[Editor's note: This story originally appeared in the March 2020 edition of E&P. Subscribe to the magazine here.]
The tens of thousands of horizontal wells drilled and in production since the start of the shale boom have driven the U.S. to be the world’s largest oil producer. But to drill and complete those tens of thousands of miles-long horizontal wells, massive quantities of water are needed, with estimates by the Southwest Research Institute (SWRI) of more than 9.7 MMgal per well. In addition to requiring substantial amounts of water to drill and complete just a single well, shale wells can produce an average 10 bbl of water with each barrel of oil, according to the American Geosciences Institute. In short, water management has emerged as a multibillion industry in North America. According to Bluefield Research, the water-for-fracking market in the U.S. accounts for $17 billion in spending from 2019 to 2028.
Along with the tremendous amounts of infrastructure needed to move around that water, including manpower and machinery, the oil and gas industry is rapidly deploying innovative technologies that help increase efficiencies, drive down costs and improve environmental stewardship. Both operators and service providers have recognized that reusing produced water for fracking operations is both cost-effective and environmentally beneficial. Meanwhile, work is being done on systems that help eliminate the ever-increasing amounts of produced water that aging shale wells tend to produce. A consortium of research institutes, service providers and operators are examining alternatives to traditional water-based frac fluids. And a leading service provider will soon deploy a system that will help push large quantities of water at low pressures through vast networks of water pipelines in West Texas.
Much of the focus on water management operations and technology innovation has been focused in the Permian Basin. According to Bluefield Research, the Permian represents 54% of the annual total water management demand. By comparison, the Marcellus and Utica in the gas-rich Appalachian Basin make up 14% of water management spending.
“Driven out of the Permian Basin, but also different basins like in the Bakken, produced water volumes are increasing. If you look at the trends over the past 10 years, they are increasing rather substantially,” said Nathan Holland, global product line director for Baker Hughes. “I don’t think that really comes as a surprise when we think about how many new wells have been drilled in that fiveto 10-year span, specifically with the focus on the horizontal plays. But how do we handle this water? What do we do with it? Where will we put it?”
Water treatment and chemistry
A recent report issued by the Texas Alliance of Energy Producers found that many, if not all, producers in the Permian Basin have deployed water recycling programs. According to the report, Pioneer Resources recycles 15% of its produced water, EOG Resources recycles 20%, Apache recycles 30% and both XTO and Concho are recycling 10%.
The report estimates that overall in the Permian Basin, about 450,000 bbl/d of water, as much as 9% of all produced water in the basin, are being recycled and reused as frac fluids. To advance the water that comes back from a producing well into a usable, cleaner version for fracturing, service companies deploy an array of treatments and chemicals to rid it of contaminants and solids.
Oilfield chemistry company Solugen focuses on, among other solutions, treating water for scale, which can include combinations of iron, calcite and barium. Tom Swanson, vice president of innovation, explained that as a result of shortages of aquifer or other source waters, operators are blending mixes of source and reuse water with produced water. He said this can result in high levels of chloride and other scale-forming cations, which then leads to elevated amounts of total dissolvable solids (TDS).
Operators often look for “sterile” water for fracturing operations, which won’t produce microorganisms such as sulfate-reducing bacteria to ensure the integrity of the frac operations and prevent premature souring of the reservoir, Swanson explained.
“That is usually addressed with an oxidizer or a microbiocide,” he said. “Operators are also looking for water that does not have reactive agents, such as divalents or trivalents. These are reported as iron, calcium, barium, strontium or magnesium. They want to reduce the amount of those reactive species in the water beyond chloride.”
Swanson explained that chemical technologies can be applied to produced water to rid the water of reactive TDS, particularly iron.
“Iron can also interfere with and break apart the polymers in the fracking process,” he said. “That would give operators a low-efficient frac where the frac fluid polymers aren’t carrying sand to the pores in the reservoir where oil and gas would be produced. Because when the sand-carrying polymer breaks down and prematurely loses viscosity, the sand/proppant doesn’t reach the fractures, which is referred to as sanding out. When that happens, you have a poor producing well because you reduced the porosity and permeability of those fractures, and they ultimately close under pressure without the proppant in place.”
