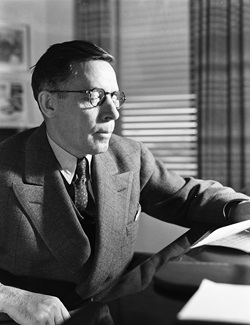
The legend goes that Erle P. Halliburton did not want to get into the hydraulic fracturing business at first.
The founder of the Halliburton Oil Well Cementing Co. was preparing both to retire and to take his company public when the potential came for Halliburton to pioneer hydraulic fracturing, and he initially saw risk and expenses rather than opportunity.
After some internal urging, Halliburton decided to invest in fracking with Stanolind Oil and Gas—the upstream arm of the Standard Oil Company of Indiana. They completed the first commercial job on March 17, 1949, in Oklahoma, helping set the course for the U.S. oil and gas boom of the 1950s and ’60s and, eventually, the shale revolution of today.
As Halliburton and the industry celebrate the 75th anniversary of commercial fracking, history shows that those small, initial frac jobs—consisting of a single 75 hp pump producing 3.5 bbl/min—led to millions of fracs performed over the decades. Intensive fracking, when combined with horizontal drilling and seismic and digital technologies, pushed the U.S. back into the role of the world’s biggest oil and gas producer. And the tools and technology continue to rapidly evolve.
“Outside of the industry, when I talk to generalist investors, people are totally clueless, and they think fracking is a brand-new thing,” said Marshall Adkins, head of energy investment banking at Raymond James and a former field engineer. “When I tell people it’s 75 years old, it just blows them away.”
Halliburton Chairman, President and CEO Jeff Miller said he is proud of how hydraulic fracturing produced surplus energy resources, enabled global development and lowered costs.
“Halliburton’s early involvement in the development of hydraulic fracturing methods, materials and equipment is an important part of our legacy,” Miller said. “It sets us apart from our competitors and propels us forward as we improve hydraulic fracturing execution and chemistry. Tight gas and shale would not be economically viable without hydraulic fracturing, and it accounts for a significant portion of production today.
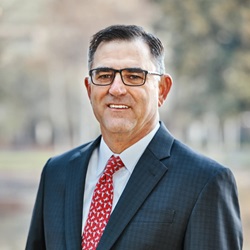
“Technological advances in horizontal drilling and stimulation transformed the industry and positioned the U.S. as a leader in the production of hydrocarbons. Tight gas and the advent of massive hydraulic fracturing treatments were significant game changers in North America.”
But it all began with Halliburton deciding in a post-World War II energy era that fracking was worth the money and effort.
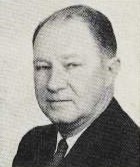
Tim Hunter, Halliburton chief technical adviser with production enhancement, credits the company’s then-chief engineer, Bill Owsley, as the chief advocate.
“Erle P. wasn’t necessarily eager to do the experimentation. The cementing business was the heart of the company, and it was an expensive venture to step into something risky,” Hunter said. “Owsley was the one who pushed it over center and eventually got Erle P. to buy in and convinced him to do it.
“I think that’s interesting. Here’s the big opportunity in front of you and the big fork in the road. Do you take the opportunity or not? Halliburton took it, and look where we are today.”
The beginnings
As far back as the 1860s, oil and gas wildcatters occasionally used explosives for fracturing. The first patent for an “oil well torpedo” was filed in 1865 shortly before the conclusion of the Civil War, but the use of explosives with nitroglycerin and other materials was not sufficient. The hydraulic portion of the equation was missing.
Stanolind engineering partners Floyd Farris and Joseph B. Clark are generally credited with developing the idea for hydraulic fracturing, a concept they introduced in 1946.
