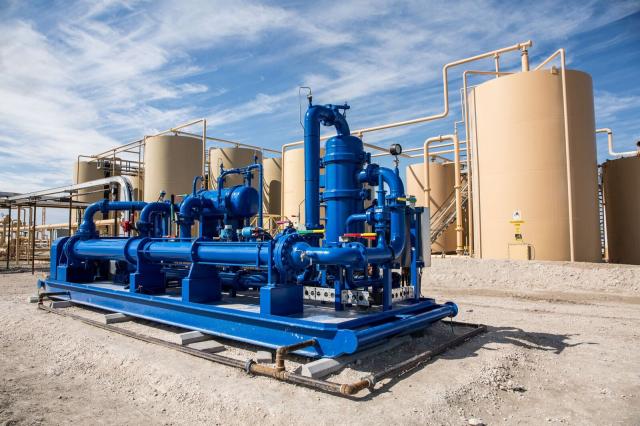
NOV’s Waterwolf dynamic oil recovery system reclaims oil and suspended solids from produced water in a single stage of treatment. (Source: NOV)
Editor's note: A version of this article originally appeared in E&P magazine. Subscribe here.
It is not difficult to see why oil and gas producers are of two minds with regard to water. For the offshore explorer, it is an ever-present, perpetual motion obstacle separating technology and the prize. The onshore producer calls water both friend and foe, depending on the timing within the development process it is encountered. You don’t want to see it downhole when you are expecting a bigger bounty, but in the same beat, water plays a crucial role in the extraction of discovered hydrocarbons, especially when dealing with tighter, unconventional formations like those that exist in the shale plays of Texas, Oklahoma, Pennsylvania, Wyoming and Ohio, among others.
Water management has always been part of the business in one form or another, but in recent years, as developers moved to extract oil and gas from more remote locations of more arid areas such as West Texas and southern New Mexico, water requirements became a higher priority. Volumes are pumped downhole for fracturing operations, and volumes are reclaimed from those same operations. For operations in the Permian Basin, an average of 4 bbl of salt-ladened water is produced for every barrel of oil. Those briny volumes have to go somewhere. Historically, the solution has been to pump the wastewater back into the earth via a network of disposal wells. However, more and more states are looking closely at the disposal process and its effects on the subsurface, linking the procedure with increased seismic activity and earthquakes in regions such as Oklahoma and Texas. According to the U.S. Geological Survey, earthquakes in West Texas and New Mexico measuring at least 2.5 on the Richter scale have tripled to more than 60 per year.
Texas is reviewing its disposal well permitting process and some expect more onerous policies to be put in place to make drilling new disposal wells a difficult proposition. That doesn’t bode well for the booming West Texas oil patch, where the number of rigs drilling for oil and gas has more than doubled since 2016, according to the Baker Hughes rig count. Enough wastewater is produced from the Permian Basin annually to cover the state of Rhode Island nearly a foot deep. Water handling has added as much as 25% in some cases to overall lease operating expenses. That kind of hit to the wallet is bound to get attention. When disposal wells are pulled out of the equation, operators are forced to either truck the water out of the region for disposal or consider investing in a recycling and reuse project.
Recycle and reuse has become the solution of choice for many in the Permian. Operators like Pioneer Natural Resources, which founded Pioneer Water Management in 2014, have led the way on reuse. The company is building a water pipeline network that will run 100 miles north-to south across Pioneer’s acreage utilizing 30-in. to 36-in. diameter pipe. It will include fiber-optic cable to support field communications and feeder lines that connect to non-potable water sources, such as contracted municipal wastewater plants. Construction will continue this year in a phased approach. The system will consist of up to 20 water subsystems branched from the mainline, connecting 125 to 150 strategically placed double-lined storage ponds that will support hydraulic fracturing operations and recycling efforts in the Midland Basin. Additional operators also have embraced water management as a full-blown midstream business—Apache and Occidental, among others.
The emerging market hasn’t gone unnoticed by investors. More cash is being moved into the market via direct investments in larger companies like Select Energy Services or even smaller niche players like Clean Chemistry, a bacteria control and solids separation company, which received an infusion from Black Bay Energy Capital last summer.