Swanson said Solugen’s ScavSol system, which is most often applied at the production stage to reduce iron sulfide buildup in hydrocarbons, also can be used to control iron in produced water.
“ScavSol keeps the iron in the water in an unreactive state and it doesn’t affect the polymers that are being applied in the fracking process,” he said. “So operators get an improved frac, and then they get improved production from that well.”
In September 2019, multi-industrial service company Sparx Engineering spun off a company called Countertrace, which treats and optimizes fluids for industrial purposes such as fracturing operations. According to a press release, Countertrace’s technology, which was developed by Sparx engineers, is based on a polymer macroparticle that can be “programmed” to identify and selectively contain and remove contaminants from complex fluids, allowing for water reuse or disposal.
As the company explained in the release, the technology works when reusable macroparticle spheres, which are covered in receptors that bind to the targeted contaminant, signal the acquisition of the target via a color changing sensor and then are filtered for reclamation.
“Simply, the hollow plastic pellets grab and hold a contaminant just with their presence in the fluid,” the release stated. “This technology reduces the amount of chemicals and water needed in the extraction process.”
Veolia Water Technologies specializes in a multitude of systems and processes for water treatment, particularly for the upstream oil and gas industry. Among those is its HPD evaporation and crystallization technology, which manages highly soluble brine to reduce system fouling and recovers high volumes of water for reuse, according to the company. The HPD system removes sodium and calcium chloride as well as heavy metals in the effluent generated in shale gas production, according to Veolia.
“There is a lot of front-end work that needs to be done to understand the analytical components of produced water prior to it being reused,” said James Welch, director of business development for Veolia. “If we’re producing water and it’s high in salinity, sulfate or iron, for instance, and the friction-reducing chemistry or stimulation chemistry has a tolerance or a limit on contaminants, then that would dictate how we might manage that water with what technologies we apply.”
Welch said the key components Veolia looks to remove from produced water are free oil, suspended solids, H2S, bacteria and iron. In such an instance, Veolia can apply its Co-Strip or ShaleFlow systems to remove dissolved gasses or free oils.
“We combine that with polishing filtration on the back end and then solids management systems to address the sludge that may come off of the water,” he said.
Welch said another complicating factor in water treatment is that water qualities vary from basin to basin. For example, he explained that in the western portion of the U.S., water qualities tend to be better and originate from a single formation, whereas in the Permian, the stacked pays create varying qualities.
“Where it gets more challenging is where you start blending waters from different zones,” he said. “In the Permian Basin, for instance, you have multiple pays where water is produced to the surface and blended in tanks or impoundments. You can have deposition problems or noncompatibility issues with the produced water in recycling.”
Holland agreed that different basins can often have slightly different chemistries that should be considered during treatments.
“We work with our sister product line and chemical division, collect samples and study those samples to understand what contaminants are in the water and when they can precipitate out,” he said. “All of this circles around different injection pressures and what that means to the equation.”
Treating for disposal
The trend toward increased water reuse and recycling is driven in part by environmental stewardship and also the inefficiencies and costs associated with downhole disposal of produced water. As Swanson explained, it might cost an operator upward of $2 million to $3 million to drill a saltwater disposal (SWD) well, in addition to operating costs. But with the disposal option still prevalent in most unconventional basins, service providers are seeking ways to improve those operations and effectively treat the water so it can be reused in fracs rather than disposed of.
“It’s quite common in saltwater disposal systems to use an oxidizer as the final stage of sterilization and clarification of produced water, because it’s cost-effective,” Swanson said. “The issue companies run into in SWD operations is when they try to precipitate all the divalents out of the water with an oxidizer alone. Iron is a unique species in that iron hydroxide does not fully precipitate. It tends to carry through, and then it forms in scale in the downhole saltwater disposal system. So they have to go in and either acidize the well to remove it or, if they’ve done enough damage, they’d have to replace that disposal well.”
Swanson said that in such cases, Solugen can offer a type of combination product that blends with hydrogen peroxide with ScavSol to better control iron and extend the life of water handling systems.
