
Exxon Mobil unconventional operations in the Permian’s Midland Basin. (Source: Exxon Mobil)
As Exxon Mobil boosts Permian Basin recovery and lowers drilling and completion (D&C) costs, the U.S. supermajor could look to target projects in the basin’s emerging secondary benches.
The Spring, Texas-based company is also deploying its own secret ingredient to ramp up recoveries: Its custom-made proppant is booting EURs by 15%.
Exxon Mobil is also seeing secondary Permian intervals—including the lower Wolfcamp benches, Mississippian benches and the Jo Mill Formation—become “highly economic” with lower drilling costs, senior vice president Neil Chapman said during the company’s Dec. 11 corporate update.
Permian operators searching for locations are landing laterals in less developed benches like the Wolfcamp D, the Dean sandstone, the Barnett Shale and the Woodford bench, according to Texas Railroad Commission (RRC) data.
Exxon is in full-scale Permian manufacturing mode after completing a transformational $60 billion acquisition of Pioneer Natural Resources in May.
Permian production averaged 1.4 MMboe/d during the third quarter, including Exxon’s heritage Permian production and the Midland Basin output added through the Pioneer deal.
Exxon aims to grow Permian production to 2 MMboe/d in 2027 and 2.3 MMboe/d in 2030.
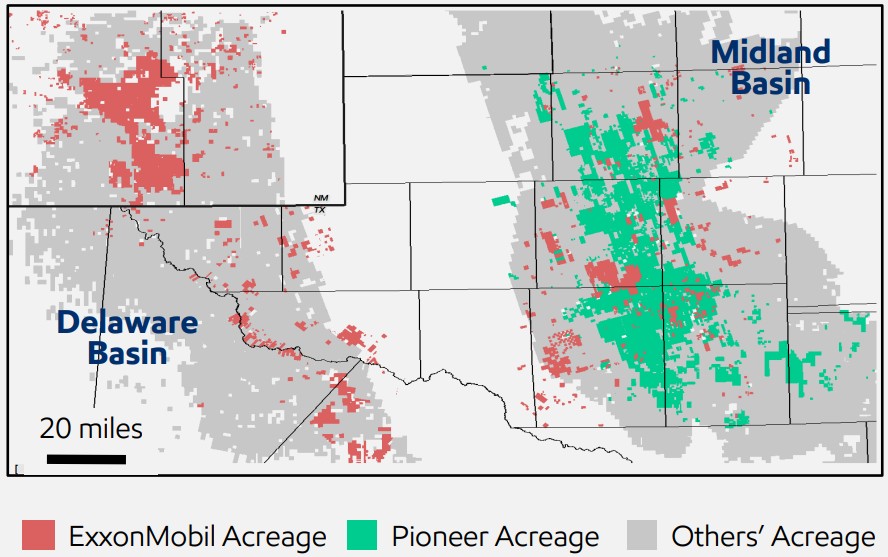
Several trends in the Permian are helping Exxon spend its money more efficiently and bring down D&C costs per lateral foot.
The massive, contiguous acreage block Exxon picked up through the Pioneer acquisition enables the company to drill fewer wells with longer laterals.
“If you don’t have large acreage, you can’t drill 4-mile laterals,” Chapman said. “The capital efficiency saving of drilling one 4-mile lateral versus four 1-mile laterals is enormous—but you have to have the resource and the acreage to do that.”
Exxon has drilled among the longest laterals in the Permian Basin, including 4-mile laterals on its legacy acreage in the New Mexico Delaware Basin.
After closing the Pioneer deal, Exxon plans to drill the first 20,000-ft lateral on Pioneer’s Midland asset before year-end.
Exxon said that drilling longer laterals reduces surface and drilling costs by at least 25%.
Changes to Exxon’s multi-bench “cube” designs also help the company spend more efficiently, Chapman said.
In the past five years, well spacing and frac sizes have been tested and tinkered on across different parts of the Permian Basin.
“The cube design should not be static,” Chapman said. “It shouldn’t be the same for all benches, and it shouldn’t be the same for all geographies.”
Exxon’s modern cube design leverages “unique” well spacing patterns, longer laterals and the company’s patented lightweight proppant technology.
“This latest cube design that we have is reducing the number of wells by 20% for the same resource recovery,” Chapman said.
RELATED
Exxon: Longer Laterals, Cube Well Design Lowering Permian Costs
Proppant tech
Exxon is seeing improved Permian well economics by rolling out a custom-made lightweight proppant from its downstream business, which is made with petroleum coke.
Lightweight proppant technologies aren’t new to the unconventional space, but predecessors have been too expensive to widely deploy, Chapman said.
“We’re manufacturing this specific type of coke in our own refineries,” he said. “That’s what makes it different and that’s what lowers the cost.”
Exxon is using a blend of sand and lightweight proppant in its Permian wells. Sand is “perfectly acceptable” to meeting the functional needs close to the wellbore, Chapman said.
But sand gets too heavy to make it to the furthest ends of the laterals. So, Exxon engineers designed a proppant light enough to travel the full length of the lateral—while maintaining the strength needed to keep fracs open.
“We’re still in the early stages of deployment,” Chapman said, “But… we’re seeing up to a 15% increase in recovery so far.”
The company’s lightweight proppant pilot was conducted on around 50 Permian wells—mostly in the Delaware and northern Midland basins, or areas with higher Exxon Mobil working interests.
Exxon is encouraged by the early results. The company plans to deploy lightweight proppant on more than 200 Permian wells in the next 12 months.
At peak deployment, Exxon forecasts call for up to 2 million tons of lightweight proppant per year. However, scaling up lightweight proppant production will take time and investment in Exxon’s refining operation, Chapman said.
RELATED
Recommended Reading
Occidental to Up Drilling in Permian Secondary Benches in ‘25
2025-02-20 - Occidental Petroleum is exploring upside in the Permian’s secondary benches, including deeper Delaware Wolfcamp zones and the Barnett Shale in the Midland Basin.
Exxon Sits on Undeveloped Haynesville Assets as Peers Jockey for Inventory
2025-04-09 - Exxon Mobil still quietly holds hundreds of locations in the Haynesville Shale, where buyer interest is strong and inventory is scarce.
Early Innings: Uinta’s Oily Stacked Pay Exploration Only Just Starting
2025-03-04 - Operators are testing horizontal wells in less developed Uinta Basin zones, including the Douglas Creek, Castle Peak, Wasatch and deeper benches.
Antero Stock Up 90% YoY as NatGas, NGL Markets Improve
2025-02-14 - As the outlook for U.S. natural gas improves, investors are hot on gas-weighted stocks—in particular, Appalachia’s Antero Resources.
Oklahoma E&P Canvas Energy Explores Midcon Sale, Sources Say
2025-04-04 - Canvas Energy, formerly Chaparral Energy, holds 223,000 net acres in the Anadarko Basin, where M&A has been gathering momentum.
Comments
Add new comment
This conversation is moderated according to Hart Energy community rules. Please read the rules before joining the discussion. If you’re experiencing any technical problems, please contact our customer care team.