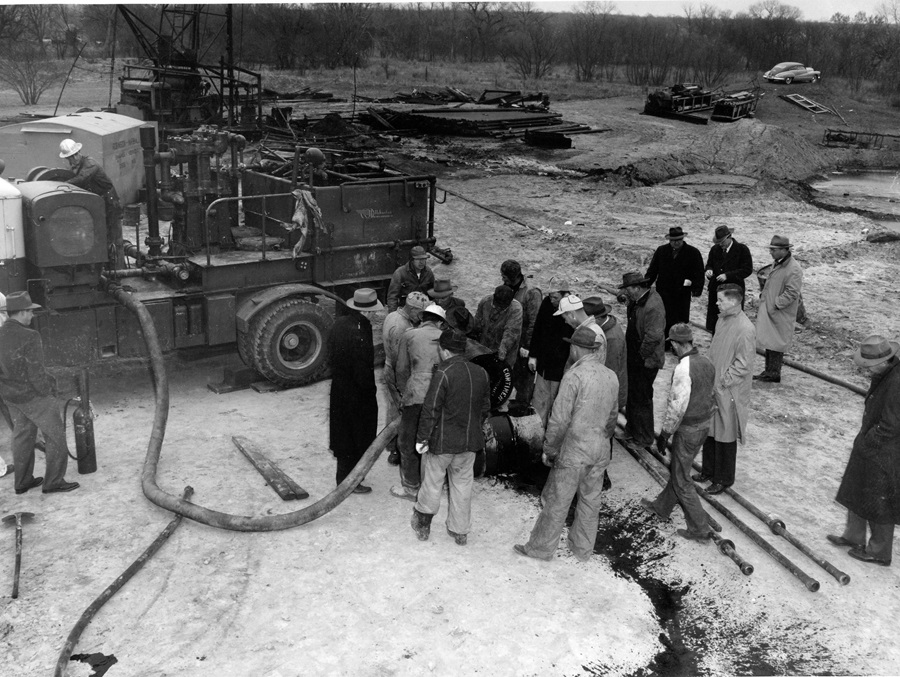
Their early experiments pumped gelled gasoline—essentially napalm—into wells at high pressures to crack the rock. Much smaller volumes of sand and other materials propped the cracks open. Of course, the early experiments were focused on conventional vertical wells and vertical fracs.
Early in the process, Stanolind secretly approached the Halliburton Oil Well Cementing Co., then commonly known as Howco, to develop the well stimulation process that would eventually become fracking. They partnered together for the first experimental fracture treatment in 1947 in the Hugoton Field in Kansas to produce natural gas from limestone from the Klegger #1 well, which was drilled to 2,400 ft.
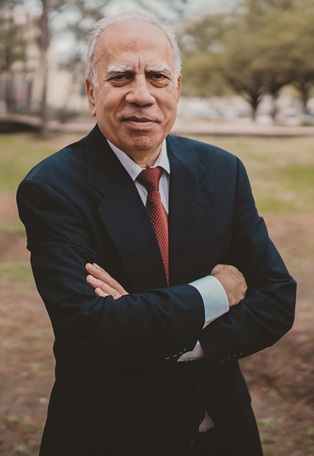
Mohamed Soliman, a University of Houston endowed professor of petroleum engineering and former Halliburton chief reservoir engineer, literally wrote the books on fracking, including "Fracturing Horizontal Wells." He also co-wrote a chronology of fracking milestones with B.W. McDaniel of Halliburton.
Soliman noted in his book that the first test well initially was considered a bust.
“At first, the treatment seemed to have failed; however, as there was disagreement as to the need to add a chemical breaker to the 1,000 gal of gelled gasoline carrying approximately 100 lbm of quartz sand, none was added. After approximately a week and some injection of fluid with a breaker chemical, the gel apparently had thinned sufficiently to allow the start of gas production, and they ultimately saw a moderately successful stimulation result.”
Other more successful test wells followed. At the end of 1948, Stanolind won a patent, and Halliburton received a three-year exclusive license to commercialize the hydraulic fracturing process, named “Hydrafrac.”
The first commercial frac job came on March 17, 1949, from Alma, Oklahoma, in the Velma Field in Stephens County. This, by no coincidence, was just a few miles from Halliburton’s home in nearby Duncan.
A second commercial well was immediately fracked in Archer County, Texas, about 100 miles south of Duncan.
The first Oklahoma well was 4,882 ft deep and was fractured with a single pump and about 150 lbm of sand.
“At that point, there was no such thing as a frac pump. We kind of begged, borrowed, cheated or stole from the cementing group to do that initial job,” said Shawn Stasiuk, Halliburton vice president of production enhancement. “We were using a steam-powered pump back then. It was around 75 hp. It was really small. It was more proof of concept. They were pumping at 3.5 bbl/min. We used oil or gelled gasoline as the base fluid back then. Obviously, pretty volatile stuff.”