Water to burn
Hydrozonix started its life as a licensee of an ozone-based technology that it then tweaked and offered to the oil field as part of a water treatment package to prevent scaling—the formation of hard water mineral deposits. However, the use of chemical scale inhibitors and the practice of blending water took care of a lot of what the company was in a position to provide. It prompted the company to look into additional technologies and diversify more broadly throughout the life cycle of oilfield water.
“You have roughly 500 million barrels of produced water generated from the Permian Basin per month,” said Mark Patton, president of Hydrozonix. “Your total demand for completions is only 200 million barrels per month. So even if you started recycling, you’re never going to recycle 200 million barrels per month. You never have all of the produced water at the right locations at the right time. Maybe a really aggressive program could get you 100 million or 150 million barrels per month, but you would still need some fresh or brackish water to supplement your source.
“But there is still excess water you have to manage that is not going into a recycling program. What do we do with that? Right now, treating to discharge to make it for agricultural reuse is a little bit expensive, though people are working on bringing that cost down. The next cheapest thing we saw that could be done was evaporation. That was the reason for the Hydroflare.”
The Hydroflare system was designed for wells in locations where gas-gathering systems do not exist and where produced water costs are high. The system burns gas that would normally be flared to evaporate flowback and produced water so it does not have to be hauled away for disposal. Solids left behind by the evaporated water are collected and conveyed to easily moved receptacles. It can help operators meet flaring reduction goals while simplifying produced water management at remote well sites. The origins of Hydroflare can be traced back to an unnamed client that had some remote wells with no access to infrastructure, which resulted in the company having to truck all of its water out of the area. The client was flaring gas as well because it wasn’t cost-effective for it to connect those wells to the gas-gathering system.

“They needed a solution,” Patton said. “If you look at the regulations rolled out under the Obama Administration, you can flare for a certain period of time, but then you had to stop and look for an alternative use. Using an evaporator that would run on that same flare gas was considered an approved alternative use. So that same gas that you’re flaring could be used for evaporation. You are still going to have dirty salt, some metals and scale mixed in that you would have to dispose of, but it would be a significantly lower volume than what you had.
“You could also not fully evaporate it; just keep it a slurry and use that as a kill fluid or as part of your drilling brine. That was a potential reuse for that material,” Patton said.
The client eventually sold the remote field and no longer had the excess water burden. The Hydroflare is idle on location in the Permian right now where Hydrozonix is conducting preliminary testing with it.
Hydrozonix’s chief offerings reside in oxidation, aeration and disinfection of produced water, or as the company calls it, the HZO trio. Its HYDRO3CIDE system uses ozone technology to treat produced and flowback water instead of liquid biocides for a chemical-free treatment process. As the company observed clients treating for bacteria throughout their entire water systems, they recognized a way to move into the production side of the business.
“The automated ozone system takes the surrounding air, strips out the oxygen and makes ozone in real time,” Patton said. “We knew we could do that and drop people’s cost. We also saw that the same system could be used in recycling programs. So we started rolling out that new product.
“Once you treat water and you decide you’re going to reuse it or recycle it, you store it in big volumes. Storing it in big volumes and just leaving it sit for a long period will allow bacteria to re grow. Aeration systems became a nice, simple way to distribute air. The oxygen in the air acts as a mild oxidizer and it starts to maintain the fluid disinfection. It provides very little additional treatment, but it prevents the bacteria from growing out of control. Think of it as preserving your treatment.”
He continued, “So we started to see that if you optimize what happens at the wellhead, tank batteries and gun barrel systems, you have eliminated most of your oil and solids, so we were able to add an automated treatment system that can save clients at least 60% in their chemical program for bacteria control. If we aerated that water after it has been treated by oxidation, that becomes your whole recycling program.”
After ozone treatment and aeration, the third leg of the trio is an On-The-Fly oxidation system that disinfects water and removes iron and sulfides without chemicals that can be incompatible with frac fluids.
Hydrozonix has 15 installed systems right now, which is just over 500,000 bbl/d of capacity. In addition, the company has 12 portable trailers that are used for on-the-fly disinfection.