“They can bind the iron, keep it soluble and unreactive and still apply their traditional oxidizer to clean the water, remove microbial bacteria and then also prevent scale and corrosion formation downhole,” he said.
Veolia’s Welch explained that operators choosing to dispose of produced water downhole want to avoid any depositions in that water that would lead to scale buildup in the SWD well.
“H2S can be corrosive to the wellbore,” he said. “Suspended solids or changes in pH that would cause precipitation in a disposal well would also be a concern. So I think a lot of the chemistry and treatment and the processes that you would use to condition water for recycling are also relevant for water going down the disposal well, but maybe not to the same extreme.”
As more wells need and produce more water, additional infrastructure is needed to move that water around, particularly in vast regions such as the Permian Basin. In an effort to solve piping challenges such as moving produced water between recycle and reuse ponds, Baker Hughes plans to unveil a pump later this year that will push large volumes of water at low pressures. Holland said the pump also could be used to move high volumes of produced water to multiple disposal wells.
“We looked at the current offerings and strategies out there today, and it is very equipment intensive and manpower intensive,” he said. “We wanted to figure out how we can get some of that intensity out of this space, because if we can make it simpler, recycling and reuse will grab traction faster, and hopefully we’ll see this trend really stick this time.”
Holland gave an example of how the new pump system would be a benefit by explaining how operations typically work at a traditional Permian fracturing site with a large water settlement pond.

“These large settlement ponds are quite massive with several pumps around that lake or pond,” he said. “They are moving that water to different locations, whether it be future frac jobs, current frac jobs, other ponds or into disposal sites for injection. There is a lot of equipment and a lot of people that have to be a part of that operation. The technology we’re looking at specifically with this pump is that it can eliminate having multiple pumps to move those volumes of water. We can do it with one pump.”
Holland said among Baker Hughes’ goals in water management is offering streamlined operations and strategies to operators. Among the challenges he and the company have identified is managing the differing strategies and philosophies of operators and midstream companies.
“It’s important for us as a service provider to get into that conversation early and help develop a strategy,” he said. “With the different divisions of Baker Hughes that handle the treatment of water specifically, and the chemicals division, we are trying to take all of that knowledge and get a seat at the table at the right time and help lay out strategies for success.”
Evaporation technologies
Water recycling and reuse as well as downhole disposal each present their own challenges. Operators looking to inject their volumes of produce water might face limited disposal well availability, particularly in the Northeast, or regulatory restrictions such as those in Oklahoma. Additionally, tight completion schedules can restrict the ability to recycle produced water.
One alternative to both produced water reuse and water disposal has been evaporation. In December 2019, Gradiant Energy Services announced the successful completion of an evaporative disposal project for an operator in the Permian Basin.
According to Gradiant, the Carrier Gas Concentration (CGC) system operates on the principal of humidification of a carrier gas via a multistage bubble column.
“Waste heat is used to heat produced water prior to entering the bubble column, where it contacts carrier gas bubbles and transfers freshwater vapor to the carrier gas,” the company explained in a release. “This continuous process results in clean water vapor released into the atmosphere and concentration of the dissolved solids in produced water to make a concentrated brine.”
That brine can then be used for drilling, workovers and completions. According to Gradiant, the CGC system was utilized to evaporate 1,000 bbl/d of water in the Permian Basin over a 25-day period using natural gas a fuel source.
“The treatment pilot consisted of H2S pretreatment via oxidation and volume reduction through a CGC unit,” the release stated. “The CGC included a natural-gas-powered hot water boiler with heat exchanger to heat the produced water and a bubble column where ambient air is introduced to extract water vapor from the produced water.”
Conformance
Conformance technologies can help reduce the production of unwanted water or gas. According to Halliburton, which has developed a series of such systems, “application of these technologies can often improve an operator’s profitability by helping to achieve a longer productive well life, reducing lift costs and reducing environmental concerns and costs.”
Julio Vasquez, global product manager at Halliburton, explained that conformance systems are most often applied to mature assets that have reached their peak production, and typically when water cut has reached values in excess of 80% to 90%, significantly reducing the well’s profitability.