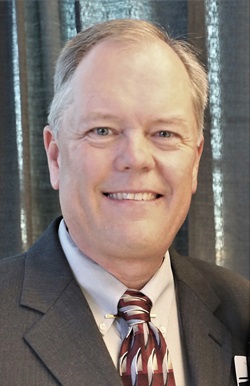
“Today, there would be a lot of HSE concerns with those sorts of things,” Hunter added.
The men on site were mostly wearing business suits, some smoking cigarettes.
“It was a little bit of a different time period,” Stasiuk said with a laugh.
The first Oklahoma frac cost about $900, and the first Texas frac was $1,000. That equates to roughly $25,000 combined today.
“It quickly showed that, yes, this technology works. It's viable, and the production uptick is fantastic,” Stasiuk said. “And, from there, it really kickstarted the industry. Halliburton is super proud to be a part of that first job. From there, things kind of just accelerated as we go through the decades.”
Fabulous ’50s and ’60s
Stanolind and Halliburton teamed up to complete more than 300 frac jobs during the following 12 months. The next year saw about 1,000 jobs, and then the final year of the exclusivity agreement added roughly 3,000 more.
“You could see the acceleration of the technology,” Hunter said, as production gains triggered faster adoption.
But fracking really took off after the exclusivity deal ended and other players joined the fray.
As Soliman wrote, the year 1953 also saw a significant leap forward when water and gelling agents replaced napalm and other petroleum products in the injection process.
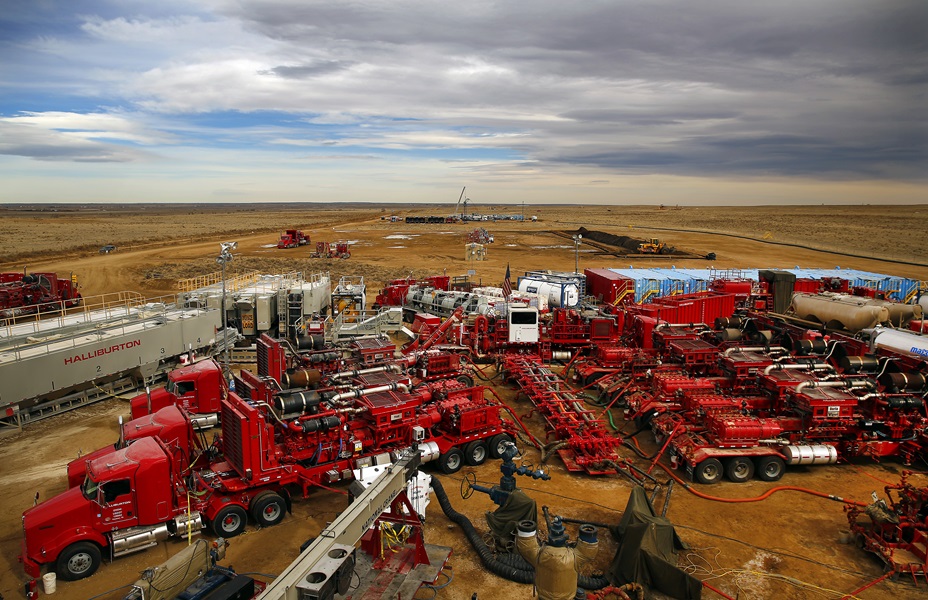
From the time of the first commercial frac in 1949 to the mid-1950s, U.S. crude production rose from 5 MMbbl/d to 7 MMbbl/d and eventually reached a then-record high of 10 MMbbl by late 1970. Hydraulic fracturing was just one component of the boom, but a key role player.
During 1953, the frac job count averaged about 2,300 per month, with other pumping service companies such as Dowell (later Dowell Schlumberger), the Western Co., and Cardinal Chemical among the top participants, according to Soliman.
At the time, jobs featured only 1,500 gal to 4,000 gal of injected fluid and just 0.5 lbm of proppant per gallon, typically at rates of up to 4 bbl/min.