“We build two to three systems per month at our facility in Greeley, Colorado,” Patton said. “We tried to build at our facility in Odessa [in Texas], but we quickly outgrew our operations there. It is very difficult to find skill trades in the Permian right now. We were having difficulty finding the right people … and when you do find them, they are expensive. We soon realized that we were flying people into Odessa from Colorado already. It just made sense to move our assembly plant to Colorado. We did that back in May [2018]. We are also modernizing our old fleet throughout 2019.”
More than 90% of the company’s business resides in West Texas; however, discussions are underway with a number of companies in the Oklahoma Scoop and Stack regarding recycling programs.
Satellite imagery
A picture can change dramatically solely based on one’s point of view. A tree in the distance can look 2-D until a person is either below it or above and sees its complete 3-D footprint. Elevation also can change perspectives, making the difference between seeing a fence and what lies on the other side.
Sourcewater is using perspective to gain a competitive advantage when it comes to oilfield water intelligence and overall operator activity. The company is using machine learning and computer vision analysis of very current satellite imagery of the Permian and other plays to detect every single frac pit and every single well pad to predict who is going to be drilling where and when.
“Today, everybody does that by looking at drilling permits,” Sourcewater CEO Josh Adler said. “We did a study on this and were shocked to discover that the average drilling permit in Texas is filed 16 days after the well has already been drilled. So if you’re in the business of trying to sell things to people who drill and you’re trying to figure out whom to sell to based on when those drilling permits come out, you’re not doing too good.
“Of course, a lot of business happens between companies that already have established relationships. But if you want to expand your business beyond the people you already know that tell you what they are going to do before they do it, your only option today is [to look at] drilling permits … and drilling permits are essentially useless.”
Sourcewater looks at new satellite imagery of the Permian Basin every five to seven days and sees it within 24 hours of the images being taken, basically reviewing activity that occurred yesterday. What are they looking for? Drilling pad construction. Most operators start construction of a drilling pad upward of three months prior to drilling, a full 12 weeks, give or take, before the rig arrives on site and well before the permit is filed.
They also look for frac pit construction and water levels. Again, pits are built and filled ahead of the job and, depending on the size of the pit, it could take several weeks to fill. In Texas permits are not required to construct a freshwater frac pit, so there is no permit trail to follow if a company is interested in collecting those data. Satellite imagery also can give the company a good idea about the amount of water in an individual pit, plus or minus 20%. All of these data get plugged into Sourcewater’s Oilfield WaterMap intelligence platform, a mapping and analysis tool that reveals water assets, development trends, market prices, business activity and ownership intelligence.
“It is useful for finding out where and how much water is available in an area,” Adler said. “We match those locations up with leases and owner records to see who owns that water, who we should contact to see if it is for sale or if it’s available, how much is there … and it all ties together in the same online platform where you can analyze all of this in relation to where the future drilling is happening.”
He continued, “What are the water production levels for the existing oil and gas wells in this area? How much produced water is coming out of the ground? Where are the disposals? How much disposal capacity is there? How much disposal capacity is coming based on the permits that have been filed but are still undrilled? How far are operators of these leases sending their water for disposal now? If they are sending it a long way that means they are probably paying a lot. So all of these data go into one geospatial mapping platform, and we put all of these analysis layers on it that allow you to make better decisions about how to plan your water infrastructure. Is there excess available infrastructure near your project? If you sell disposal or water, should you be investing in building more disposal or pipelines or capacity in a given area? Where are the best places to invest in that? Who are the operators that are going to need it? And how much would they probably be willing to pay? We are really creating a system to answer all these types of questions in one place.”
Sourcewater started about five years ago as a marketplace for water sourcing, recycling and disposal for the oil and gas industry—a place where operators could trade and reuse produced water and excess freshwater with each other, and where surface owners, treatment facility owners and disposal well owners could sell their excess capacity into the market. It was kind of like Expedia for water services.
In the last year, the company has added on to and repositioned itself as an oilfield water intelligence platform. Today, the water marketplace, which is getting close to 10,000 water and disposal for-sale listings in the Permian Basin alone, is a subcomponent of the overall oilfield water intelligence platform. “The value of the marketplace is that it feeds price and availability information and trends into our intelligence platform,” Adler said.
