are being used to pull lithium from brine using ion exchange, solvent extraction or membranes. DLE is faster and takes less space compared to lithium extraction processes that use evaporation ponds.
Lithium concentrations, measured in parts per million (ppm), vary and impact economics. Each basin and each project have their own unique problems to overcome, Huling said.
PPMs between 150 and 200 are considered to be the lower economic limit, he said. However, one brine may have a high total dissolved solvent content that may take more effort to filter, process and reinject; while another may have high temperatures “so maybe you get geothermal plus lithium” to strengthen project economics.
A variety of geologic play types are available to chase, Pugliano said— including sedimentary systems or systems where warmer fluids are present, such as volcanic deposits.
Lithium concentrations are only one factor to consider when pursuing the resource. Understanding brine chemistry is essential in informing which DLE technology to utilize, Pugliano said. The charge and size of the lithium ion compared to other ions can influence DLE technology’s effectiveness, he said. “Ions of similar size to charge ratio to lithium like magnesium, calcium ... can be very problematic and can quickly deteriorate your resin or the material that you’re using for DLE.”
Hydrogen
As a global tubular solutions manufacturer, Vallourec’s subsurface expertise includes transferring CO2 and sequestering it underground. Its technology is also underground providing hydrogen storage as an alternative to salt caverns, which aren’t available everywhere.
“We have developed an underground hydrogen storage system that is fully automated, that can store up to 100 tonnes of hydrogen in a single cavity,” said Andrew Cassidy, hydrogen storage business development manager for Vallourec.
The company’s Delphy hydrogen storage system technology takes aim at the hydrogen infrastructure challenge.
“We’re diving into where you have green ammonia, e-methanol, liquid hydrogen. If you talk green, the challenge is renewables,” Cassidy said. “You need a constant flow of molecules going into that reactor when you synthesize, let’s say, hydrogen and nitrogen to make ammonia. Renewable power is not giving you that 24 hours, so you need to have a buffer storage and you need a lot of it.”