According to Soliman, 1955 proved to be an early peak year for hydraulic fracturing with almost 45,000 frac jobs recorded, and treatment sizes averaging 7,000 gal. They mostly used a thin crude oil to begin the fracture growth, and a more viscous crude to carry proppant.
Still, fracturing remained quite rudimentary by today’s standards, and that led to the emergence of the “pump whisperers.”
“Every piece of equipment, pumping equipment, blending equipment, had at least an operator stationed on the equipment. Even until the early ’80s, we had people that would literally sit on top of a driveline or a pump, and they developed a sense of feel and hearing that, if something went wrong with the pump, they could tell you pretty close to what was wrong with it just from the experience and the vibration,” Hunter said.
“We called them the pump whisperers. But it took a tremendous amount of manpower to run spreads that way. And it was dangerous. Today, we’d call it the red zone,” Hunter said. “Back then, you'd see those guys sitting just happily up on top of a pump, and they may be pumping 12,000 psi [pounds per square inch] while smoking a cigarette, no safety glasses. That’s just how the oilfield was. It hadn’t matured into the safety-oriented environment that we have today.”
Going into the late 1950s and the early ’60s, the technologies evolved, Stasiuk said. The companies went from pumping 3.5 bbl/min to more than 20 bbl/min.
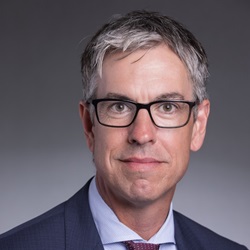
“What they also realized was the more volume they put in the ground, the more volume they would produce,” Stasiuk said. “Everyone was looking for, oddly enough, horsepower density, just like they’re looking for that today.”
That shift necessitated more specialized hydraulic fracturing gear, including more advanced frac pumps, which grew from 75 hp to more than 1,200 hp, and two or three pumping units on a site by 1963. By 1964, more than 400,000 Hydrafrac treatments had been pumped as most oilfield operators accepted the process, according to Soliman. By the late 1960s, Pan American Petroleum, formerly Stanolind, was leading high-injection fracs in Oklahoma with close to 250,000 pounds of proppant. That's a sizable jump in scale, although it pales to the several million pounds of proppant in most shale wells today, according to Soliman.
Stanolind was renamed Pan American before becoming Amoco, named after Indiana Standard’s American Oil Co. subsidiary. BP would merge with Amoco in 1998.
A National Petroleum Council study titled, “Impact of New Technology on the Petroleum Industry 1946-1966,” cited the two most significant technology advancements as water injection, or flooding, and hydraulic fracturing.
By the mid-1960s, hydraulic fracturing had spread internationally and offshore. The first hydraulic fracturing of an offshore U.K. well occurred in the North Sea West Sole well, east of the Humber estuary.
“We talk about speed of change in the business, but the speed of change from 1949 to the early 1960s was just a crazy amount of change,” Stasiuk said. “They were moving at light speed at that point in terms of the amount of innovation that was happening in the industry.”
Technology comes into focus
As OPEC flexed its muscle with embargoes, U.S. production faltered, and the so-called peak oil discussions escalated.
But the waning U.S. oilfield activity also allowed for greater focus on technological evolution.
The reality is that well into the 1970s, oilfield operators still understood relatively little about the rocks, perforating and other downhole conditions. The focus was on drilling technologies. Core studies were few with respect to fracturing stimulation.
“The ’70s and even the ’80s were filled with high-tech chemistry, heavy-gel systems and things that for unconventional wells would just kill the reservoir,” Hunter said. “That was one of the hurdles.”
Eventually, fracking became more analytical and scientific and, therefore, more useful.
The Gas Research Institute (GRI), founded in 1976, started contributing substantially to hydraulic fracturing research. In the late 1970s, Amoco fracking pioneers Ken Nolte and Mike Smith, among others, set out to study and better understand observed pressures during hydraulic fracturing treatments. At the annual Society of Petroleum Engineers convention in 1979, Nolte and Smith presented their conclusions in landmark papers, setting the basis for the fracturing net pressure analysis and its concepts.
In the late 1970s and especially during the 1980s, the industry saw the proliferation of large fracturing treatments placing more than 1 MMlb of sand in single-stage treatments into low-permeability formations, mostly gas-bearing sands, according to Soliman.