“We recently acquired Digital H2O, which was really the only other company in this space,” he continued. “What Digital H2O is known for is that they take the well reports from the state of Texas for commercial disposal wells and basically use those to visualize the logistics, flow and utilization relationship between every operator lease and every commercial disposal well in Texas. So you can see exactly which leases send water and how much to which disposal wells; the utilization levels at those disposal wells; and which leases send water to which disposals so disposal companies can see who is doing business with my competitors, how busy my competitors are, how much water is coming from these leases and where is it going. It’s a piece of the second Big Data contributor to our water intelligence platform, which is all kinds of government record datasets—the Texas Railroad Commission, Texas Water Development Board, drilling permits, producing well permits, initial production reports, flow rates from water wells, the water quality from the water wells, the surface water permits—there are just so many of these datasets.”
Sourcewater is looking to add a new suite of digital tools to its platform this year to help with the planning of water transfer projects and pipeline projects. The suite is designed to make it easy
for companies to optimize the route, pump sizing and pump placement for their water pipelines and transfer lines right on the map.
“There is a lot of overspending when it comes to pump capacity for moving water … and on power,” Adler said. “That doesn’t need to be wasted. So this set of water project planning tools on WaterMap will allow people that plan and move water to do it much more efficiently.”

The company is focused on the Permian Basin, both Texas and New Mexico, but has some coverage in North Dakota due to the Digital H2O acquisition. Spreading coverage to other basins is in the offing as well as increased use of satellite imagery, focusing on earlier detection of projects and higher resolution visuals to build a more accurate dataset.
Bubbling to the surface
Select Energy Services Inc. is a water management company that provides services throughout the life cycle of oilfield water, from sourcing to disposal. According to the company, its late 2017 merger with Rockwater Energy Services, a provider of water management solutions, positioned Select as a leader in the market, especially around North American shale.
The company’s technology slate includes its AquaView monitoring, automation and information platform; automated proportioning systems for dynamic and precise mixing of fresh and produced water; and chemical-add trailers that allow injection of a suite of chemicals during water transfer and water recycling. This suite of technologies and the associated information and data are managed and accessible through real-time customer portals on AquaView.com and SESTreatment.com. Select also offers a comprehensive package of frac water treatment services, and these service offerings and technologies continue to evolve as the company explores better, faster and more efficient ways to solve its clients’ water issues.
In addition to providing produced water treatment services for reuse in fracturing, Select provides chemical additives to enhance downstream properties.
“We address issues, such as wellbore and surface facility maintenance, by adding corrosion or scale inhibitors or biocides using our chemical-add trailers,” said Cindy Peña, senior scientist at Select Energy Services. “The SESTreatment.com platform is a solution for operators and frac providers to monitor additives and correlate chemical addition data with changes in well performance. As a premier in-basin manufacturer and distributor of production, completions and specialty chemicals, we have the expertise to properly analyze customer needs and apply the most effective chemical additives based on water quality.”
Peña continued, “We’ve also been exploring nano-bubble technologies. When larger microbubbles are applied to water, a milky froth results. With nano-bubbles—if they are true nano-bubbles—they’re so small that you can’t see them in the water, and the significantly smaller diameter bubbles remain suspended in the water much longer. If you had a cup of water with nano-bubbles in it, it would look like flat water, not club soda. The nano-bubble matrix in water is very stable, so you don’t lose a lot of these bubbles to the air. In fact, special lab equipment is required to measure the number and size of nano-bubbles.”
Peña also points out that specialty gases may be used to achieve specific water treatment goals such as enhanced oil separation.
“Our ultimate goal in injecting nano-bubbles is to extend the life of treated water quality. Nano-bubbles using air is a potential method to address oxygen demand-related issues in pits and large volumes of stored water. One limitation to conventional aeration is the time required to saturate the water with oxygen to meet the demand of the pit. This is especially true when waters are re-inoculated with contaminants that are hard to control post-treatment,” she said.
“Conventional aerated bubbles are larger and tend to come to the surface faster reducing the window of time for the oxygen to react with organic matter and sulfide contaminants. Nano bubbles, however, theoretically have the ability to stay in the water longer, thereby extending their reaction time. The end result may be higher quality water by meeting the oxygen demand more efficiently than with traditional aeration. Treating with nano-bubbles may not only increase the rate of cleanup but could also potentially reduce the amounts of air/oxygen and chemicals.”
