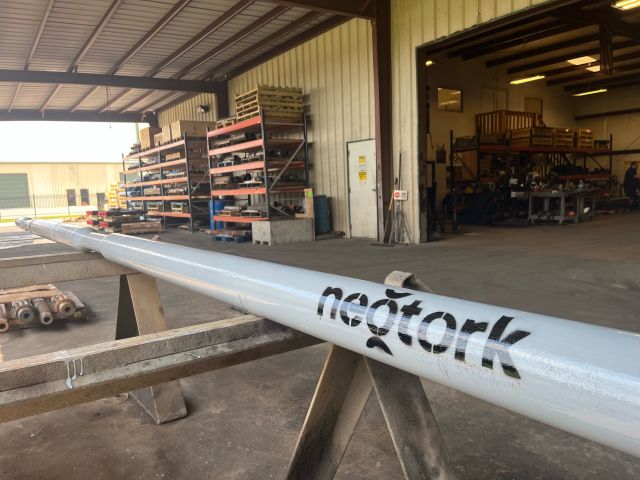
NeoTork is typically around 25-ft long, making it compact when compared to other BHA attachments. (Source: Neo Oiltools)
Though The Beach Boys may have picked up on “good vibrations,” the same can’t be said when it comes to downhole drilling.
Out in the field, vibration is a killer. Vibration causes the drill bit to bounce against the sides or bottom of the hole, causing premature bit or drill string failure and low rates of penetration. This can accelerate machine wear, consume excess power and cause equipment to be taken out of service, resulting in unplanned downtime.
There are four key types of vibrations and torque dysfunctions encountered in the oil field: Axial dysfunction is the up and down motion along the drill string axis, while lateral dysfunction is perpendicular to the drill string axis and bit. Stick-slip is an irregular rotational motion occurring when objects in contact slide over each other and HFTO is another form of stick-slip caused by the interaction between the drill bit and the rock.
While there has been a variety of vibration stick-slip tools and other instruments created to address and lessen the impact of vibration, it’s difficult for drillers to know what they will encounter downhole.
To prevent excessive vibration and mitigate several types of drilling dysfunction, operators have begun to add multiple VSS tools simultaneously to a rig’s bottomhole assembly (BHA). However, the caveat is increased BHA length, which is suboptimal as they are more effective the more compact they are, in turn leading to increased operational costs.

Neo Oiltools’ NeoTork can mitigate multiple types of vibrations downhole compared conventional tools used to suppress one type of vibration. NeoTork connects to a rig’s BHA and protects against all 4 types of vibrations by focusing on the depth of drill bit cut to improve efficiency, profitability and safety for all drilling projects. NeoTork also reduces the number of tools needed, which reduces operating costs while increasing efficiency and drilling speed.
“What NeoTork does is try to decrease the vibrations in all the different directions,” Robert Borne, CEO of Neo Oiltools, told Hart Energy. “If you can decrease the vibrations, you can minimize the potential damage or early wear to your drill bit, minimize any potential early failures and make the MWD [measurement while drilling], [logging while drilling] and the rotary steerable pieces last longer or not fail.
“If you can minimize vibrations, you can end up putting more weight on the bit, which means you can push harder, and if you can push harder, you can drill faster. If you can drill faster, you win.”
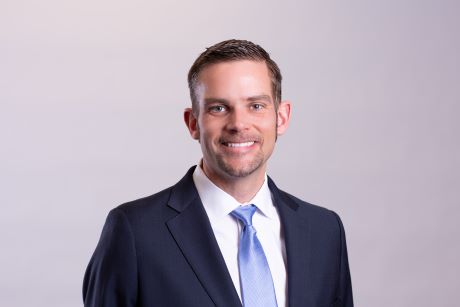
NeoTork’s design consists of cables and flat springs. When drilling, the torque created by the bit turning against the rock causes a lot of torque up the drill string. The cables allow the drill bit to stay in contact with the rock at all times, taking the majority of the torsional vibration and dysfunction out of the interaction between the rock and the drill bit. With little to no vibration, the well becomes easier to drill.
While the bottom half of the tool, which holds the cables, doesn’t change, the amount of springs involved in the tool is adapted to each individual wellbore.
“We can determine how many springs we want to put in [the tool] to determine how strong we want to make the tool based on the well we’re going into; we can calibrate the tool to the conditions of a specific well,” Borne said.
A supermajor compared NeoTork against an unnamed competitor in an SPE paper, finding that it reduced tangential vibration in a well, enabling a rotary steerable and MWD system to be rerun on the next well. The field testing showed NeoTork to be more effective and reduced “risk of failure.”
NeoTork is also able to greatly increase the speed of operations.
The typical drilling cost in the Delaware and other onshore basins in West Texas or New Mexico is $1/second, Borne said, which averages out to $85,000 per day to $100,000 per day, a time consuming and costly process for operators to drill just one to two wells per month.
“We just did two wells in the Delaware Basin that we drilled a curve and lateral on two consecutive wells on a pad, and our results saved them 1.5 days on each of those wells,” Borne said. “We just saved that operating company three days’ worth of rig time to finish those two wells total. If I do the math, that’s somewhere between $50,000 and $300,000.”
NeoTork is currently deployed in 80 projects to 100 projects a month globally, but it was its work in the U.S. that refined the tool.
“If you can figure out how to drill in the Permian Basin, you can figure out a lot of other places around the world,” Borne said.
“We do face a lot of tough environments. We deal with vertical wells, we deal with the vertical plus the curve [of the well] plus the lateral wells,” Borne said. “We get pressed a lot to hopefully achieve in one run that entire vertical curve lateral without ever coming out of the ground, which you can imagine is a huge potential savings for the client and directional driller, and thankfully we do it a lot.”
NeoTork has been used by operators and NOCs alike, working in North America and the UAE, as well as the Permian Basin.
Neo Oiltools is now looking to expand usage of NeoTork and make its mark on the industry. “Every single well on the planet would do better on the drilling side if you can minimize vibrations downhole,” Borne said.
The company’s strategy focuses on expanding operations within its existing geographies and basins, but does plan on continuing its global spread-out.
“We’re very close to being on the ground for our first well in Australia and have talked about a couple of places in South America, exploring a number of other countries in the Middle East. We’ll see what’s to come in those areas, but we’re growing where we currently are.”
Recommended Reading
SM Energy Restructures Leadership Team
2025-02-20 - SM Energy Co. has made several officer appointments and announced the retirement of Jennifer Martin Samuels, the company’s vice president of investor relations and ESG stewardship.
APA Updates Leadership, Names Ben Rodgers as EVP, CFO
2025-04-14 - APA Corp. is making several leadership changes, including appointing Khalda Petroleum board director Ben Rodgers as executive vice president and CFO.
Infrastructure Firm HASI Makes Executive Leadership Changes
2025-02-18 - HA Sustainable Infrastructure Capital Inc. announced four executive leadership appointments, effective March 1.
USA Compression Names Chris Wauson as COO
2025-03-07 - Chris Wauson, currently the leader of natural gas compression company USA Compression Partners’ Permian office, has been chosen as the company’s new COO.
Chevron Makes Leadership, Organizational Changes in Bid to Simplify
2025-02-24 - Chevron Corp. is consolidating its oil, products and gas organization into two segments: upstream and downstream, midstream and chemicals.
Comments
Add new comment
This conversation is moderated according to Hart Energy community rules. Please read the rules before joining the discussion. If you’re experiencing any technical problems, please contact our customer care team.