But the focus was still on vertical, conventional wells. The first horizontal well was drilled in 1921, but horizontal wells were not common until the 1980s and, even then, they were not combined with hydraulic fracturing.
George Mitchell, the “father of fracking,” began experimenting with shale fracking at Mitchell Energy in the 1980s with the goal of cracking the code on shale gas. It took until the late 1990s and early 2000s to truly solve.
In the 1990s, Chesapeake Energy founders Aubrey McClendon and Tom Ward pushed ahead with more modern fracking techniques in the Austin Chalk, but achieving success took time.
Soliman said he and others at Halliburton and elsewhere believed in the combination of horizontal drilling and fracking back in the 1980s, but the best techniques and shale formations were still unclear. He made his first presentation on the topic in 1987.
“I think one of the problems was it was coming from a service company when we started,” Soliman said. “The pushback was, ‘You are coming from a service company, and you guys are just trying to make money.’
“Once you create one fracture, you have to isolate it to create another fracture. So, there was an extra cost, and extra technology coming from a service company. All of that caused reluctance to use it,” Soliman said. “The technology now is so much better. You can create so many fractures. At the time, we were creating every fracture by itself and going to four to six fractures. So, it’s expensive.”
It took a producer to convince others.
“I give Mitchell Energy credit that they decided to apply it and see what happens,” Soliman said.
Digitalization and the shale boom
It may seem rudimentary now, but the pivot away from the slide rule and the adoption of handheld calculators to the oil patch in the 1980s proved greatly beneficial for efficiency.
Then came personal computers, digitalization and the development of microseismic technologies.
The shale boom wasn’t just the combination of intensive hydraulic fracturing and horizontal drilling, but also the additions of digital tools that improved seismic interpretation, said James West, senior managing director at Evercore ISI.
“We had to get better with seismic to understand where the reservoir was,” West said.
But that wouldn’t be enough. Drilling technologies also needed to improve to extract the best value form the reservoir, West said.
“We had to develop directional drilling tools that were better able to get into the reservoir to drill down and drill over and into the reservoir and had a diagonal or a curvature that could get us into that reservoir,” he said. “And then we had to test and evaluate where we should be fracking in that reservoir.”
Mitchell Energy did the first horizontal completion in the Barnett Shale in 1992, but it was not economic, nor did it utilize large, multistage fracking.
It would take Mitchell several more years to develop the slickwater fracking that would herald the beginning of the shale boom. As Soliman put it, success finally came when engineers decided to mimic the way water fracs were most successful in the Cotton Valley Sands of East Texas, which used massive volumes of water and high injection rates.
Mitchell Energy was sold in 2001 to Devon Energy, which further developed the combination of intensive fracking and horizontal drilling in the Barnett.
The shale boom, of course, would then spread throughout the country with land grabs in the Bakken, Marcellus and Haynesville plays before the tight oil boom was triggered with the Eagle Ford and the Permian Basin, now by far the most active basin.
From 1949 to the early 2000s, fracking really focused on “one or two stages of fractures and then not much else,” West said.
“When George Mitchell and his crowd started to experiment with shale reservoirs, which had to be fracked, and could be fracked in multiple areas in multiple zones, that led to what we now have as the shale revolution,” West said. “First, it was natural gas, and it’s now become more associated with oil. We’re doing 40 or 50 stages of fractures and pumping millions of pounds of sand into reservoirs and lots and lots of water and fluids into the same reservoirs.
“Fracking really took the U.S. market back to the place it is today as the largest producer of hydrocarbons in the world. And it’s probably only going higher, at least a little bit higher, from here as we continue to unleash American energy superiority.”
Continuing to evolve
The shale boom still seems relatively new, but it has evolved remarkably since the early shale years of the Barnett more than two decades ago.
“The scale has just gone up dramatically,” Adkins said. “There’s a gazillion evolutions along the way that I don’t think people really understand.”
Forty years ago, he said, a frac job might represent 10% to 20% of the total well cost. Now, fracking costs typically are two-thirds of the cost of the well. “The importance and cost of the completion and frac job has gone up massively compared to other costs related to drilling and producing oil and gas.”