Technologies for oilfield water treatment continue to evolve, and Select is keen to stay on the forefront of new developments. Oilfield water treatment often utilizes a number of technologies including gas flotation units for solids separation and walnut-shell filters for dispersed-oil removal. Select also uses water-clarifying chemistries to reduce turbidity and enhance frac-quality water. Aeration is commonly used with stored treated water to maintain the water quality. There is no silver bullet when it comes to water treatment, as every operator has unique requirements, so the team is constantly developing customized solutions for specific customer applications utilizing multiple technologies, rather than promoting any single type of treatment technology for every instance.
“Water recycling and reuse services are becoming more prevalent due to the growing produced water volumes, sensitivity toward subsurface disposal and increasing frac water requirements. Additionally, Select’s focus on monitoring and automation capabilities across its services provides the customer with additional visibility, controls and risk management protections, resulting in safer and more environmentally responsible management of produced water. Technology will continue to add critical value to produced water management,” Peña said.
Convention and the challenge offshore
National Oilwell Varco (NOV) handles produced water issues both onshore and offshore with an array of technologies designed to deliver smart, cost-effective results to clientele across the globe. In some cases, that means taking a closer look at what has become the norm across the industry and turning it on its ear—in the case of NOV’s horizontal gun barrel (HGB) separators, quite literally. The company examined the traditional vertical separators being used for decades and found them inefficient, with solids buildup leading to poor oil/water separation. In late 2015, the company installed its first HGB, designed to give the user a significant increase in recovered oil volume, thus adding profitability. Combined with NOV’s online Tore de-sanding technology, the vessel provides greater efficiencies and reduced maintenance costs.
Well fluids are introduced into the HGB, where two distribution baffles spread the fluid across the vessel into the primary separation section. Oil and water separate via gravity, and solids settle and accumulate on the bottom of the separator. The vessel can operate at a range of pressures, allowing the effective flow of the separated streams to lower pressure receiving systems by level control instrumentation.
“We are seeing success with our horizontal gun barrel separators, which are a more modern take on a traditional and far less efficient tank-based design,” explained James Vanjo-Carnell, Produced Water product line manager for NOV Completion & Production Solutions. “The horizontal gun barrel was introduced to the North America onshore market in response to large flowback produced water volumes in unconventionals. The HGB improves oil recovery and solves solids buildup issues while maintaining cost competitiveness for saltwater disposal [SWD] facilities. To date, over 70 HGB systems have been installed in North America.”
NOV’s WaterWolf is another tool used to recover oil and suspended solids from produced water in a single stage of treatment, without chemicals or filters. Introduced in 2015, WaterWolf uses enhanced gravity systems to separate oil, eliminating or reducing the need for treatment chemicals altogether. It builds on the heritage of proven hydrocyclone technology, long used in offshore oil fields to optimize produced water handling and extend well life. The dynamic oil recovery (DOR) processes are unaffected by changes in upstream flow rate or pressure and can be adapted to a wide variety of treatment scenarios.
“We’ve fed back into the design to continuously improve the offering,” Vanjo-Carnell said. “The technology always offered a balance that allowed a type of ‘fit-and-forget’ system within the DOR concept that eliminated turndown and shear issues associated with de-oiling and de-sanding hydrocyclone operation. The concept builds on the use of no-shear pumping systems that NOV manufactures within an automatically balanced flow loop. Technologies can be incorporated into the DOR loop to enhance robustness and processing capability if required. We’ve now enhanced this with a system that better manages reject fouling issues, which can be further optimized by digitization techniques.”
NOV’s water management technology offerings continue to grow. “We have a much more expansive produced water treatment portfolio since WaterWolf’s inception through our acquisition of Fjords Processing,” Vanjo-Carnell said. “Many of the technologies that came with it are ideally suited to become part of the WaterWolf DOR concept, such as our Mare’s Tail inline oil droplet coalescer and our compact flotation technologies. We are also working to increase the capacities of the WaterWolf system and are currently designing a mobile, skid-mounted, produced water treatment system based on Water-Wolf concepts that will achieve 126,000 barrels per day in a transportable footprint of 12 by 40 feet.”
Like its peers, NOV is keen to evolve with the changing demands of its client base. As new concepts and technologies are introduced, new rules are implemented and field demands morph over time, the company strives to keep ahead of the game when it comes to improved economics and overall cost-competitiveness.