“Water production is being seen in the industry as one of the major challenges, because it’s not only expensive to handle water, but it typically is associated with reduced hydrocarbon production,” Vasquez said. “Disposing of water, surface facilities construction to handle water, reinjecting the water—all of that is detrimental to the profitability of the reservoir. So whenever you see the water production going up to, say 60%, 80% water cut, then hydrocarbon production typically starts going down. That’s where we see the main value on implementing this type of technology.”
About two years ago, Halliburton released EquiSeal fluid treatment service, a porosity fill-sealant designed to help control unwanted fluid production in horizontal or highly deviated wellbores. According to the company, EquiSeal allows precise placement of a gel system due to its stressdependent rheological properties. Vasquez said EquiSeal has been deployed in about 30 to 40 wells so far since its initial commercialization.
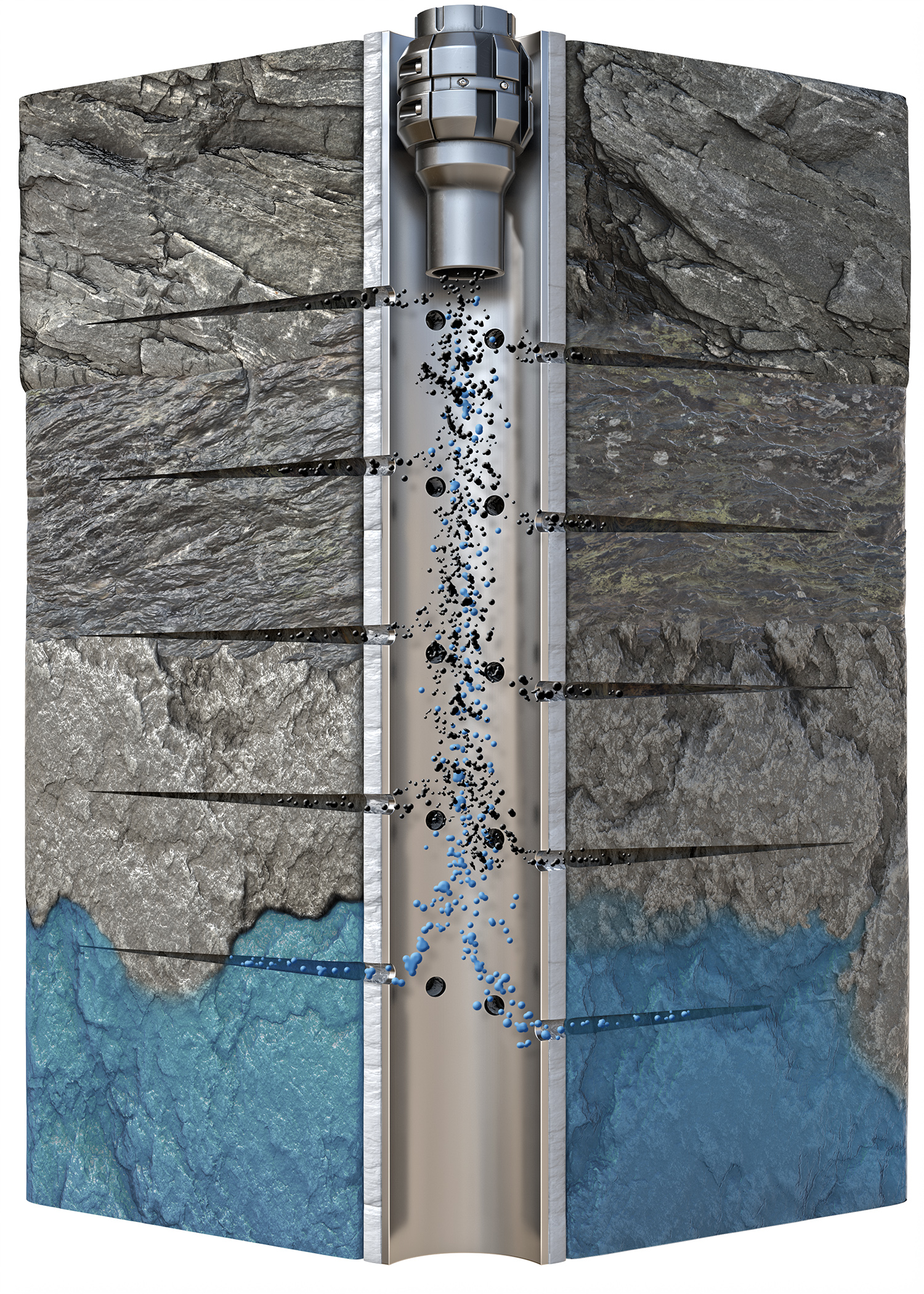
“A main benefit of this technology is that we added thixotropic properties to the system to allow a more controllable and precise placement,” he said. “Whenever the treatment is reaching the horizontal section, or in a highly deviated part of the well, this system will not slump down because of its optimized fluid rheology. Once in place, EquiSeal fluid treatment service will eventually crosslink at a predicted time and shut off the permeability of the water producing zone.”