Horizontal laterals grew to 1,000 ft or so, then to 1 mile, 2 miles and now even 4-mile laterals are common that include horseshoe shapes and other modifications. The industry moved from zipper fracs to simul-fracs to, now, trimul-fracs to complete as many wells as efficiently as possible.
Proppants have changed, as well. For a while, the industry used higher-cost ceramics, then switched to white sand, and then realized it could make do with plain in-basin sand.
Everything is exponentially more efficient, Hunter explained, “Back 35 years ago, the frac crew would leave the field camp at 3 a.m. They’d go out to location, rig up, you’d run until the late morning or early afternoon, tear down and, by the end of the day before sunset, everything was gone. That’s how fracturing was and continued for a decade or two. But today, the equipment hardly goes back to the yard. Multiple shifts rotate, and we pump around the clock. It’s totally different out on location than it was when I joined.”
A single well can require 25 million gallons of fluid and 25 million pounds of proppant, he said, in some cases requiring 90,000 hp. “It’s really like a factory that exists on location that pumps 24 hours a day. That’s what everyone’s goal is. It doesn’t shut down, and it stays there for long periods of time.”
Stasiuk elaborated: “If we look at what a frac spread is today versus what it looked like even in 2019, it’s entirely different. It is crazy to see just how fast the industry is changing right now. With electrification, you’ve got spreads running off power lines that no one would’ve believed back in the day was even a potential thing. You’ve got a ton of automation going into the equipment now. We just pumped our first fully autonomous frac job, which is a pretty crazy thing to see. That speed of change right now in the fracking industry is just something we’ve never seen before.”
Everything will continue to become more autonomous, more compact and modular, more electrified and more efficient, Stasiuk said, noting that more progress can still be made on lateral footage completed per day.
James West said he also anticipates better understanding and efficiencies to come for reservoir characterization.
“With understanding where to put the fractures, we’re probably in the fifth or sixth inning. We’re not fully there yet. The reservoirs are all different. We’re not quite sure why they change like they do,” West said. “So, we do too many stages of fractures, and some of those fractures don’t work. So, we’re wasting a little bit of money on those fractures. I think there’s still some optimizations that can happen there.”
Maybe 75 years is a long time to achieve this level of progress, but innovative ideas and economics and technological advancements all need to combine to bring things to reality. This is the natural evolution of technology.
Hunter illustrated this fact with something a mentor once told him, “Good design work looks obvious in the end. It’s not easy to get there. And a lot of people might say, ‘Well, I could have done that.’ But it’s not easy to see out the windshield; it’s easy to see in the rearview mirror.
“I think the shale development is exactly that.”
Recommended Reading
Not Sweating DeepSeek: Exxon, Chevron Plow Ahead on Data Center Power
2025-02-02 - The launch of the energy-efficient DeepSeek chatbot roiled tech and power markets in late January. But supermajors Exxon Mobil and Chevron continue to field intense demand for data-center power supply, driven by AI technology customers.
Phillips 66’s NGL Focus, Midstream Acquisitions Pay Off in 2024
2025-02-04 - Phillips 66 reported record volumes for 2024 as it advances a wellhead-to-market strategy within its midstream business.
Viper to Buy Diamondback Mineral, Royalty Interests in $4.45B Drop-Down
2025-01-30 - Working to reduce debt after a $26 billion acquisition of Endeavor Energy Resources, Diamondback will drop down $4.45 billion in mineral and royalty interests to its subsidiary Viper Energy.
Phillips 66’s Brouhaha with Activist Investor Elliott Gets Testy
2025-03-05 - Mark E. Lashier, Phillips 66 chairman and CEO, said Elliott Investment Management’s proposals have devolved into a “series of attacks” after the firm proposed seven candidates for the company’s board of directors.
EnLink Investors Vote in Favor of ONEOK Buyout
2025-01-30 - Holders of EnLink units voted in favor of ONEOK’s $4.3 billion acquisition of the stock, ONEOK announced Jan. 30.
Comments
Add new comment
This conversation is moderated according to Hart Energy community rules. Please read the rules before joining the discussion. If you’re experiencing any technical problems, please contact our customer care team.