“We’ve just come out of a really tough period within the industry, and we have simply had to sharpen our pencils,” Vanjo-Carnell said. “We see the same demand for aggressive cost performance but also an awareness pertaining to system process and mechanical performance. This is an interesting challenge for us, as it is in line with our core principles. We aim to use smart engineering to offer technically and commercially aggressive solutions—backed up by our validation techniques and experience base—to give the industry what it needs.”
Customer needs are varied, especially when considering produced water treatment requirements for offshore operators. The evolution of discharge regulations in certain parts of the world, such as Mexico and Brazil, are starting to highlight the increasing importance of understanding dissolved organic loading as this applies to typical offshore produced water treatment design.
“A dissolved treatment kit is expensive, and when you are working with large produced water flows, it becomes prohibitively so,” Vanjo-Carnell said. “To be able to offer an economical and technically acceptable design, it is important to understand the target dissolved organics and be able to map their fate through pressure and temperature changes that occur within a traditional (mechanical) produced water treatment system. Once this has been completed, the true loading and removal demand from a dissolved treatment system can be defined, and the dissolved system becomes more economically viable.”
Within the offshore sphere, NOV is seeing a push toward reduced/unmanned facilities. Unmanned facilities can make lower yield or aging fields more competitive to produce since the labor (and all associated logistics) costs are reduced.
“This means that to be able to reliably meet regulations for discharge, where produced water re injection isn’t available 100%, the produced water treatment equipment has to be reliable, predictable and very simple to maintain since the maintenance window is likely to be quite small,” he said.
A spin on the road to delivery
For operators, formulating the right water management scheme is dependent on a number of factors including land position—continuous acreage allows for centralized processing facilities with an integrated water pipeline network whereas disconnected acreage requires trucking of the water. To offset rising transportation costs, operators and service providers are looking for more robust mobile solutions featuring a reduced footprint and lower-weight equipment. Automation of basic activities, including inline sampling, also remains a priority for both service companies and operators as a means of improving process safety and managing labor expenditures, according to Schlumberger. This requires advancements in sensor technologies for conducting various water composition studies—from the on-the-fly water quality analysis to determining salinity levels.
“For the latter, Schlumberger has launched the AquaWatcher Surface water salinity sensor that determines water salinity in real time by employing microwave sensor technology to continuously measure water conductivity in wet gas and multiphase (water-continuous) flow,” said Laure Mandrou, marketing and technology manager for Testing Services at Schlumberger. “This automated measurement reduces operating costs by eliminating manual water sampling and analysis.”
In the Midland Basin, the AquaWatcher Surface sensor was installed at a well site for a long-term flowback test, and it reported continuous measurement of the water conductivity to the data acquisition computer. The real-time salinity was used to automatically update monitoring of the flowback water properties. Personnel was not required to visit the remote well site and manually measure and enter the salinity value. The accuracy of the flow-rate measurements was improved for better understanding of the results of the flowback test while operating costs for site visits were significantly reduced.

“What these current trends have in common is a pursuit of optimizing water treatment operations while decreasing environmental impact,” explained Katherine Rojas, water business manager at Schlumberger. “Ultimately, reducing the cost per barrel of water through a combination of innovative and environmentally minded solutions and engineering processes will continue to be a driving force for all major water management decisions.”
Schlumberger’s footprint in the water management space continues to expand with the recently introduced Voraxial impeller-induced cyclonics. Debuted in North America, the new technology provides instantaneous, continuous, concurrent separation of water, oil and solids at very high flow rates to bring new efficiencies to oilfield water sourcing and management.
“This efficient inline water treatment process cleans water from varying sources by separating out oil with any entrained gas and solids with different specific gravities,” Rojas said. “The technology outperforms conventional centrifuge or hydrocyclone separation, which requires a booster pump to counter its performance-constraining pressure drop and must use multiple units and multiple passes for the separate removal of oil and solids from the liquid.”
Instead of employing a conventional hydrocyclone to convert the incoming liquid velocity into rotary motion for separating heavy and light components, Voraxial cyclonics use a unique no-shear impeller to induce radial and axial flow for three-way separation of water, oil and solids. The application of simultaneous separation during continuous flow means that only one pass is required through the unit, and there is no associated pressure drop.