Another conformance system Halliburton applies is WaterWeb treatment service. According to the company, WaterWeb is a relative permeability modifier designed to selectively reduce water flow from the treated area with little or no damage to hydrocarbon production.
“WaterWeb treatment service is a selective chemistry that allows [users] to simply bullhead the treatment into the open perforations,” Vasquez said. “It selectively reduces permeability to water with minimum reduction to hydrocarbon permeability. Because of this feature, mechanical isolation may not be necessary. You can simply bullhead it into all the open perforations with minimum risk of damaging hydrocarbon production.”
He said WaterWeb has been deployed on about 2,500 jobs since its initial commercialization.
Although conformance technologies are most often applied to mature wells that are in the midst of late-life production, Vasquez said there can be value in deploying them earlier in a well’s life.
“Customers that are more proactive have seen great results with these technologies in their mature fields, rather than waiting until the asset is completely watered out,” he said.
Vasquez noted an E&P company operating offshore Latin America experienced water coning problems.
“They have a very active aquifer below the hydrocarbon production formation,” he said. “After a few years of production, water production starts coning up and reducing hydrocarbon production. But they have had success with these conformance technologies that provide a long treatment life in terms of slowing down the coning effect. Now, whenever they move to a new field, they are sometimes doing these types of treatments as preventative treatments rather than remedial treatments.”
Vasquez added, “Diagnostics is key to have a high success ratio and increase well performance through these customized intervention solutions and ultimately provide reliable execution to the operators.”
Read E&P magazine's March 2020 "Water Management Techbook" articles:
OVERVIEW:
Bringing Balance to Water Demands
KEY PLAYERS:
Meeting Water Management Demands
TECHNOLOGY:
Innovations in Water Management Technology (story above)
MIDSTREAM:
The Rise of Water in the Midstream
Recommended Reading
Ring May Drill—or Sell—Barnett, Devonian Assets in Eastern Permian
2025-03-07 - Ring Energy could look to drill—or sell—Barnett and Devonian horizontal locations on the eastern side of the Permian’s Central Basin Platform. Major E&Ps are testing and tinkering on Barnett well designs nearby.
E&P Highlights: March 10, 2025
2025-03-10 - Here’s a roundup of the latest E&P headlines, from a new discovery by Equinor to several new technology announcements.
E&P Highlights: Feb. 24, 2025
2025-02-24 - Here’s a roundup of the latest E&P headlines, from a sale of assets in the Gulf of Mexico to new production in the Bohai Sea.
E&P Highlights: Feb. 10, 2025
2025-02-10 - Here’s a roundup of the latest E&P headlines, from a Beetaloo well stimulated in Australia to new oil production in China.
E&Ps Pivot from the Pricey Permian
2025-02-01 - SM Energy, Ovintiv and Devon Energy were rumored to be hunting for Permian M&A—but they ultimately inked deals in cheaper basins. Experts say it’s a trend to watch as producers shrug off high Permian prices for runway in the Williston, Eagle Ford, the Uinta and the Montney.
Comments
Add new comment
This conversation is moderated according to Hart Energy community rules. Please read the rules before joining the discussion. If you’re experiencing any technical problems, please contact our customer care team.