For Cassidy, the magic wand would unleash technology that makes it easier to extract natural hydrogen deposits.
Like natural gas, naturally occurring hydrogen can be tapped by drilling wells into reservoirs and pumping it back to surface where it is purified before use. The U.S. Geological Survey (USGS) in January released its first map identifying potential areas across the U.S. with geologic hydrogen deposits. Two USGS researchers have estimated the Earth may hold 6.2 trillion tons of hydrogen, according to media reports.
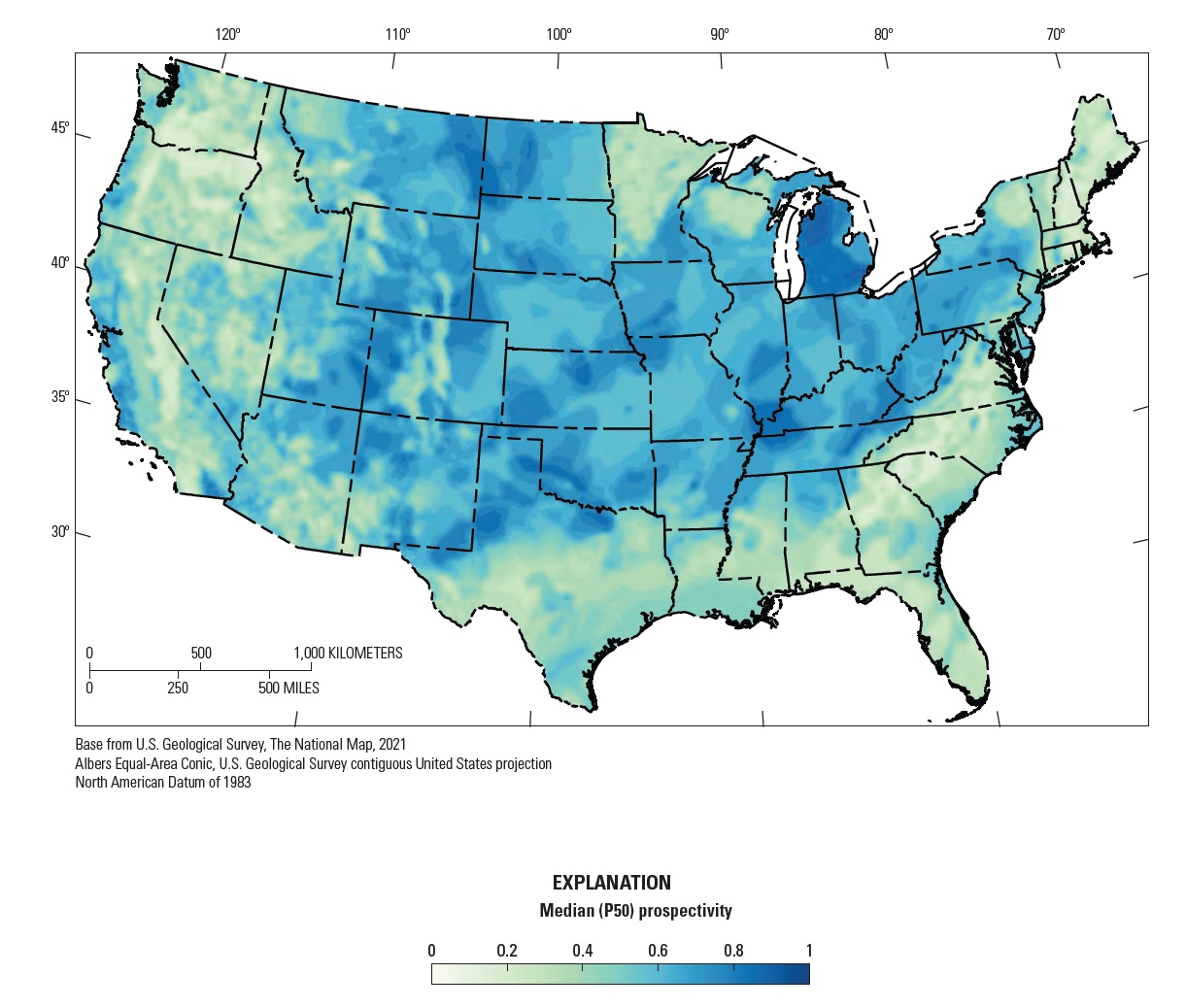
Currently, hydrogen is mostly made from natural gas using steam methane reforming but CO2 is also produced. Using renewable energy-powered electrolyzers to split water molecules into hydrogen and oxygen is among the cleaner hydrogen production methods but costs are high—about $4 to $7 per kilogram by Cassidy’s estimates.
“If you get that down closer to $1, that unlocks really the hydrogen market,” he said.
Recommended Reading
Exxon Slips After Flagging Weak 4Q Earnings on Refining Squeeze
2025-01-08 - Exxon Mobil shares fell nearly 2% in early trading on Jan. 8 after the top U.S. oil producer warned of a decline in refining profits in the fourth quarter and weak returns across its operations.
Phillips 66’s NGL Focus, Midstream Acquisitions Pay Off in 2024
2025-02-04 - Phillips 66 reported record volumes for 2024 as it advances a wellhead-to-market strategy within its midstream business.
Rising Phoenix Capital Launches $20MM Mineral Fund
2025-02-05 - Rising Phoenix Capital said the La Plata Peak Income Fund focuses on acquiring producing royalty interests that provide consistent cash flow without drilling risk.
Equinor Commences First Tranche of $5B Share Buyback
2025-02-07 - Equinor began the first tranche of a share repurchase of up to $5 billion.
Q&A: Petrie Partners Co-Founder Offers the Private Equity Perspective
2025-02-19 - Applying veteran wisdom to the oil and gas finance landscape, trends for 2025 begin to emerge.
Comments
Add new comment
This conversation is moderated according to Hart Energy community rules. Please read the rules before joining the discussion. If you’re experiencing any technical problems, please contact our customer care team.