Reliable delivery of a high-rate daily output of frac-grade water, once only a remote technological vision, is now a reality. Schlumberger’s oilfield water treatment services enable using surface water for onsite frac water sourcing. By substantially reducing the need to access and produce from freshwater aquifers or truck-in water supplies, the company’s self-contained, trailer-based, plug-and-play system significantly reduces water costs. The mobile in-line treatment automatically adapts to changing input quality and quantity without interrupting operations for reconfiguration. Produced water also can be easily treated to augment frac water inflow.
“The performance predictability of single-sourced or commingled frac water is assured by at-rate separation as needed,” Rojas said. “Nonproductive time resulting from poor or inconsistent water quality, such as screenouts and pump failures, is prevented to support operational continuity. Based on customers’ water requirements, the Voraxial impeller-induced cyclonics inside the mobile unit can be paired with a high-intensity UV [ultraviolet] light source to efficiently neutralize any biologically active agents in the water and prevent souring. Further chemical treatments can be added on the fly in the mobile unit.”

Depending on specific water needs, the separation process can be followed with UV light, oxidation and biocide treatments to destroy polymer content for frac water recycling, sterilize microbes for pit and pond maintenance, and reduce select ions for protection of tanks and pipelines and SWD.
Schlumberger is continuing its work with clients to achieve business, environmental, social and governance objectives when it comes to water management. Given the radically different variables that can be applied to any one project, the company recognizes that there is no magic solution applicable to all scenarios. It continues to come down to having the right tools and expertise.
“Streamlining water treatment through innovative technologies and environmentally intelligent chemistry applications is an important step in both improving performance and reliability and adding new dimensions to the professional competency of personnel,” Rojas said. “This can be accomplished when operators and service companies collaborate on sharing data from performance testing, including full analytical profiles of chemical constituents and process simulation testing, to develop comprehensive water management practices.”
As the water treatment sector matures and expertise becomes more attainable and transferable to field personnel and remote operation centers, workflows for mechanical separation and chemical treatment processes will become more defined, enabling operators to achieve consistency in treated water quality, according to Schlumberger.
“As a result,” Rojas added, “these improvements will lead to smaller equipment footprints, less chemicals, less people on the ground and less waste—all contributing to a sustainable use of environmental and human resources.”
Read E&P's other 2019 Water Management Techbook articles:
OVERVIEW:
Managing Water for Increasing Production Volumes
As production rates continue to climb, so does the amount of water produced.
KEY PLAYERS:
Companies Focus on Replacing Freshwater Sources
These 40 companies are representative of some of the key players in water management.
MIDSTREAM:
Full Immersion: Industry Gets Religion on Produced Water
Volumes could reach 50 MMbbl/d in just the Permian; all options are on the table.
CASE STUDIES:
Adopting an Infrastructure Approach for Produced Water Management
One possible answer to the Permian Basin’s water woes lies in the sands of Oman.
Technology Reduces Produced Water By 50%
Proppant-bonded technology reduces formation water without hindering oil and gas production.
Recommended Reading
Phillips 66’s NGL Focus, Midstream Acquisitions Pay Off in 2024
2025-02-04 - Phillips 66 reported record volumes for 2024 as it advances a wellhead-to-market strategy within its midstream business.
Rising Phoenix Capital Launches $20MM Mineral Fund
2025-02-05 - Rising Phoenix Capital said the La Plata Peak Income Fund focuses on acquiring producing royalty interests that provide consistent cash flow without drilling risk.
Equinor Commences First Tranche of $5B Share Buyback
2025-02-07 - Equinor began the first tranche of a share repurchase of up to $5 billion.
Q&A: Petrie Partners Co-Founder Offers the Private Equity Perspective
2025-02-19 - Applying veteran wisdom to the oil and gas finance landscape, trends for 2025 begin to emerge.
Chevron Makes Leadership, Organizational Changes in Bid to Simplify
2025-02-24 - Chevron Corp. is consolidating its oil, products and gas organization into two segments: upstream and downstream, midstream and chemicals.
Comments
Add new comment
This conversation is moderated according to Hart Energy community rules. Please read the rules before joining the discussion. If you’re experiencing any technical problems, please contact our customer care team.