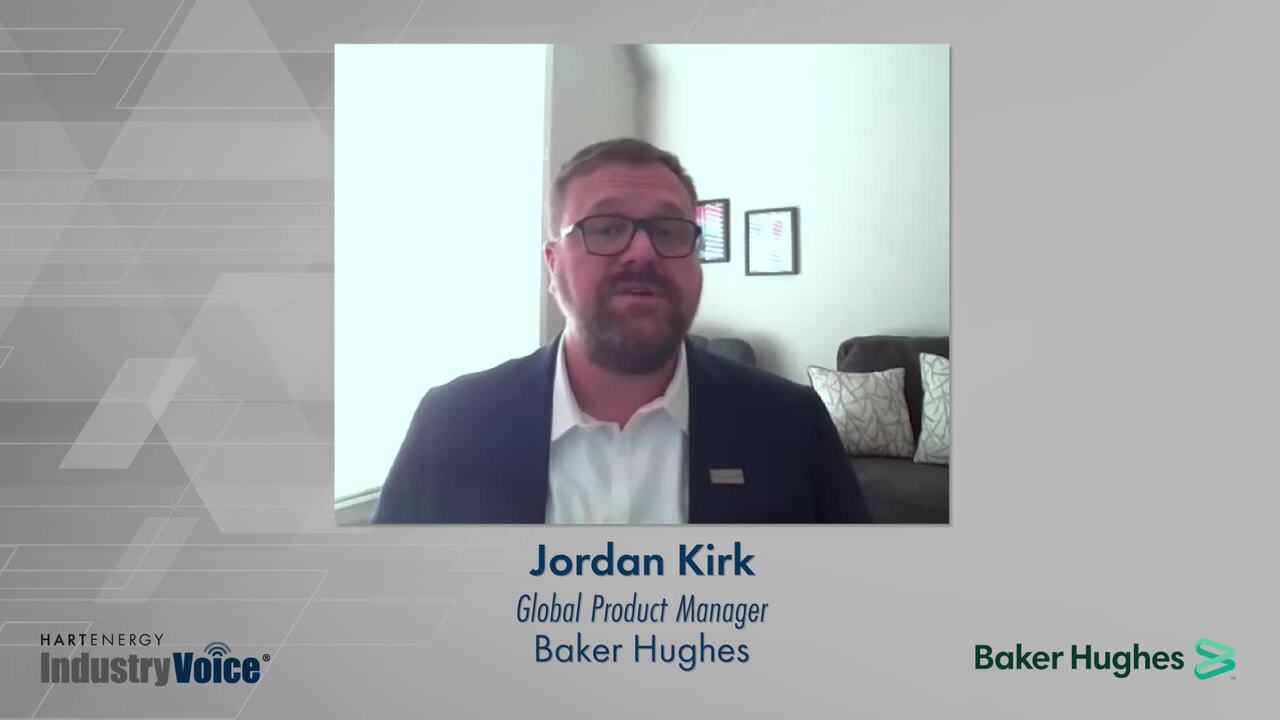
In their efforts to decarbonize daily operations and progress on their path to net zero carbon emissions, operators across several industrial sectors are looking to carbon capture, utilization, and storage (CCUS) as a viable solution. In fact, CCUS might be the only solution to address the nearly 25% of industrial CO2 emissions that cannot be avoided simply by switching to alternative fuel sources.
In 2020, CCUS storage capacity totaled roughly 40 million tons of CO2 from 26 active project sites around the world. According to the International Energy Agency’s Sustainable Development Scenario, a total capacity of 7,600 million tons will be required by 2050 to meet decarbonization goals set forth in the Paris Climate Accords.
Meeting this capacity goal will require a sizable and sustained investment in new CCUS projects. As more projects come online in coming years, operators will need cost-effective pumping systems that can easily adapt to growing storage capacity needs in the future. This need prompted Baker Hughes to redesign its HPump surface pumping system. The system was first designed for high-flow water injection in water alternating gas injection processes more than 40 years ago. Since then, the company deployed more than 400 units for CO2 pumping in EOR projects.
The pumping system consistently met oilfield operators’ needs for a reliable solution for moving CO2, using proven and familiar equipment. Based on electrical submersible pump (ESP) technology and installed horizontally per API 686 (Recommended Practice for Machinery Installation and Installation Design) and Baker Hughes recommendations, the surface-mounted system incorporates several design modifications to optimize CO2 pumping. Reliable, rotating-shaft seals based on aerospace technology provide a tandem-cartridge, mechanical shaft seal, and supporting seal flush on the suction intake side. In addition, the system is engineered with an optimized stage count for the pumps, which ensures highly efficient movement of the required volume of CO2 at reduced densities.
The pumping system’s success in oilfield CO2 pumping operations caught the attention of early-stage CCUS operators. A growing number of CCUS projects are leveraging the system’s modularity and scalability for sizable performance gains at significantly lower CAPEX and OPEX.
Meeting changing capacity needs through a scalable, modular design
The storage capacities of many CCUS projects will likely ramp up over the next 1-5 years, but the exact timing is uncertain. The surface pumping system is well-suited for on-demand capacity changes thanks to a modular design that can be modified in place to accommodate pumps ranging from 25 to 2500 hp.
Customers can quickly expand flow capacities and increase pumping pressures by installing a larger diameter pump right on site. The modular design also allows operators to scale back their pumping capacities by installing smaller pumps on location. No other pumping solution on the market provides this level of capacity flexibility while minimizing nonproductive time to make equipment changes.
Gaining greater flexibility from a lower-cost alternative to API pumps
Surface pumps use standardized components that are sourced from multiple storage locations worldwide. As a result, these pumps are significantly less expensive than conventional API-style pumps, which are typically custom-built with non-standardized parts.
Operators are saving time and money on delivery and installation as well. The surface pumps are typically delivered in eight weeks and installed in less than two weeks. API pumps might take nine months to deliver after the order is placed and then require a full month to install.
Surface pumping systems' lower upfront and operating costs give operators greater pumping flexibility. Many customers install and run two or more surface pumps in parallel, often for the same cost as a single API-style pump. Running redundant pumps ensures that pumping will continue if one unit goes down and must be repaired. And when both pumps are running, the operation gains greater flow assurance and CO2 pumping capacity at typically half the operating cost of a single API pump.
Access Baker Hughes' case study on CO2 Injection below.